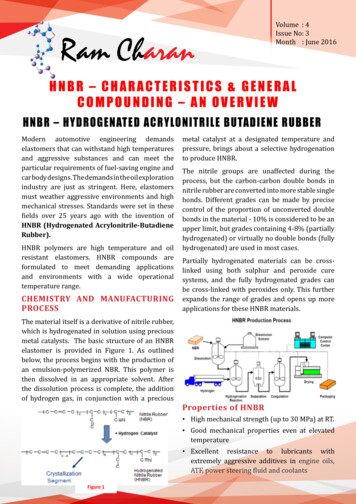
Transcription
Volume : 4Issue No: 3Month : June 2016HNBR – CHARACTERISTICS & GENERALCOMPOUNDING – AN OVERVIEWHNBR – HYDROGENATED ACRYLONITRILE BUTADIENE RUBBERModern automotive engineering demandselastomers that can withstand high temperaturesand aggressive substances and can meet theparticular requirements of fuel-saving engine andcar body designs. The demands in the oil explorationindustry are just as stringent. Here, elastomersmust weather aggressive environments and highmechanical stresses. Standards were set in thesefields over 25 years ago with the invention ofHNBR (Hydrogenated Acrylonitrile-ButadieneRubber).metal catalyst at a designated temperature andpressure, brings about a selective hydrogenationto produce HNBR.The nitrile groups are unaffected during theprocess, but the carbon-carbon double bonds innitrile rubber are converted into more stable singlebonds. Different grades can be made by precisecontrol of the proportion of unconverted doublebonds in the material - 10% is considered to be anupper limit, but grades containing 4-8% (partiallyhydrogenated) or virtually no double bonds (fullyhydrogenated) are used in most cases.HNBR polymers are high temperature and utthecarbon- ‐carbondoubleresistant elastomers. HNBR compounds are tablesinglebonds.Differentgradeshydrogenated materials can be erteddoublebondsintheformulated to meet demanding applications linkedmaterial- aining4- ed)areusedinmostenvironmentswith elastomersa widethatoperationalsystems,and the fully hydrogenated grades eparticularrequirementsofcases.temperaturefuel- ntheoilexplorationindustrybe cross-linked with peroxides only. This edmaterialscanbecross- dthefullyhydrogenatedgradescanbecross- ‐linkedperoxidesexpandstherangeof le- ‐ButadieneRubber).applicationsfor these HNBR e material itself is a derivative of nitrile environmentswithawidewhichis hydrogenatedin solution using preciousoperationaltemperaturerange.metal catalysts. The basic structure of an HNBRCHEMISTRYANDMANUFACTURINGPROCESSelastomer is provided in Figure 1. As ber,whichishydrogenatedinsolutionbelow, the process begins with the production eginswiththeproductionofanemulsion- propriatesolvent.Afterthethen dissolved in an appropriate solvent. rocess temperatureis complete,the tiesofHNBRCHEMISTRY AND MANUFACTURINGPROCESSof hydrogen gas, in conjunction with a preciousPropertiesHNBR Highmechanicalsoftrength(upto30MPa)atRT. Goodmechanicalpropertiesevenatelevatedtemperature vesengine Highmechanicalstrength(up toaggressive30 MPa)at inRT.oils,ATF,powersteeringfluidandcoolants VerygmechanicaloodhotairandsteamResistance. Goodpropertieseven at elevated Verygoodlowtemperatureflexibility. eseltemperature LowpermeabilitytovolatilesandgasesFigure1 Excellent resistance to lubricants withextremely aggressive additives in engine oils,ATF, power steering fluid and coolants
Very good hot air and steam Resistance.b. Effect of RDB Content Very good low temperature flexibility. Excellent resistance to many modern fuelsincluding biodiesel Low permeability to volatiles and gases Good resistance to crude oil even in the presenceof hydrogen sulfide, amines, alkaline corrosioninhibitors and Oxidizing media. Good ozone resistance very good abrasion resistance (DIN abrasion:30 - 50 mm3)1. By controlled hydrogenation of NBR a HNBR,with different amounts of RDB (residualdouble bond) contents can be produced.1. HNBR with high RDB can be cross-linked usingsulfur and Peroxideb. EffectofRDBContent1. osslinkingdensitycontentscanbeproduced.2. HNBRwithhighRDBcanbecross- inkingdensity1.HighHighRDB cincreasesthe compression set and4. ngstabilityofthereduces the ageing stability of the materialmaterial Excellent Chemical Resistance Low compression set even at high temperature Good resistance to high energy radiation Low noise/vibration transmissionSelection Criteria for HNBRComparison of HNBR with other Polymers interm of Heat and Oil resistanceWhen selecting a HNBR polymer for a specificapplication, three criteria to eatandOilresistance1. Acrylonitrile content: fluid resistance as wellas low temperature properties2. Hydrogenation level: influences heat, chemicaland ozone resistance3. Polymer Mooney Viscosity: influences theprocessing of the compound and also thephysical properties of the final article.a. Effect of Acrylonitrile Content1. The nitrile group, coming from incorporatedBASIC Compounding and Processingacrylonitrile monomers (ACN) stronglyBASICCompoundingandProcessinga. Selection of Grade: There are a wide varietyinfluences the oil resistance and ylonitrile(ACN)contentof ofacrylonitrilecontentpolymerstemperature ngefromapproximately17to50%available in the HNBR today. They range from2. Higher ACN content means better oil resistance, alsoimpactstheapproximately 17 to 50% ACN. The ACN contentlow- merisincreased,fuel resistance and gas willdecreasethelow- ‐not reasesthe3. Higher ACN content means poorer lowimpacts the low-temperature performance. vehighervolumetemperature flexibilityACN contentof thepolymeris increased,swelltheandimprovedlow- ‐temperatureflexibility.the asvolumeswell betterof sistancewhereashigherRDB%willimprovewill decrease while the ndCrosslinkingdensity.flexibility will become poorer. Alternatively, lablepermitstheone decreases the ACN level of the transfer,orwillinjectionmoldingvs.extrusion).the eyviscosityfrom50toapproximately100whenvolumeswell andwithimprovedlow-temperaturemeasuredatML(1 4)@100 C.,specialgradeshavingMooney40.flexibility.
Likewise, as RDB% lower, better is Heatresistance, Ozone resistance, Compression setand Chemical resistance where as higher RDB% will improve Dynamic properties, Hardness,Modulus and Crosslinking density.Lastly, the wide range of Mooney viscositiesgrades available permits the compounder tochoose a product which best suits their specificmethod of manufacturing (e.g., compression,transfer, or injection molding vs. extrusion).Today, HNBRs range in Mooney viscosity from50 to approximately 100 when measured atML(1 4)@100 C., with special grades havingMooney around 40.A typical recipe of HNBR is listed in Table belowIngredientsHNBRMetal oxidesAntidegradentsProcess AidPhr1000–51.5 – 30–3Filler40 – 100Co-agents0-5PlasticizerCuratives0 – 203 – 10b. Metal Oxides: 2 – 10 Phr of ZnO/MgOrecommended for Sulphur cure whereas 2 Phrof ZnO/MgO is recommended for Peroxidecure compounds, in combination with stearicacid.c. Antidegradents: Many antioxidants likePhenolic type interfere with peroxidecrosslinking,affectingpropertiessuch as modulus and compression setresistance. A combination of 0.4 phr of zincmethylmercaptobenzimidazole and 1.1 phrsubstituted or styrenated diphenyl amine(SDPA) provides the best balance of protectiontogether with minimum effect on vulcanizateproperties, in the case of peroxide cure.For sulfur cure systems, levels of 1 phr zincmethylmercaptobenzimidazole and 2 phrSDPA are best.Antiozonants are not needed.d. Process Aids: Process improvement additivescan be incorporated in high-viscosityformulations at nominal 2.0 phr levels, tofacilitate mold flow and reduce cycle times.Generally Zinc salts of high molecular weightfatty acids are effective process aids, M C Waxlike R A Wax 1080 also improves processing.e. Fillers – Carbon Black: The physicalproperties of HNBR compounds reinforcedwith carbon black depend on the particle sizeand structure of the black. Mostly FEF blackis generally recommended to get optimumproperties. Highly reinforcing black increasesstiffness of compound permitting low doses.By increasing particle size of carbon black(FEF, GPF and MT) Resistance to compressionset and heat resistance improve whereastensile strength, tear resistance, and abrasionresistance are reduced.f.Mineral fillers: Precipitated silica providesthe highest level of reinforcement; however,it yields very stiff, high viscosity compounds.Precipitated silicas generally improve theheat resistance of HNBR vulcanizates.Silane coupling agent improves rubber fillerinteraction.French powder (talc) is much easier toincorporate and yields comparatively similarmodulus and hardness values as with silica.Blends of silica and talc are often utilizedfor balancing vulcanizate properties withprocessing characteristics.g. Plasticizer: Selection of Plasticizer is mostimportant criteria of HNBR compounds.Plasticizers used to improve low temperatureflexibility, to optimize physical properties andprocessing characteristics with low volatilityat approx. temperature 150 C (302 F) andalso resistance to extraction in oils and fuels.Generally Trimellitate plasticizers Like TOTM,TIOTM is being used. Sebacates, adipatescan also be utilized but affects slightly hightemperature ageing.h. Vulcanization: HNBR with less than 1%residual double bonds must be vulcanized withperoxide or high-energy radiation, as there isinsufficient unsaturation to obtain a practicalstate of cure with sulfur systems.EV (efficient vulcanization) and semi-EV
sulfur cure systems can be used effectivelywith partially saturated grades to achieveimproved adhesion to reinforcing substratesand to obtain favorable properties in dynamicapplications.HNBR elastomers are typically cured witheither peroxide or sulfur/sulfur-donor curesystems. Comparisons of sulfur/sulfurdonor and peroxide cured HNBR compoundsindicate that peroxide curing providesbetter compression set and heat resistance.Because HNBR has fewer highly reactive allylposition hydrogens versus other diene-basedelastomers, it is necessary to add 50-100%more peroxide in order to produce excellentcuring characteristics. Many kinds of peroxidesare available for curing HNBR. However, it isimportant to select one that is the most suitablebased on the process and cure temperaturethat will be utilized to produce the finishedparts.i.j.approximately 140 C. This master batch isthen run through the mixer a second timeadding the cure chemicals and again droppedfrom the mixer at approximately 100-110 C.HNBR polymers generate more heat duringcompounding in internal mixers or on openmills than NBR polymers; however, this canimprove processing due to the thermoplasticnature of the polymers.Subsequent processing steps (extrusion,preform, moulding) should be carried outat the highest practical temperature to takeadvantage of the thermoplastic characteristicsof the compound. This aspect of HNBRpolymers is of particular importance forhigh-hardness formulations. Extrusion andCalendaring requires higher temperature ascompare to NBR.Application of HNBR1 Automotive: Gaskets, Seals, Diaphragms,Since peroxides have different molecularBoots, Timing Belts, Shaft Seals.weights and decomposition temperatures, itWith the continued trend to ever decreasingis imperative to select the correct one ersisofparticularspace ofinthetheenginebay,temperatureson the criteria noted above or one can greatlyimportanceforhigh- uirescontinue to rise, placing ever more demandingaffect the processability and requirements on the components operating inof producing the finished goods in question. ApplicationofHNBRthis environment. One consequence of this isCoagents: Resistance to heat and compression 1. lts,ShaftSeals.the needfor Elastomerscapableof ever-greaterset can be maximized by nebay,selected coagents with peroxides to demandingrequirementsonToday’s elastomer must withstand nsequenceofthisisthethe state of cure. Triallyl isocyanurateenvironmentsin theengine compartment.needforElastomerscapableofever- ‐greaterlong- ‐termhigh- ‐temperatureimproves compression set andharshenvironmentsintheengineHigher operating temperatures have eresultedinthedevelopmentliquid 1,2-polybutadiene, N,N’-m-phenylenein aggressivethe developmentof lubricants,more atingthedimaleimide effective at low ininggreaterheatandfluidresistance.fluidsand lpropanetrimethacrylatenecessitatingtheHNBRuse polymersof uecombinationof(TMPTMA) can be used as effective obilesand fluidexcellentcompressionsetresistance.Processing of HNBRresistance. The automotive industry seeks aAll of the commercially available HNBRs canbe mixed either on a two-roll mill or with aninternal mixer. Most HNBRs are mixed bythe use of internal mixing equipment. This isdone to improve the quality of the finishedcompound while also significantly reducingthe typical mix times.Typically, HNBRs are two-pass mixed in aninternal mixer where the first pass throughthe mixer without the cure chemicals andis typically dropped out of the mixer at
tough elastomer with improved resistance tochemical, fuel and heat. HNBR polymers offer aunique combination of resistance to coolants,fuels and oils used in today’s automobileswhile providing excellent compression setresistance.3 Industrial and other Application: Rollersfor Printing, Textile, Heat Exchanger Gaskets,Expansion jointing’s, Pumps and Couplings,Textile applications like Spinning cots andAprons etc.Due to the ethylene content of HNBR polymers,2. Oil Industry: Stators, Packers, Drill Bit seals,they are resistant to many chemicals used inBlow out preventorsthe roll industry offering excellent heat andsteam resistance, for plate heat exchangerHNBR compounds meet the extreme demandsfor Fat/Oil application, it provides highin oilfield applications which require excellenttemperature resistance and low compressionproperties in the harsh conditions likeset at high temperature including FDA. It isresistance to corrosion inhibitor, Hydrogenalsoused as sexpansionjoint, eincludingFDA.Itisasulfide / Sour gas, Resistance to crude and s,CouplingsetcforverygoCouplings etc for very good dynamicdrilling fluids, High Tear and Abrasion s and heat resistance.resistance, Low water swell. Low compressionset and most importantly very good resistanceto Extrusions and Explosive Decompression(Rapid Gas Decompression) seen with today’soilfield industry. While HNBR polymer canwithstand the harshabuse encountered in2. reventorsdrilling operations, these compounds are plicationswhichable to stand up to the high temperatures ikeresistancetocorrosionencounteredin nsetandwith the excellent resistance to the nsandExplosivefluids such as crude oil, gases,acids and andtheharshabuseencounteredindrillingHNBR compounds can meet anduptothehightemperaturesrequired for application in these shenvironments.Note: For the requirement of HNBR,kindly contact us.3. otsandApronsetc.Email : videshightemperatureTamil NaduAndhra PradeshWest BengalMaharashtra::::Chennai, Hosur, Madurai, CoimbatoreHyderabadKolkataMumbaiContact : 044-43541200 022-40154487sKeralaKarnatakaNCR:::Trissur, ErnakulamBangalore, BelgaumFaridabad, Ghaziabad
the volume swell of the associated compound will decrease while the low-temperature flexibility will become poorer. Alternatively, if one decreases the ACN level of the polymer, the associated compound will have higher volume swell and improved low-temperature flexibility. b. Effect of RDB Content 1. By controlled hydrogenation of