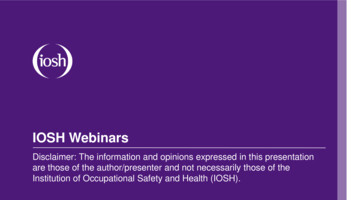
Transcription
IOSH WebinarsDisclaimer: The information and opinions expressed in this presentationare those of the author/presenter and not necessarily those of theInstitution of Occupational Safety and Health (IOSH).
Process SafetyAwarenessBeginner's Guide to Process SafetyIOSH Hazardous Industries and Offshore Groups JointPresentationBy Shailesh Purohit
What do you think led to this incident?
Now Watch this video: Filling blind- This is an incident video of a manualoperation for a typical Oil storageand Distribution facility using nonautomated equipment and manuallevel Checks- What are your thoughts?- What if the level gauges did notread correct?(Courtesy: Chemical Safety Board, USA)4
Filling Blind Animation: Courtesy: Chemical Safety Board US
Objectives of the PSM Awareness (ProcessSafety Management) Training) Define process safetyExplain the difference between OccupationalSafety and Process SafetyDescribe the Ten Pillars of Complianceelements of process safety as applicable to OilStorage & Transfer operationsOutline consequences of Process SafetyfailuresHighlight the key part played by humanfactors (people) in achieving high ProcessSafety standards6
HSE Response to the Buncefield DisasterCourtesy: ITN News
What is Process Safety? Process Safety generally refers to theprevention of unintentional releases ofchemicals, energy, or other potentiallydangerous materials during the course ofchemical processes that can have aserious effect on the plant andenvironment.Process safety involves, for example, theprevention of leaks, spills, equipmentmalfunction, over-pressures, overtemperatures, corrosion, metal fatigueand other similar conditions.Process safety programmes focus ondesign and engineering of facilities,maintenance of equipment, effectivealarms, effective control points,procedures and training.It is sometimes useful to consider ProcessSafety as the outcome or result of a widerange of technical, management andoperational disciplines coming together inan organised way.8
Occupational Safety relates to personal safety of theemployees/ contractors/ visitors however, processsafety refers to the actual operational safety andprevention of long term harm to environment.Taken from ENFORM: The Safety Association for Canada’s UpstreamOil & Gas Industry9
Injuries from poor manualhandling or exposure of anemployee to toxic vapours wouldbe considered under occupationalsafety management.Process safety managementwould refer to fire/ explosion/toxic vapour releases that affectsurrounding population.Taken from ENFORM: The Safety Association for Canada’s Upstream Oil &Gas Industry10
Process safety incident results in a catastrophic event includinglong term pollution. Occupational safety incident would affectpersonal safety of an employee or a few of the colleagues.There is no dividing line between the two types of safety and aconsequence could be attributed to both types.Taken from ENFORM: The Safety Association for Canada’s Upstream Oil & Gas Industry11
Ten Pillars of Compliance Approach toProcess Safety- What are the Ten Pillars of Compliance and how do they relateto Process Safety?List of Ten Pillars of Compliance asfollowed by Competent Authority(HSE EA)1.2.3.4.5.6.7.8.9.10.PILLAR 1 - Safety ManagementSystemPILLAR 2 - Ageing PlantPILLAR 3 - CompetencePILLAR 4 - Safety InstrumentedSystemsPILLAR 5: OverfillPILLAR 6 - Secondary and TertiaryContainmentPILLAR 7 - Internal EmergencyPlansPILLAR 8 – External EmergencyPlansPILLAR 9 - Process SafetyPerformance IndicatorsPILLAR 10 - Safety LeadershipThisHappenedIn UKClips taken from “An Engineer’s View of HumanError- I ChemE - Adventures of Joe Soap”12
PerformanceDescription – 10Strategic PillarsAction RequiredSituationTen Pillars of Compliance Rating as per CompetentAuthorityUnacceptableRed StopDangerous &/or illegalSituationVery PoorPerformanceCease activity and rectify Improvement neededbefore recommencing.within a very shorttimescale – Action planAction Plan forwithin 1 week, signed-offimprovement requiredby relevant Seniorwithin 3 days, signed-off Manager and Lineby CE and relevant LineManager.Manager.None of success criteriamet.Poor StandardAction Plan required to be inplace and being worked onprior to next inspection,signed-off by the relevantLine Manager.Majority of success criteria Many success criteria notnot met or not fully met. met or not fully met.Broadly CompliantGood Standard /PerformanceExcellent level ofCompliance, Standard &PerformanceAttention to detail required. Site has adopted many areasof best practice.Review with site lead howbest to improve the issues Provide positive feedback.and drive forward CIPprojects.Some success criteria notfully met. May not preclude Good practice in mostclose out depending on scope respects. Most successof improvements required criteria met.and operator attitude.ExemplaryBest PracticeSite has adopted bestpractices in all areas withtotal adherence to the SMS.Letter providing positivefeedback issued to all siteemployees signed by the CE.Good practice or above in allrespects. All success criteriafully met.ScorePerformance Description – H&S TermsVery high risk of seriousinjury or fatality.Serious or imminent risk ofMATTEClear breach of legalrequirements / noevidence of systems ormanagement controls ofany kind.Systems and / ormanagement controls notbeing utilised or adheredto.60Performance / systems needfurther improvement toensure effectiveThe performance noted onHigh risk of fatality orPossible environmental LoC management controls inthe site is well beyondserious injury.place and being adhered to. system compliance but it notSome breach of legaldeemed innovation i.e.Possible risk of MATTE.requirements systems notElements of the SMS are not Standard industry bestbeing used on this occasion. being adhered to but the site, practice.Breach of legalor elements of the works,requirements / nowhich is being scored areevidence of systems beinglegally compliant.used in general.Risk of serious injury.50403020Innovation being adoptedacross the businessIndustry best practice inplace.1013
PILLAR 1 - Safety ManagementSystem Evidence of PTW (permit to work) ,Operation & MaintenanceProcedures, Management ofChange, Hazard Recognition &Reduction, Safety Reports, Bow TieReports, HAZOPs, etc.Which of the following disasterswere a result of poor or total lackof management of change?Flixborough 1974 – 28 deadPiper Alpha 1988 – 167 deadBhopal Toxic Gas Tragedy 1984 –Estimated 8000 immediately andup to 20,000 later on and stillaffecting new-bornhttps://www.youtube.com/watch?v HsuUQzhP2DsDo you think your Organisation isgood at managing change? Why?14
PILLAR 2 - Ageing Plant“Ageing is not about how old yourequipment is; it’s about what youknow about its condition, and howthat’s changing over time”.There are well known corrosionmechanisms that EngineeringDepartments deal with daily and takeactions to prevent/ minimise these soas to prevent loss of containment.In case you are wondering whatcauses plant to age, the following areall reasons: Corrosion, stress,erosion, fatigue, embrittlement,physical damage, spalling (degradedconcrete), subsidence, weathering,expansion/contraction due to thermalchanges, instrument drift, dry jointsand detector poisoning.These ageing mechanisms can affectprimary containment such as tanksand pipelines as well as supportingstructures such as pipe bridges andsupports, electrical, control andinstrumentation systems andsafeguard systems.Tank has been decommissioned15
PILLAR 3 – Competence What is your understanding of“Competence”Is it training and experience – abilityto do a task according to standardprocedures? Would you call ability torespond under pressurecompetence?Competency aspect of operating aCOMAH Site includes many otheraspects such as Recruitment,Performance Management. All theseand much more.The ability to carry out safety criticaltasks correctly every time is a keyprocess safety requirement. So,which of the following do you thinkis a “safety critical task”Option 1: Safety induction of visitorsOption 2: Line breaking formaintenanceOption 3: Wearing correct personalprotective equipmentClips taken from “An Engineer’s View of Human Error- I ChemE Adventures of Joe Soap”16
PILLAR 4 - SafetyInstrumented Systems Prevention of loss ofcontainment and fire/explosion is based onreliability of SafetyInstrumented Systems (SIS)An example of suchequipment is shown here.This is a level gauge whichalarms when pre-set levelsare reached and also maytake executive action byclosing inlet valves to preventoverfilling.Another example isInterceptor Pollution Probewhich alarms upon detectingoil and in some cases- alsoshuts the final valve leadingto public water courses.17
PILLAR 5: Overfill Overfill of the tanks is one ofthe most common processsafety events that may lead tofire/ explosion or severeenvironmental contamination.Factors that we must get rightare:People – competent andfollowing route cards everysingle timeUse of Maintenance Systemsto inspect/ proof test all safetycritical plant and equipmentUse of Containment PolicyScore Cards to identifyimprovement areas & SiteImprovement PlansReproduced from CSB IncidentReport on COPECO18
PILLAR 6: Secondary & Tertiary Containment Secondary Containmentrefers to Bunds thatwould catch any loss ofcontainment fromprimary containmentsuch as steel tanks.Concrete Jacketssurrounding the tanksdo not meet the criteriafor secondarycontainment.Tertiary Containmentrefers to containment ofproduct that hasovertopped secondarycontainment and usuallycould be shown asdams/ pools/ lagoons onsiteCourtesy: CIRIA 764 Guidance19
PILLAR 7 - InternalEmergency Plans MAPP: This is Major AccidentPrevention Policy and sets out theframework and commitment of theCompany to prevent MajorAccidents.PIZ: Pubic Information Zones areestablished by the CompetentAuthority based on Safety Reportreviews to provide area surroundingsites where the public must beprovided key emergency informationabout our site and what to do incase of a COMAH alarm soundingExercises: Invite local fireauthorities to the site regularly toconduct annual on-site table top orphysical exercises to keep themupdated and also comply with theRegulatory ExpectationsEmergency Procedures arecontinuously reviewed and updatedas new changes to the site aremade.20
PILLAR 8 – External Emergency Plans: The External Emergency plans areprepared by the Local Authority andhas input from all emergencyresponders such as the Fire Brigade,Police, Ambulance, Public HealthEngland, HSE, Environment Agency,Highways Authority, Water Authorityand so onLiaison Meetings are held regularly withthe Local Council to plan for andexecute External Emergency exercises.These exercises are a legal requirementand must be done every 3 years.At a recent External Emergency Planexercise, over 110 participants invarious roles such as players, observersand umpires at strategic andoperational levels were present. Therewas a hot and cold debrief after theconclusion of the successful exercise.The aim of these exercises is tovalidate the External Emergency Planand continuously improve observeddeficiencies.21
PILLAR 9 - Process SafetyPerformance Indicators - From HSG 254: Developing Process SafetyPerformance IndicatorsProcess Safety PerformanceIndicators (PSPI) provide assuranceto the stakeholders that processsafety issues are being managed toprevent catastrophic incidents.Typically, these are risk controlbarriers such as OperatorCompetence, OperationalProcedures, Management ofChange and Permit to Work and soon.These can be pro-active whichindicate good practice such asplanned preventive maintenancetasks or reactive which could benumber of loss incidents. They areboth useful in terms of continuousimprovement in process safety onsites.Can you think of what else wouldbe a good process safety indicator?22
PILLAR 10 - SafetyLeadership Behaviour & Culture:Process Safety leadershipis a must for anysuccessful Organisationand Senior LeadershipTeam (SLT) sets thestandard by personalcommitmentO & M TeamEngagement: SeniorLeadership Team (SLT)site visits to engage withlocal staff, carry out twoway conversations tounderstand theirconcerns and promoteProcess Safety Issues onsites.23
Summary To recap, Process Safety is different as compared toOccupational Safety.Process Safety relates to safe operation of the plant tominimise the potential for fire/ explosion and/ orsevere environmental contamination.Process safety management involves a lot of differentaspects where competency of the operators,understanding of control measures, understandingwhat to do in abnormal process conditions, safetycritical maintenance are some of the key issues thatmust be managed by all employees and managementto ensure safe operation of the plant.24
I could have saved a life today – but I chose tolook the other way
Final Thoughts: I CHOSE TO LOOK THE OTHER WAYA poem by Don MerrillI could have saved a life that day,But I chose to look the other way.It wasn’t I didn’t care;I had the time, and I was there.But I didn’t want to seem a fool;Or argue over a safety rule.I knew he’d done the job before;If I spoke he might get sore.The chances didn’t seem that bad;I’d done the same, he knew I had.So I shook my head and walked on by;He knew the risks as well as I.He took the chance, I closed an eye;And with the act, I let him die.I could have saved a life that day,But I chose to look the other way.Now every time I see his wife,I know I should have saved his life.That guilt is something I must bear;But it isn’t something you need share.If you see a risk that others take,That puts their health or life at stake,The question asked or thing you say;Could help them live another day.If you see a risk and walk away,Then hope you never have to say,“I could have saved a life that day,But I chose to look the other way”Written after an actual eventh
Process safety incident results in a catastrophic event including long term pollution. Occupational safety incident would affect personal safety of an employee or a few of the colleagues. There is no dividing line between the two types of safety and a consequence could be attributed to both types. Taken from ENFORM: The Safety Association for Canada’s Upstream Oil & Gas Industry 11. Ten Pill