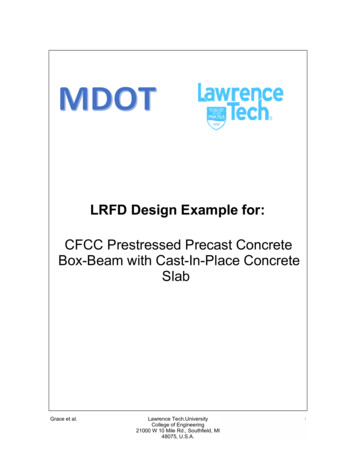
Transcription
LRFD Design Example for:CFCC Prestressed Precast ConcreteBox-Beam with Cast-In-Place ConcreteSlabGrace et al.Lawrence Tech.UniversityCollege of Engineering21000 W 10 Mile Rd., Southfield, MI48075, U.S.A.7/1/20197/1/2019
Disclaimer"This publication is disseminated in the interest of information exchange. TheMichigan Department of Transportation (hereinafter referred to as MDOT) expresslydisclaims any liability, of any kind, or for any reason, that might otherwise arise out ofany use of this publication or the information or data provided in the publication.MDOT further disclaims any responsibility for typographical errors or accuracy of theinformation provided or contained within this information. MDOT makes nowarranties or representations whatsoever regarding the quality, content, completeness,suitability, adequacy, sequence, accuracy or timeliness of the information and dataprovided, or that the contents represent standards, specifications, or regulations.”“This material is based upon work supported by the Federal Highway Administrationunder SPR-1690. Any opinions, findings and conclusions or recommendationsexpressed in this publication are those of the author(s) and do not necessarily reflectthe views of the Federal Highway Administration.”Grace et al.Lawrence Tech.UniversityCollege of Engineering21000 W 10 Mile Rd., Southfield, MI48075, U.S.A.7/1/20197/1/2019
About this Design ExampleDescriptionThis document provides guidance for the design of CFCC prestressed precast concrete beamsaccording to AASHTO LRFD Bridge Design Specifications with the neccessary ammendmets whereapplicable, based on available literature and experimental data from tests conducted by Grace et. al atLawrence Technological University. The cross-section of the bridge is Type B as described byAASHTO Table 4.6.2.2.1-1.StandardsThe following design standards were utilized in this example: AASHTO LRFD Bridge Design Specification, 7th Edition, 2014 Michigan Department of Transportation Bridge Design Manual, Volume 5 Michigan Department of Transportation Bridge Design Guide ACI 440.4R-04, Prestressing Concrete Structures with FRP TendonsCode & AASHTO LRFD UPDATESThis Mathcad sheet is developed based on available design guidelines and availableAASHTO LRFD edition at the time of writing the sheet. Designer shall check and updatedesign equations according to the latest edition of AASHTO LRFDGeneral notesThe following notes were considered in this design example:1- Guarnateed strength of CFRP is reduced to account for environmental effect. The design guarnateedstrength is taken as 0.9 x guarnateed strength recommended by manufacturer2- Initial prestressing stress is limited to 65% of the design (reduced) guaranteed strength according tocurrent ACI 440.4R-04. This limit is subject to change. Check the latest recommendations forinitial/jacking stress in CFRP strands3- CFCC strength immediately following transfer is limited to 60% of the design (reduced) guaranteedstrength according ccording to current ACI 440.4R-04. This limit is subject to change. Check the latestrecommendations4- The depth of the haunch is ignored in calculating section properties or flexural capacity, while isincluded in calculating the dead loads5- In strength limit state flanged section design, the concrete strength of the beam portion participating ithe stress block was conservatively assumed equal to the concrete strength of the deck (AASHTO LRFC5.7.2.2)6- Barrier weight was taken as 475 lb/ft. While, weight of midspan diaphragm was 500 lb/beam7- In the Mathcad sheet, the option of debonding as well as top prestressing strands are offered asGrace et al.Lawrence Tech.UniversityCollege of Engineering21000 W 10 Mile Rd., Southfield, MI48075, U.S.A.7/1/20197/1/2019
pgmeans of reducing the end tensile stresses of the beamsppg8-The example provided herein is a box beam with varying web thickness from a maximum of 12 in. atthe beam ends to a minimum of 4.5 in. at midspan. This is the same cs that was used in theconstruction of M-102 bridge in Southfield, MI. Shear requirements necessitated the increase in theweb thickenss near the ends of the span9-The box beam in this example is also provided with end diaphragms, which affect the stresscalculations at beam ends at prestress release10- In strength limit state check, the design addresses six different failure modes as follows:Tension controlled rectangular section (depth of stress block is less than or equal the depth of thedeck slab and the reinforcement ratio is less than balanced reinforcement ratio, CFRP ruptures beforeconcrete crushing)Compression controlled rectangular section (depth of stress block is less than or equal the depthof the deck slab and the reinforcement ratio is larger than balanced reinforcement ratio, Concretecrushes before CFRP rupture)Tension controlled flanged section (depth of stress block is larger than the depth of the deck slabbut less than the combined depth of the deck slab and beam top flange. The reinforcement ratio is lessthan balanced reinforcement ratio, CFRP ruptures before concrete crushing)Compression controlled flanged section (depth of stress block is larger than the depth of the deckslab but less than the combined depth of the deck slab and beam top flange. The reinforcement ratio islarger than balanced reinforcement ratio, Concrete crushes before CFRP rupture)Tension controlled double flanged section (depth of stress block is larger than the combineddepth of the deck slab and beam top flange. The reinforcement ratio is less than balancedreinforcement ratio, CFRP ruptures before concrete crushing)Compression controlled double flanged section (depth of stress block is larger than the combineddepth of the deck slab and beam top flange. The reinforcement ratio is larger than balancedreinforcement ratio, Concrete crushes before CFRP rupture)Designer is advised to check the ductility of the beam and the deflection at failure in case ofdouble flanged section because in that case, the N.A. of the section lies within the web of thebeam and the ductility of the section may be compromised11- This design example is developed based on allowable jacking strength and stress immediatelyafter transfer according to the limits presented in the ACI 440.4R-04. The document can be updatedusing other prestress limits such as those presented in MDOT SPR-1690 research report and guideGrace et al.Lawrence Tech.UniversityCollege of Engineering21000 W 10 Mile Rd., Southfield, MI48075, U.S.A.7/1/20197/1/2019
LRefToRef 75ftDRefAtoBearing 50.5inDRefBtoBearing 50.5inL LRefToRef DRefAtoBearing DRefBtoBearing 66.583 ftbrgoff 8inCenter to center span LengthCenter of bearing offset to end of beam (same vaLue at both ends isassumed)Lbeam L 2 brgoff 67.917 ftTotaL length of beamlship 12 inDistance from support to the end of the beam after force transferand during shipping and handlingLship Lbeam lship 2 65.917 ft Distance between supports during handling and shippingdeckwidth 61ft 8.5inOut to out deck widthclearroadway 52ft 0inCLear roadway widthdeckthick 9inDeck slab thicknesstwear 0 inWearing surface is included in the structural deck thickness onlywhen designing the deck as per MDOT BDM 7.02.19.A.4. It is notused when designing the beam.tfws 2inFuture wearing surface is applied as dead laod to accuant foradditional deck thickness if a thicker rigid overlay is placed on deckwalkwidth 6ft 0insidewalk widthwalkthick 0insidewalk thickness (0" indicates no separate sidewalk pour)S 8ft 0inCenter to center beam spacingNObeams 8Total number of beamshaunch 0inAverage haunch thickness for section properties andstrength calculationshaunchd 2.0inAverage haunch thickness for Load calculationsGrace et al.Lawrence Tech.UniversityCollege of Engineering21000 W 10 Mile Rd., Southfield, MI48075, U.S.A.7/1/20197/1/2019
overhang 2ft 11.5inDeck overhang width (same vaLue on both overhangs isassumed)Barrier width; include offset from back of barrier to edge ofdeckHz distance between center of gravity of two exteriorgirdersbarrierwidth 1ft 2.5inSexterior 56ft 0in clearroadway 4.0012ft Lanes floor The number of design traffic Lanes can becaLcuLated as2051 anglecrossing 45 deg 45.35 deg60 3600 Angle measured from centerline of bridge to thereference lineθskew 90deg anglecrossing 44.65 degAngle measured from a line perpendicular tothe centerline of bridge to the reference lineConcrete Material Propertiesfc deck 5ksiDeck concrete compressive strengthfc beam 8ksiFinaL beam concrete compressive strengthfci beam 0.8fc beam 6.4 ksi Beam concrete compressive strength at reLeasekipωconc 0.1503ftUnit weight of reinforced concrete for load calculationsbarrierweight 0.475kipWeight per foot of barrier (aesthetic parapet tube, see MDOT BDG6.29.10)ftUnit weights of concrete used for modulus of eLasticity calculations, AASHTO Table 3.5.1-1 γc f'c 0.145kipft0.1403kipft3 γc.beam γc fc beam 148 pcfγci.beam γc fci beam 146.4 pcfif f'c 5ksiγc.deck γc fc deck 145 pcf f'c kip otherwise ksi ft3 0.001 Concrete Modulus of ElasticityElastic modulus for concrete is as specified by AASHTO A 5.4.2.4 with a correction factor of 1.0 γci.beam Ec.beam i 120000 kip ft3 Grace et al.2.0 fci beam ksi 0.33 ksi 4745.73 ksiLawrence Tech.UniversityCollege of Engineering21000 W 10 Mile Rd., Southfield, MI48075, U.S.A.Beam concrete at reLease7/1/20197/1/2019
γc.beam Ec.beam 120000 kip ft3 γc.deck Ec.deck 120000 kip ft3 2.02.0 fc beam ksi fc deck ksi 0.33 ksi 5220.65 ksiBeam concrete at 28 days0.33 ksi 4291.19 ksiDeck concrete at 28 daysCFCC Material Propertiesds 15.2mm 0.6 inPrestressing strand diameter2Astrand 0.179 inEffective cross sectionaL areaEp 21000ksiTensile elastic modulusTguts 60.70kipGuaranteed ultimate tensile capacityTgutsf'pu 339.11 ksiAstrandCalculated ultimate tensile stressCEse 0.9Environmental reduction factor for prestressed concreteexposed to weather for service limit state calculationsfpu.service CEse f'pu 305.2 ksiCEst 0.9Environmental reduction factor for prestressed concreteexposed to weather for strength limit state calculationsfpu CEst f'pu 305.2 ksiModular Ration Ec.beamnp Ec.deckEpEc.deck 1.217Modular ratio for beam 4.89Modular ratio for Prestressing CFCCBox-Beam Section Properties:bft 48inWidth of top flangedft 6inThickness of top flangebfb 48inWidth of bottom flangeGrace et al.Lawrence Tech.UniversityCollege of Engineering21000 W 10 Mile Rd., Southfield, MI48075, U.S.A.7/1/20197/1/2019
dfb 6inThickness of bottom flangebweb.min 4.5inMinimum web thicknessbweb.max 12inMaximum web thicknessLend 32 inLength of the solid end block at beam endLvar 176 inLength where web is tabered from maximumto minimum widthd 33inDepth of beambwebf ( x) ( 24 in) if 0 x Lendx Lend bweb.max bweb.max bweb.min if Lend x Lend LvarLvar bweb.min if x Lend LvarAbeamf ( x) 2bft d 0.5625 inif 0 x Lend2 b d d d d b 2 bftfbftwebf ( x) 17.4375 in if Lend x ft3Ibeamf ( x) bft d12if 0 x Lend3d dft dfb 4bft bft 2 bwebf ( x) 1485 in12123dif Lend xyt 16.5inDepth from centroid to top of beamyb 16.5inDepth from centroid to soffit of beamSTf ( x) SBf ( x) Ibeamf ( x)ytIbeamf ( x)ybSection modulus about top flangeSection modulus about bottom flangeProperties of the section at midspan (minimum concrete area)Grace et al.Lawrence Tech.UniversityCollege of Engineering21000 W 10 Mile Rd., Southfield, MI48075, U.S.A.7/1/20197/1/2019
Lbeam 2 782.437 in 2 Abeam Abeamf Lbeam 4.5 in 2 Minimum area of beam sectionbweb bwebf width of the web at midspan Lbeam bv 2 bwebf 9.00 in 2 combined web width at midspan(two webs per beam)ωbeam Abeam ( 150pcf ) 815.04 plfBeam weight per foot Lbeam 5 4 1.151 10 in 2 Ibeam Ibeamf Minimum moment of inertiayt 16.5inDepth from centroid to top of beamyb 16.5inDepth from centroid to soffit of beamST Ibeam3 3 6.978 10 inytSB Ibeam3 6977.86 inybMinimum section modulus about top flangeMinimum section modulus about bottom flangeEffective Flange Width of Concrete Deck Slab, AASHTO A 4.6.2.6Beam Design "Interior"Choose the design of the beam either"Interior" or "Exterior"beff.int S 8.00 ftbeff.ext beff Effective flange width of deck slab for interior beams1 S overhang 6.96 ft2Effective flange width of deck slab for exterior beamsbeff.int if Beam Design "Interior" 2.438beff.ext if Beam Design "Exterior"dtotal deckthick d 42 inTotal depth of section including deckDynamic load AllowanceDynamic load allowance from AASHTO Table 3.6.2.1-1 is applied as an increment to the static wheelloads to account for wheel load impacts from moving vehicles.Grace et al.Lawrence Tech.UniversityCollege of Engineering21000 W 10 Mile Rd., Southfield, MI48075, U.S.A.7/1/20197/1/2019
IM 1 33% 1.33Design FactorsThese factors are related to the ductility, redundancy and operational importance of the bridgestructure components and are applied to the strength limit state.DuctilityFor Strength limit State, a factor of 1.05 is used for nonductile components and connections, 1.00 forconventional designs and details complying with these specifications, and 0.95 for components andconnections for which additional ductility-enhancing measures have been specified beyond thoserequired by these specifications, AASHTO A 1.3.3.η D 1.00RedundancyFor Strength limit State, a factor of 1.05 is used for nonredundant members, 1.00 for conventional levelsof redundancy, foundation elements where ϕ already accounts for redundancy as specified in AASHTOA 10.5, and 0.95 for exceptional levels of redundancy beyond girder continuity and a torsionally-closedcross-section, AASHTO A 1.3.4.η R 1.00Operational ImportanceFor the Strength limit State, a factor of 1.05 is used for critical or essential bridges, 1.00 for typicalbridges, and 0.95 for relatively less important bridges, AASHTO A 1.3.5.η I 1.00Ductility, redundancy, and operational classification considered in the load modifier, AASHTO Eqn.1.3.2.1-2.η i η D η R η I 1.00Composite Section PropertiesThis is the moment of inertia resisting superimposed dead loads.Elastic Section Properties - Composite Section: k 2ksdl 2Ahaunchkn bftksdl ndhaunchkn d 2 haunch 0 inhaunch2effective area of haunch 33 inDepth of centroid of haunch to bottom of beam3Adhaunchkn dhaunchkn Ahaunchkn 0 inGrace et al.Lawrence Tech.UniversityCollege of Engineering21000 W 10 Mile Rd., Southfield, MI48075, U.S.A.7/1/20197/1/2019
beffkn beff 39.45 inksdl ndslabkn d haunch Transformed deck widthdeckthick twear 37.5 in2Area of transformed deck section2Aslabkn deckthick beffkn 355.09 in3Adslabkn Aslabkn dslabkn 13315.82 indk Abeam yb Adslabkn Adhaunchkn3Ioslabkn 4 2396.85 in12bftIhaunchkn ksdl nStatic moment of inertia of transformedsection about soffit of beam 23.06 inAbeam Aslabkn Ahaunchknbeffkn deckthickDepth from center of deck to beam soffitDepth of CG of composite section from beamsoffitMoment of inertia of transformed deck aboutcentroid3 haunch4 0 in12Effective moment of interia of the haunchMoment of inertia of composite section to resist superimposed dead loads calculated using parallelaxis theorem 2 Ioslabkn Aslabkn dslabkn dk 2 Ihaunchkn 225243.5 in42 Ahaunchkn dhaunchkn dk I3n Ibeam Abeam dk ybyb3n dk 23.055 inSb3n Depth of CG of composite section frombeam soffitI3n3 9769.69 inyb3nSection modulus about bottom of beamyt.bm.3n d yb3n 9.94 inSt.bm.3n I3nyt.bm.3nDepth of CG of composite sectionfrom top of beam3 22649.67 inyt3n d haunch deckthick twear yb3n 18.94 inSt3n I3n3 11889.54 inyt3nSection modulus about top of beamDepth of CG of composite sectionfrom top of deckSection modulus about top of deckElastic Section Properties - Composite Section: k 1These properties are used to evaluate the moment of inertia for resisting live loadsGrace et al.Lawrence Tech.UniversityCollege of Engineering21000 W 10 Mile Rd., Southfield, MI48075, U.S.A.7/1/20197/1/2019
Assumed wearing surface not included in the structural design deck thickness, per MDOT BDM7.02.19.A.4.k 1Ahaunchkn bft2kndhaunchkn d haunch 0 ineffective area of haunchhaunch 33 in2Depth of centroid of haunch to bottomof beam3Adhaunchkn dhaunchkn Ahaunchkn 0 inbeffkn beffkn 78.91 indslabkn d haunch Transformed deck widthdeckthick twear 37.5 in22Aslabkn deckthick beffkn 710.18 inArea of transformed deck section3Adslabkn Aslabkn dslabkn 26631.64 indk Abeam yb Adslabkn AdhaunchknAbeam Aslabkn AhaunchknIoslabkn beffkn deckthickbftIhaunchkn 312k nDepth from center of deck to beam soffit4 4793.7 in 26.49 inStatic moment of inertia of transformedsection about soffit of beamDepth of CG of composite sectionfrom beam soffitMoment of inertia of transformed deck aboutcentroid3 haunch4 0 in12Effective moment of interia of the haunchMoment of inertia of composite section to resist superimposed dead loads calculated using parallelaxis theorem 2 Ioslabkn Aslabkn dslabkn dk 2 Ihaunchkn 284103.5 in42 Ahaunchkn dhaunchkn dk In Ibeam Abeam dk ybybn dk 26.492 inGrace et al.Depth of CG of composite section frombeam soffitLawrence Tech.UniversityCollege of Engineering21000 W 10 Mile Rd., Southfield, MI48075, U.S.A.7/1/20197/1/2019
Sbn In3 10724.26 inybnSection modulus about bottom of beamyt.bm.n d ybn 6.51 inSt.bm.n Inyt.bm.nDepth of CG of composite section fromtop of beam3 43652.33 inSection modulus about top of beamytn d haunch deckthick twear ybn 15.51 inStn In3 18319.42 inytnDepth of CG of composite section fromtop of deckSection modulus about top of decklive load lateral Distribution FactorsType BCross-section classification.Distribution of live loads from the deck to the beams is evaluated based on the AASHTO specifieddistribution factors. These factors can only be used if generally, the following conditions are met; Width of deck is constant. Unless otherwise specified, the number of beams is not less than three Beams are parallel and have approximately the same stiffness. Curvature in plan is less than the limit specified in AASHTO A 4.6.1.2.4. Unless otherwise specified, the roadway part of the overhang does not exceed 3.0 ft. Cross-section is consistent with one of the cross-sections shown in AASHTO Table 4.6.2.2.1-1.Distribution of live loads for Moment in Interior Beams, AASHTO Table 4.6.2.2.2b-1Range of Applicability.if ( 6ft S 18ft "ok" "not ok" ) "ok"if ( 18in d 65in "ok" "not ok" ) "ok"if ( 20ft L 140ft "ok" "not ok" ) "ok" if NObeams 3 "ok" "not ok" "ok"One lane loaded S Mlane1 int 3.0ft Grace et al.0.35 S d ft 2 in 12.0L 0.25 0.374Lawrence Tech.UniversityCollege of Engineering21000 W 10 Mile Rd., Southfield, MI48075, U.S.A.7/1/20197/1/2019
Two or more lanes loadedS Mlane2 int 6.3ft 0.6 S d 12.0Lft 2 in 0.125 0.595 live load moment disribution factor for interior beam Mlane int max Mlane1 int Mlane2 int 0.595Distribution of live loads for Moment in Exterior Beams, AASHTO Table 4.6.2.2.2d-1One lane loaded (using the lever rule)The lever rule involves the use of statics to determine the lateral distribution to the exterior girder bysumming moments about the adjacent interior girder to determine the wheel-load reaction at the exteriogirder assuming the concrete deck is hinged at the interior girder. A wheel cannot be closer than 2'-0" tothe toe of barrier, and the standard wheel spacing is 6'-0". The evaluated factor is multiplied by themultiple presence factor, AASHTO Table 3.6.1.1.2-1.Summing moments about the center of the interior beam6 ft S overhang barrier width 2 ft 2 0.594R SThis factor is based on the lever armrule considring the wheel load andnot the resultant of both wheelMoment distribution factor for exterior beam, one load loaded. The 1.2 accounts for the multiplepresence factor, m from AASHTO Table 3.6.1.1.2-1 for one lane loadedMlane1 ext R 1.2 0.713Two or more lanes loadedHorizontal distance from the centerline of the exterior web of exterior beam at deck level to the interiorweb edge of curb or traffic barrier must be greater than 0'-0" de max overhang barrierwidth 0.5bfb 0.5bweb 0ft 0.00 ft Range of Applicability if 1ft de 5.5ft "ok" "not ok" "ok"lane fractione 0.97 de28.5ft 0.97Moment distribution factor for exterior beam, two or more lanes loadedMlane2 ext Mlane int e 0.577Grace et al.Lawrence Tech.UniversityCollege of Engineering21000 W 10 Mile Rd., Southfield, MI48075, U.S.A.7/1/20197/1/2019
Distribution of live loads for Moment in Exterior Beams, AASHTO C4.6.2.2.2dAASHTO LRFD 2014 recommends the rigid plate analysis only for steel beam-slab bridges. This wasa change from ealier versions of AASHTO. It is up to the designed to ignore the rigid plate analysis ortake it into consideration when calculating the DF for exterior beamAdditional special analysis investigation is required because the distribution factor for multigirder incross section was determined without consideration of diaphragm or cross frames. The multiplepresence factors are used per AASHTO Table 3.6.1.1.2-1. This analysis should be done by sketchingthe cross section to determine the variables required for this example, the defined deck geometry isused. For any other geometry, these variables should be hand computed and input:Horizontal distance from center of gravity of the pattern of girders to the exterior girderXext Sexterior2 28.00 ftEccentricity of the center line of the standard wheel from the center of gravity of the pattern of girders6fte1 Xext overhang barrierwidth 2ft 24.75 ft2e2 e1 12ft 12.75 fte3 e2 12ft 0.75 fte4 e3 12ft 11.25 ftGrace et al.Lawrence Tech.UniversityCollege of Engineering21000 W 10 Mile Rd., Southfield, MI48075, U.S.A.7/1/20197/1/2019
Summation of eccentricities for number of lanes considered:eNL1 e1 24.75 ftOne lane loadedeNL2 e1 e2 37.5 ftTwo lanes loadedeNL3 eNL2 e3 38.25 ftThree lanes loadedeNL4 eNL3 e4 27 ftFour lanes loadedHorizontal distances from the center of gravity of the pattern of girders to each girder 28.00 20.00 12.00 4.00 Xbeams for i 0 NObeams 1 ft 4.00 Xi Xext ( i S) 12.00 X 20.00 28.00 Summation of horizontal distances from the center of gravity of the pattern of girders to each girderXNB Xbeams2 2688.00 ft2Xext eNL1 1m1R 1.2 0.459XNB NObeams Reaction on exterior beam when one lane is loadedenhanced with the appropriate multiple lane factorfrom AASHTO Table 3.6.1.1.2-1Xext eNL2 2m2R 1.0 0.641XNB NObeams Reaction on exterior beam when two lanes are loadedenhanced with the appropriate multiple lane factorfrom AASHTO Table 3.6.1.1.2-1Grace et al.Lawrence Tech.UniversityCollege of Engineering21000 W 10 Mile Rd., Southfield, MI48075, U.S.A.7/1/20197/1/2019
Xext eNL3 3Reaction on exterior beam when three lanes arem3R 0.85 0.657 loaded enhanced with the appropriate multiple laneXNB NObeams factor from AASHTO Table 3.6.1.1.2-1Xext eNL4 4Reaction on exterior beam when four lanes arem4R 0.65 0.508 loaded enhanced with the appropriate multiple laneXNB NObeams factor from AASHTO Table 3.6.1.1.2-1live load moment disribution factor for exterior beam Mlane ext max Mlane1 ext Mlane2 ext m1R m2R m3R m4R 0.713Reduction of load Distribution Factors for Moment in longitudinal Beams on Skewed SupportsWhen the line supports are skewed and the difference between skew angles of two adjacent lines ofsupports does not exceed 10 degrees, the bending moments and shear forces are reduced inaccordance with AASHTO Table 4.6.2.2.2e-1 and 4.6.2.2.3c-1 respectively.MomentRange of Applicabilityθskew θskew if θskew 60 deg 44.652 deg60 deg if θskew 60 deg Mcorrfactor min 1.05 0.25 tan θskew 1.0 0.803Correction factor for momentReduced distribution factors at strength limit state for interior girders due to skewDF strength moment int Mlane int Mcorrfactor 0.477MomentReduced distribution factors at strength limit state for exterior girders due to skewDF strength moment ext Mlane ext Mcorrfactor 0.572MomentDesign distribution factors for service and strength limit statesDistribution factor for moment at strength limit stateDF strength moment DF strength moment int if Beam Design "Interior" 0.477DF strength moment ext if Beam Design "Exterior"Grace et al.Lawrence Tech.UniversityCollege of Engineering21000 W 10 Mile Rd., Southfield, MI48075, U.S.A.7/1/20197/1/2019
live load AnalysisFlexureAs per AASHTO A 3.6.1.2.1, vehicular live loading designated by the standard Hl-93 truck shall be acombination of the design truck or design tandem, and the design lane load. To produce extreme forceeffects, the spacing between the two 32-kip axles are taken as 14 ft.Calculate the maximum moment due to the truck load. Maximum truck load moment occurs when themiddle axle is positioned at distance 2.33 ft from the midspan. Maximum momment occurs under themiddle axle load. Moment due to distributed load occurs at midspan.Unless more detailed analysis is performed to determine the location and value for the maximummoment under combined truck and distributed loads at both service and strength limit state, themaximum moment from the truck load at distance 2.33 ft from midspan can be assumed to occur atthe midspan and combined with the maximum moment from other dead and live distributed loadsCalculate the reaction at the end of the span8kip L 2R 16.33ft 32kip 2.33ft 32kip L 2 L 2L 11.67ft 38.527 kipCalculate the maximum momentLMtruck R 2.33ft 32 kip 14 ft 924.387 kip ft 2 Maximum moment due to design lane load, AASHTO A 3.6.1.2.4X L 33.292 ft2Mlane 0.64klf L X2 0.64klf X22 354.67 kip ftMaximum moment due to design tandem, MDOT BDM 7.01.04.AMtandem 60kip L4 998.75 kip ftMaximum moment due to vehicular live loading by the modified Hl-93 design truck and tandem perMDOT BDM 7.01.04.A. Modification is by multiplying the load effects by a factor of 1.20. Dynamic loadallowance is considered only for the design truck and tandem, AASHTO A 3.6.1.2.2, 3.6.1.2.3 &3.6.1.2.4. MLLI 1.20Mlane IM 1.20 max Mtruck Mtandem DF strength moment 964.28 kip ft Grace et al.Lawrence Tech.UniversityCollege of Engineering21000 W 10 Mile Rd., Southfield, MI48075, U.S.A.7/1/20197/1/2019
Dead load AnalysisNoncomposite Dead load (DC1) Lbeam ωconc 2 wwebf ( x) Abeamf ( x) Abeamf kipw1 wwebf ( 0 in) 0.834 ftacting onkipw2 wwebf Lend 0.328 ft acting onLend 2.667 ftas uniform loadLvar 14.667 ftas triangular loadAdditional moment at mid-span due to weight of varying web width2Msw.web w1 Lend2ωbeam LMbeam 8 Lvar 3 0.5 w2 Lvar Lend 21.15 kip ft2 451.67 kip ftMswbeam Msw.web Mbeam 472.82 kip ftkipdeck deckthick beff haunchd bft 0.15 1.00 klf3ft Mdeck deck L8 Total moment due to selfweight ofbeamSelfweight of deck and haunch onbeam2 554.17 kip ft Moment due to selfweight of deck andhaunchsip 15psf beff bft 0.06 klfGrace et al.Total moment due to selfweight of beamwithout the varying width15 psf weight included for stay-in-placeforms per MDOT BDM 7.01.04.ILawrence Tech.UniversityCollege of Engineering21000 W 10 Mile Rd., Southfield, MI48075, U.S.A.7/1/20197/1/2019
Msip sip L82 33.25 kip ftMoment due to stay-in-place formsdiaint 0 kipWeight of diaphragm at mid-span pereach interior beam. Zero if nodiaphragm is useddiaext 0 kipWeight of diaphragm at mid-span pereach exterior beam. Zero if no diaphragmis useddiaphragm diaint if Beam Design "Interior" 0 kipdiaext if Beam Design "Exterior" spadia 2 S bfb tan θskew 7.904 ftOne row of diaphragms at midspan areused.LMdia diaphragm 0 kip ft4Dead load (wt of beam deck SIPforms) acting on non-composite sectionDC1 ωbeam deck sip 1.875 klfMDC1 Mswbeam Mdeck Msip Mdia 1060.23 kip ftTotal midspan moment actingon the non-composite sectionComposite Dead load (DC2)util 12 ( 0plf ) 0 klfbarrier1weight 0.475barrier2weight 0.475sidewalk barrier kipftWeight per foot of first barrier (aestheticsparapet tube, MDOT BDG 6.29.10)kipftWeight per foot of first barrier (aestheticsparapet tube, MDOT BDG 6.29.10)2 walkwidth walkthick ωconcNObeamsbarrier1weight barrier2weightNObeamssoundwallweight 0.0 Grace et al.No utilities are supported by thesuperstructure 0.00 klf 0.12 klfWeight to due extra thickness ofsidewalk per beamTotal barrier weight per beamkipftWeight of the sound wall, ifthere is a sound wallLawrence Tech.UniversityCollege of Engineering21000 W 10 Mile Rd., Southfield, MI48075, U.S.A.7/1/20197/1/2019
Weight of the sound wall for exterior beam design assuming lever arm and an inetremiate hinge onthe first interior beamsoundwall kipif Beam Design "Interior"ft0 0 kipft( S overhang) soundwall if Beam Design "Exterior"weight S DC2 sidewalk barrier util
7- In the Mathcad sheet, the option of debondin g as well as to p prestressing strands are offered as Grace et al. Lawrence Tech.University College of Engineering 21000 W 10 Mile Rd., Southfield, MI 48075, U.S.A. pg pp