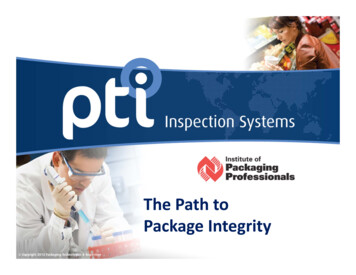
Transcription
The Path toPackage Integrity
Outline Package integrity logic and thought process.Establishing quality standards.Evaluation of common methodologies.Alternative methodologies.Driving forward with package integrity solutions.
Package Integrity Package Integrity –maintaining a sterile barrier. Package integrity is a sub‐category of quality and isexclusive of: Peel Strength Burst Testing Visual InspectionPackageIntegrityPackageQuality
Implications of Integrity Deviations Transfer of environmental contaminants. Release of critical ingredients/flavors. Synergistic effects of contaminants (O2,H2O, Bacteria). Defects that will progress to leakage.
How to discuss integrity? What is important to your customer? What is important to the product? What is Important to the package?Integrity can be defined.Level of assurance is open to discussion.
Six Sigma Framework ‐ DMAIC Define Measure Analyze Improve Control
Foundation of Quality ControlDefineQuality cannot be controlled without discreteand measurable characterizations of quality.MeasureQuality cannot be controlled without accurateand definitive measures of quality.
Determining Critical to Quality Baseline Package validation via ISO 11607. Package validation should include CTQ defect studiesrespective of the product. Desiccant weight gain Flavor evaluation Product performanceWhat level of defect will deteriorate my product?
Microbes & Target Leak SizesWolf, et al, PDA J Pharma Sci & Technol 2009, 63, 5 489‐498Kirsch, et al, PDA J Pharm Sci & Technol 1997, 51, 5, p. 200
Characterizing Defects Pinholes Flex Cracks Channel Defects 3mm Incomplete Seal 3mm Wolf, et al, PDA J Pharma Sci & Technol 2009, 63, 5 489‐498 Torturous path of channel defects. Pinhole is not equal to a channel defect
Flow Rate is the Critical Parameter300Leak Size (microns)250200150Wolf, et al, PDA J Pharma Sci & Technol 2009, 63, 5 489‐4981005000200400Flow Rate (ccm)600800
Pinhole vs. Channel Defect80075µ Pinhole – 44 sccm70075µ 20mm Channel – 6.4 sccmDifferential Pressure, Pa60050075 micron400100 micronExpon. (75 micron)Expon. (100 micron)300200100001020304050Capillary Length, mm60708075µ 40mm Channel – 3.2 sccm
Common Approachesto Defining Package Integrity “Looks good”Capability (Best Available Technology)Equal to/Better thanThird Party White PapersGrandfathered Industry Standards“Critical, Major, Minor”
Industry CodificationVisually O.K.Visually DefectiveMajorNo Physical Leak/No ContaminationMinorPhysical Leak/ContaminationCriticalCritical
The Ideal Test MethodInformativeAccurateSimpleCost EffectiveReduces WasteIncreases Productivity
Navigating Regulation FDA recognizes methodology. Manufacturers must prove validated methodologyconsistent with product requirements for label claims. Methods listed by organizations (ASTM, ISO, USP) areonly guidance's. Listed methodologies:– Capabilities are irrespective of package/productrequirements.– Capabilities vary based on package a product characteristics.
Direct Measures of QualityISO 11607 – Annex B Vacuum Decay (ASTM F2338)Seal Strength (ASTM F88)Airborne Ultrasound Seal Inspection*Visual Inspection (ASTM F1886)Dye Migration (F1929)High Voltage Leak Detection*Burst Strength (ASTM F2054)Bubble Immersion (ASTM F2096, D3078)* Not listed in ISO 11607 or ASTM
Test Method CostGreen Coffee Wholesale 0Jan‐09 Water Bath – Flexible Barrier SystemsMoisture/Flavor critical defect size – 15micronsWater bath sensitive to 25‐50 micronsTypically test 20 pouches/line/hourCurrent market price of coffee 2.00/lbcents/lb ASTM F2096‐04www.ico.orgBags Tested 1lb Bags /lbHours, Days, Weeks Up‐Time20 x 1 x 2 x 24 x 7 x 52 x 0.5 174,720
Cost of Deploying Destructive MethodsProductCost arHour Shift (2 Shifts, 250 Days)Dry Fill Soup 0.23Mix8Every 30min. 29.44 14,720EffervescentTablets 0.0480Every 30min. 51.20 25,600CoffeeSingles Pod 0.06200Every Hour 96 48,000Luer‐LokSyringe 0.2050Every 30min. 160 80,000PharmaBlister Pack 1.1210Every 30min. 179.20 89,600
Test Method EffectivityASTM F1886 Channel leaks down to “75 μm [0.003 in.]with a 60–100 % probability”1.80%Assumptions1,000 Packs/Day 1% Defect Rate10 Defects/Day 2,500 Defects Per Year80% POD (Above Average)80%80%80%100% Inspection 500 Defects/Year200% Inspection 100 Defects/YearProbability of Detection10090807060400% Inspection (4 Operators)4 Undetected Defects/Year504030200.16% probability that a defect will go undetected.100102030405060Time on Task, min708090Drury & m
ASTM F2714‐08Cost of Slow Information 02 Head Space Analysis.6 day dwell.3% pass/fail limit.50 micron defect 700 gr. dry fill pouch.O2 shifted from 1% to 2.5%.ppmUp‐TimeMinutes, Hours, DaysUnits60 x .5 x 60 x 24 x 6 259,200kg/unithttp://future.aae.wisc.edu 4.41/kgCost/kg259,200 x .7 x 4.41 800,150
Consider Alternative Methods Non‐Destructive vs. DestructiveQuantitative vs. AttributeNon‐Subjective vs. Operator DependentCalibration CapabilityValidation EffectivenessSimple Methodology (no sample prep)
Direct Measures of QualityISO 11607 – Annex B Vacuum Decay (ASTM F2338)Seal Strength (ASTM F88)Airborne Ultrasound Seal Inspection*Visual Inspection (ASTM F1886)Dye Migration (F1929)High Voltage Leak Detection*Burst Strength (ASTM F2054)Bubble Immersion (ASTM F2096, D3078)* Not listed in ISO 11607 or ASTM
Non‐Subjective, Quantitative Vacuum Decay (ASTM F2338) Seal Strength (ASTM F88) Airborne Ultrasound Seal Inspection High Voltage Leak Detection Burst Strength (ASTM F2054)
Non‐Destructive Vacuum Decay (ASTM F2338) Airborne Ultrasound Seal Inspection High Voltage Leak Detection
Vacuum Decay Leak Testing
ASTM F2338‐09Vacuum Decay Test Method206001816144001210300820064100200012345Test Cycle678910Differential Pressure, Pa/sec(Secondary Transducer)Vacuum Level BelowAtmospheric Pressure, mb500Test Cycle PassTest Cycle FaildP PassdP Fail
ASTM F2338‐09TEST PARAMETERSRefTest #1234567891011700.2Vacuum, mb450.2Vacuum Level BelowAtmospheric Pressure, mbVac.Vacuum, .0641.6TStrokeTEqualTTestdP/dt, Pa/s60035.21.5020.005.00TFill, s15.0020500400dP/dt, Pa/s3002001000Pass/Fail27.3P27.3P26.7P25.7P26.7P0 1 2 3 4 5 6 7 895.4FTest Cycle90.5F56.6F52.4F40.4F39.4F15Differential Pressure, Pa/sec(Secondary Transducer)Vacuum Decay for Flexible PackagingCommentsGood Product10Good Product5Good ProductGood Product0Good Product9 1025 micron25 micron15 micron15 micron10 micron10 micronTest Cycle PassTest Cycle FaildP PassdP Fail
Micro Leak Detection908070Diff dP, Pa60504030Avg dp20Upper 99% LimitLower 99% Limit10000.1 (3.4 μm)Leak Rate cc/min0.5 (7.5 μm)
Vacuum Decay Application Flexible/Rigid BarrierAir/Liquid ContentsNo Sample PreparationQuantitative andRepeatable Test Data Non‐Subjective Zero Waste
Airborne Ultrasound Through Transmission
Ultrasonic SignalPropagate through single ormultiple layers of well bondedmaterials.Reflection/absorption of soundwaves by multiple layers.
Analysis of Ultrasonic SealingPower Setting C‐scan 660‐10.145‐20.6Side Seal(Heat Seal)Side Seal(Heat Seal)‐17.6‐16.9
Controlled Seal Quality00204060‐5‐10Avg, %‐15‐20‐25Power (Joules)80100120
Seal‐Scan Online Pouch Seal Inspection
Integrated Solution
Airborne Ultrasound Application Non‐Destructive Seal InspectionQuantitative Materials AnalysisFlexible and Semi‐Rigid PackagingSeal Process OptimizationOn‐line Defect Detection
High Voltage Leak Detection(HVLD)
HVLD Defect Detection for Pouches Micro leaks down to 5 micronsPinholesCracksCrystallized leaksChannel defects
HVLD Technology High voltage applied to container Ideally non‐conductive materials Liquid triggers conductivity spike
HVLD Detection
HVLD Application Quantitative High Speed Inspection Non‐porous, Non‐conductive Materials Package Contents:‐ liquid products‐ protein based liquids‐ suspensions or emulsions Flexible or Rigid Barrier
When to Develop Methodology Should begin at the point of package development.Phase III Pharma Development.New production line engineering.When the method in place has failed.Packaging that is immune to test methodologyplagues the industry.
Pitfalls Mixing methods and test requirements. Taking test method standards as law and notguidance. Taking white papers as applied fact to specificapplications. Process improvements are vulnerable to validationhurdles. Patching the problem, not developing a solution.
What’s ahead? PDA’s TR27 – Moving to quantitative testmethodology. Track & Trace – Connecting non‐destructive testresults with specific units. Green Initiatives – Eliminating line waste with non‐destructive methods. CTQ defect stability package validation. Automated SPC testing.
Package Integrity Package Integrity –maintaining a sterile barrier. Package integrity is a sub‐category of quality and isexclusive of: Peel Strength Burst Testing Visual InspectionPackageIntegrityPackageQuality
Foundation of Quality ControlDefineQuality cannot be controlled without discreteand measurable characterizations of quality.MeasureQuality cannot be controlled without accurateand definitive measures of quality.
Thank You!Oliver a.com
Simple Cases in Testing Some products are moisture sensitive, but contentsare marginally affected by leaks. Detection to themoisture level may be over kill. Some product have desiccants to keep them dry, butreal concern may be mold or bacteria. Commonmethods may not cut it. Some production processes have high incidence ofrandom catastrophic defects. Statistical ProcessControl (SPC) will not meet quality needs.
Quantitative Measures ProvideGreater Access to Statistical Tools Ultrasonic AttenuationThicknessPeel StrengthPermeationLeak RateAttribute data fails to producepredictive measures of quality.
Vacuum Decay (ASTM F2338) Seal Strength (ASTM F88) Airborne Ultrasound Seal Inspection* Visual Inspection (ASTM F1886) Dye Migration (F1929) High Voltage Leak Detection* Burst Strength (ASTM F2054) Bubble Immersion (ASTM F2096, D3078) * Not listed in ISO 11607 or ASTM . Non‐Subjective, Quantitative Vacuum Decay (ASTM F2338) Seal Strength (ASTM F88 .