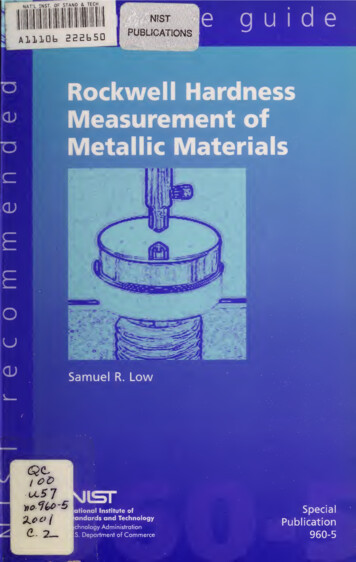
Transcription
NISI;PUBLICATIONSAlllOb 222b5DguideRockwell HardnessMeasurement ofMetallic MaterialsSamuel R.LowocS?ational Institute ofandards and Technologyichnology Administrationa.I2 S.Department of Commerce
RecommendedNISTPracticeGuideSpecial Publication 960-5Rockwell HardnessMeasurement ofMetallic MaterialsSamuelR.LowMaterials Science andEngineering LaboratoryJanuary 2001U.S.Department of CommerceDonaldL.Evans, SecretaryTechnology AdministrationKaren H. Brown, Acting UnderCommerceSecretary offor TechnologyNational Institute of Standards and TechnologyKaren H. Brown, Acting Director
Certain commercial entities, equipment, or materialsmay be identified indocument in order to describe an experimental procedure or conceptadequately. Such identification is not intended to imply recommendation orendorsement by the National Institute of Standards and Technology, nor is itintended to imply that the entities, materials, or equipment are necessarily thethisbest available for the purpose.National Institute of Standards and TechnologySpecial Publication 960-5Natl. Inst. Stand. Technol.Spec. Publ. 960-5116 pages (January 2001)CODEN: NSPUE2U.S.GOVERNMENT PRINTING OFFICEWASHINGTON:2000For sale by the Superintendent of DocumentsU.S. Government Printing OfficeInternet: bookstore.gpo.govPhone: (202)512-1800Mail: Stop S SOP, Washington,DC20402-0001Fax: (202)512-2250
FOREWORDThe Rockwell hardnesstestcontinues to be applied as a tool for assessingon the acceptable materialAdhering to "good practice"procedures when performing Rockwell hardness measurements andthe properties of a product while the toleranceshardness have become tighter andcalibrationsisof this Guideresultsandtotighter.a beneficial step to reducingisto explain the causesmeasurementerrors.The purposeof variability in Rockwell hardnesstestsupplement the information given in test method standards withgood practice recommendations. Although this Guide is directed more towardsRockwell hardness having the greatest concern for accuracy inthe users oftheirmeasurements,much of thethat only require test results toaccuracyisnot asinformation givenisalso applicable for usersbe within wide tolerance bands, where highcritical.More information onthe SP 960 series can be found on the internet athttp;//www.nist.gov/practiceguides. This web site includes a completelist of NIST Pratice Guides and ordering information.iii
ACKNOWLEDGMENTSThe author wouldlike tothank the following persons for sharing theirexperience and providing information for this Guide. Their input and reviewhas provided a link to the practical world of Rockwell hardness testing.*T.Robert Shives, ConsultantRichard Antonik,Robert A.Thomas P.EllisSUN-TEC Corporationand Richard'A.Farrell,Ellis,David L.Ellis Co., Inc.Mitutoyo America CorporationGiancarlo Mazzoleni and Douglas B. McGhee,NewageTestingInstruments, Inc.Michael L. Milalec and Richard J. Snow, Gilmore Diamond Tools,Inc.PaulM. Mumford, United Calibration CorporationEdward L.Tobolski,Wilson Division of Instron CorporationThe author would also like to thank present and former NIST co-workersJames L. Fink, Carole D. Flanigan, Robert J. Gettings, Walter S. Liggett, Jr.,David J. Pitchure, John H. Smith, and John Song for their contributions towardsthe Rockwell hardness standardization program at NIST.*The acknowledgements of the persons and companies listed above shouldnot be interpreted as an endorsement by NIST of their products or services.v
Table of ContentsList of FiguresixList of Tablesxii1.Introduction12.Rockwell Hardness Test23.4.5.6.2. 1Significance of the test22. 2Rockwell indentation test principle22.3Rockwell hardness scales42.4Rockwell hardness number42.5Testmethod standards6Test Procedure93. 1Choosing the appropriate Rockwell scale3.2Test surface preparation133.3Rockwell hardness testing machine133.4Hardness measurement26Reference Test Block Standards374. 1Primary reference test blocks374.2Secondary reference404.3Use of referencetest blocksstandards41Hardness Machines44test blockVerifications of Rockwell95. 1Direct verification445.2Indirect verification475.3Correctingmeasurement biasesMonitoring Test Machine Performance49516.1Reproducibility516.2Daily verification52vii
Table of Contents7.8.9.10.Reducing Measurement Differences and Errors7. 1Reduce machine component operating7.2Verify7.3Measurementerrorsmachine measurement intyand Uncertainty53565658error58Status of Rockwell Hardness Standardizationin the Year 2000639.1United States639.2International65BibliographyAnnex A: Applied ForceAnnex69EffectB.2 Effect of dwell times1C:78Use of NIST Rockwell C ScaleRecommendationsfor7374Effect of force application rate1C.71B: Rockwell Hardness Testing Cycle EffectB.AnnexSRMTest BlocksuseC.2 Calculation of certified values for arbitrary locationsvffi5355locationsTraceability, Error,53848486
Table of ContentsList of FiguresFigure1:Plots of force vs. time (a)time (b) for anand themeasurements hcycle partsFigure 2:Forceand indenter-depthHRC test illustrating thedifference in indenter depth.3time plot (Figure A)vs.vs.testingand indenter-depthvs.time plot (Figure B) demonstrating the effect of anincreaseHRAFigure 3:inthe preliminary-force for a Rockwell16testForcetime plot (Figure A)vs.and indenter-depthvs.time plot (Figure B) demonstrating the effect of anincreaseFigure 4:inthe total-force for a RockwellHRAtest17Diagram of cross-sectional view of spheroconicaldiamond indenter tip2428Figure5:Eight steps of the Rockwell test cycleFigure6:Four examples of the hardness profile across thetest surface of 25 HRC test blocks, illustrating howthe non-uniformity in hardness can vary within ablock and differs from block to block. Each linerepresents a hardness change of0.02 HRC.Light to dark areas represent hard to soft areasFigure7:Hardnessprofileacross the test surface of a38NISTThe NIST calibration measurements areindicated by the solid circles, and the locations oftest block.the certified values for untested locations areindicated by theFigure 8:Figure 9:openAlternate pattern for mentsof the three bias points corrected by a50correction curveFigure 10: Illustration of reproducibility data taken over ten daysFigure 11:48NIST Rockwell hardnessstandardizing machine5157
Table of ContentsFigure 12:General trend of the difference between NIST andU.S. industry Rockwell C scales. The line representsthe approximate increase in the HRC scale asdetermined by NIST (for hardness levels as indicatedon the bottom axis) with respect to the HRC scaleused by U.S. industry prior to development of theNISTFigure 13:Results of 1999 international comparison of HRCscale.Figure A.1:64scaleThe heavyChangechangeininline indicates theNIST data67due to adiamond indenterthe Rockwell hardness valuethe preliminary force forscales (Figure A) and selected ball scales (Figure B)Figure A. 2:Changechangeinin(Figure A)71due to adiamond indenter scalesthe Rockwell hardness valuethe total force forand selectedFigure A. 3: The possible offsetinball scales (Figure B)71Rockwell hardness measurementvalues that could be obtained for the diamond indenterscales by varying the applied preliminary forces andtotal forces within theandFigure B.1:Figure B.2:theASTM tolerancesISO tolerances(Figure A)72(Figure B)Force and indenter depth oscillations that canoccur when the force application rate is too fastChangeinapparentHRC hardness duetochanges76inthe additional force application rate (indenter velocity)Figure B.3:Expanded view of thematerial creep77and recoveryduring the dwell times of a Rockwell hardness test78Figure B.4: Relationship between the preliminary force dwelltimeandtheHRC measurement valuetest blocks at threefor steelhardness levelsFigure B.5: Relationship between the total force dwell timetheHRCat threemeasurement valueandfor steel test blocks80hardness levelsFigure B.6: Relationship between the total force dwell timeHRB measurementhardnessx79levels.and thevalue for brass test blocks at three81
#Figure B. 7Relationship between the recovery dwell timeHRC measurement valueand thefor steel test blocks at threehardness levelsFigure C.1Test block surface illustrating the locations(lettersgivenFigure C.282Ainthrough K) of certified hardness valuesTable C.2Test surface of the Rockwell hardnessindicating the locationindentations87SRMsand sequence of certification90
Table of ContentsList ofTableTablesRockwell hardness scales with the corresponding1:indenter type, applied forces and typical applicationsRanges of Rockwell scales givenTable 2:Table A.Table1:O 1:ISO standardsin51272Specified test forces with tolerancesHypothetical certified hardness values for theaverage of six specifictest block locationsas87illustrated in Figure 0.1Table 0.2: Hypothetical certified hardness values for specifictest block locations.that locationindentationx 4),0,The xy is-y coordinate system is such(NISTat the block centerand oriented withbottom of the block astheNIST logoat theillustrated in Figure 0.188Table C.3: Hypothetical semivariogram coefficients thatdescribe test block nonuniformity and repeatabilityTable 0.4: HypotheticalNIST hardness readingsfor specific test89block locationsTable 0.5: Matrixr91Table 0.6: Inverse matrix r 1 with elements g TableO 7:Table 0.8:xii91Sources of uncertainty for the certified average HROhardness value with hypothetical values to be usedin the examplesThe coordinates for the locations usedExample 2calculations of89in92the100
1INTRODUCTIONWorkingin a ball-bearingmanufacturing plant in 1919, StanleyP.Rockwellinvented the Rockwell hardness test as a tool for obtaining a rapid andmore accurate measure of the hardness of ball races . Soon after,Charles H. Wilson expanded on Rockwell's invention, and he advanced theRockwell hardness test into what is today the most widely used method foracceptance testing and process control of metals and metal products. Sinceitsdevelopment, the popularity of the Rockwell hardnessgrown. The Rockwell hardnesstesttesthas steadilycontinues to be applied as a tool forassessing the properties of a product while the tolerances on the acceptablematerial hardness havebecometightermanufacturing tool has developed intomeaningful measurement resultsThe once-thought-ofa metrological instrument. To achieveandtighter.in these circumstances,it isimportant thatmake every effort to reduce measurement errors. This is more easilyaccomplished when the influences contributing to the error in a Rockwellthe userhardnesstest areknown, and thereisan understanding of what can be done toreduce these errors. Adhering to "good practice" proceduresRockwell hardness measurements and calibrationsmeasurement errors.iswhen performinga crucial step to reducingThe purpose of this Guide is not to specify the requirements for conductinga Rockwell hardness test. Test method standards published by national andinternational standards writing organizations, such as the American SocietyTesting and Materials(ASTM) and theforInternational Standards Organization(ISO), provide specific requirements and procedures for Rockwell hardnessThe intention of this Guide is to explain the causes of variability inRockwell hardness test results and to supplement the information given in testmethod standards with good practice recommendations. Although this Guidetesting.isdirectedmore towardsthe users of Rockwell hardness having the greatestconcern for accuracy in their measurements,ismuch of theinformation givenalso applicable for users that only require test results to be withintolerance bands, where high accuracyRockwell hardnessplastics;however,isthisisnot ascritical. It iswiderecognized thatoften used for testing non-metallic materials such asGuideisprimarily applicable to the testing of metallicmaterials.This Guide also provides recommendations for conducting verifications ofRockwell hardness machines based on the procedures specified by the testmethodstandards.Someprocedures recommended by this Guide exceedcurrent requirements of the test methods; however, they can be very usefulin helping todetermine and limit sources of measurementerror.1
Rockwell Hardness TestROCKWELL HARDNESS TEST2the Test2.1 Significance ofThe Rockwell hardness test is an empirical indentation hardness test. Itsworldwide adoption has likely resulted from the many advantages provided bythe test method. The test is fast, inexpensive, and relatively non-destructive,Theleaving only a small indentation in the material.simplicity in the operationof a Rockwell hardness machine has provided the added advantage thatRockwell hardness testing usually does not require a highlyBy waytestskilled operator.of correlation with other material properties, the Rockwell hardnesscan provide important information about metallic materials, such as thetensile strength,wearresistance,andductility.Thetest is generally useful formaterial selection, for process and quality control, and for acceptance testingof commercial products. Consequently, in today's manufacturing facilities,Rockwell hardness machines can be found in use in almost every testingenvironment, from the hot, oily surroundings of some manufacturing facilities,to environmentally controlled metallographicand calibration laboratories.2.2 Rockwell Indentation Test PrincipleThe Rockwell hardnesstest isone of severalcommonindentationhardness tests used today, other examples being the Brinell hardnessand Vickers hardnesstest.Most indentation hardnessthe deformation that occurswhentests are athe material under testspecific type of indenter. In the case of theof force are applied to the indenteristestmeasure ofpenetrated with aRockwell hardness test, two levelsand with specified dwellat specified ratesRockwell C scale (HRC) test in Figure l Unlikewhere the size of the indentation is measuredfollowing the indentation process, the Rockwell hardness of the material isbased on the difference in the depth
TableofContents ListofFigures ix ListofTables xii 1.Introduction 1 2.RockwellHardnessTest 2 2.1Significanceofthetest 2 2.2Rockwellindentationtestprinciple 2 2 .