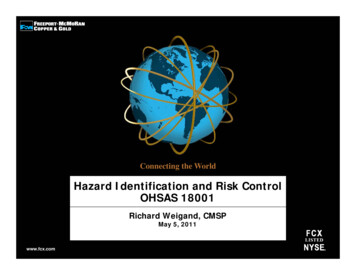
Transcription
Connecting the WorldHazard Identification and Risk ControlOHSAS 18001Richard Weigand, CMSPMay 5, 2011www.fcx.com
Presentation Topics OHSAS 18001 Health and Safety Management System- Hazard Identification- Workplace Examinations (Compliance)- Roles and Responsibilities for Supervisor’s- Risk Assessment and Determination of Controls- COPPER Vision- Engaging our people Results
OHSAS 18001 Occupational Health and Safety Assessment Series (OHSAS)18001. OHSAS is our next step in the Health and Safety evolutionprocess because -Outlines the requirements of an Occupational Health and Safety ManagementSystem from being good to a World Class organization.-Enables an organization to control its OH&S risks by setting up the guidelinesto implement, maintain and continually improve an OH&S managementsystem.
OHSAS – PDCA Cycle Set goals (Plan)Educate and trainworkforce (Do)Check progress (Check)Improve (Act)PLANACTThe management systemidentifies significant risksand implementsdocumented proceduresand training to manage andminimize those risks.DOCHECK
Workplace Examinations 30 CFR 56.18002 Examination of working places. (a) A competent person designated by the operator shall examineeach working place at least once each shift for conditions which mayadversely affect safety or health. The operator shall promptly initiateappropriate action to correct such conditions. (b) A record that such examinations were conducted shall be kept bythe operator for a period of one year, and shall be made available forreview by the Secretary or his authorized representative.
Identifying Electrical HazardsWhich one startswhat?
Identifying Electrical Hazards Grounding togrid Brush/weedfree Grounding ongate Locked gate
Identifying Guarding HazardsIf you see aguard on theground youbetter see thepiece ofequipmentlocked out.
Expectations for Supervisors Ensure each work area is being examined.Ensure competent persons are assigned to examine work areas.Ensure employees know what to look for:- How would they know?- Have Supervisors show them in the field.- Talk is cheap – action in the field works.- Check the quality of inspections every shift.Ensure employees know how to respond when concerns are identified:- Fix it immediately or prevent exposure by flagging /barricading area off.- Call the Supervisor immediately if it cannot be fixed immediately.Ensure your employees turn in their workplace exams and keep the recordfor one year.Ensure that all concerns identified have been resolved (flagged off, workorders, etc).
Workplace Exams – Trust but Verify!
Risk Assessment and Control Freeport-McMoRan Bagdad has identified 720 tasksperformed on a routine basis. Risk assessments have been conducted using thesecriteria:- What hazards may be created?- What is the “potential” consequence of the hazard?- What is the likelihood of occurrence without controls?(Pure Risk)- Review effectiveness of existing controls. (Hierarchy)- What is the likelihood of occurrence with our existingcontrols?- What else can we do? (Continuous Improvement)
Risk Matrix Used
Risk AssessmentsSite: Bagdad OperationsEvaluation Team:Department: Mine Maintenance - Small Vehicle ShopSupervisorJob Tasks: All JobsTrainerDate:Revision:EmployeeGroupSmall Vehicle ShopSmall Vehicle ShopSmall Vehicle ShopNumberExposed222TaskHazardsType ofHazardFumes, Dust, or MistExposureHealthSlip or TripPinch PointsSafetySafetyTroubleshootand ReplaceAlternator or Heat Surface or ObjectBatteryElectricalExplosionUneven fetyFumes, Dust, or MistExposureSlip or TripHealthStruck BySafetyPinch PointsRepair Brakes Falling ObjectsSafetySafetySafetyStored EnergySafetyFumes, Dust, or MistExposureSlip or TripHealthFatigueHeat Surface or ObjectStored Energy(4) Weekly(3)Significant9(5) Daily(1) ntrolsLikelihoodConsequence(probability or(Outcome of Hazardfrequency) ofRatingevent) withevent withcontrolscontrolsTraining - SOP JSA - OTJSafetyInexperienced PersonnelStruck ByVehicle ServiceA/C Repair Pinch PointsInexperienced PersonnelConsequence (OutcomeFrequency ofHazard Exposureof event)taskRating Judgmentwithoutcontrols(2) Quarterly (2) Moderate4PPESpecial Tool Serpentine beltUnacceptabl wrencheTraining – SOP –JSA - OTJEngineering Controls- LOTOTO,Communication Rework meetingWork OrderAcceptable Workplace HazardExaminationSpecial tool /equipmentTraining – SOP –JSA -OTJEngineering Controls- LOTOTO,Communication Rework meetingUncertainWork OrderWorkplace HazardExaminationSpecial tool / equipment(2) Possible(2) Moderate4(2) Possible(1) Minor2(2) Possible(1) Minor2
Lessons Learned It was found that with minimal training employees can quicklyidentify unacceptable risks. Safety focused conversations/exercises in conjunction withtraining are effective. Employee input and participation are the cornerstones in thedetermination of effective controls.
COPPERFreeport-McMoRan Bagdad Health & Safety andEnvironmental Vision“COPPER” acronym Simplified Vision Easier to remember Employee ownership Promotes our values Employee commitment
Health and Safety VisionComply with Health and SafetyRequirementsOn and Offthe Job ateHazardsRelationship with Stakeholders
00.60.6 110.50.60.790.780.6 80.780.870.860.8 760.8541.2321.81.011.681.51.27 41.411.051.140.880.750.81.51Mar2. 522.133. 53JanFreeport-McMoRan Bagdad TRIR2009 to Current Rolling Average w/Contractors54.54200920102011
Presentation Summary Any Questions? Thank You for your Attention and Participation.
18001. OHSAS is our next step in the Health and Safety evolution process because - Outlines the requirements of an Occupa tional Health and Safety Management System from being good to a World Class organization. - Enables an organization to control its OH &S risks by setting up the guidelines to implement, maintain and continually improve an OH&S management system. OHSAS – PDCA Cycle