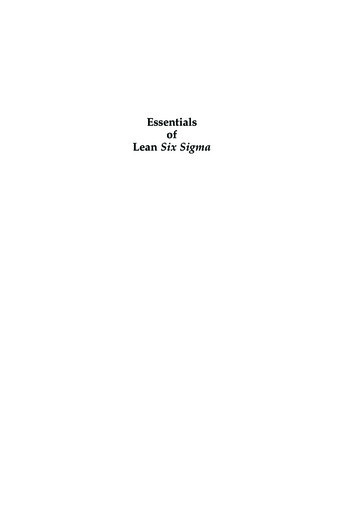
Transcription
EssentialsofLean Six Sigmafm-P370502.indd i4/21/2006 5:16:52 PM
fm-P370502.indd ii4/21/2006 5:16:53 PM
EssentialsofLean Six SigmaSalman TaghizadeganAMSTERDAM BOSTON HEIDELBERG LONDONNEW YORK OXFORD PARIS SAN DIEGOSAN FRANCISCO SINGAPORE SYDNEY TOKYOAcademic Press is an imprint of Elsevierfm-P370502.indd iii4/21/2006 5:16:53 PM
Butterworth–Heinemann is an imprint of Elsevier30 Corporate Drive, Suite 400, Burlington, MA 01803, USALinacre House, Jordan Hill, Oxford OX2 8DP, UKCopyright 2006, Elsevier Inc. All rights reserved.No part of this publication may be reproduced, stored in a retrieval system, or transmitted in anyform or by any means, electronic, mechanical, photocopying, recording, or otherwise, without theprior written permission of the publisher.Permissions may be sought directly from Elsevier’s Science & Technology Rights Department inOxford, UK: phone: ( 44) 1865 843830, fax: ( 44) 1865 853333, E-mail: permissions@elsevier.com. You may also complete your request on-line via the Elsevier homepage (http://elsevier.com), by selecting “Support & Contact” then “Copyright and Permission” and then “ObtainingPermissions.”Recognizing the importance of preserving what has been written, Elsevier prints its books onacid-free paper whenever possible.Library of Congress Cataloging-in-Publication DataApplication submittedBritish Library Cataloguing-in-Publication DataA catalogue record for this book is available from the British Library.ISBN 13: 978-0-12-370502-0ISBN 10: 0-12-370502-9For information on all Butterworth–Heinemann publicationsvisit our Web site at www.books.elsevier.comPrinted in the United States of America06 07 08 09 1010 9 8 7654321Working together to growlibraries in developing countrieswww.elsevier.com www.bookaid.org www.sabre.orgfm-P370502.indd iv4/21/2006 5:16:53 PM
To my loving wife, Leila and our daughters, Sara and Setareh.To my father and my late mother who asked so little and gave so much.fm-P370502.indd v4/21/2006 5:16:53 PM
fm-P370502.indd vi4/21/2006 5:16:53 PM
ContentsPrefacexiiiAcknowledgmentsAbout the AuthorxvxviiPART IStatistical Theory and ConceptsChapter 1Introduction to Essentials of Lean Six Sigma(6s) Strategies1.1 Lean Six Sigma (6s) Concept Review1.1.1 The Philosophy11.1.2 Lean/Kaizen Six Sigma Engineering1.2 Six Sigma Background31.3 Some Six Sigma Successes412Chapter 2Statistical Theory of Lean Six Sigma (6s) Strategies2.1 Normal Distribution Curve72.2 Six Sigma Process Capability Concepts72.2.1 Six Sigma Short-Term Capability102.2.2 Estimation of Six Sigma Long-Term Capability13viifm-P370502.indd vii4/21/2006 5:16:53 PM
viiiContentsChapter 3Mathematical Concepts of Lean Six SigmaEngineering ss Modeling—The Heart of Lean Six SigmaThe Normal Distribution25The Standard Normal Distribution27t-Distribution293.4.1 Confidence Interval for the Difference ofTwo Means29Binomial Distribution32Poisson Distribution34Exponential Distribution35Hypergeometric Distribution35Normality Tests363.9.1 Kurtosis373.9.2 Anderson Darling37Reliability Engineering and Estimation38Quality Cost4121PART IISix Sigma Engineeringand ImplementationChapter 4Six Sigma Continuous Improvement4.1 Six Sigma Continuous Improvement Principles4.2 Six Sigma Systems444.3 Six Sigma Improvement and Training Models4345Chapter 5Design for Six Sigma: Roadmap for SuccessfulCorporate Goals5.1 Design for Six Sigma (DFSS) Principles5.2 Design for Six Sigma Steps515.3 Six Sigma Ergonomics54fm-P370502.indd viii494/21/2006 5:16:53 PM
Contents5.4 Tools and Techniques5.5 Process Managementix5557Chapter 6Design for Lean/Kaizen Six Sigma6.1 Lean Six Sigma and Principles596.1.1 Elements of Lean Manufacturing/Production616.1.2 Waste Types in Lean Manufacturing636.1.3 The Five Lean Themes and Steps666.2 The Elements of Lean Performance Measurements686.2.1 Strategic Measurement Model696.2.2 Key Elements That Make a Product Successful in theMarketplace716.3 Competitive Product Benchmarking Concepts716.4 Integration of Kaizen, Lean, and Six Sigma736.4.1 Six Sigma, Lean, and Kaizen Principles736.4.2 Prolong Production Performance (PPP)766.4.3 A Lean Concept in Reduction of Lead Time796.5 Lean/Kaizen Six Sigma Infrastructure Evolution Tools andHighlights in Summary806.5.1 Corporate Commitment806.5.2 Steps to Achieve the Six Sigma Goals816.6 Mathematical Modeling of Lean Six Sigma Relations846.6.1 Lean Six Sigma Experimental Design85Chapter 7Roles and Responsibilities to Lean Six Sigma Philosophyand Strategy7.1The Roadmap to Lean Six Sigma Philosophyand Strategy1037.2 Creation of Six Sigma Infrastructure1037.2.1 Executive Sponsor1047.2.2 Champion1047.2.3 Master Black Belt1047.2.4 Black Belt (Team Leader)1057.2.5 Green Belt (Team Participant)1067.2.6 Team Recognition/Compensation106fm-P370502.indd ix4/21/2006 5:16:53 PM
xContentsChapter 8Road Map to Lean Six Sigma Continuous ImprovementEngineering Strategies8.1 Six-Sigma Continuous Improvement Engineering1078.2 Definition and Measurement1088.2.1 Phase 0: Process Definition/Project Selection1088.2.2 Phase I: Process Measurement1168.3 Evaluation of Existing Process Sigma/Baseline Sigma1438.4 Data Analysis1438.4.1 Phase II: Process Analysis1438.5 Optimization and Improvement1508.5.1 Phase III: Process Improvement1508.6 Evaluation of New Sigma1598.7 Process Control1608.7.1 Phase IV: Process Control and Maintain160PART IIICase StudiesChapter 9Six Sigma Green and Black Belt Level Case Studies9.1 Case Study: Methodology for Machine Downtime Reduction—A Green Belt Methodology1759.1.1 Phase 0: Problem Statement1759.1.2 Phase 1: Data Collection and Measurement1759.1.3 Phase 2: Analysis of Measurement1799.1.4 Phase 3: Improve and Verify Analyzed Data1799.1.5 Phase 4: Control and Maintain1829.2 Case Study: Methodology for Defect Reduction in InjectionMolding Tools—A Black Belt Methodology1849.2.1 Phase 0: Definition and Statement of Issues1849.2.2 Phase 1: Data Collection and Measurement1849.2.3 Phase 2: Analysis of Collected Data1919.2.4 Phase 3: The Process of Improvement1919.2.5 Phase 4: The Process of Control andMaintenance197fm-P370502.indd x4/21/2006 5:16:53 PM
ContentsxiChapter 10Six Sigma Master Black Belt Level Case Study10.1 Case Study: Defect Reduction in Injection Molding a MultifactorLean Central Composite Design Approach20510.1.1 Scope of Injection Molded Parts20510.1.2 Scope of Study20510.2 Composite Design Methodology20610.3 Modeling21210.4 Simulation21510.5 Conclusion222Bibliography223Appendix: Statistical Tables Used for Lean Six SigmaAI: Highlights of Symbols and Abbreviations227AII: Chapter 10 Case Study Extended Equations229AIII: Values of y exp( h)233AIV: DPMO to Sigma to Yield % Conversion Table235AV: Standard Normal Distribution237AVI: Critical Values of t-Distribution241AVII: Critical Values of Chi-Square Distribution with Degreesof Freedom245AVIII: Upper Critical Values of the F-Distribution for df1Numerator Degrees of Freedom and df2 DenominatorDegrees of Freedom251AIX: Deming’s Condensation of the 14 Points forManagement265AX: Scorecard for Performance Reporting267AXI: Scorecard for Performance Reporting (Partly CompletedExample)269Index271fm-P370502.indd xi4/21/2006 5:16:53 PM
fm-P370502.indd xii4/21/2006 5:16:53 PM
PrefaceABOUT THIS BOOKBefore the 1970s, the industry standards were based on 3s and percent (%)defect. Now, as population grows and industrial volume due to global economybecomes mass production, the 3s and percent defect evaluations are no longervalid. The 6s and defect per million are today’s standard for ultimate customersatisfaction and maximum profitability. Knowing that customer satisfaction is thenumber one priority on any organization’s list, the success of any company dependson quality and competitive product pricing. Today the globalized market allows nospace for error. Thus, Six Sigma is necessary for all organizations. The theory ofSix Sigma demonstrates the bottom line and customer satisfaction improvement.Unlike other programs that concentrate on quality only, Six Sigma focuses oncustomer satisfaction and the bottom line. This also means the highest quality:As defects drop to 3.4 per million, quality improves dramatically.This book explains the Lean Six Sigma concepts, the essential theory and analysisfrom the engineering point of view in three different parts. Part I: Statistical Theoryand Concepts; Part II: Six Sigma Engineering and Implementation; and Part III: CaseStudies. Throughout this book numerous examples have been cited, particularly inthe plastics industry of injection molding. All other manufacturers may also benefitto a great extent. Consequently, any other organization may engineer their Six Sigmaprogram using this book, as well. A brief description of each chapter follows:Part I. Statistical Theory and ConceptsChapter 1. Reviews Lean Six Sigma concepts and background (history).Chapter 2. Demonstrates normal distribution, process capability estimation of1 sigma through Six Sigma.Chapter 3. Explains essentials of mathematical concepts in Lean Six Sigmaengineering strategies, as well as a review of standard normal distribution and normality tests.xiiifm-P370502.indd xiii4/21/2006 5:16:53 PM
xivPrefacePart II. Six Sigma Engineering and ImplementationChapter 4. The essentials of Six Sigma continuous improvement principles andtraining models.Chapter 5. The essentials of design for Six Sigma principles, tools, andtechniques.Chapter 6. The essentials of design for Lean Six Sigma and training models.Chapter 7. The roles and responsibilities to Six Sigma philosophy and SixSigma infrastructure.Chapter 8. The road map to Lean Six Sigma continuous improvement engineering strategies.Part III. Case StudiesChapter 9. Case studies with complete Six Sigma applications in injectionmolding plastics manufacturing for Green and Black Belts.Chapter 10. An expanded version of the case study published by the author forthe Black Belt level in reduction or minimization of variation in aninjection molding plastic industry.Salman Taghizadeganfm-P370502.indd xiv4/21/2006 5:16:53 PM
AcknowledgmentsThe author wishes to thank Keith Boyle (Quality & Productivity Resources)for his inspiration, assistance, and contributions throughout this book. He alsoprovided my Black Belt training at the University of California at San Diego.Much appreciation goes to my family. To my wife, Leila, and my daughter, Sara,thank you for your long-lasting patience and continuous support. I would like toacknowledge Hunter Industries for supporting and giving me the opportunity toimplement Lean Six Sigma concepts in practice. I thank Diane Clark for hersupport of the publication of this book (and for putting in long hours and makingthis book easier to read). Finally, my thanks to Joel Stein at Elsevier Science forhis support and patience throughout the publishing process and other membersof the Elsevier Science team for their support and assistance in making this worka reality. My thanks to Shelley Burke for her assistance throughout the publishingprocess. Furthermore, thanks goes to Carl M. Soares for managing the Publication process.xvfm-P370502.indd xv4/21/2006 5:16:53 PM
fm-P370502.indd xvi4/21/2006 5:16:53 PM
About the AuthorDr. Salman Taghizadegan has substantial experience in chemical and plastics processing, design, control, and analysis. He received his B.S. in chemistryfrom Western Illinois University, his B.S. in chemical engineering from theUniversity of Arkansas, his M.S. in chemical engineering from the Texas A&MUniversity, and his Ph.D. in chemical engineering with emphasis in plastics fromthe University of Louisville.He has over 20 years of academic and full-time industrial experience in plastics and chemical processing, design, and control engineering, primarily in injection molding industries. He has authored numerous technical publications andhas spent most of his professional career as an adjunct professor in engineering,as a highly technical specialist in the plastics industry, as a leader in quality andprocess improvement, and as the manager of waste reduction in the manufacturing environment. Dr. Taghizadegan is certified Six-Sigma Black Belt and MasterBlack Belt through the University of California at San Diego and the universityof San Diego. He is a member of the Society of Plastics Engineers.xviifm-P370502.indd xvii4/21/2006 5:16:53 PM
Six Sigma Green and Black Belt Level Case Studies 9.1 Case Study: Methodology for Machine Downtime Reduction— A Green Belt Methodology 175 9.1.1 Phase 0: Problem Statement 175 9.1.2 Phase 1: Data Collection and Measurement 175 9.1.3 Phase 2: Analysis of Measurement 179 9.1.4 Phase 3: Improve and Verify Analyzed Data 179 9.1.5 Phase 4: Control and Maintain 182 9.2 Case Study: