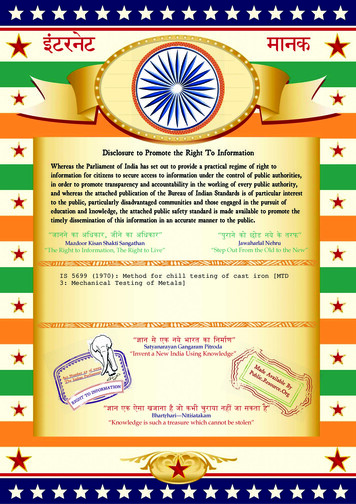
Transcription
इंटरनेटमानकDisclosure to Promote the Right To InformationWhereas the Parliament of India has set out to provide a practical regime of right toinformation for citizens to secure access to information under the control of public authorities,in order to promote transparency and accountability in the working of every public authority,and whereas the attached publication of the Bureau of Indian Standards is of particular interestto the public, particularly disadvantaged communities and those engaged in the pursuit ofeducation and knowledge, the attached public safety standard is made available to promote thetimely dissemination of this information in an accurate manner to the public.“जान1 का अ धकार, जी1 का अ धकार”“प0रा1 को छोड न' 5 तरफ”“The Right to Information, The Right to Live”“Step Out From the Old to the New”Mazdoor Kisan Shakti SangathanJawaharlal NehruIS 5699 (1970): Method for chill testing of cast iron [MTD3: Mechanical Testing of Metals]“!ान एक न' भारत का नम-ण”Satyanarayan Gangaram Pitroda“Invent a New India Using Knowledge”“!ान एक ऐसा खजाना जो कभी च0राया नहB जा सकता nowledge is such a treasure which cannot be stolen”
IS :5699- 1970Indian Standard( Reaffirmed 2003 )METHODS FOR CHILL TESTING OF C&T IRONf SecondUJX\.Reprint JU NE 1990 669.13:620.192.422:@ Copyright 1971BUREAUOFINDIANSTANDARDSMANAK BHAVAN, 9 BAHADUR SHAH ZAFAR MARGNEW DELHI 110002Gf23QWW1971
IS :5699- 1970Indian StandardMETHODS FOR CHILL TESTING OF CAST IRONkfethodsof PhysicalTestsSectionalCommittee,3Reprcsen tin ChairmanSHRI S. N. MUKERJISMDClNationalTrst House,NationalPhysicalCalcuttaMembersDR. B. K. AGARWALASHRI L. J. BALASUNDARA INationalLaboratoryMetallurgical( CSIRJamslredpuiThr Indian Iron & Steel Co Ltd,DR U. N. BHRANYSHRI K. H. SHARMA ( Alternate )DirectorateSHRI P. R. CHANDRAsEKilAIlTourismHindustanSHRI G. CHATTERJERSnnrU. C. IAI M,\), New DelhiLaboratory( CSIR),BurnpurGcnrralof Civil Aviation& Civil Aviation )Steel Ltd, Ranchi( Ministry01( &erna/e)Ministry of IVEWORKRASSWTANT DIRECTOR RESEARCI ( MET ) RESEARCH, DESIGNS ANDSTANDARDS ORGANIZATION,CHIT’PARANJAN ( Alternate )Ministry of Drfencr( DGOF )SHRI R. N. DATTASHRI D. K. CBAKRAVORTY ( Alternate I )SHRI D. SEN ( Alternate II )Ministry of Defencr ( R & D )SHRI N. T. GEORQESI RI D. K. JO HI ( Alternate )Tata Iron & Steel Co Lrcl: JnmshrdputSHRI M. C. KU IARASWAM InspectionWing, DirrctorntcGvnr-mlSnnr M. R. PATR:r.& Disposals,SHRI .J. P. SEN ( Altrrnate )SIIRI N. A. I’RAnlIuoC SuppliesNrw DrlhiM N. Dastur and Co ( 1’ ) Ltd, CkdcultnMiningand Allied MachinrryCorporationDurgapurSHRI N. v. RAWihVhNDR P. R. K. SARMA ( Akcrrrate )SIiltI V. RAMASWAMYSHRI M. B. SEIANKARSIIRI P. K. KI’RIAN ( Alternate )DR A. K. SINCULtil.Ministry of Drfcncc ( DGI )HindustanArronauticsLtd, Bang&xcNationalAcronnuticnlLaboratory( CSIR).Bangalore( Continued on pqBUREAUMANAKOFBHAVAN,INDIANSTANDARDS9 RAHADURSHAHNEW DELHI110002ZAFARMARC2)
IS:5699 - 1970( Canti*urd rom page I )RepresentingMembersSHRIK. C.ItidianSRIVASTAVASugarand Generaltion, YamunanagarEngineeringDirrctorateof TechnicalDevelopment&tion (Air ) ( Departmentof Defencetion )SHRIR. P. VAR HNEY ( Alternate )DirrctorGeneral,ISI ( Ex-oj’icio Member )SHRIR. K. SRIVASTAVA,Deputy Director ( Strut & Met )Strur A. UYAMAHERWARAN.SecfetatySHRI P. K. J&INAssistantDirector( Met ), IS1CorporaProducProduc-
IS:5699-1970Indian StandardMETHODS FOR CHILL TESTING OF CAST IRON0.FOREWORD0.1This Indian Standard was adopted by the Indian Standards Institt tion on 6 July 1970, after the draft finalized by the Methods of PhysicalTests Sectional Committee had been approved by the Structural andMetals Divisoin Council.0.2 It is often required in a cast iron foundry to measure the chillingtendencies of the metal in order to avoid any chilling or to have a specified depth of chill where extreme hardness on the cast surface is required.This is evaluated by performing the chill test. This standard has beenprepared to ensure more unified practice and help in attaining satisfactoryresults.0.3 Out of the two methods covered in this standard, the wedge test isgenerally better adapted to the higher strength grey irons. The accelerated cooling rate to induce the formation of a chill is brought about throughthe design of the test specimen.0.3.1 The chili test is adapted to the softer grades of grey iron andshould be used if the .casting is to have a specified depth of chill.Thechill in this type of test is induced by casting one edge of the test specimenagainst a metal or graphite chilled plate or block.0.4 In the preparation of this standard, assistance has been derived fromASTM Designation : A 367-1967 ‘ Methods of chill testing of cast iron’published by American Society for Testing and Materials.0.5 In reporting the result of a test or analysis made in accordance withthis standard, if the final value, observed or calculated, is to be roundedoff, it shall be done in accordance with IS : 2-1960*.1.SCOPE1.1 This standard prescribes the following two methods for chill testing ofgrey iron:a) Wedge test, andb) Chill test.‘Rulesfor roundingoff numericalvalues ( revised ).3
IS:5699-19702. WEDGE TEST2.0 Application - Selection of a test specimen of appropriate dimensionswill allow measurement of chilling tendencies of all grey iron compositions,with the exception of those having silicon contents much over 2.5 percenttogether with carbon contents over 3.5 percent.2.1 Test Specimen - The patterns for the test specimens shall be madeof metal and shall be of dimensions given in Table 1. The length of thespecimen shall not differ from the values indicated in Table 1 by morethan f 3 mm, and the tolerance on other dimensions shall be f 1 mm.The radius on the apex of the wedge shall be formed by filing a 1 mm flaton the sharp edge of the metal pattern and then carefully rounding theedges formed by 1 mm flat and the sides of the wedge. If draft on thepattern is desired, it may be obtained by varying dimension H from oneend of the specimen to the other. The pattern shall be mounted in a corebox so that the final core may be poured with the wedge in such a position that its length is vertical. There shall be minimum of 25 mm sand atthe bottom of the core.TABLE 1 RECOMMENDEDCROSS SECTIONWEDGE No.‘BmmWEDGE DIMENSIONSOF 1001001004532”125w5305034’5”1504
IS:5699-19702.2 Cores - The test shall be made in a core. The cores shall be eithersingle cores or gang cores. If a gang core is used, the minimum amountof sand between adjacent test specimens shall be not less than 2.5 X B. ‘Thesand cores shall be well-baked and may be either resin or oil bonded. Thebase sand shall be of such fineness that a smooth casting is obtained.Asand with a fineness of about 70 when determined in accordance withIS : 191%1966* will be satisfactory, although a sand with a fineness of 100or finer may be used for the small test specimens.2.3 Pouring Practice -Thetest specimens shall be poured at a fairlyuniform temperature.Precautions shall be taken to obtain a representative’sample of iron for the test specimen.Best results are obtained with asample ladle lined with a refractory mixture which is free of graphite andchilled &on. The ladle shall hold at least 2’5 kg of iron in order to avoidexcessive chilling of the iron before the test specimen may be poured.Filling the ladle once with iron just prior to obtaining the sample for testis recommended,2.4 Cooling of Test Specimen - If time is an important factor in control applications, the test specimen shall be quenched in water as soon asit is completely solid. The quenching shall be done carefully to avoidcracking of the chilled apex of the wedge. This may be accomplished bygrasping the wedge with tongs at the apex of the wedge and immersingabout 5 to 10 mm of t%e base of the wedge in water.The wedge shallthen be gradually quenched but shall be removed while there is stillsufficient heat in the wedge to dry off the water.If speed of testing isnot important, the test specimen may be either cooled in the core Jr in theair.If cooled to a very dull red before quenching in water, the demarcation between the chilled iron and the grey iron is somewhat clearer than ifthe test specimen is quenched as soon 5s it is solid.2.5 Measurementof Chill - The test specimen shall be broken by striking with a hammer in such a manner that the fracture is straight andmidway of its length.The chilled iron at the apex of the wedge with afew exceptions consists of two zones. The portion nearest the apex entirely free ofiany grey spots shall be designated as clear chili.The portionstarting with the end of the clear chill and continuing to the locationwhere the last spot of cementite or white iron is visible shall be designatedas the mottlid zone.The extent of the mottled zone may vary from virtually nothing to an amount equal to and even greater than the amount ofIf the wedge is measured at the junction of the grey fracthe clear chill.ture with the first appearance of chilled iron, the measurement shall bedesignated as total chill.In all cases, the chill shall be expressed inmillimetres as measured across the wedge. For structural control purposesit is generally satisfactory to measure the wedge where the structure is*Methods of physical tests for foundry sands.
IS : 5699 - 1970approximately50percent whiteing the chill measurement,theed.A chill reported as W3-12and the width at the junction ofture was 12 mm.3. CHILLiron and 50 percent grey iron. In reportsize of the test specimen shall be indicatwould indicate that wedge W3 was usedthe chilled and grey portions of the frac-TEST3.0 Application - This methodis better adapted than wedge test toirons having silicon contents of 2.5 percent and over and carbon contentsof 3.5 percent and over.It is also useful for control purposes in high production foundries making iron somewhat lower in carbon and silicon thanindicated above.This method is also preferable for applications in whichthe casting is to have a specified depth of chill.3.1 Test-Specimen- The patterns for the test specimens shall be madeThe length of theof metal and shall be of dimensionsgiven in Table 2.specimen shall not differ from the values indicatedin Table 2 by morethan f 3 mm, and the toleranceon other dimensions shall be f 1 mm.‘The specimen shall be cast with the chilled face in a horizontal position.For high productionwork a gang core box and pattern may be used inwhich case a test specimen with the chilled face in a vertical position maybe found more convenient.3.2 Cores - The test shall be made in a core.For general application aIf a gang core issingle core may be more satisfactorythan a gang core.used, the amount of sand between test specimens shall be 25 mm minimumor 2.5 x A ( see Table 2 ), whichever is greater.3.3 Chill Plates - Chill plates may be cast iron, steel, copper, or graWhen single testThe surface of the chill plate shall be machined.phite.specimens are cast, the chill plate shall extend at least 25 mm beyond thetest specimens in all directions and shal! be at least 25 mm thick. For highproduction work, a sufficient number of chill plates should be available tokeep the temperatureof the plate below 250 C.A water-cooledsteelplate may be found more satisfactory for high production work. The chillplate shall be kept free of fire cracks and all foreign matter as the depthof chill is markedly affected by the presence of films of burned oil or otherThe- best practiceis to clean off the plate with a wireaccumulations.blush as soon as the core and test specimen is removed.3.4 Pouringwith .4.1 Iron shall not be poured directly on the chill plate as the depthItof chill may be affected or the test specimen may burn on chill plate.6
IS : 5699 -1970may be desirable to place a I\-eight on the core when pouring it as thereThe openingmay be a tendency for the core to lift as it is being poured.in the core shall be free of sand fins and shall set flat on the chill plate.In the event the core does not ,fit the chill plate, it shall be rubbed untilit does.3.5 Coolingwith 2.4.TABLE 2ofTestSpecimen--RECOMMENDEDThisDIMENSIONSshallbe doneinaccordanceFOR CHILL TEST SPECIMEN( Clause3.1 )All dimensionsin 01001252022.522.5252512.512.512’516163.5.1 If rapid testing is desired,water, starting with the edge farthestGSRECOMMENDEDCHILL DEPTHR.%NGE0.80.81.61%2’452.5 to 105555the specimenmay befrom the chilled edge.7356103,,,,,,,quenched12202440in
IS : 5699 - 19703.6 Measurementof Chill - The test specimen shall be broken in sucha manner that the fracture is straight and follows the notch in the testspecimen.The chill from the chilled face to the first appearance of a greyspot shall be designated as cfe r chill. The distance from chilled face to thelast appearance of a spot of white iron shall be designatedas total chill.The portion of the chill affected zone between the clear chill and the totalchill shall bi designatedas the mottled tone.For general structureandquality control purpose the chill shall be measured from the chilled face toa location where the structure is approximately50 percentwhite ironwhich is roughly half-way through the mottled zont?. If the chill test isused for the control of iron for castings having a chilled surface for wearit would be desirableto measure and record clearresistantpurposes,chill.If the casting with a chilled surface is to have some machining operation in the proximity of the chilled surface, it may also be necessary tospecify maximum depth of total chill as well as depth of clear chill. In allcases, the depth of chill shall be expressed in millimetresand the size ofthe test specimen used shall be indicated.
BUREAUOFINDIANSTANDARDSHeedquarters:Manak Bhavan, 9 Bahadur Shah Zaf
sand cores shall be well-baked and may be either resin or oil bonded. The base sand shall be of such fineness that a smooth casting is obtained. A sand with a fineness of about 70 when determined in accordance with IS : 191%1966* will be satisfactory, although a sand with a fineness of 100