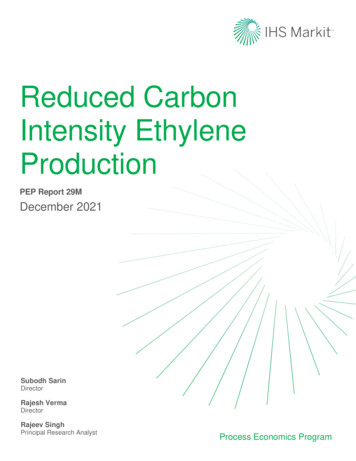
Transcription
Reduced CarbonIntensity EthyleneProductionPEP Report 29MDecember 2021Subodh SarinDirectorRajesh VermaDirectorRajeev SinghPrincipal Research AnalystProcess Economics Program
IHS Markit PEP Report 29M Reduced Carbon Intensity Ethylene ProductionContactsSubodh SarinDirectorsubodh.sarin@ihsmarkt.comRajesh VermaDirectorrajesh.verma@ihsmarkt.comRajeev SinghPrincipal Research Analystrajeev.singh@ihsmarkit.comMichael ArnéDirector, Process Economics Programmichael.arne@ihsmarkt.comConfidential. 2021 IHS Markit. All rights reserved.1December 2021
IHS Markit PEP Report 29M Reduced Carbon Intensity Ethylene ProductionPEP Report 29MReduced Carbon Intensity Ethylene ProductionSubodh Sarin, DirectorRajesh Verma, DirectorRajeev Singh, Principal Research AnalystAbstractEthylene is the largest-volume basic petrochemical, produced primarily by steam cracking ofhydrocarbons (naphtha, gas oil, ethane, and LPG) and is utilized to produce a spectrum of chemicalintermediates. Ethylene consumption has been increasingly driven by its demand in emerging countriesand the consumption has increased at an average rate of 4% per year over the past decade.Ethylene production is one of the three largest CO2 emitters in the chemical industry; the other two arethat of propylene and ammonia. Conventional cracking generates roughly 1–1.8 metric tons (Mt) ofCO2 for every metric ton of ethylene produced. Globally, that amounts to more than 260 million tonsof CO2 emissions per year.This report provides an overview of the developments in ethylene production technology with a focuson reduced carbon intensity. Numerous technological advancements have been presented whichsignificantly reduce CO2 emission from ethylene plants. Detailed technical and economic evaluationsare presented for the following three technologies with reduced carbon intensity for ethyleneproduction: EcoCatalytic chemical looping technology Coolbrook’s roto dynamic reactor (RDR) technology Electric furnace technologyThe analysis and techno-economic design results for the above three technologies are based on theproduction of 1 MMtpa polymer-grade ethylene. Electric furnace and Coolbrook’s roto dynamicreactor have been evaluated with wide range naphtha (WRN) as feed while the design of theEcoCatalytic technology will be based on ethane feed. The capital and production cost results hereinare presented for the fourth quarter of 2020 on a US Gulf Coast basis.The analysis is based on information by the technology provider presented in the open literature (suchas patents or technical articles) or in-house generated data (e.g., HYSYS simulation, equipment costestimation). While this assessment may not reflect the actual plant data fully, we do believe that it issufficiently representative of the process and process economics within the range of accuracy necessaryfor economic evaluations of a process design.Confidential. 2021 IHS Markit. All rights reserved.2December 2021
IHS Markit PEP Report 29M Reduced Carbon Intensity Ethylene ProductionContents1234IntroductionSummaryProcess economicsEnergy and carbon intensityImpact of cost of electricity on the process economicsIndustry statusCharacteristics of the marketTechnology reviewDecarbonization measure in a steam crackerCoke inhibition technologyMechanical device for enhanced heat transferMechanical device for increased surface areaMechanical device for increased heat transfer coefficientSurface technologiesAluminum-based alloyCeramic materialPermanent surface coatingsFeed additivesMethod to improve furnace thermal efficiencyCombustion air preheatGas turbine integrationHigh-emissive refractory coatingHeat recovery schemeAlternate feedstock and fuel for olefins sis oilBiogas as fuelHydrogen as fuelOxy-fuel combustionCarbon capture in an ethylene plantCarbon capture and utilizationTechnology readiness levelOxidative dehydrogenation of ethane (ODHE)Chemical loopingCatalystsEcoCatalytic chemical looping process for ethylene productionAcetylene hydrogenationEthylene and propylene recovery systemCoolbrook RDR reactor [US 20210171836A1, 202129112]BackgroundCurrent statusElectric furnace for steam crackingOhmic or joule heatingInduction-heated reactorMicrowave/radio frequency (RF) heatingLatest development by petrochemical playersBASF electric furnace technologyConfidential. 2021 IHS Markit. All rights 51525354December 2021
IHS Markit PEP Report 29M Reduced Carbon Intensity Ethylene Production5Ethane oxidative dehydrogenation of ethylene production using EcoCatalyticchemical looping technologyBasis of designMaterial of constructionStorage tanksProcess descriptionEthane ODH reaction and catalyst regenerator (Section 100)ODH reaction effluent compression and de-methanizer (Section 200)Ethylene recovery section (Section 300)Propylene recovery section (Section 400)Ethylene and propylene refrigeration systemHydrogen purification (PSA) systemCO, CO2 gases removal systemProcess discussionReactor/regenerator systemCO2 recovery optionFront-end DeC1 vs front-end DeC2Propylene recovery optionEmission and wastesCost estimatesFixed capital costsProduction costs6Naphtha cracking for ethylene production using Coolbrook RDR technologyBasis of designStorage tanksProcess descriptionSection 100—Pyrolysis and quenchCold sectionSection 200—Compression, drying, and de-propanizerSection 300—Subcooling and separationsSection 400—Product separationSection 500—RefrigerationSection 600—Steam distributionProcess discussionImpact of renewable electricity on process economicsPotential to use renewable electricitySpecific energy calculationSteam system designStage of development of technologyProduct slateEthylene cracker with RDR—configuration optionsNumber of furnacesCold section designEnvironmentMaterial of construction (MOC)Carbon and water footprintCost estimateFixed capital costsProduction costs7Naphtha cracking for ethylene production using electric furnace technologyBasis of designProcess descriptionSection 100—Pyrolysis and quenchSection 200—Compression, drying, de-propanizerConfidential. 2021 IHS Markit. All rights 9120120121121121122123125125127128129December 2021
IHS Markit PEP Report 29M Reduced Carbon Intensity Ethylene ProductionSection 300—Subcooling and separationSection 400—Product separationSection 500—RefrigerationSection 600—Steam distributionProcess discussionImpact of cost of renewable electricity on the process economicsPotential to use renewable electricitySpecific energy calculationElectric furnace yieldSteam system designNumber of furnacesStage of development of technologyEthylene cracker with an electric furnace—configuration optionsCold section designEnvironmentMaterial of constructionCarbon and water footprintCost estimatesFixed capital costsProduction costsAppendix A—Design and cost basisAppendix B—Cited referencesAppendix C—Process flow 155155155155156157159163173TablesTable 2.1 Overall summary of the ethylene technologiesTable 2.2 Specific energy consumption—hydrocarbon cracking processTable 2.3 Carbon footprint based on the use of net-zero-carbon renewable electricityTable 3.1 World capacity/consumption for ethylene (thousands of metric tons)Table 3.2 World consumption of ethylene by end-useTable 3.3 World top producers of ethylene—2020Table 4.1 Mechanical device for enhanced heat transfer coefficientTable 4.2 Composition of Centralloy HT E by Schmidt and ClemensTable 4.3 Permanent surface coatingTable 4.4 EcoCatalytic CL-ODH process—operating conditions [US 20200062677, WO2016049144, WO 2018005456]Table 5.1 EcoCatalytic CL-ODHE process—Design basis and assumptionTable 5.2 EcoCatalytic CL-ODHE process—Material balance and key performance parametersTable 5.3 EcoCatalytic CL-ODHE process—Major stream flowsTable 5.4 EcoCatalytic CL-ODHE process—Major equipmentTable 5.5 EcoCatalytic CL-ODHE process—Utility summaryTable 5.6 EcoCatalytic CL-ODHE—FE DeC1 vs FE DeC2 option economic comparisonTable 5.7 EcoCatalytic CL-ODHE process—with and without the propylene recovery optioneconomic comparisonTable 5.8 EcoCatalytic CL-ODHE process—Environmental footprintTable 5.9 EcoCatalytic CL-ODHE process—Total capital investmentTable 5.10 EcoCatalytic CL-ODHE process—Total capital investment by sectionTable 5.11 EcoCatalytic CL-ODHE process—Variable costsTable 5.12 EcoCatalytic CL-ODHE process—Production costTable 6.1 Coolbrook RDR process—Design bases and assumptionsTable 6.1a Coolbrook RDR process—cracking yield (wt%) [US 20210171836A1, 202129113]Confidential. 2021 IHS Markit. All rights 84858990December 2021
IHS Markit PEP Report 29M Reduced Carbon Intensity Ethylene ProductionTable 6.2 Coolbrook’s RDR process—Major stream flowsTable 6.3 Coolbrook’s RDR process—Major equipmentTable 6.4 Coolbrook RDR process—product slate (conventional vs RDR)Table 6.5 Total energy requirement (1 MMtpa ethylene, wide range naphtha)Table 6.6 RDR process—Carbon emissions and water usageTable 6.7 Coolbrook RDR process—Total capital investmentTable 6.8 Coolbrook RDR process—Variable costsTable 6.9 Coolbrook RDR process—production costsTable 7.1 Electric furnace process—Design bases and assumptionsTable 7.1a Electric furnace process—Cracking yields (wt%)Table 7.2 Electric furnace process—Major stream flowsTable 7.3 Electric furnace process—Major equipmentTable 7.4 Total energy requirement (1 MMtpa ethylene, wide range naphtha feed)Table 7.5 Electric furnace process—Carbon emissions and water usageTable 7.6 Electric furnace process—Total capital investmentTable 7.7 Electric furnace process—Variable costsTable 7.8 Electric furnace process—Production 57158FiguresFigure 2.1 Net production cost vs electricity price (RDR process)Figure 2.2 Net production cost vs electricity price (EF process)Figure 4.1 Low-Emission cracking furnace [US 20200172814]Figure 4.2 Circulating fluidized bed Chemical looping reactorFigure 4.3 Effect of CaSO4 promoter on ethylene selectivity [US 20200062677]Figure 4.4 Effect of ethane conversion on ethylene selectivity [US 10919027]Figure 4.5 Effect of ethane conversion on H2 conversion and water formation [US 10919027]Figure 4.6 Effect of steam addition on olefin selectivity in the ODH process [US 20200123084]Figure 4.7 Effect of operating pressure on ethylene yield [US 20200123084]Figure 4.8 Effect of system pressure on net energy requirement [US 20200123084]Figure 4.9 Effect of ethane conversion on ethylene yield and selectivity [US 20200123084]Figure 4.10 Naphtha pyrolysis—influence of temperature and residence timeFigure 4.11 Relative size of a conventional gas furnace and RDR facilityFigure 4.12 Representation of an RDR machineFigure 4.13 Electric resistance-heated methane steam reformerFigure 4.14 Electric induction-heated methane steam reformerFigure 4.15 Conventional furnace with heat and material balance across plant [EP 3725865]Figure 4.16 Electric furnace with heat and material balance across plant [EP 3725865]Figure 4.17 Electric furnace with feed/effluent exchanger [EP 3725865]Figure 5.1 Process schematic of an ethylene and propylene refrigeration systemFigure 5.2 Process schematic for an H2 PSA systemFigure 5.3 Process schematic for a CO, CO2 removal systemFigure 5.4 Effect of plant capacity on investment costsFigure 5.5 Effect of waste plastic feed on net production cost and product valueFigure 5.6 Effect of light oil by-product on net production cost and product valueFigure 5.7 Effect of plant operating level on net production costFigure 6.1 BFD of a naphtha cracker using RDRFigure 6.2 Heat balance across a conventional gas furnace for wide range naphthaFigure 6.3 RDR options—comparison with a conventional gas furnace designFigure 7.1 Heat balance across the electric furnace for wide range naphthaFigure 7.2 BFD of a naphtha cracker using an electric furnaceFigure 7.3 Electric furnace options—comparison with a conventional gas furnace designConfidential. 2021 IHS Markit. All rights 66678586868792117119126127154December 2021
IHS Markit PEP Report 29M Reduced Carbon Intensity Ethylene ProductionAppendix C FiguresFigure C.1 EcoCatalytic oxidative dehydrogenation of ethane for ethylene productionchemical loopingFigure C.1 EcoCatalytic oxidative dehydrogenation of ethane for ethylene productionchemical loopingFigure C.1 EcoCatalytic oxidative dehydrogenation of ethane for ethylene productionchemical loopingFigure C.1 EcoCatalytic oxidative dehydrogenation of ethane for ethylene productionchemical loopingFigure C.2 Ethylene from naphtha using the RDR technology (Sheet 1 of 6)Figure C.2 Ethylene from naphtha using the RDR technology (Sheet 2 of 6)Figure C.2 Ethylene from naphtha using the RDR technology (Sheet 3 of 6)Figure C.2 Ethylene from naphtha using the RDR technology (Sheet 4 of 6)Figure C.2 Ethylene from naphtha using the RDR technology (Sheet 5 of 6)Figure C.2 Ethylene from naphtha using the RDR technology (Sheet 6 of 6)Figure C.3 Ethylene from naphtha using the electric furnace technology (Sheet 1 of 6)Figure C.3 Ethylene from naphtha using the electric furnace technology (Sheet 2 of 6)Figure C.3 Ethylene from naphtha using the electric furnace technology (Sheet 3 of 6)Figure C.3 Ethylene from naphtha using the electric furnace technology (Sheet 4 of 6)Figure C.3 Ethylene from naphtha using the electric furnace technology (Sheet 5 of 6)Figure C.3 Ethylene from naphtha using the electric furnace technology (Sheet 6 of 6)Confidential. 2021 IHS Markit. All rights 0181182183184185186187188189December 2021
IHS Markit Customer Care:CustomerCare@ihsmarkit.comAsia and the Pacific RimJapan: 813 6262 1887Asia Pacific: 604 291 3600Europe, Middle East, and Africa: 44 1344 328 300Americas: 1 800 447 2273DisclaimerThe information contained in this presentation is confidential. Any unauthorized use, disclosure, reproduction, or dissemination, in full or in part, in anymedia or by any means, without the prior written permission of IHS Markit or any of its affiliates ("IHS Markit") is strictly prohibited. IHS Markit owns all IHSMarkit logos and trade names contained in this presentation that are subject to license. Opinions, statements, estimates, and projections in this presentation(including other media) are solely those of the individual author(s) at the time of writing and do not necessarily reflect the opinions of IHS Markit. Neither IHSMarkit nor the author(s) has any obligation to update this presentation in the event that any content, opinion, statement, estimate, or projection (collectively,"information") changes or subsequently becomes inaccurate. IHS Markit makes no warranty, expressed or implied, as to the accuracy, completeness, ortimeliness of any information in this presentation, and shall not in any way be liable to any recipient for any inaccuracies or omissions. Without limiting theforegoing, IHS Markit shall have no liability whatsoever to any recipient, whether in contract, in tort (including negligence), under warranty, under statute orotherwise, in respect of any loss or damage suffered by any recipient as a result of or in connection with any information provided, or any course of actiondetermined, by it or any third party, whether or not based on any information provided. The inclusion of a link to an external website by IHS Markit should notbe understood to be an endorsement of that website or the site's owners (or their products/services). IHS Markit is not responsible for either the content oroutput of external websites. Copyright 2021, IHS Markit . All rights reserved and all intellectual property rights are retained by IHS Markit.
Reduced Carbon Intensity Ethylene Production PEP Report 29M December 2021 Process Economics Program Subodh Sarin Director Rajesh Verma Director