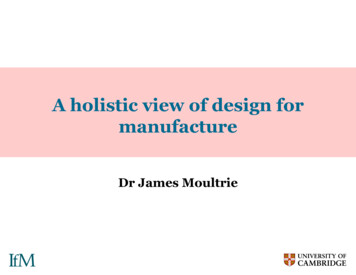
Transcription
A holistic view of design formanufactureDr James Moultrie
Agenda A brief history lesson ! Design for manufacture Design for assembly Product architecture Product platforms
A brief history lesson
Eli Whitney . Originally a blacksmith:nails and hatpins Attended Yale in mid 20s Taught Worked on a plantation– Designed a machine toclean cotton– Did work of several people– But machine copied– Nearly ruined in courtcases Penniless at 39Source: www.eliwhitney.org/
Eli Whitney . Took an impossibleorder to make 10,000muskets at 13.40 each Up to then, all rifles werehandmade Invented the millingmachine He created (arguably)standardised andinterchangeablecomponents Tolerances!Source: www.eliwhitney.org/
Henry Ford . 1907: assembly line divided manual assemblyoperations into short cyclerepetitive steps Model T ford standardised parts,simplification Serviceability - easy accessfor repair“We start with theconsumer, work backthrough the design andfinally arrive atmanufacturing”
Value analysis . General Electric 1940 Systematic review ofproduct costs Initially applied toexisting products Value engineering:applied during designphaseSource: http://dismuke.net/howimages/gerefrig1940large.jpg
1960 onwards . 1960s: Producibility & manufacturability– GE developed internal guide - “manufacturing producibilityhandbook”– c. 1985 DfM came into wider use 1968: Systematic methods for Design for Assembly– Boothroyd & Redford: studied automatic assembly– Later Boothroyd & Dewhurst– Lucas Engineering Systems
1980’s: Concurrent engineering Market developmentIdeaProduct designManufacturing process design
1990s DfX and Product architecture Df environment, safety, etcProduct platformsProduct architectureModularityReuse
Design for manufacture
Component optimisationComponent commonalityProcess selectionProcess optimisationComponent
DFM elements Appropriate process selection––––material, volumetolerances, complexityset up costsexpertise (internal / external) Reduce the number of process stages– eliminate and combining processes– reducing set up requirements Optimise for the process– recognise the process limitations– exploit benefits of the process– DFM process specific guidelines
Process guidelines
Examples machined part guidelines Don’tDoDO - Design holes to the shape of thetool. If a hole is to be tapped, providespace for it.Don’tDoDon’t 6.1211 6.125DoDO - Use standard dimensions wherever possible(NB - these may vary depending on the toolingavailable)Don’tDoDO - Provide an undercut for threads in turnedcomponentsDO - Provide appropriate fillet radii (matched to tool tips)DO - Place holes away from edges - allow room for tool
Design for assembly
Sub-system optimisationAssemblyAssembly optimisationComponent minimisation,handling, fitting, feedingComponent optimisationComponent commonalityProcess selectionProcess optimisationComponent
DFA - Design for Assembly Design guidelines or design rules– System level– Issue specific - handling, fixing etc Systematic methods to analyse an assembly– Lucas Engineering & Systems– Boothroyd & Dewhurst Basic philosophy of all approaches– minimise the number of components– maximise ease of locating & joining
Don’t fight gravity
Open enclosuresAvoid confined spacesDon’t ‘hide’ key components
Assemble from a single direction
Integrate components .
Systematic methods Functional analysis– Is each component needed? Handling analysis– Are the components simple to handle? Fixing analysis: Mapping assembly sequence:– Insertion / holding process– Securing / fixing processes– Additional (non-assembly) processes
Component functional analysis Does the part moverelative to parts whichhave already beenanalysed?YNIs the part made of adifferent material tothose with which therewas no relativemovement?NYNYNIs the part separate toallow for maintenance,adjustment orreplacement?Is the movementessential for the productto function?Is the materialdifference essential forproduct function?Is the maintenance,adjustment orreplacement Must the part beseparate to providethis movement?Must the part beseparate to satisfy thedifferent materialrequirement?NYNNon essential ‘B’ componentMust the part beseparate to enableadjustment orreplacement?YNEssential ‘A’componentNeed foradjustment /replacement
Component handling & feeding Handling– Presentation of parts in manual assembly Feeding– presentation of parts in automated assembly Scores based on:– size and weight– specific handling difficulties– part orientation - symmetry
Component handling Component size &weightHandling difficultiesBeta (rotational)symmetry:0135Convenient sizeOne hand onlySmallFiddly or requirestoolsLarge / heavy2 hands or toolsVery large / heavy2 people or hoistNo handlingdifficultiesNeed care to gripAdherence, delicate,sharp / abrasiveDifficult to gripFlexible,untouchable,awkwardTangling & severenestingAny orientationEasy to orient:orientation easy tosee and mistakeproofTricky to orient:Orientation difficultto see but mistakeproofDifficult to orient:Orientation difficultto see – mistakespossibleAny orientationEasy to orient:orientation easy tosee and mistakeproofTricky to orient:Orientation difficultto see but mistakeproofDifficult to orient:Orientation difficultto see – mistakespossibleabout axis of insertionAlpha (end-to end)symmetry:perpendicular to axis of insertionEase of delivering, handling and orientingeach component in preparation for assemblyTOTAL HANDLINGSCOREScore20
Maximise symmetry
Fitting & fixing Insertion / holding process Securing / fixing processes Additional (non-assembly) processes Scores based on:––––––does it need a fixture?The assembly directionAlignment difficultiesRestricted vision or accessInsertion forceEtc.
Component insertion / holding process Gripping / holdingduring insertion0135Holding simpleduring insertion no tools neededNeed tools to gripduring insertion but simpleDifficult to holdsecurely duringinsertionNo suitable / easyto access grippingsurfaces duringinsertionSelf sustaining - stays in place without holding downNeeds holding inplace – securedlaterView during insertionClear view duringinsertionView partlyobscured duringinsertionView badlyobscured duringinsertionNo view duringinsertion – feel onlyAccessClear accessduring insertionPartly obscuredaccess duringinsertionBadly obscuredaccess duringinsertionNo access to insertInsertion directionStraight line fromaboveStraight line, fromsideStraight line frombelowNot in a straightlineInsertion resistanceNo resistanceLight resistanceSignificantresistanceLarge resistance –need leverageHolding downTOTAL INSERTIONSCORE5Score25
8Fixing / securing processes 0135Threaded fastenersNo threaded fastenersSelf drilling / tappingscrewsStud / bolt & nutScrewNut, bolt & washer(separate loose parts)Non-threadedfastenersSnap fit or light pushfitRivetSimple crimping orbendingDifficult crimping orbendingSoldered / WeldedjointsNo welded jointsSimple solder / weldDifficult weldGlued jointsNo glued jointsSimple glued jointDifficult glued joint
Fixing & joining Eliminate / minimise fasteners– Separate fasteners of same type– Different types fasteners– Avoid threaded fasteners Carefully position fasteners– Away from obstructions– Provide flat surfaces– Provide proper spacing betweenfasteners Simple fastening–––– Self fastening featuresOne handed assemblyParts secured on insertionSingle linear motionMinimise assembly toolsParts should easily indicateorientation direction– Self alignment– Self orienting / no orientation needed
Additional (non-assembly) processes 01335Additional screwingNo threaded fastenersSome additionalscrewingSignificant additionalscrewingSettingNo setting requiredSimple / quick settingComplex / slowsettingTest & measureNo testing & measuringEasy / quick testingDifficult / slow testingFill / emptyNo filling / emptyingSimple / quick fill /empty liquid / gasComplex / slow fill /empty gasRe-orientationNo reorientationSmall reorientationSignificantreorientation
Product architecture
System optimisationProduct architecture designWholeproductSub-system optimisationAssemblyAssembly optimisationComponent minimisation,handling, fitting, feedingComponent optimisationComponent commonalityProcess selectionProcess optimisationComponent
Functional elements physical elements Function 1Function 2Function 3Function 4Function . nA product’sarchitecture isthe way inwhich thefunctionalelements areassigned to thephysicalelements andthe way inwhich theseelementsinteractPart 1Part 2Part 3Part 4Part 5Part 6Part 7Part . n
Integrated product structures .Part 1Function 1Part 2Function 2Part 3Part 4Function 3Part 5Function 4Part 6Part 7Function . nPart . n
Modular product structures .Module 1Part 1Function 1Part 2Function 2Part 3Function 3Part 4Module 2Part 5Function 4Part 6Module 3Function . nPart 7Part . nModule 4
Product change Integral products– Changes to one element can result in changes to many others– A functional change demands physical change Modular products– changes can be made to isolated elements independently Design goal .– Minimise physical changes to enable functional changes
Types of functional change . Upgrade: more memory in a PC Add-ons: a new flash gun for a camera Adaptation: different power supplies for differentmarkets Wear / maintenance: replacement razor blades Consumption: replacement film, or printer ink Flexibility in use: changeable lenses
Example: Cooke movie lenses Lots of commonality inproduction:– Common external mechanics,different lens and iris assemblies– Common parts– Common features on parts: differentlengths, reuse of CAM– Common tool set: radii, thread forms,holes etc– Common processes: designed forsingle M/C tool Modularity: optical elements, lensto camera interface, Iris assembly
321814501002514181675322521275035121804075 10065135
Product platforms
Product rangeProduct range planningPlatform planningSystem optimisationProduct architecture designProduct rangeWholeproductSub-system optimisationAssemblyAssembly optimisationComponent minimisation,handling, fitting, feedingComponent optimisationComponent commonalityProcess selectionProcess optimisationComponent
Volkswagen A-PlatformAudi A3Audi TT coupeAudi TT roadsterVW Golf IVVW Beetle &convertible VW BoraSkoda OctaviaSeat Toledo Successor(Coupe, Saloon,Convertible)Aprox 19 vehicles based on A-platformVW estimates development and investment costsavings of 1.5 billion/yr using platforms
VW Platform: common components Source: Shimokawa, K., Jurgens, U., and Fujimoto, T. (Eds.), 1997, Transforming AutomobileAssembly, Springer, New York.
Market segmentation grid Segment CSegment BSegment AMarket 1Market 2Market 3Shared product platform /technology - common subsystemsand interfaces
No leveraging Uniqueproductstargeted atindividualsegmentsSegment CSegment BSegment AMarket 1Market 2Market 3Shared product platform /technology - common subsystemsand interfaces
Horizontal leveraging Reuse ofplatformelementsacrossmarkets, andwithin asegmentSegment CSegment BSegment AMarket 1Market 2Market 3Shared product platform /technology - common subsystemsand interfaces
Vertical leveraging Reuse ofplatformelementswithin amarket andacrosssegmentSegment CSegment BSegment AMarket 1Market 2Market 3Shared product platform /technology - common subsystemsand interfaces
Beach-head leveraging Segment CSegment BSegment AMarket 1Market 2Market 3Shared product platform /technology - common subsystemsand interfacesHorizontaland verticalreuse ofplatformelementsacrossmarkets andacrosssegments
Example: Cooke lenses TelephotoNormalWide angle35mm film16mm filmDigitalZoom lensesProduction methods, housings, irises, optics
System architecture vanced201320152021
System roadmap 2012Functionality2013Simple A B C D EMiddle P Q R S TAdvanced20152021 F G U V W X Y Z X Y CoretechnologiesSimple New materials New sensorsMiddle Existing sensor New materialsAdvanced Communications RFID GPS Data logging Data management
StrategicProduct rangeProduct range planningPlatform planningSystem optimisationProduct architecture designProduct rangeWholeproductSub-system optimisationAssembly optimisationComponent minimisation,handling, fitting, feedingAssemblyComponent optimisationComponent commonalityProcess selectionProcess optimisationTacticalComponent
StrategicWhen to consider platforms etc .PlatformPlanningProduct onalityFeature & ProcessCommonalityAd-HocConcept designConsciously Different componentsUnconsciously different componentsDesign DecisionsDetail engineering
Thank you
Design for manufacture Design for assembly Product architecture Product platforms. A brief history lesson Eli Whitney . Originally a blacksmith: . Product design Market development Idea Manufacturing process design. 1990s DfX and Prod