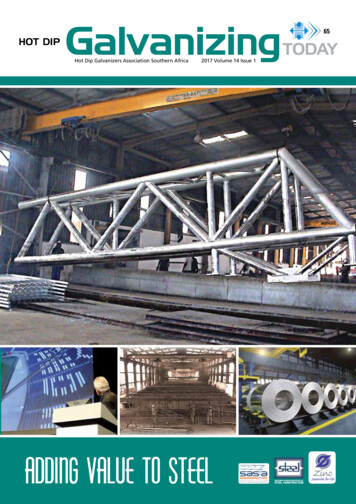
Transcription
Galvanizing today65hot dipHot Dip Galvanizers Association Southern Africa2017 Volume 14 Issue 1ADDING VALUE TO STEEL
Galvanizing today65hot dipHot Dip Galvanizers Association Southern Africa2017 Volume 14 Issue 1Official journal of the Hot Dip Galvanizers Association Southern AfricaISSN 1023/781XContents22Advertisers’ IndexRegulars2Executive Director’s Comment24Personality Profile2focus on2Intergalva 2018 Update6Phoenix GalvanizingTechnical12Zinc, zinc-aluminium and duplex coated sheeting14Durability of hot dip galvanized sheeting exposed to generalatmospheric conditions16History of zinc, its production and usage (Part 2)6education and training21Courses offered22UJ students introduced to hot dip galvanizing22Training courses9general92016 Hot Dip Galvanizing Awards10Devland Soweto Education Campus22Malcolm Wilson202017 Golf Day1024The Association is an information centre established for the benefit of specifiers, consultants, end users and its members.Published by:Hot Dip Galvanizers Association Southern AfricaBedfordview Office Park, Building 2, Ground Floor, 3 Riley Road, GermistonP.O. Box 2212 Edenvale 1610 Tel: 011 456 7960 Fax: 011 450 0728 Email: hdgasa@icon.co.za Website: www.hdgasa.org.zaExecutive Director:Publication Liaison:Robin Clarke Cell: 082 909 5119 Email: robin@hdgasa.org.zaAnthony Botha Cell: 076 440 2793 Email: anthony@hdgasa.org.zaAdvertising and Sales:Anne van Vliet Tel: 011 462 5073 Cell: 082 775 0711 Email: anne@communiquepr.co.zaRichard van Vliet Cell: 076 299 3471 Email: rvanvliet076@gmail.comSandra Addinall Tel: 011 868 3408 Email: cbtdesign@adcot.co.zaCamera Press Tel: 011 334 3815 Fax: 011 334 3912 Email: cpress@iafrica.comDesign and Layout:Reproduction and Printing:Views expressed in articles and advertisements are not necessarily the views of HDGASA. Articles or extracts thereof may be reproduced providedfull acknowledgement is given. Should you wish to receive a regular copy of the magazine, kindly contact usVolume 14 Issue 1 2017 Hot Dip Galvanizing Today1
COMMENTExecutive Director’sHeadingCommentWelcome to the latest edition of HotDip Galvanizing Today.There are various mechanismsthrough which the Hot DipGalvanizers of Southern Africamarkets and promotes the use ofhot dip galvanizing as a preferredtechnology for corrosion control ofsteel and iron components.One of the most important activities centers around “spreadingthe word” through education. The Association is able to tailorcourses to suit the needs and requirements of any interestedparty. Such courses or presentations may range from one-dayseminars to our universally recognized “level two” course.This course has, with minimal tailoring for local consumption,been adopted for training in both Brazil and Spain. TheIntergalva 2018UpdatePreparations are already well advanced for the 25th InternationalGalvanizing Conference – Intergalva 2018 – to be held at the EstrelHotel, Berlin, 17 to 22 June 2018. This ‘must-attend’ event forthe worldwide galvanizing industry includes conference sessionsthat cover technical, commercial and environmental topics and isaccompanied by an extensive exhibition of equipment, services andmaterials for the industry.The Intergalva series began as long ago as 1950 and was last held inLiverpool in 2015 (see issue Volume 12 Issue 2 2015). The 2018 eventis organised by European General Galvanizers Association (EGGA) andhosted by Industrieverband Feuerverzinken. The 3-day conferencelevel two course is aimed at qualifying inspectors to performprogramme with simultaneous translation planned in German, Italian,inspections relative to appropriate SANS/ISO standards forSpanish, French, Polish, Chinese and Japanese languages. Participantsbatch, continuous, spin, wire and fastener galvanizing. Thewill include owners, operators and managers of galvanizing plants;Level 2 course carries accreditation for the awarding of threeusers of galvanized products; corrosion specialists; suppliers ofCPD points.equipment and services to the galvanizing industry and suppliers ofzinc and zinc alloys.All courses have a broadly similar structure, this being: The fundamentals of corrosion How zinc protects Standards and methods for predicting service life of Hot dipBerlin is Germany’s top tourist destination – with three UNESCOWorld Heritage sites and 180 museums. It also has a reputation for a‘great for a night out’ with over 11 200 restaurants, 2 300 bars and200 different performance stages in the city.galvanized components Standards and methods for the inspection of Hot dipgalvanized componentsA ‘Call for Papers’ has recently been launched with proposals soughtin these topics: Market and product development – including coating durability;The Association website carries comprehensive details relating tonew applications in bridges, concrete reinforcement and otherthese courses, as well as target dates and venues for 2017.sectors; coating technology.The Association has watched with interest one of the heaviest Process technology – including plant design; kettle management/cost drivers in the galvanizing industry worldwide, namely theprice movement of Zinc.The price of zinc escalated by approximately 30% in the periodJune 2015 to July 2016. The following 6 months to year end2016 saw a further 11% increase. Drawing from research ofthe Lead and Zinc study group as well as the USA researchconsultancy CRU, this price phenomenon has arisen primarily asa result of decreasing zinc concentrate levels due to mines beingclosed or mothballed. Whilst a global “inventory overhang”exists there is decreasing gap between stock of refined zincand production of the concentrate. This trend is predicted tocontinue until, in the medium- term, mining activity is increasedto restore concentrate levels to match market demand for zincconsumption.Robin Clarke2Hot Dip Galvanizing Today Volume 14 Issue 1 2017The Brandenburg Gate (German: Brandenburger Tor) is an 18th-century neoclassicalmonument in Berlin, and one of the best-known landmarks of Germany.
FOCUS ONlife; flux and degreasing technology;innovative use of galvanized steel bydelegate fee when registration opens inpost-treatments; bath alloys.architects, engineers and steel constructorsDecember 2017. A discount code will be(see https://www.intergalva.com/awards/).provided by the association and should beimprovements in environmentalHDGASA members will be able to registerused during the online registration process.performance; operational safety; materialas delegates to Intergalva 2018 at a reducedAnother benefit of membership! Environment and safety – includingefficiency. Regulatory status – including regulatoryissues affecting markets/applications;future evolution of environmentalcontrols on processes. Sustainable development –galvanizing’s contribution to meetingthe goals of sustainable building andmaintaining the value of infrastructureassets. Galvanizing in architecture –applications in building and construction.The deadline for submissions is 1 July 2017and accepted papers will now be notified by1 November 2017.A feature of Intergalva 2018 will be theGerman galvanizing plant.opportunity to visit some of Germany’sleading and most technologically-advancedgalvanizing plants. The programme of visitshas already been drafted and will include 14plants spread across the country. In additionto visits around the Berlin area, delegateswill be able to plan their trip to Intergalva2018 to include 2-day visits on 21/22 June2018 to the areas of Munich, Cologne orBremen that will include a chance to dosome sightseeing alongside the visits to theplants.A briefing session for major exhibitorswas already held at the Estrel Hotel on8 February 2017 – to demonstrate theexhibition facilities and the opportunities forExhibition stands for galvanizing equipment.large-scale displays of plant and equipment.The floor plan and exhibition sales will beavailable from mid-2017. With the FIFA2018 World Cup taking place during theevent, large TV screens and refreshmentswill likely feature in the exhibition boothsand the exhibition will be open through theevening to create a ‘fan zone’ atmosphere!Intergalva 2018 will also continue the shortworkshops that were new for the 2015event. Consultations will start very soon,through an online survey and LinkedIndiscussion, to identify the workshop topics.During 2017, the entry process for theGlobal Galvanizing Awards 2018 will start.These awards will be held in conjunctionwith Intergalva 2018 – to recognise the4Hot Dip Galvanizing Today Volume 14 Issue 1 2017Exhibition booths for process and product exhibitors.
FOCUS ONPhoenix Galvanizing celebrated 20 years inbusiness in 2016Phoenix Galvanizing – KZN’s largest hot dipcommission and build the largest hot dipremain at the helm as part of the company’sgalvanizer celebrated its 20th anniversarygalvanising plant in KwaZulu-Natal. Phoenixteam of directors, who together have grownin September of 2016. Phoenix GalvanizingGalvanizing became a reality when thePhoenix Galvanizing into a household nameranks among the galvanizing industry’sfirst dip took place on September 6, 1996.that still boasts the status of being thesignificant players. The company had ratherSignificantly, the first item ever to be hot diplargest hot dip galvaniser in the province.humble beginnings. Phoenix Galvanizinggalvanized was a Hindu Aum sign.Phoenix Galvanizing boasts a moltenwas launched in 1996 by entrepreneurialbrothers, Roy and Anni Ramkisson. TheyIn addition to its size and capacity, Phoenixzinc tank, or kettle, 14 metres in length,were in the steel fabrication business atGalvanizing was also ground breaking in2.5m deep and 1.4m wide. It has a totalthe time, specialising in domestic andthat it was the first fully non-white ownedzinc capacity of 330 tons of molten zinc,industrial steel security products whenand operated hot dip galvanising businesswhich is maintained at a temperature ofthey identified a niche in the market for ain South Africa. “The opportunity to venture450 degrees Celsius. The zinc kettle wascompany that could provide local, qualityinto new territory was largely due to thedesigned to accommodate some of thehot dip galvanising. Armed just with theirdawn of the new democracy in 1994, withlargest single pieces of steel fabrication.passion, drive and determination to build athe late Madiba taking office as the firstbusiness that could make a difference andblack President of South Africa,” explainsThe costs of fabrication as well as thestand out from the rest, they proceeded toAnni Ramkisson. He and his brother, Roy,onsite construction costs are reduced whenlonger and wider sections are manufacturedas a single piece and subsequently hotdip galvanized as one large article offabrication.Phoenix Galvanizing’s large tank enables notonly significant operational efficiencies andproductivity advantages, it also affords itscustomers significant cost savings overall.Phoenix Galvanizing strives for the highestlevel of professionalism and service byusing its facilities, innovation, businesscharacteristics and strategies to provide thecustomer with a competitive advantage notavailable anywhere else in KZN.Phoenix Galvanizing has a passion for thecustomer service and streamlined businessprocesses which drive their uncompromisingservice in KZN. Their highly efficient andproductive 24-hour operation enablesAerial view of Phoenix Galvanizing.delivery at industry-leading turnaroundtimes. The combined experience andexpertise of the team provides forconsultative input on special projects fromthe design stage which have includeduShaka Marine World’s award-winningPhantom Ship, Moses Mabhida Stadium andthe King Shaka International Airport as wellas numerous Transnet projects.Phoenix Galvanizing’s large, fully-servicedand secure yard space of around 6 000m2in laydown space is made available tocustomers to store their steel productsDirectors (from left to right): Ron Ramkisson( Fin. Dir); Roy Ramkisson (CEO); Yashira Ramkisson (Dir: Ops & QS);Ashish Ramkisson (Dir: Ops & Maint); Anni Ramkisson (MD); Amish Ramkisson (Dir: Sales & Mkt).6Hot Dip Galvanizing Today Volume 14 Issue 1 2017free of charge during the period betweenfabrication and hot dip galvanizing.
FOCUS ONPhoenix Galvanizing also offers fullcontainerisation services that include all thenecessary pre-load quality checks, correctloading of the galvanised products into thecontainer and the transport of the containerdirectly to the harbour for export.Dedicated transport facilities collectingfabricated steel at the point of manufactureby Phoenix Galvanizing offers customers acombined service that can also be used todeliver the finalized galvanised steel to site.The fleet consists of vehicles that vary in sizefrom one-ton bakkies to 24-ton horse andtrailers.Phoenix Galvanizing has a depot in PortShepstone, where steel is dropped off bycustomers and delivered back to the clientwithin 48 hours.Phoenix Galvanizing dedicated transport service fleet.Here, small items are galvanised in a smallerbeen a member of the Hot Dip Galvaniserszinc tank and spun to remove excess zincAssociation of Southern Africa sincefrom the articles. The centrifuge plantinception and complies with all aspects ofspecialises in threaded sections, includingthe associations standards and codes beingPhoenix Galvanizing’s transport servicesare available on a daily basis to the northcoast as far as Richards Bay as well asto the Midlands covering Howick andPietermaritzburg.the galvanising of nuts and bolts.a responsible corporate citizen.Phoenix Galvanizing takes its marketComing from a disadvantaged background,status seriously being an accredited LevelAnni and Roy have always placed great2 B-BBEE company and holds both SANSemphasis on sharing their success by givingPhoenix Galvanizing boasts the only hot9001:2008 (Quality Management Systems)back to the local community and supportingdip galvanising centrifuge plant in KZN.and SANS 121:2011 certification. It haslocal charities. Among the many causesVolume 14 Issue 1 2017 Hot Dip Galvanizing Today7
FOCUS ONit supports are the Verulam Frail and DayCare Centre, Phoenix Child Welfare and theMariamman Temple in Mount Edgecombe.Phoenix Galvanizing actively fundraisesfor by arranging events such as golf daysand sponsoring special annual events. Thedirectors are also patrons of Duffs RoadChild Welfare, and each year, the companyhosts the packing of Diwali hampers for theunderprivileged. The directors of PhoenixGalvanizing also spearhead the building ofthe Phoenix Community Hospice and DayCare Centre. The project is progressingwell, with the hospice board memberssuccessfully achieving the required PBOnumber.For the directors behind PhoenixGalvanizing’s 20-year success story, thissignificant achievement is all about thelegacy they have built in a unique fieldZinc plant kettle.this success. We are also immensely proudwhile some have even been on board sinceof the fact that we have been able to buildits inception.a business that provides people with reliableemployment and a means by which they“We understand that Phoenix Galvanizing’scan improve their lives,” says Anni.achievements have been as a result of thecollective effort of the people who make upthat was historically predominantly white-8dominated prior to their arrival. “As theThis focus on employee welfare, trainingthe company – and we remain passionatedirectors, we have always been passionateand skills development has paid dividendsabout continuing to do business thisabout this business and are proud of thein the form of high staff retention. In fact,way,” he concludes, “As a result, Phoenixhands-on approach we have followedabout 40 percent of employees have beenGalvanizing looks set for even furthertogether with our staff members to createwith the company for more than 10 years,success well into the future.”Hot Dip Galvanizing Today Volume 14 Issue 1 2017
2016 HOT DIP GALVANIZING AWARDS2016 HOT DIP GALVANIZING AWARDSAdvanced Galvanizing team: Denzil Clifford (Prod Mgr); Sim Swart (GM) andJohan Louw (MD).Charlene and Robert Bossert.The 2016 Hot Dip Galvanizing Awards held at Thaba Eco Hotel inThe next Hot Dip Galvanizing Awards will be held in 2018 giving allstakeholders and disciplines involved with galvanizing and the useof galvanized steel plenty of time to enter their submissions. TheHDGASA would like to thank all parties who made the event possiblefrom our Platinum Sponsor – Columbiana Boiler Company to the GoldSponsors – Monoweld Galvanizers and Transvaal Galvanizers to ourSilver Sponsors – Lianru Galvanizers and METSEP. The HDGASA hasexpressed a special “Thank You” to Charlene Bossert, who managedthe project in support of the HDGASA team and without whom theevent would have been an arduous task.Klipriviersberg Johannesburg in November 2016 was a splendidsuccess and justifiably the highpoint of the galvanizing industry’syear. Winners were acknowledged for excellence in their respectivecategories. The overall winner, as judged by the HDGASA panel, was‘The Boomslang’ at Kirstenbosch Botanical Gardens in the WesternCape. Officially named ‘The Centenary Canopy Walkway’ theproject and all the stakeholders were recognized for the exceptionalengineering of a superb engineering feat.Volume 14 Issue 1 2017 Hot Dip Galvanizing Today9
NEWSDevland Soweto Education CampusA collaborative development CommunitySocial Investment (CSI) project managedby Growing Up Africa (GUA), is currentlyconstructing an educational campus inSoweto funded by more than 60 partnercompanies. The HDGASA was contacted,by Monoweld Galvanizers (MWG), toassist GUA regarding corrosion control ofseven brackets that had been cast into theconcrete superstructure prior to galvanizing.MWG have galvanized the majority ofbrackets and columns for this project attheir facility in Germiston.The project broke ground in February2014 and has been the proving ground formore than 200 national and internationalRobin Clarke Executive Director, HDGASA withDeborah Terhune of Growing Up Africa.Columns and brackets galvanized by MonoweldGalvanizers.and Structural Engineering to Architecturetime on site experience of each student isand an ongoing program of knowledgeand Industrial Engineering. GUA liaisesachieved to the benefit of all stakeholders.exchange with these future decision makersclosely with the universities and mentoringLectures relating to the project have beenanticipates at least twice as many will beorganizations to ensure practical real-presented to more than 800 studentsthird year university students and newgraduates in disciplines ranging from Civilexposed to the numerous aspects of theproject.The HDGASA team met with GUA founder,Deborah Terhune and Dimakatso Rampediaka ‘DK’, a third year Civil Engineeringstudent, at site to discuss the options forcorrosion control of the non-galvanizedbrackets. The brackets, having been castinto the concrete super structure, couldno longer be hot dip galvanized therebylimiting corrosion control options. TheHDGASA preferred recommendation wasto apply zinc metal thermal spray, with aminimum mean coating of at least 100µm.This approach would ensure both barrierand galvanic corrosion control, ensuringa long service life, of these importantstructural elements.The HDGASA is eager to continuesupporting this project and similaractivities that engage and develop futureprofessionals in our arena of corrosioncontrol. The HDGASA will presentworkshops on hot dip galvanizing tothe students and support the transfer ofpractical implementable corrosion controlknowledge in this venture and others like it.10Hot Dip Galvanizing Today Volume 14 Issue 1 2017
TECHNICALZinc, zinc-aluminium and duplex coatedsheetingDefinitionsproduced or stored within a building and/ orestablished that thickness for thickness,Coil coated sheeting: Thin gauge steelthe presence of corrosive fumes produced asthe Galvalume type coating providessheeting produced in coil form, which isa result of various manufacturing activitiesa corrosion resistant coating betweensubsequently de-coiled, passed through afor which the building is used.two to four times that of pure zinc butwith less cathodic protection and withcontinuous metal coating processing lineand then re-coiled.The metal coating systems available for thethe inherent problem of aluminium inprotection of steel sheeting fall into threemain categories:contact with alkalis such as cement.Duplex coil coated Sheeting: Coil coatedsheeting which is provided with an organicAluminium and zinc are described asamphoteric metals in that they react1. Zinc-aluminium alloy coated steelpaint coating over an initially applied metalaggressively at both low and high pHsheetingcoating.levels. This is in contrast to steel whereWhen it was recognized that aluminiumWhile hot dip galvanized profiled roofin zinc increased its corrosionsheeting has performed very well for manyresistance, the steel industry developedyears both in Southern Africa and abroad,a coating alloy consisting of 55%other protective coating systems have beenaluminium, 1.5% silicon and the restdeveloped which may in many applicationszinc. This product was first producedprovide a possible cost effective corrosionby Bethlehem Steel Company andcontrol alternative.marketed under the name Galvalumethe corrosion rate decreases as the pHincreases. Aluminium is tolerant downto pH levels of 3.6 while above pH 8.6 itcorrodes. The equivalent range for zincis from about pH 5.5 up to pH 12.5.The 55% Al –Zn alloy provides goodperformance under paint, good ductilityand subsequently Zincalume.and reasonable edge protectionThe first step in selecting a coating systemfor a structure, is to understand and assessCompetitive product is now producedalthough hot dip galvanized sheet hasthe degree of corrosion attack likely toby other manufacturers under namesbeen shown to have still better edgebe encountered in service. This will besuch as Alugalva, Aluzinc, Algafortprotection, particularly on sheets moreinfluenced to a large extent by environmentaland Zalutite. The coating is applied onthan about 1.5mm thick. Likewise,conditions which are broadly described asnon-oxidising continuous anneal hot dipthe galvanized zinc coating has betterCoastal Marine (very aggressive corrosion-coating lines to a wide range of strengthductility properties.*CX), Industrial (aggressive corrosion-*C4levels.Figures 2, 3 and 4 provide the results ofor C5) and Rural (benign to moderatelya) Corrosion resistancecorrosive – *C1 to C3).[* Ref ISO 9223].Relying on long term atmosphericon hot dip galvanizing, Galvalume (55%A further factor to consider is the extentexposure tests (accelerated laboratoryaluminium) and hot dip aluminiumto which corrosion inducing chemicals aretests are unreliable), it has beencoated sheets. The latter aluminiumCorrosion loss, Microns ( umeGalvalume55Galvalume5Aluminium-coated type 200246 8 10 12Exposure time, years14Figure 2: Corrosion performance ofgalvanized, aluminium coated andGalvalume sheet in a severe marineatmosphere.12long term atmospheric exposure testsHot Dip Galvanizing Today Volume 14 Issue 1 201700246 8 10 12Exposure time, yearsFigure 3: Corrosion performance ofgalvanized, aluminium coated andGalvalume sheet in an industrialatmosphere.1400246 8 10 12Exposure time, yearsFigure 4: Corrosion performanceof galvanized, aluminium coatedand Galvalume sheet in a ruralatmosphere.14
TECHNICALcoating is more expensive and it is notreliable indication, the mean coatingtype of organic coating selected will varyavailable commercially in RSA.thickness per side of the 55% aluminiumdepending on the corrosive substancescoated sheet is 14µm compared withpresent in the atmosphere (e.g. marineThe excellent performance of Galvalume19µm per side of Z275 galvanizedor chloride attack and industrial SO2 acidin the industrial atmosphere (SO2material (137.5 g / m2 19µm).attack).pollution) is clear indication of the abilityof aluminium to withstand corrosionb) Zincalume Resin Coated Steel c) GalfanUnlike other types of steel roof sheeting,Galfan is a 5% aluminium, 95%this can be easily prepared and coatedZinc coating with a small amountWhen extrapolating these exposure testduring or immediately after installation.of mischmetal. In this particularresults with a view to reliably predictingCorrosion “duplex theory” states thatapplication, mischmetal (a speciala maintenance free service life, it isthe combined life of a zinc containingmix of various “rare earth metals”) isimportant to take into considerationcoating plus a matched organic coatingrequired to promote effective bondingthe original as applied coating thicknessapplied early in the life cycle of thebetween the steel substrate and theprior to exposure. Specifications forsheeting, will be considerably longermetal coating. It has become a standardcoated steel sheet define the requiredthan the sum of the lives of the twoproduct in many countries for the wirecoating by mass expressed as the sum ofproducts when used separately.industry and it is being processed inattack down to relatively low pH levels.ever increasing quantities by the steelthe coating on both sides of the sheetin g/m2. This can lead to confusion,Therefore the best protection andcoil coating industry. Galfan is alsoparticularly if a less dense aluminiumhence, life of this type of roof sheetingsuccessfully used to coat steel tubing.containing coating is being evaluatedwill be assured by applying a suitableagainst a normal zinc coating. As acoating early in the life of the roof. TheThis coating is more ductile than the55% aluminium alloy which is one ofthe reasons why it has been developedDurability of hot dip galvanizedsheeting exposed to generalatmospheric conditionsfor protecting wire. Cathodic protectionprovided by Galfan is more or less thesame as that for galvanizing, whilegeneral resistance to corrosion is saidto be up to twice that obtained frompure zinc. Galfan performs extremelywell in coastal marine atmospheresThere is no doubt that in order to optimise the service life of the sheeting on abut understandably the 55%building in any environment, a factory painted galvanized steel sheeting system isaluminium alloy is superior in industrialpreferred. Alternatively, the zinc coating on the sheeting could be over coated withenvironments.a suitable paint system preferably shortly after the building is erected. The latteralternative requires a comprehensive coating and application specification and theTests undertaken in Belgium indicateservices of a skilled applicator to successfully apply the paint.that the performance of Galfan inburied conditions is considerably betterDuplex coating technology suggests that the combined life of the zinc coating andthan that obtained from the 55%the paint coating can be multiplied by a factor of between 1.5 and 2.7, dependingaluminium coating. The Galfan coatingon the conditions at hand.is generally thicker due to the presenceof Zn/Fe alloys in the coating structure.However, an elaborate duplex coating system is only necessary if the service liferequired by the sheeting is indeterminable and the additional costs are considerednegligible.If on the other hand, the required service life is determinable such that the overalllife of the sheeting is required to be say 15 to 20 years in a C1 to C3 environment,making use of a Z275 class of coating, would be appropriate. Z275 has a nominalcoating thickness of about 20µm.2) Continuously hot dip galvanizedsheetingThe coating applied by this processconsists almost entirely of pure zinc witha trace of aluminium (about 0.02%)added to the zinc melt. The coating isductile and provides excellent cathodicprotection at uncoated edges andSimilarly, if a 35 to 40 year service life in a C1 to C3 environment is required, asurfaces where coating damage hasZ600 class of coating would be appropriate. Z600 has a nominal coating thicknessoccurred.of 43µm.Hot dip galvanized roof sheetingMaking use of inappropriately coated roof fixing screws or a possible futureis available in a range of coatingvariance in the local micro-climatic conditions over the prescribed life of theclassifications, the most available ofsheeted project, can negatively influence the corrosion rate and hence shorten thewhich are three zinc coating grades:overall service life of the sheeting. Z275 (137.5 g/m2 per side) meancoating thickness 19µm14Hot Dip Galvanizing Today Volume 14 Issue 1 2017
TECHNICALin moderately corrosive environments.Coil coated sheeting is an excellentWhen this coating is used in corrosivechoice for vertical cladding of acoastal marine or heavily pollutedbuilding and other high visibility areas.industrial applications, duplex protectionIf correctly installed, it will provideby means of an organic paint coatingexcellent durability both inland and inThese are distinguished by the mass ofis recommended. Painting should takecoastal marine environments, otherzinc present per square metre of sheetplace sooner rather than later in order toavoid an accumulation of zinc corrosionthan in the aggressively corrosive zonesurface. Z450 (225 g/m2 per side) meancoating thickness 32µm Z600 (300 g/m per side) mean2coating thickness 43µmproducts on the zinc surface which maySince the life of a zinc coating is morebe difficult to remove prior to painting.or less proportional to its thickness inFor optimum corrosion free life as wella given environment, it follows thatas for aesthetically pleasing architecturalthe Z600 zinc coating will providepurposes, duplex coating is alsomore than twice the maintenance freerecommended in environments wherelife available from the Z275 coating.moderately corrosive conditions pertain.The long term atmospheric exposuretests depicted in figures 2, 3 and 43) Duplex coil coated sheetingwhich, depending on land contours andprevailing wind direction, is more or less
450 degrees Celsius. The zinc kettle was designed to accommodate some of the largest single pieces of steel fabrication. The costs of fabrication as well as the onsite construction costs are reduced when longer and wider sections are manufactured as a single piece and subsequently hot dip galvanized as one large article of fabrication.