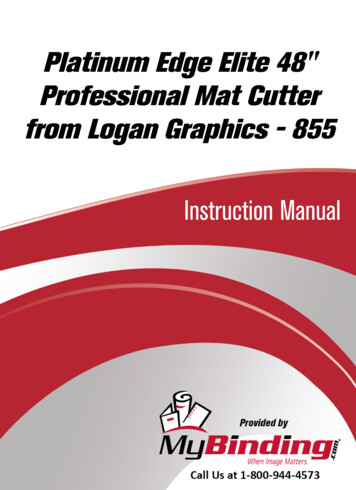
Transcription
Platinum Edge Elite 48"Professional Mat Cutterfrom Logan Graphics - 855Instruction Manual
PROFESSIONAL SERIESMODEL 850, 855, 860MAT CUTTERINSTRUCTION AND OPERATION MANUAL Professional mat cutting system with aluminumbaseboard, magnetic production stop, 32 in(81 cm) removable squaring arm, plus dualstraight and bevel cutting headsFor best results use onlyauthentic Logan blade #267CAUTION!!MAT CUTTING BLADES ARE SHARPMat border calculatorMobile appPurchase DateID Number (on bottom of board)Date (on bottom of board)Logan Graphic Products, Inc.1100 Brown StreetWauconda, IL 60084 USAPhone 847-526-5515 Fax 847-526-5155cs@logangraphic.com LoganGraphic.comL3097N3 6-12
INTRODUCTIONThe Logan Platinum Edge Mat Cutter (Model 850, 855 & 860) is designed specifically with the framer in mind. All the materials are heavy-duty to withstand the rigors of professional mat cutting and to provide the accuracy framers demand.Features include super-smooth cutting head glides, 4- and 8-ply cutting capability, quick-change magnetic blade cartridges,micro-adjustable moving magnetic stop, 32” (81cm) removable scaled squaring arm, and heavy-duty all-metal constructionwith aluminum base. Use Logan Replacement Blade Model 267.We are confident that the quality, accuracy and dependability of the Platinum Edge will be everything you expect in a professional mat cutter.This instructional manual is written to acquaint you thoroughly with this product. Referred to at the outset, it will answer manyquestions that may arise during use. You will find that the time taken will be well worth it and you will be cutting top qualitymats in no time.ta b le o f contentsOut Of Box Set Up.1Changing/Installing Mat Cutter Blades.2Cutting A Beveled Mat.3Line to Line Method.3Production Stops Method.4Platinum Edge Precision Mat Cutter Diagram.6Sizing The Mat Board.7Cutting V-Grooves.8Making Adjustments.8Re-squaring the Squaring Arm.8Cutting Head.9Bevel Blade Tip Adjustment Screw.10Production Stop Micro-Adjustments.10Mat Guide.10Re-Parallel the Mat Guide.10Troubleshooting.11More Great Logan Products.12Warranty. 13Logan Graphic Products, Inc. 1100 Brown Street, Wauconda, IL 60084 USA Phone (847) 526-5515 Fax (847) 526-5155 www.logangraphic.com
Out Of Box Set UpAbove: Additional parts includedin this package: Four Allenwrenchs, sizes 1/8”, 5/32”,5/64” & 1/16”, Handle Bar LiftKnob and screw, two replacementblade packs (5 ct. each)Figure 1The Platinum Edge Mat Cutter has been aligned and calibrated at our facility before shipping. With a fewsimple steps, you will be able to set up your mat cutter and begin production immediately.Remove the Platinum Edge Mat Cutter from the box and unwrap the pieces carefully. Your PlatinumEdge should be set up on a flat, stable work table, aligned so that you can easily access the handle barlift and cutting head (Figure 2.1). Follow the assembly guide (Figure 2.2).ASSEMBLY INSTRUCTIONS(See page 6 for parts identification)1. Insert Right Side Squaring Arm into Squaring ArmMount2. Hook the Squaring Arm Strut onto the StrutBracket3. Attach the Handle Bar Lift Knobusing the enclosed screw and5/32” Allan wrench2Figure 2.113Figure 2.2 Assembly GuideIMPORTANT: Do not oil or lubricate the cutting head or guide rail.1Logan Graphic Products, Inc. 1100 Brown Street, Wauconda, IL 60084 USA Phone (847) 526-5515 Fax (847) 526-5155 www.logangraphic.com
Changing andInstalling MatCutter Bladesbevel blade holding knobFigure 33/4”A note about Mat Cutter Blades: They are sharp. Super sharp. Imagine a sharpthing and then multiply it by a power of three. That sharp. So, be careful.SingleBevelBevel Cut BladeMagazinescribelineblade depthadjustment screwThe Platinum Edge Mat Cutter uses Logan Blade Model 267, which is a 0.012” thick double bevel blade.However, any blade that is 3/4” in height may be used, as long as the blade depth and productionstops are adjusted accordingly for accurate results (See “Making Adjustments” starting on Page 16).Whether you use single bevel blades or double bevel blades is really up to you, but either version can bepurchased from an authorized art materials dealer.DoubleBevelsharpedgeStraight CutBlade MagazineFigure 4Always use a sharp blade when cutting mats. Signs your blade may be too dull include ragged cuts or atendency for the blade to tear the mat rather than slice it. When a blade becomes dull you will need toremove it and either exchange it for a new one or, in the case of double bevel blades, reverse the bladeto use the as-yet-unused side. To remove a blade magazine from the blade carrier, first loosen the bevelblade holding knob located beneath the front handle of the blade carrier (Figure 3).Take hold of the black adjustment screw at the rear of the magazine and pull the magazine out. If themagazine does not come out smoothly, loosen the thumb screw a bit more.Setting the Bevel Blade DepthNOTE: It is important to distinguish thedifference between the Bevel Cut andStraight Cut blade magazines. Identifythe scribe line on the Bevel Cut BladeMagazine. This inserts on the left side(bevel side) of the cutting head.Place a fresh blade on the magazine with the sharp edge down – the magnet will hold it in place (Figure4). Insert the magazine into the blade holder slot until the rear of the magazine is flush with the rear ofthe blade holder, then tighten the blade holding knob securely. You will be able to feel where the bladeholding knob falls into the divot machined into the blade magazine (Figure 5).Blade depth adjustments are made by loosening the blade holding knob slightly and turning the bladedepth adjustment screw in or out. Each blade should be set so it only just cuts through the matbeing cut and slightly scores the slipsheet.TIP The bevel cut blade magazine features a scribe line (Figure 4) as a suggested place to align the rearof the blade. This line was factory tested with a commonly available 4-ply mat board. Your matboardthickness may vary, in which case the blade will require adjustment as described above.Inserting the Bevel BladeHolding MagazineInserting the StraightBlade Holding MagazineCAUTION!!MAT CUTTING BLADES ARE SHARPbevel bladeholding knob2Figure 5Logan Graphic Products, Inc. 1100 Brown Street, Wauconda, IL 60084 USA Phone (847) 526-5515 Fax (847) 526-5155 www.logangraphic.com
Cutting a Beveled MatLine to Line Methodslip sheetmatFigure 6Bevel cutting is done from the back side of the mat with the colored side down. Always use a slip sheetof scrap mat board beneath the mat you intend to cut in order to provide a crisp edge (Figure 6).A slip sheet usually measures about 6 inches wide and is at least a few inches longer than the mat youintend to cut. The bevel blade should extend far enough so that it slices through the mat you are cuttingand then just score into the slip sheet.TIPAfter you have cut a few mats, you may wish to move the slip sheet or flip it so that the blade doesnot follow the same slip sheet furrows. Having fresh mat board beneath the surface you intend to cuthelps to provide a crisply cut edge. Line to Line MethodStep 1Set the mat guide only at desired border size like 2” for this example (Figure 7).Step 2Insert a mat board blank, color side down, on top of a slip sheet. Using a pencil, mark lines along theleft side of the cutting bar from end to end of the mat board blank and repeat for all four sides.Figure 7 TIPA suggestion to learn where to start and stop with your blade:Mark out four even size borders on a mat blank. Then set your production stops (see page 7) to cutthat same size even border. Cut the mat using the production stops. While cutting, watch and takemental note of where the blade enters and exits the mat in relation to the pencil lines while using theproduction stops. Seeing where the blade starts and stops using the production stops will teach youwhere to manually duplicate these entry and exit points when cutting line to line.Step 4Repeat this process for the next side, and stop to inspect the corner. If the corner is hung up and the window isnot dropping out, OR if there is significant overcut in the corners, then adjust where you start and stop.Blade inserts 3/16”above pencil lineFigure 8Step 3Slide the cutting head to the top line and position it so the entry point of the blade tip is roughly 3/16” above thepencil line (Figure 8). Rotate the blade holder to insert the blade, and pull back to cut while applying steady, evenpressure, stopping when the tip of the blade passes the bottom pencil line by roughly 3/16”.TIPThe mat cutting technique described above (without production stops or stop/start indicators) is usedby professional framers. Although it takes some practice to perfect, the tips provided here combinedwith patience and persistance will help you quickly master the technique. continued on page 43Logan Graphic Products, Inc. 1100 Brown Street, Wauconda, IL 60084 USA Phone (847) 526-5515 Fax (847) 526-5155 www.logangraphic.com
Cutting a Beveled MatLine to Line Method(continued)1. While rotating the blade into the mat, hold the cutting head still to prevent it from creepingforward upon insertion, which can cause an overcut.TIP2. Maintain constant downward pressure on the bevel blade holder throughout the cut to ensure theblades passes through the mat board. 3. Pushing down on the long handle bar during cutting is unnecessary and not recommended.4. Cutting 8-ply or Double Thick Mat Board - After increasing the blade depth, use a pieceof test 8 ply mat board to mark out and line to line cut one corner that can be inspected. Do notuse the production stops for this test cut. Cut from line to line, starting and stopping the bladeapproximately 3/8” past the marked lines. Inspect the slip sheet to see you are just barely scoringinto the surface. Inspect the corner on the test mat to check for overcuts.5. Cleaning debris from under the cutting bar - Occasionally some debris may collect under thecutting bar, which could cause cutting inconsistencies. To remove the debris, use a clean cloth, softbrush or compressed air. Do not use cleaning fluids that may leave a film on the mat cutter. Thisfilm may damage the matboard.Cutting aBeveled MatProduction StopsMethodUsing the ruler guides on the left side squaring arm (Figure 9), cutting head (Figure 10), and clamprail (Figure 11), set the desired border width for your finished mat. The example shown is for cutting amat with a 2” border.Standing at the end of the mat cutter, use the handle bar lift to raise the guide rail above the surfaceof the base (Figure 12).2”Figure 92”2”4Figure 10Figure 11Logan Graphic Products, Inc. 1100 Brown Street, Wauconda, IL 60084 USA Phone (847) 526-5515 Fax (847) 526-5155 www.logangraphic.com
Cutting a Beveled MatProduction Stops Method(continued)Figure 12Mat GuideSquaringArmSlide the mat and slip sheet beneath the guide rail and align the lower corner of the mat you intend to cutat the junction of the squaring arm and mat guide. It is important to make sure the mat you are about tocut sits squarely against the squaring arm and the mat guide. Lower the lifter bar mechanism to secure themat in place for cutting (Figure 13).Slide the cutting head up the guide rail until the magnetic moveable stop catches the cutting head. Theblack foot of the stop should be in an elevated position to avoid catching on the slip sheet.Slide the cutting head down the guide rail until the black foot of the automatic stop has gone past theupper edge of the slip sheet and then drop it down into position. When the foot catches the edge of themat you are about to cut, rotate the cutting head down into the mat, starting your cut (Figure 14).Figure 13SquaringArmfootslip sheetPull the cutting head towards you, and the magnetic moveable stop will automatically release. Continuethe cut with a steady pull until the cutting head makes contact with the lower stop. Rotate the blade outof the mat. Raise the handle bar using the handle bar life (Figure 12) to release the mat, turn the mat90 degrees, align the corner of the mat back into the corner of the mat stop and mat guide and repeatthe cutting process.mat1. While rotating the blade in, hold the cutting head still to prevent it from creeping forward uponinsertion which can cause an overcut.2. Maintain constant forward pressure on the bevel blade holder throughout the cut to ensure theblades passes through the mat board.Figure 14TIP 3. Pushing down on the long handle bar during cutting is unnecessary and not recommended, as itmay cause hooks and curves in the mat opening.5Logan Graphic Products, Inc. 1100 Brown Street, Wauconda, IL 60084 USA Phone (847) 526-5515 Fax (847) 526-5155 www.logangraphic.com
Platinum Edge Precision Mat CutterDiagram1412Left Side:Bevel Cutting13191111517161810Right Side:Straight Cutting22202219374681 Left Side Squaring Arm2 Mat Guide3 Handle Bar4 Base5 Cutting Bar6 Support Arm7 Hinge8 Cutting Bar Bracket59 Magnetic Moveable Stop10 Cutting Head11 Squaring Arm Mount12 Right Side Squaring Arm13 Squaring Arm Stop14 Bottom Stop15 Handle Bar Lift16 Squaring Arm Strut17 Strut Bracket18 Bevel Blade Holding Knob19 Bevel Blade Holding Magazine20 Straight Blade HoldingMagazine21 Straight Blade Holding Knob22 Lockdown Pin6Logan Graphic Products, Inc. 1100 Brown Street, Wauconda, IL 60084 USA Phone (847) 526-5515 Fax (847) 526-5155 www.logangraphic.com
Sizing Mat BoardSquaring Arm StopFigure 15Full size mat boards can be cut down to a desired size using the straight blade side on the cutting head.The removable squaring arm is helpful for squaring and sizing the mat (Figure 15).Step 1Set the squaring arm stop for the measurement you want and tighten the knob (Figure 15).Lockdown PinFigure 16Figure 17Step 2TIPFull sheet mat board is most oftennot square when purchased new.Leaving any factory corners canproduce unsquare mats. If youneed to square the board, trim asmall amount off all four sides ofthe mat board using the straightcut side. When trimming, cutopposite sides first and then theremaining opposite sides. (trimeach long side first then trim theshort sides) Remove the mat guide and the slip sheet. Place the mat board under the cutting bar and against thesquaring arm and squaring arm stop (Figure 16). The lower stop should be moved all the way to thebottom of the guide rail bar – it does not need to be tightened.Step 3Adjust the straight cutting head blade so it will cut about 1/32nd of an inch deeper than the mat boardyou are cutting. To cut, position the cutting head above the top edge of the mat board and rotate thestraight cutting head down as far as it will go. Lock it in position with the lockdown pin for the cuttingprocess (Figure 17).7Logan Graphic Products, Inc. 1100 Brown Street, Wauconda, IL 60084 USA Phone (847) 526-5515 Fax (847) 526-5155 www.logangraphic.com
Cutting V-GroovesFor professional quality V-Grooves, the Logan Model 706 Universal V-Groover is compatible withModel 850. It is available from picture frame suppliers and art supply dealers. See Page 21 for moreinformation.Above are twoexamples of artworkthat are enhancedwith V-Groove matsMaking AdjustmentsFigure 18From time to time, you may need to make adjustments to your Platinum Edge Mat Cutter. The followingcategories will guide you through the process of adjusting your mat cutter if some fine tuning is needed.Re-squaring the Squaring ArmIt is possible over time for the squaring arm to come slightly out of square to the cutting bar. In thissituation, you will need to re-square the squaring arm.Before making any adjustments, check the squareness of the machine with this test. You will need an Lshaped carpenter’s square found in any hardware store.Step 1Insure that you have the long 32” squaring arm tightly attached to the squaring arm mount.Step 2Remove any mat board or slip sheet material from the machine.Figure 19Step 3Slide the cutting head to the far end of the cutting bar out of the way.Step 4Place the L shaped carpenter’s square into the machine into the 90 degree corner formed by the cuttingbar and the squaring arm. (Fig 19 & 20)Step 5Figure 20Check the relationship of the L shaped carpenter’s square to the cutting bar and squaring arm. It shouldfit tightly with no movement. If there is movement, determine which direction the squaring arm needsto move to be square again and allow the L shaped carpenter’s square to snugly fit into the machinewith no movement.continued on page 98Logan Graphic Products, Inc. 1100 Brown Street, Wauconda, IL 60084 USA Phone (847) 526-5515 Fax (847) 526-5155 www.logangraphic.com
Making AdjustmentsStep 6ScrewsFigure 21 - Strut Bracket(continued)Loosen the squaring arm strut bracket screws (Figure 21) and gently tap the bracket forward or backwardto pull or push the squaring arm the direction it needs to go to be square again. Moving the strut bracketup or down slightly will push or pull the angle of the squaring arm back into square. (Fig 22).Step 7Once the squaring arm is square to the L shaped carpenter’s square, re-tighten the squaring arm bracketin place. The machine is now re-squared.Cutting HeadIf the cutting head begins to wobble side-to-side, there are three setscrews to tighten.Caution: do not over-tighten these screws.On the right side of the cutting head there are two recessed holes. One is to the left of the 90 degreeblade carrier behind the knurled screw and one is to the right of the blade carrier behind the extendedblade (remove blade before adjusting) (Figure 23).Figure 22Figure 23With the Allen wrench provided, slightly tighten the front bushing screw. After each adjustment, slide thecutter back and forth until some resistance is felt. If there is too much resistance, loosen the screw veryslightly so the cutting head slides easily. Repeat this process on the rear bushing. The third adjustmentscrew for the cutting head is in a recessed hole on the top of the head (Figure 24).This tightens the roller bearing. Again, slightly tighten the bearing screw and check for resistance bysliding the cutting head. As soon as resistance is felt, loosen the setscrew slightly.Caution: do not over-tighten these screws or damage to the bearing or bushings rmay result.Figure 249Logan Graphic Products, Inc. 1100 Brown Street, Wauconda, IL 60084 USA Phone (847) 526-5515 Fax (847) 526-5155 www.logangraphic.com
Making Adjustments(continued)Blade Tip AdjustmentScrewBevel Blade Tip Adjustment ScrewFigure 25If you are experienceing hooks or curves in your cuts even though the blade depth is set properly so it only scores into the backing sheet, anadjustment to the blade tip adjustment screw may be needed (Figure 25). Remove the bevel blade magazine and the blade and locate the smallscrew on the magazine located near where the tip of the blade rests. Using the Allen wrench provided, turn the screw in slightly to put morepressure on the blade tip while cutting. DO NOT OVERTIGHTEN. Too much pressure from this screw can drive the blade into the cutting bar. Toolittle pressure from this screw can create “slack” in the blade which can allow it to flex while cutting which can produce hooks or curves.Production Stop Micro AdjustmentsIf you are experiencing over cuts or under cuts using productin stops even though the blade depth is set properly so it only scores into the backingsheet, adjustments to the production stops may be needed. On the mat guide, bottom stop and magnetic movable stop, you will find a small knobthat moves the indicator plate over the scale. This indicator plate can be moved slightly to correct an over cut or under cut. For example, if you areexperiencing an over cut at the start of a 2” border cut using themagnetic movable stop, turn the micro adjustment on the magneticmovable stop to slightly less than 2” and then loosen and adjustMat GuideMat Guide Microthe entire magnetic movable stop back to the 2” mark. This willLock KnobAdjustment Knobremove some or all of the over cut allowing you to still set the stopIndicatorproperly at the 2” mark each time. For under cuts, turn the microadjustment on the magnetic movable stop to slightly more than2” and then loosen and adjust the entire magnetic movable stopback to the 2” mark. This will remove some or all of the under cutallowing you to still set the stop properly at the 2” mark each time.Figure 26Mat GuideFine tuning the width of the border is done on the mat guide. If you need to make the border width abit narrower, turn the mat guide micro adjustment knob counter-clockwise. Conversely, turning the knobclockwise will widen the border width slightly (Figure 26).Re-Parallel the Mat GuideIf the Mat Guide is not parallel to the cutting bar,it can be adjusted to re-parallel.1. Move top stop to end of machine (Figure 27).Figure 27MOVETOP STOPMOVETOP STOP2. Loosen mat guide knob.3. Slide mat guide against cutting bar and tighten.4. Look for gaps.5. To eliminate gap, loosen mat guide knob and turn screwusing allen wrench provided. Use Screw A if gap is near theend of the machine (Figure 27). Use Screw B if gap is nearthe mat guide knob (Figure 28).Figure 286. Retighten mat guide knob and check for gaps.10CAUTION!!MAT CUTTING BLADES ARE SHARPLogan Graphic Products, Inc. 1100 Brown Street, Wauconda, IL 60084 USA Phone (847) 526-5515 Fax (847) 526-5155 www.logangraphic.com
TroubleshootingProblemPossible ReasonsRagged cutsCutting without a slip sheet (Page 3)Slip sheet is worn out (Page 3)Dull or chipped blade (Page 2)Inconsistent pressure being applied on the cutting head while cutting (Page 4)Putting unneeded pressure down onto the handle bar (Page 4)Overcut at the start of the cutAllowing the cutting head to “creep” forward upon blade insertion (Page 4)Starting the cut too far past the pencil line (Page 3)Too much blade depth (Page 2)Production stop not set properly or needs micro adjustment (Page 10)Overcut at the end of the cutCutting too far past the bottom pencil line (Page 3)Too much blade depth (Page 2)Production stop not set properly or needs micro adjustment (Page 10)Blade not cutting through materialPushing down on the handle bar while cutting (Page 4)Inconsistent pressure being applied on the cutting head while cutting (Page 4)Debris caught under the cutting bar (Page 4)Blade depth set too shallow (Page 2)Cutting through the mat in some areas but not in othersPushing down on the handle bar while cutting (Page 4)Slip sheet not the full length of the mat being cut (Page 3)Inconsistent pressure being applied on the cutting head while cutting (Page 4)Debris caught under the cutting bar (Page 4)Hook in corner or long curve in the cutToo much blade depth allowing the blade tip to flex (Page 2)Dull blade (Page 2)Pushing down on the handle bar while cutting (Page 4)Slip sheet not the full length of the mat being cut (Page 3)Inconsistent pressure being applied on the cutting head while cutting (Page 4)Possible adjustment needed to the blade tip adjustment screw (Page 10)Cutting heads hard to pull when cuttingDull blade (Page 2)For bevel cutting, too much blade depth (Page 2)For straight cutting, did not remove slip sheet before cutting (Page 7)Possible adjustment needed on cutting head tension screws (Page 9)Borders of mats inconsistent size from one end to the otherNot placing the mat and slip sheet tightly against the parallel mat guide (Page 5)Mat guide not parallel and needs adjustment (Pages 8-9)Mat board not squared properly before cutting (Page 7)Machine not producing square cuts when downsizing mat boardNot placing the mat squarely against the squaring bar while cutting (Page 5)Squaring arm no longer square and needs adjustment (Pages 8-9)Trim all four sides of an unsquare mat board before using (Page 7)Cutting head loose on the railPossible adjustment needed on cutting head tension screws (Page 9)Production stops producing over or under cutsBlade depth set too deep or too shallow (Page 2)Possible micro adjustment needed on the production stops (Page 10)11Logan Graphic Products, Inc. 1100 Brown Street, Wauconda, IL 60084 USA Phone (847) 526-5515 Fax (847) 526-5155 www.logangraphic.com
W a r r ant yLogan Graphic Products, Inc. (“Logan”) warrants the Platinum Edge (Models 850, 855 & 860) to be free fromdefects in parts and workmanship for a period of two years from the date of original purchase. Logan warrants thatit will either repair or replace, at its sole discretion, any necessary replacement parts found to be defective. Shouldthe product need to be returned to Logan for repair or replacement parts, authorization for any return must comefrom Logan in writing. Costs of returning the product to Logan, including insurances, shall be borne by the purchaser.Logan shall not be liable for any damages or losses, incidental or consequential, direct or indirect, arising from theuse of this product. This warranty extends only to the original purchaser and is not assignable or transferable. Thiswarranty is in lieu of all other warranties, expressed or implied. Be advised that any Logan products purchased as“new” from an unauthorized dealer, such as an online auction site or similar, may be void of their warranty.12Logan Graphic Products, Inc. 1100 Brown Street, Wauconda, IL 60084 USA Phone (847) 526-5515 Fax (847) 526-5155 www.logangraphic.com
Logan QualityCommitmentLogan Graphic Products, Inc. is committed to delivering products that work and exceed our customers’expectations. If you are dissatisfied with your tool’s performance, do not understand the directions, orfeel that you are not getting the results you expected, DON’T GIVE UP! Contact us by emailor phone, and let us help solve your problem. We are here for you, and want you to be thrilled with yourLogan purchase.email: cs@logangraphic.comphone: 800 331 6232 847 526 551513Logan Graphic Products, Inc. 1100 Brown Street, Wauconda, IL 60084 USA Phone (847) 526-5515 Fax (847) 526-5155 www.logangraphic.com
14Logan Graphic Products, Inc. 1100 Brown Street, Wauconda, IL 60084 USA Phone (847) 526-5515 Fax (847) 526-5155 www.logangraphic.com
To remove a blade magazine from the blade carrier, first loosen the bevel blade holding knob located beneath the front handle of the blade carrier (Figure 3). Take hold of the black adjustment screw at the rear of the magazine and pull the magazine out. If the magazine does