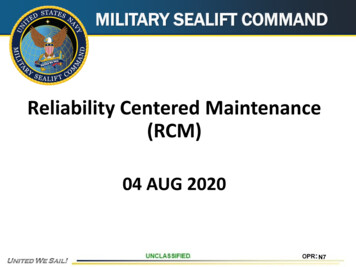
Transcription
MILITARY SEALIFT COMMANDReliability Centered Maintenance(RCM)04 AUG 2020N7
MSC RCM Process MSC’s Maintenance Philosophy Reliability Centered Maintenance (RCM) Maintenance Effectiveness Review (MER) SAMM AuditN7
Framework MSC MissionN7
MSC’s Maintenance Philosophy People: Maintain trained, motivated andforward-thinking shipboard andshore-side personnelN7 This Photo by Unknown Author is
MSC’s Maintenance Philosophy Tools: Provide the necessary technology,tools, and equipment to analyze anddocument operating conditions andmaintenance history, in order toenhance maintenance planning andexecution This Photo by Unknown Author isN7
MSC ENGINEERING APPLICATIONSShipside Remote ToolsShoreside: MSC IS PortalSAMMSAMMOil AnalysislabCMSLO ExpertsystemFluid AnalysisSystem (FAS)CombustionAnalysisMSC Oil Analyst(asCombustionAnalystVibration AnalysteduirreqDataReplicationDexterCMS: Lube OilSampling,Vibration,CombustionShips LogShipboard UsersCombustiondata collector)Vibration ExpertsystemVibration nceManagement(LAMM)Pocket PCShip checkLog BookLog BookPM, MachineryHistory, Repair,WorkbookPM, MachineryHistory, Repair,WorkbookCQA Web TrackerCorrectiveMaintenanceVibrationdata collectorShips LogSMART / CQAFeedbackTracking systemSMART / CQASmart llectionPENGMaintenanceDecision SupportToolDataReplicationPENGPENG AvailabilityStaff7/23/2008N7
MSC’s Maintenance Philosophy Maintenance Management Approach: Comply with commercial regulatory andinternational requirements Maintain Flexibility in addressingmaintenance needs through a mix ofcontinuous ship’s force maintenance,technical representative service, andindustrial assistanceN7
MSC’s Maintenance Philosophy Ensure Fiscal responsibility and authority: Align life cycle management responsibilitieswith fiscal oversight to optimize shipavailability for customer requirements usingbest-value principles.N7
MSC’s Maintenance Philosophy Promote Optimization: Continue to improve life cyclemanagement and engineeringprocesses Evaluate the application of newtechnologies to improve life cyclemanagement effectivenessN7
Maintenance Strategy More simply put, the 5-Rs: The Right Maintenance on the Right Equipment, at the Right Time with the Right people in the Right way Employ an efficient and costeffective maintenance approachthat strives to ensure safety, meetsregulatory requirements, andsupports reliability in support ofMSC missions.N7
Reliability Centered Maintenance Reliability Centered Maintenance:A methodology for determiningApplicable & Effective preventivemaintenance requirements basedon the analysis of MachineryHistory and the Experience ofShips’ PersonnelN7
Commercial & Government AgenciesEmbrace RCMN7
Why Implement RCM? Common approach to justify PM changes Results based on machinery history data Justification for the task is recorded PM Feedback adjudicated more quickly Eliminates non-value-added PMs Ensures accurate/value-added PMs Best practices detailed in PM narratives Identifies Maintenance gaps (3 types)N7
What Is “Maintenance”?Maintenance consists of actionstaken to ensure components,equipment, and systems providetheir intended functions whenrequired to do so.N7
Understanding Function Basic requirement of maintenanceis to preserve function Not necessarily design / appearance Defining “intended function”properly is essential Procurement specifications setacceptance criteria In-service requirements may be lessrigorousN7
We do maintenance because: We believe hardware reliabilitydegrades with age There is something we can doto restore or maintain theoriginal reliability It pays for itselfN7
7 Backfit RCM Questions Function: What function does the hardwareperform? Functional Failure: What failure will interruptthe function? Failure Mode: What causes the functionalfailure? Failure Effect: What happens when the failureoccurs? Failure Consequence: What is the impact of thefailure? Task Identification: Is the PM based oncondition, time, hidden failure, etc? Redesign or No Task Required: What actionshould be taken if a proactive task is notidentified?N7
Amplification Functional Failure The term that describes the loss offunction If the function is to provide water at 60PSI, 100-120 degrees F The Functional Failure is - it doesn’tprovide water at 60 PSI, 100-120 deg F Failure Mode What caused the failure? Materialcondition after failure (e.g. seizedbearing) Reliability The ability to provide its intendedfunction when called upon to do soN7
Goal being e: MakingCommon SenseCommon Practice 3rdEditionLoss of Ship Availability andEquipment DowntimeUnnecessary Maintenance RepairsandRoot Cause AnalysisReliabilityCentered MaintenanceBy Ron MooreN7
Three types of maintenanceType iveShipaltsCorrect unsatisfactoryconditionsMinimize unsatisfactoryconditionsEliminate unsatisfactoryconditionsAdjust orReplaceAlignComponents ComponentsDiagnose ConditionTestInspectPreempt WearoutRestoreReplaceOtherOtherSchedulingSample TasksPlanned /Unplanned Technicalrepresentativevisits Voyage repairs CasualtycorrectioneffortsCheck HiddenFunctionUpgrade to MeetNewSpecifications(Revolution)ServicePlanned (Recurring Action) Rebuild/restore Oil or grease Evaluate conditions:- Vibration analysis- Infrared imaging- Performance testModify to MeetCurrentRequirements(Evolution) Discard & replace Top off fluids- ND test- Oil analysis- Visual inspectionsPlanned (One-Time Action) Redesign component(s) Redesign equipment Redesign system(s)N7
Recurring PM Task Types in ken c ofa Failure Modethat can beMeasuredAccurately &Consistently“Life Renewal”(restore orreplaceregardless ofcondition)“Hidden Failure”Determine whethera functional failurehas alreadyoccurredSufficient TimebetweenDetecting aProblem andActual FailureProbability ofFailureIncreases withTime(Wear out)No MeasurableCharacteristicFailure of off-line or“hidden” TimeDirectedFailure FindingServicing &LubricationService,Refurbish, orRenewOil, grease orotherwiselubricatePeriodic OEMAction RequiredMaintainLubricationAll tasks are Scheduled on a time or situational basisN7
RCM For CBMABS CM/PMprogram relieson CBMcomplianceN7
Simple WearoutProbabilityof FailurePfWearoutZoneAgeN7
Complex Systems - Random FailureCharacteristicsProbabilityof FailurePfComplexSystemsAgeN7
Age-Reliability StudiesAge-RelatedPfUAL1968Broberg1973MSDP omEvidence of WearoutNo Evidence of WearoutN7
Age-Reliability StudiesAge-RelatedPfUAL1968Broberg1973MSDP omEvidence of WearoutNo Evidence of WearoutN7
Different Ages at FailureFunctionalFailureRfARfBResistanceto Failure( Rf ) σΒσΑStress(σ)PFAge (operating time, cycles, calendar time)Source: Reliability-Centered Maintenance, Nowlan and HeapN7
Different Ages at FailureFunctionalFailureRfARfBResistanceto Failure( Rf ) σΒσΑPStress(σ)PFFAge (operating time, cycles, calendar time)Source: Reliability-Centered Maintenance, Nowlan and HeapN7
Different Ages at FailureFunctionalFailureRfARfBResistanceto Failure( Rf ) σΒσΑPStress(σ)PFFAge (operating time, cycles, calendar time)Source: Reliability-Centered Maintenance, Nowlan and HeapN7
Different Ages at FailureFunctionalFailureRfARfBResistanceto Failure( Rf ) σΒσΑPStress(σ)PFFAge (operating time, cycles, calendar time)Source: Reliability-Centered Maintenance, Nowlan and HeapN7
Different Ages at FailureInspection Interval ½ (F- P) or ½FunctionalFailureRfARfBResistanceto Failure( Rf ) σΒσΑPStress(σ)PFFAge (operating time, cycles, calendar time)Source: Reliability-Centered Maintenance, Nowlan and HeapN7
RiskProbability x Severity5Likelihood5 certain4 high3 moderate2 low1 unlikelyPf (Likelihood)4Consequence5 dire4 severe3 moderate2 low1 minor32112345Sf (Consequence)N7
RiskProbability x Severity5light bulbLikelihood5 certain4 high3 moderate2 low1 unlikelyPf (Likelihood)4(Fix when failed)Consequence5 dire4 severe3 moderate2 low1 minor32112345Sf (Consequence)N7
RiskProbability x Severity5criticalregulatorlight bulbLikelihood5 certain4 high3 moderate2 low1 unlikelyPf (Likelihood)4(Fix when failed)Consequence5 dire4 severe3 moderate2 low1 minor32112345Sf (Consequence)N7
RiskProbability x Severity5criticalregulatorlight bulbLikelihood5 certain4 high3 moderate2 low1 unlikelyPf (Likelihood)43(Fix when failed)Consequence5 dire4 severe3 moderate2 low1 minorredundantregulators2112345Sf (Consequence)N7
RiskProbability x Severity5criticalregulatorlight bulbLikelihood5 certain4 high3 moderate2 low1 unlikelyPf (Likelihood)4(Fix when 5 dire4 severe3 moderate2 low1 minor112345Sf (Consequence)N7
RiskProbability x Severity5criticalregulatorlight bulbLikelihood5 certain4 high3 moderate2 low1 unlikelyPf (Likelihood)4(Fix when failed)transformer3redundantregulators(Fix when failedto conditiondirected)2Consequence5 dire4 severe3 moderate2 low1 minor112345Sf (Consequence)N7
RiskProbability x Severity5criticalregulatorlight bulbLikelihood5 certain4 high3 moderate2 low1 unlikelyPf (Likelihood)4(Fix when failed)oil filter replacement10,000 mi3transformerredundantregulators(Fix when failedto conditiondirected)2Consequence5 dire4 severe3 moderate2 low1 minor112345Sf (Consequence)N7
RiskProbability x Severity5criticalregulatorlight bulbLikelihood5 certain4 high3 moderate2 low1 unlikelyPf (Likelihood)4(Fix when failed)oil filter replacement10,000 mi3transformer(Time directedmaintenance)redundantregulators(Fix when failedto conditiondirected)7,500 mi2Consequence5 dire4 severe3 moderate2 low1 minor112345Sf (Consequence)N7
RiskProbability x Severity5criticalregulatorlight bulbLikelihood5 certain4 high3 moderate2 low1 unlikelyPf (Likelihood)4(Fix when failed)oil filter replacement10,000 mi3transformer(Time directedmaintenance)redundantregulators(Fix when failedto conditiondirected)7,500 mi2Consequence5 dire4 severe3 moderate2 low1 minor3,000 mi112345Sf (Consequence)N7
Backfit RCM TriFoldN7
RCM Principle Application: 1st FilterEach PM Task is designed to prevent ormitigate a failure mode that will result in afunctional failure of the equipment orsystemN7
1st Filter: Age Degradation If Delete TaskN7
1st Filter: Age Degradation If “yes”, Determine/Classify Task Type CD: Condition Directed TD: Time Directed FF: Failure Finding S: Servicing L: Lubrication then go to next filter: ApplicabilityN7
1st Filter: Age Degradation then go to next filter: ApplicabilityN7
nd2Filter: ApplicabilityTo answer this question, only apply theRules for Applicability associated with theTask Type identified in Step 3N7
nd2Filter: ApplicabilityThe task only has to satisfy the questionsassociated with its corresponding task type.N7
nd2Filter: Applicability Does the Task Restore or MaintainInherent Reliability? If “No”, then Review ImprovementOptions: Can the task be modified to form anApplicable Task? If “Yes”, either Change Task Type Change scope/requirements Change periodicity If “No”, Delete the taskN7
nd2Filter: Applicability Does the Task Restore or Maintain InherentReliability? If “Yes”, then Identify one or more functional failureconsequences the task intended to prevent or mitigateN7
3rd Filter: EffectivenessN7
3rd Filter: Effectiveness In other words: Is the Task Worth Doing? Safety and/or Regulatory Does the Task Reduce the Probabilityof failure to an acceptable level(The probability of failure is never zero.) Operational performance (Mission) Does this task reduce the risk (Probability XConsequences) of impacting the mission toan acceptable level All other failuresPM Is the Cost of PM Less than the Cost of RepairPlus the Cost of Lost CapabilityN7
3rd Filter: Effectiveness If the task DOES NOT satisfy its associated area,then Review Improvement Options Can the task be improved to form an EffectiveTask? If not, delete the task.If the task DOES satisfy its associated area, thenconsider whether it can be improved, documentany changes, and schedule the TaskN7
3rd Filter: Effectiveness Whether or not a Task satisfies theRules for Effectiveness, the Taskshould be reviewed as to how itcould be improved to form anEffective Task, or a More EffectiveTask by: Extending its Periodicity Changing the Scope orRequirements Combining with related tasksN7
Backfit RCM ExampleExample No.1 Maintenance Task – Inspect& Check Injection PumpsN7
Backfit RCM ExampleN7
1st Filter: Age Degradation Task: M-Code 0498, Inspect & CheckInjector Pumps 12000 hrs Functional Failure: Injector PumpDelivery Erratic Failure Mode: Loose Pump Bolts Does Failure mode Occur in Service?:No, Failure is highly unlikely to occur inservice life. Action: Delete TaskN7
Backfit RCM ExampleExample No.2 Maintenance Task –Inspect Cylinder HeadsN7
1st Filter: Age DegradationN7
1st Filter: Age Degradation Task: M-Code 0536, InspectCylinder Heads 6000 hrs Functional Failure: Inadequatecylinder compression. Roughrunning Failure Mode: Cylinder HeadCracks/Valve Assembly Wear Does Failure mode Occur inService?: Yes Action: Identify Task Type andDetermine if the Task is ApplicableN7
2nd Filter: ApplicabilityTask: M-Code 0536, Inspect CylinderHeads 6000 hrs Task Type – Condition Directed Task Does the Task Satisfy Applicability Rules?:No, scale deposit is not quantified orassociated with cracked heads or wornvalve assemblies Action: Change to TD Task - Add detailedprocedure to recondition cylinder headsat 12000 hrs, then Identify FunctionalFailure Consequences and determine ifthe Task is Effective N7
Redesigned TaskN7
3rd Filter: Effectiveness Safety and/or Regulatory - No Operational Performance (Mission) –Yes, loss an engine due to a crackedhead would affect mission readiness All other failures - Cost of PM versus the cost of repair andlost capability refurbishing a head ischeaper than a day off-hire Action – None; further improvementsunknownN7
Backfit RCM ExampleExample No.3 Maintenance Task – CheckRocker Arm IndependentLube CircuitN7
Backfit RCM ExampleN7
1st Filter: Age Degradation Task: M-Code 0508, Inspect &Check Rocker Arm LO Circuit At1500 hours Functional Failure: Lube oilpump not providing adequatepressure. Failure Mode: Worn pumpinternals, from debris in LO. Does Failure mode Occur inService?: Yes Action: Identify task type andcontinue to the ApplicabilityFilter.N7
2nd Filter: Applicability Task: M-Code 0508, Inspect & CheckRocker Arm LO Circuit At 1500 hours Task Type – Condition/Time DirectedTask Does the Task Satisfy Applicability Rules?:No: Wear is caused by debris in the LubeOil, so checking Lube Oil pressure onlyidentifies a failure rather than prevent ormitigate it Action: Change to a CD task – Lube OilSampling, identify functional failureconsequences, and continue to theEffectiveness Filter.N7
3rd Filter: Effectiveness Safety and/or Regulatory - No Operational Performance(Mission) - No All other failures - Yes Cost of PM determined to beless than the cost of repair andlost capability. Action – NoneN7
We do maintenance because: We believe hardware reliability degradeswith age Does the failure mode occur? There is something we can do to restoreor maintain the original reliability Does theTask restore/maintain the InherentReliability? It pays for itself Is the Task Worth Doing(Risk/Reward)?N7
Document Failures in SAMM Define the problem What indicated the need for repair? What were the operating conditions at the time? Did the failure have an immediate impact on thefunction of the system? Define the Repair What was replaced? Are there visual indicator of what may have causedthem to fail? Take and upload pictures in SAMM What is the suspected cause of failure? What is thesupporting evidence? Did the repair eliminate the symptoms? What was done to validate the repair? Lessons Learned Provide any recommendations to avoid future failuresN7
SAMM AUDIT Simplified Maintenance EffectivenessReview Data Analysis: Repair data applied against equipmentover Five Years PM Conformance is compared toEquipment Repair History (AgeDegradation) Periodicity Changes Requires Chief Engineers concurrenceN7
SAMM AUDITTypical Data Analysis ResultsN7
SAMM AUDITExample: Recommended ChangesN7
Paradigm Shift“Prove to me thatfailure won’t occurif you change this.”“Prove to me thatfailure will occur if Ichange this.”Limits ofApplicable andEffectiveMaintenanceN7
Reliability . Centered Maintenance . Goal being Reliability. N7. As important as maintenance is to reliability, there are other factors that also play a role, however today well will focus on\ഠ