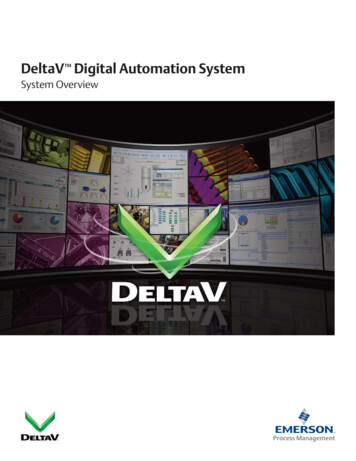
Transcription
DeltaV Digital Automation SystemTMSystem Overview
DELTAV DIGITAL AUTOMATION SYSTEMWith continued focus on human centered design, the DeltaV system deliverssignificant enhancements that help eliminate unnecessary work processes,removes the complexity of using the latest technologies and embeds specializedknowledge–improving your operations, easy.What you want, when you want it, where you want it.With the introduction of I/O onDemand, an unprecedentedamount of field I/O adaptability,ease-of-integration and plantavailability becomes possible.Costs and concerns around singlepoints of failure, marshalled crosswiring, power and grounding ofFOUNDATIONTM fieldbus segments,and late project I/O and processdesign change orders cancompletely disappear.Regardless of I/O type–traditionally wired I/O, FOUNDATIONfieldbus, Profibus DP, DeviceNet,AS-i bus, or even redundantInherent functionality regardless of size.Process control facilities andapplications certainly come in allsizes and levels of complexity. Tomaximize the return on yourinvestment, the automationsystem should easily scale withoutadding complexity.Part of Emerson's PlantWebTMarchitecture, the DeltaVTM systemis built from the ground up forultimate scalability. Regardless ofyour application’s size, the DeltaVPage 2–DeltaV System Overviewsystem keeps the same look andfeel. This reduces administrationand training costs, and optimizesboth initial investment and futureexpansions.From bench top, to pilot plant, tofull production; from 25 I/O pointsto over 1 million, your systemadapts to meet your needs. Sameoperations experience. Samemaintenance experience. Samesystem, scaled to fit. Easy.wireless–you can add and beginusing the information all nativelyand with far less engineering,design, and field work.You choose the I/O you need, wemake it easy. I/O on Demand–yourI/O, any type, anytime, anywhere.
Advanced technologies that are easy to use and maintain.Plant availability at peakperformance, that’s really theultimate goal of any automationsystem. Keeping the facilityrunning in a safe and securemanner, while optimizing theproduction, is what the DeltaVsystem with AMS Suite: IntelligentDevice Manager is all about.All the predictive power of smartdevices is combined with the latestadvanced control technologies toprovide the ultimate in embeddedintelligent control. Whether it’sthe latest in virtualization,predictive device alerts, adaptivetuning, or model predictivecontrol–you have the power ofembedded intelligent controlwithin an integrated system that’seasy to use and maintain.Delivering the power of PlantWeb to every installation.The DeltaV system has thecommissioning power of AMSDevice Manager included. Thiscombination connects youroperations with the predictiveintelligence in smart devices–forgreater availability.The inherent integration of theDeltaV system extends to batch,advanced control, changemanagement, engineering tools,diagnostics, simulation, and eventand continuous historian.Emerson provides solutions thatintegrate with your plant systemsabove, below, and in parallel withthe DeltaV system. And, it is tightlyintegrated with:n SyncadeTM suite which providesoperations managementn AMS Suite which providespredictive maintenancen DeltaV SISTM system whichprovides an integrated yetseparate safety systemn Integrated machinerymonitoring.Designed specifically for your process control applications.Over the last ten years, commercialoff-the-shelf technologies (COTS)have provided tremendousincreases in functionality and costadvantages. The DeltaV systemwas the first such system on themarket, and continues to provideopen, proven products to itsprocess manufacturers.However, while COTS have givenmany advantages, it has also comewith expensive administration andlife-cycle cost requirements. Abetter approach is to takeadvantage of the cost benefits andopen standards of COTS, but toadd functionality that allows theequipment to function more likeother parts of the system–plugand-play, full lifecycle supportwithout upgrades, built-in security,etc. We call this balance “built forpurpose”, and the DeltaV system isthe first automation system toaddress this critical need in manyof the most important facets of thesystem.Page 3–DeltaV System Overview
I/O on DemandUltimate ScalabilityEmbeddedIntelligent ControlThe DeltaV ArchitectureThe proven PlantWeb digital plantarchitecture helps you detectoperations, process, and equipmentproblems before they even occur,so you can move from reactive toproactive and profitable plantoperations.Page 4–DeltaV System OverviewMaintenanceApplicationStation
InherentlyIntegratedServicesBuilt for PurposeThe DeltaV architectureprovides reliability throughredundancy:n Ethernet network connectionsincluding Virtual I/O Modules (VIM)n Controllersn System powerEngineeringOperationsn Field interface power suppliesn Digital HART I/O and classic fieldinterface cardsn H1 FOUNDATION fieldbus withintegrated power and diagnosticsn Profibus DP Master interfacen Modbus RTU/ASCII interfacen SIS logic solversn SISNet communicationsn Batch Executiven Zone serversn OPC serversDigitalCommunicationsn FOUNDATION fieldbusn HARTn WirelessHARTn Profibus DPn DeviceNetn AS-i busn Modbus RTU/ASCII/TCPn Ethernet/IPn OPC classicn OPC .NET 3.0Page 5–DeltaV System Overview
I/O on DemandUltimate ScalabilityEmbeddedIntelligent ControlFlexibility to give you the I/O you want, when you want it, where you want it.The DeltaV system’s uniqueflexible field architecture deliversI/O on demand–providing the I/Oyou want, when you want it, whereyou want it. It is flexible becauseyou can now decouple the processdesign from the I/O infrastructuredesign, to easily incorporate lateprocess changes into theautomation system.Electronic Marshallingmade easyElectronic Marshalling makesdesign easier and more forgiving,because any input value can beread by any DeltaV controllerregardless of where the wiringis landed.DeltaV Electronic Marshallingeliminates the complexityassociated with marshalling fieldwiring in a control system.Electricians can terminate the fieldwires on terminal strips in thesame way they have in the past,but the cross-wiring from themarshalling panel to I/O cards hasbeen eliminated. This greatlysimplifies control cabinet design,installation, and maintenance.disconnect eliminates the worryover accidentally induced faultsduring hot cutovers andmaintenance.Increased robustnessTroubleshooting of installationissues can be done on a channelby-channel basis, becauseproblems are isolated to a singlechannel–providing increasedrobustness.Because each analog CHARMcomes fully equipped with theability to read HART v7 data,intelligent field devices can bemonitored and quickly diagnosedaround the clock. In addition HARTdata access is quicker with CHARMsthan with traditional I/O cards.Redundancy ensures reliability:n Redundant CHARM I/O cardn Redundant communicationsbetween CHARMS and theCHARM I/O cardn Redundant power betweenCHARM I/O card to each CHARMn Redundant network communications between CHARMI/O cards and controllers.Electronic MarshallingInstallation of ElectronicMarshalling is intuitive and easy,because it is similar to existingmethods for terminating fieldwiring. No special training orexpertise is needed to terminatewiring on the terminal blocks. Anintegrated “knife-edge”Page 6–DeltaV System OverviewTight project schedules withchanging requirements duringdesign and implementation are away of life. DeltaV ElectronicMarshalling lets you land fieldcabling wherever you want,regardless of signal type orcontrol strategy.With Electronic Marshalling, eachterminal block has a channelcharacterization module, orCHARM, which includes signalcharacterization for different typesof I/O. Field wiring of any signaltype can be terminated anywhereand characterized by the variousCHARMs. A digital communicationbus runs along the terminal strip tosend device signal information tothe top, the redundant CHARM I/Ocard, a redundant 96 channelbased multipurpose I/O card,where I/O conditioning iscompleted.CHARM Terminal BlockCHARM
InherentlyIntegratedBuilt for PurposeServicesCHARM I/O Carrier(fiber optic or copper ethernet connectors)CHARM I/O Card(redundant)Channel Identififier(separation wall)CHARM base plate(passive rail carrying field powerand communications)CHARMS(CHARacterization Module)Marshalling CabinetIntegrated CHARMSn CHARM base plate snaps on railn CHARM terminal block snapsinto baseplaten Auto keying sets terminal blockwhen first CHARM is insertedn CHARM secured with lockingmechanism in both operatingand “knife-edge” disconnectpositionsn Insertable/removable underpower in a Zone 2 environmentn Signal fault protection andcircuit protection built inn Single channel fault isolationbuilt inn Can be mixed with IS CHARMsusing a separate baseplate.Intrinsically Safe inhazardous areasThe DeltaV Intrinsically Safe I/OM-series subsystem provides theperfect solution for locating I/O inhazardous areas. The I/Osubsystem connects intrinsicallysafe field circuits and field devicesinto FM Class I, Division 1, Zone 1,and Zone 0 hazardous areas formost standard analog input,discrete input and discreteoutput applications.With the addition of IntrinsicallySafe CHARMs to the S-seriesElectronic Marshalling concept,field wiring to hazardous areas iseven easier. Field devices located inFM Class I, Division 1, ATEX orIECEx Zone 1 or Zone 0 hazardousareas can now directly beconnected to the flexible IS AI andIS AO CHARMs, IS DI NAMUR and ISDO as well to IS RTD and ISTC CHARMs.Late project changes?No problem.Every project has late changes that can havesignificant impact on cost and schedule. Makingthese late changes is now easier, because newfield wiring can be added to cabinets at any timewith no impact on the system architecture.Page 7–DeltaV System Overview
I/O on DemandUltimate ScalabilityEmbeddedIntelligent ControlProven, plug and play–a smart choice for your control system.Traditional I/O is a modularsubsystem that offers flexibilityduring installation. It’s designed tobe installed in the field near yourdevices. Modularity, protectionkeys, and plug-and-playcapabilities make DeltaVtraditional I/O a smart choice foryour process control system.Traditional I/O is available in twodesigns–the established M-seriesand the S-series. The S-seriesincorporates human-centereddesign concepts to improveusability and robustness with thesame proven technology inside.The exterior hardware designdelivers easier installation andimproved robustness.S-series I/O interfaces snap to 8-wide I/O carrier withintegrated 24 VDC bussed field power distribution.Redundant controllers withsystem power supplies on2-wide carriers.Easy snap-in installationInstallation is easy since I/O isautomatically auto-sensed whenadded to the system. No-valueengineering is eliminated.S-series traditional I/O is equippedwith a snap-in retention system forquick installation and error-freemaintenance.A guide prevents bent pins andcards easily snap in to place.Carriers snap onto the DIN Rail–notools required. Snap-in technologymakes cards easy to install withtight connections every time andeasy to release with a push ofa button.I/O cards, terminal interfaces andterminal blocks have I/O functionkeys. This ensures the correct I/OPage 8–DeltaV System Overviewcard is always plugged into itscorresponding terminal block.All wiring is through the carriersand terminal blocks so that I/Ocards and system power suppliescan easily be removed withoutdisconnecting any wires.The DeltaV system supports a fullrange of analog, discrete, digitalbus, thermocouple, and RTD fielddevices.Reliable means availableReliability and increased systemavailability are built in throughoutthe rugged DeltaV controlhardware. Redundancy options areavailable for:n Controllersn System powerRails slide togethereasily and securely.n Field interface powern Controller Ethernetcommunicationsn Many classic field interface cardsn H1 FOUNDATION fieldbusn Profibus DPn Serial interface.Online addition of new I/O cardsmeans your process does not getinterrupted. The DeltaV systemenables you to add systemcomponents including controllers,I/O cards, field devices andworkstations while the system ispowered and running byautosensing the new componentwithout the need of presetting anaddress. This enables you toexpand and upgrade your systemon-the-fly with no downtime.
InherentlyIntegratedBuilt for PurposeThe rugged S-series hardwareincludes a venting system thatprevents screws, metal shavings,and other debris that could shortcircuit electronic componentsfrom entering.Modular design foradded flexibilityBoth the S-series and M-seriestraditional I/O hardware can coexist in the same DeltaV systemwith no trade-offs orincompatibilities.The modular design lets you buythe exact number of I/O cards,8-wide carriers, power/controllers,and 2-wide carriers you need andadd more DeltaV I/O as yoursystem grows.Rugged design for useanywhereServicesalmost anywhere. It is designed forextreme field installationconditions, including:n Class 1 Division 2 areasn CENELEC Zone 2 areasn ISA-71.04-1985 AirborneContaminants Class G3.All DeltaV traditional I/O cards arerated for extreme operatingtemperature ranges of -40 to 70 C(-40 to 158 F). You can mount theI/O interface carrier in a junctionbox in the field, significantlyreducing your equipmentfootprint.Shared remote I/O is available forZone 2 installations. Unlike otherremote I/O, DeltaV remote I/O canbe shared among severalcontrollers for a greater range ofapplications and installationflexibility.DeltaV control hardware is builtrugged and flexible to mountLatched installation deliverstight connections every time.Screw fasteningeliminated.No broken cards dueto over-tightening.Venting systemprevents debris/objectsfrom entering.Guide prevents bent pinsand card snaps in place.With snap-clamps thecorrect tightness isassured. Cards remainsecurely in place.Rugged S-serieshardware addressesyour tou
Part of Emerson's PlantWebTM architecture, the DeltaVTM system is built from the ground up for ultimate scalability. Regardless of your application’s size, the DeltaV system keeps the same look and feel. This reduces administration and training costs, and optimizes both initial investment and future expansions. From bench top, to pilot plant, to