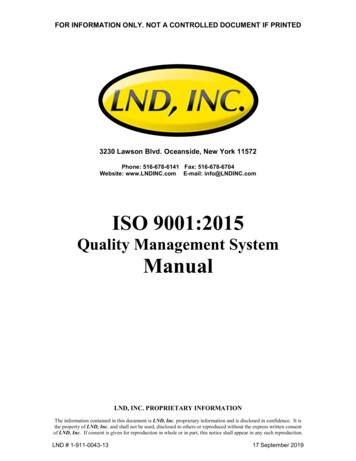
Transcription
FOR INFORMATION ONLY. NOT A CONTROLLED DOCUMENT IF PRINTED3230 Lawson Blvd. Oceanside, New York 11572Phone: 516-678-6141 Fax: 516-678-6704Website: www.LNDINC.com E-mail: info@LNDINC.comISO 9001:2015Quality Management SystemManualLND, INC. PROPRIETARY INFORMATIONThe information contained in this document is LND, Inc. proprietary information and is disclosed in confidence. It isthe property of LND, Inc. and shall not be used, disclosed to others or reproduced without the express written consentof LND, Inc. If consent is given for reproduction in whole or in part, this notice shall appear in any such reproduction.LND # 1-911-0043-1317 September 2019
Quality System Manual - Section 00QM INDEX, QMS FORMS, AND REVISION STATUSIssued by: Quality AssuranceEff. Date: 9/17/19Rev.: NSECTION 00 – QM INDEX, QMS FORMS, AND REVISION STATUSRev. NSECTION 1 – SCOPERev. E1.1About LND Quality Manual1.2Company Background1.3Products and Services1.4ExclusionsSECTION 2 – NORMATIVE REFERENCES2.1Regulatory Requirements2.2Standards and GuidelinesRev. JSECTION 3 - TERMS AND DEFINITIONSRev. DSECTION 4 – CONTEXT OF THE ORGANIZATIONRev. F4.1Understanding the Organization and its Context4.2Understanding the Needs and Expectations of Interested Parties4.3Determining the Scope of the Quality Management System4.4Quality Management System and its ProcessesSECTION 5 - LEADERSHIP5.15.25.3Rev. FLeadership and Commitment5.1.1General5.1.2Customer FocusPolicy5.2.1Establishing the Quality Policy5.2.2Communicating the Quality PolicyOrganizational Roles, Responsibilities and Authorities5.3.1Management RepresentativeSECTION 6 - PLANNINGRev. G6.1Actions to Address Risks and Opportunities6.2Quality Objectives and Planning to Achieve ThemApproved by/date:Spencer B. Neyland17 September 2019Pg. 2 of 50
QM INDEX, QMS FORMS, AND REVISION STATUSQuality System Manual6.3Section 00Rev.: NPlanning of ChangesSECTION 7 – SUPPORT7.1Rev. re7.1.4Environment for the Operation of Processes7.1.5Monitoring and Measuring Resources7.1.67.1.5.1General7.1.5.2Measurement TraceabilityOrganizational 7.5Documented Information7.5.1General7.5.2Creating and Updating7.5.3Control of Documented InformationSECTION 8 - OPERATION8.1Operational Planning and Control8.2Requirements for Products and Services8.3Pg. 3 of 508.2.1Customer Communication8.2.2Determining the Requirements for Products and Services8.2.3Review of the Requirements for Products and Services8.2.4Changes to Requirements for Products and ServicesDesign and Development of Products and Services8.3.1General8.3.2Design and Development Planning8.3.3Design and Development Inputs8.3.4Design and Development ControlsRev. F
QM INDEX, QMS FORMS, AND REVISION STATUSQuality System Manual8.48.58.3.5Design and Development Outputs8.3.6Design and Development ChangesSection 00Pg. 4 of 50Control of Externally Provided Processes, Products and Services8.4.1General8.4.2Type and Extent of Controls8.4.3Information for External ProvidersProduction and Service Provision8.5.1Control of Production and Service Provision8.5.2Identification and Traceability8.5.3Property Belonging to Customers or External Providers8.5.4Preservation8.5.5Post-delivery Activities8.5.6Control of Changes8.6Release of Products and Services8.7Control of Nonconforming OutputsSECTION 9 – PERFORMANCE EVALUATION9.1Rev.: NRev. BMonitoring, Measurement, Analysis and Evaluation9.1.1General9.1.2Customer Satisfaction9.1.3Analysis and Evaluation9.2Internal Audit9.3Management Review9.3.1General9.3.2Management Review Inputs9.3.3Management Review OutputsSECTION 10 – IMPROVEMENT10.1General10.2Nonconformity and Corrective Action10.3Continual ImprovementRev. C
QM INDEX, QMS FORMS, AND REVISION STATUSQuality System ManualSection 00Rev.: NPg. 5 of 50ATTACHMENTS1NOTE:ISO9001:2015 Comparison to ISO9001:2008Rev. AFor a complete listing of all current Quality Operational Procedures (QOP) andWork Instructions (WI) related to the LND QMS refer to LND procedure 1-9110091.
QM INDEX, QMS FORMS, AND REVISION STATUSQuality System ManualSection 00QUALITY SYSTEM FORMS1-900-0012Re-graded Tube Assemblies1-900-0017Design Specification Sheet1-901-0001Plant Maintenance Work Order1-901-0003Scrap-Do Not Salvage1-901-0007Supplier Certification1-904-0004Customer Property Inventory1-911-0004Material Rejection Report (MRR)1-911-0005Supplier Corrective Action Request (SCAR)1-911-0006Engineering Change Request (ECR)1-911-0008Calibration Record Card1-911-0009Employee Qualifications1-911-0028Engineering Change Order (ECO)1-911-0032Audit Nonconformity Report (QF-82-02-2)1-911-0033Supplier Quality System Survey1-911-0034Corrective Action Request (QF-85-03-1)1-911-0038Conditional Acceptance Authorization and Validation1-911-0039Internal Audit Checklist1-911-0040Internal Audit Plan (QF-82-02-1)1-911-0064Quality Audit of LND Suppliers1-911-0084In-House Calibration Certificate1-911-0086FMEA Worksheet1-913-0004Customer Return Disposition Log1-914-0004WIP Output Log1-915-0013Training Record1-511-0069Initial Electrical Test Card1-511-0062NCR Tag1-511-0075Rework TagQF-85-02-1Customer ComplaintRev.: NPg. 6 of 50
QM INDEX, QMS FORMS, AND REVISION STATUSQuality System ManualRev.: NSection 00Pg. 7 of 50Quality System Manual RevisionsREV.PAGESCHANGEREQUEST #DATEAUTHORIZED BY00AllInitial Release10/18/07S. Neyland01IncorporatedECR 8528/21/09S. Neyland02IncorporatedECR 126011/1/10S. Neyland03IncorporatedECR 13382/11/11S. Neyland04IncorporatedECR 153011/30/11S. Neyland05IncorporatedECR 17392/12/13S. Neyland06IncorporatedECR 18669/27/13S. Neyland07IncorporatedECR 21438/25/14S. Neyland08IncorporatedECR 23409/8/15S. Neyland09IncorporatedECR 25319/1/16S. Neyland10IncorporatedECR 269512/14/17S. Neyland11Update manual to the ISO9001:2015standard.ECR 27571/30/18S. Neyland12Corrections to a QOP-74-01 and 74-03callouts. Removing para 6.1.3 –Preventive ActionECR 29875/21/19S. Neyland13Revise the Process Map, correct QOPtitles, and correct formatting errorsECR 30519/17/19S. Neyland
QM INDEX, QMS FORMS, AND REVISION STATUSQuality System ManualQuality System Manual AvailabilitySection 00Rev.: NPg. 8 of 50Copies of this manual are available online at the LND, Inc. website (www.LNDINC.com) fordownloading and also on the LND intranet PICS system affording access to all LND employees.Printed copies of this manual are considered to be uncontrolled and the information obsoleteimmediately upon being printed.
Quality System Manual - Section 1SCOPE AND EXCLUSIONSIssued by: Quality Assurance1.1Eff. Date: 1/31/18Rev.: EPg. 9 of 50About LND Quality ManualLND, Inc. Quality System Manual provides general policies and procedures for themanufacturing, packaging, testing, storage, and distribution of products and services.The LND, Inc. Quality System Manual is a top-tier quality document for LND, Inc.located at 3230 Lawson Blvd, Oceanside, NY 11572.1.2Company BackgroundLND, Inc. designs, engineers and manufactures gas-filled nuclear radiation detectors.Since 1964, LND has developed a product line that encompasses all the commercial,scientific and military applications for nuclear radiation detectors, and we have soldover two million detectors worldwide.LND, Inc. developed and implemented a quality management system to demonstrateits ability to provide products and services that consistently meet customer, statutoryand regulatory requirements, and to address customer satisfaction through the effectiveapplication of the quality management system, including continual improvement andthe prevention of nonconformities. The quality management system complies with theinternational standard ISO 9001:2015 and government specification MIL-PRF-1N.1.3Products and ServicesLND’s product line includes Geiger-Mueller Tubes, Energy Compensated GeigerMueller Tubes, End- and Side-Window X-ray Proportional Counters, PositionSensitive Detectors, BF3 and 3He Neutron Proportional Detectors, IonizationChambers, Fission Counters, Neutron Beam Monitors, Flow Counters, and PolymerWindow Proportional Counters.Applications for LND products include, but are not limited to, Health Physics,Analytical Instrumentation, Environmental and Air Quality Monitoring, PersonnelMonitoring, Power Plant Applications, Industrial Gauging, Medical Instrumentation,High Energy Physics Research, X-Ray Spectroscopy, Non-Destructive Testing,Homeland Security, and Space Exploration.1.4ExclusionsNo exclusions taken.Approved by/date:Spencer B. Neyland27 April 2018
Quality System Manual - Section 2NORMATIVE REFERENCESIssued by: Quality Assurance2.1Eff. Date: 5/21/19Rev.: JPg. 10 of 50REGULATORY REQUIREMENTS10CFR50, Appendix B: Quality Assurance Criteria for Nuclear Power Plants and FuelReprocessing Plants15CFR Parts 730 – 774: Export Administration Regulations (EAR)MIL-PRF-1: Performance Specification; Electron Tubes, General Specifications for49CFR Parts 106, 107 and 171 – 180: Pipeline and Hazardous Materials Administration,Department of TransportationInternational Civil Aviation Organization (ICAO) – Technical Instructions for the Safe Transportof Dangerous GoodsInternational Maritime Dangerous Goods Code (IMDG)ADR/RID Transportation Regulations (EU)IATA Dangerous Goods Regulations2011/65/EU and EU 2015/863 – Restrictions on Hazardous Substances II & III (RoHS)Directives2012/19/EU – Waste Electrical and Electronic Equipment (WEEE) DirectiveEC/1907/2006 – Registration, Evaluation and Authorization of Chemicals (REACH) DirectiveDodd-Frank Wall Street Reform and Consumer Protection Act – Section 1502, Conflict Minerals2.2STANDARDS AND GUIDELINESInternational Standard ISO9001:2015: Quality management systems - RequirementsAmerican National Standard ANSI/ISO/ ASQ Q9000-2015: Quality management systemsFundamentals and vocabularyAmerican National Standard ANSI/ISO/ ASQ Q9004-2009: A quality management approachManaging for the sustained success of an organizationISO 10002-2014: Quality Management - Customer Satisfaction – Guidelines for complainthandling in organizationISO 11118-2015: Gas cylinders – Non-refillable metallic gas cylinders-Specification and testmethodISO 19011-2018: Guidelines for auditing management systemsApproved by/date:Spencer Neyland22 May 2019
Quality System Manual - Section 3TERMS AND DEFINITIONSIssued by: Quality AssuranceEff. Date: 1/31/18Rev.: DPg. 11 of 503.1Audit: Systematic, independent and documented process for obtaining objectiveevidence and evaluating it objectively to determine the extent to which the auditcriteria are fulfilled.3.2Audit Criteria: Set of policies, procedures or requirements used as a reference againstwhich objective evidence is compared.3.3Audit evidence: Documented information, statements of fact or other information,which are relevant to the audit criteria and verifiable.3.4Competence: Ability to apply knowledge and skills to achieve intended results.3.5Context of the organization: Combination of internal and external issues that canhave an effect on an organization’s approach to developing and achieving itsobjectives.3.6Continual improvement: Recurring activity to enhance performance.3.7Correction: Action taken to eliminate a detected nonconformity.3.8Corrective action: Action to eliminate the cause of nonconformity and to preventrecurrence.3.9Customer owned property: Any type of part, sub-assembly, fixture, accessories,manuals, drawings, computers, software, shipping containers that belong to acustomer.3.10Customer satisfaction: Customer’s perception of the degree to which the customer’sexpectations have been fulfilled.3.11Defect: Nonconformity related to an intended use or specific use.3.12Document: Information and the medium on which it is contained.3.13Documented information: Information required to be controlled and maintained byan organization and the medium on which it is contained.3.14External provider: Organization that provides a product or a service.3.15Interested party: Person or organization that can be affected, be affected by, orperceive itself to be affected by a decision or activity.3.16Nonconformity: Nonfulfillment of a requirement.3.17Outsource: Make an arrangement where an external organization performs part of anorganization’s function or process.3.18Procedure: Specific way to carry out an activity or a process.Approved by/date:Spencer B. Neyland27 April 2018
QUALITY MANAGEMENT SYSTEMQuality System ManualSection 03Rev.: DPg. 12 of 503.19Process: Set of interrelated or interacting activities that use inputs to deliver anintended result.3.20Products and services: Output of an organization that can be produced without anytransaction taking place between the organization and the customer.3.21Quality: Degree to which a set of inherent characteristics of an object fulfillsrequirements.3.22Quality assurance: Part of quality management focused on providing confidence thatquality requirements will be fulfilled.3.23Quality control: Part of quality management focused on fulfilling qualityrequirements.3.24Quality improvement: Part of quality management focused on increasing the abilityto fulfill quality requirements.3.25Quality management: Coordinated activities to direct and control an organizationwith regard to quality.3.26Quality policy: Overall intentions and direction of an organization related to qualityas formally expressed by top management.3.27Record: Document stating results achieved or providing evidence of activitiesperformed.3.28Risk and opportunity action: Action to eliminate the cause of a potentialnonconformity or other potential undesirable situation.3.29Service: Output of an organization with at least one activity necessarily performedbetween the organization and the customer.3.30Top management: Person or group of people who directs and controls anorganization at the highest level.3.31Validation: Confirmation, through the provision of objective evidence, that therequirements for a specific intended use or application have been fulfilled.3.32Verification: Confirmation, through the provision of objective evidence, that specifiedrequirements have been fulfilled.
Quality System Manual - Section 4CONTEXT OF THE ORGANIZATIONIssued by: Quality Assurance4.14.2Rev.: FPg. 13 of 50Understanding the Organization and its Context4.1.1LND, Inc. identifies the processes needed for the Quality ManagementSystem and their application per the Process Flow Diagram and the ProcessMap Diagram in paragraph 4.4 of this manual.4.1.2LND, Inc. determines the sequence and interactions of processes by carefullyanalyzing processes, systems, and procedures per Operational Procedure QOP84-01, Analysis of Data. Documented information of these process sequenceand interactions may be in various forms, such as; flowcharts, memoranda,and other internal documents.4.1.3LND, Inc. determines criteria and methods to ensure Quality ManagementSystem processes based on nature, relative importance, and priority. Thesemethods and criteria are documented as per Operational Procedure QOP 5601, Management Review.4.1.4LND, Inc. ensures the availability of resources and information necessary tosupport the operation and monitoring of these processes per OperationalProcedures QOP 62-01, Competence, Awareness and Training, and QOP 6301, Equipment Maintenance.4.1.5LND, Inc. monitors, measures, and analyzes these processes per OperationalProcedure QOP 74-01, Evaluation and Monitoring.4.1.6LND, Inc. implements actions necessary to achieve planned results perOperational Procedure QOP 85-03, Corrective Action.4.1.7LND, Inc. performs risk assessments and takes action to address these risksand opportunities per LND procedure 1-911-0095, Risk Analysis.4.1.8LND, Inc. shall determine external and internal issues that are relevant andhave an impact on the Quality Management System. These issues areaddressed with senior management during the course of the ManagementReview process.Understanding the needs and expectations of interested parties4.2.14.3Eff. Date: 9/17/19LND, Inc. monitors and reviews the needs of interested parties during thecourse of the Management Reviews. Refer to LND procedure 1-911-0099,Interested Parties.Determining the scope of the quality management system4.3.1LND, Inc. quality management system is designed to meet the requirementsof our commercial and government customers per ISO9001:2015 and MIL-Approved by/date:Spencer B. Neyland17 September 2019
QUALITY MANAGEMENT SYSTEMQuality System ManualSection 4Rev.: FPg. 14 of 50PRF-1.4.3.2The LND, Inc. Quality System Manual is a top-level or Level 1 document,along with policies, objectives, and organization interaction of processes perOperational Procedure QOP 42-01, Control of Documents.LND, Inc. Quality Operational Procedures (QOPs) and documents requiredby the ISO 9001 standard are Level 2 documents.LND, Inc. work instructions, engineering drawings, testing procedures,manufacturing specifications, and other technical documentation that describeproduct manufacture, servicing processes, and flowcharts are Level 3documents.LND, Inc.’s production records, test records, training records, internal andexternal audit reports, and other quality records, etc. are Level 4 documents.4.3.3Quality System ManualLND, Inc. maintains a Quality System Manual that is reviewed over thecourse of a year during the Management Review process. Anychanges/revision to the manual can only incorporated by the QA Manager aspart of LND procedure 1-900-0007, Engineering Changes. All revisionchange requests must be reviewed and signed by the persons listed in theEngineering Changes procedure.4.3.4ScopeThe scope of this Quality Management System includes the design andmanufacturing of nuclear radiation detectors.4.3.5ApplicabilityIn total, LND, Inc. applies all elements of the ISO 9001:2015 standard.4.4Quality Management System and its processesThe Quality Management System is designed as a system of interrelatedprocesses. All main activities of the system are defined as Quality SystemProcesses (QSPs) and are grouped into the following four categories (refer tothe Process Matrix and Process Map in this section of the Quality Manual): Product Realization Processes (PRP), Measurement, Analysis and Improvement Processes (MIP), Management Responsibility Processes (MRP), and Resource Management Processes (RMP)These processes are organized as Plan-Do-Check-Act (PDCA) loops.The sequence and interrelation between the four groups and individual QSPsare illustrated in the Processes Map diagram. For a detailed illustration ofsequence and interaction production processes, including key processindicators, refer to Operational Procedure QOP-41-01, Production Processes.
QUALITY MANAGEMENT SYSTEMQuality System ManualSection 4Rev.: FPg. 15 of 50Quality system documentation also defines criteria and methods needed toensure that the operation and control of quality system processes are effective.This includes assignment of responsibilities and allocation of resources for theprocess, instructions on how to carry out (or operate) the process, anddefinition of methods for monitoring and/or measuring the effectiveness of theprocess.The Quality Management System (QMS)Process Flow Diagram
QUALITY MANAGEMENT SYSTEMQuality System ManualRev.: FSection 4Pg. 16 of 50CustomerRFQs, Quotes, OrdersMarket ResearchPROCESS MAPPRP01PRP09RMP02RMP03Sales and OrderProcessingDesign andDevelopment ofProducts andServicesInformation,Document Controland ITFacilities,Equipment &Work EnvirmntRMP01PersonnelCompetenceand AwarenessResourcesResource Mngmnt Processes onitoring,Measurement,Analysis andEvaluationProduct Realization Processes (PRP)ReceivingProduction andQualityPlanningPolicies &DirectionsMngmnt ResponsibilityProcesses esses,Products andServicesMRP03ImprovementPolicies &DirectionsMRP01Planning PRP05Production andServiceMeasurement, Analysisand Improvement Processes (MIP)MIP01Control ataMIP02MIP03Non-conform,Corr. Action,Risk and Opp.Internal AuditsMIP04CustomerComplaints/SatisfactionCustomer
QUALITY MANAGEMENT SYSTEMQuality System ManualSection 4Rev.: FPg. 17 of 50PROCESS MAP MATRIXPRODUCT REALIZATION PROCESSES (PRPs)PurposeSales and Order ProcessingTo determine customer requirements, prepare bids and quotations, submit tenders, and takeorders from, or enter into contracts with, customers.Process OwnerSalesSub-Processes Determining products and services requirementsDetermining customer requirementsEvaluating capability and capacity to meet requirementsPreparing quotations, bids and tendersEntering orders (or signing contracts)Receiving, entering and processing change ordersProviding products and services informationDesign and Development of Products and ServicesPurposeProcess OwnerTo design and develop products and services meeting the design input requirements.Sub-Processes PurposeEngineeringPlanning and scheduling design projectsReviewing and controlling design inputPerforming design activitiesConducting design reviewsEstablishing design output documented informationVerifying and validating products and services designsControlling design changesProduction/Quality PlanningTo plan and develop processes needed for manufacturing and verification of products andservices.Process OwnerEngineeringSub-Processes Determining quality objectives and requirements for products and services Developing, validating and documenting production processes (process sheets, equipmentsetup instructions, tooling specifications, operator instructions, etc.) Establishing products and services acceptance criteria and products and servicesverification requirements (measuring, inspections, tests, etc)PurposeExternally Provided Processes, Products and ServicesProcess OwnersSub-ProcessesTo select qualified external providers and to purchase from them materials, components, andservices necessary for the manufacture and delivery of the products and services (for fullscope of application refer to 1-901-0005, LND Supplier Manual).Purchasing / Quality ReceivingEvaluating and selecting external providersMaintaining a list of approved external providers (approved vendor list)Preparing, reviewing and issuing purchasing documented informationCommunicating with external providers regarding their quality performance (notifications,requests for corrective actions, etc.)
QUALITY MANAGEMENT SYSTEMQuality System ManualPurposeProcess OwnerSub-ProcessesPurposeSection 4Rev.: FPg. 18 of 50To receive purchased products and services, visually verify their conformity, and mark/labelproducts with their identification and/or acceptance status, as applicable.Receiving Receiving purchased products Visually inspecting incoming products Applying and/or recording product identification and traceability of incoming productsIdentification and TraceabilityTo receive, store and issue materials, components and parts to be incorporated into finishedproducts and services.Process OwnerStock RoomSub-Processes Operating and maintaining storage areasIdentifying and protecting product in storageMaintaining special storage conditions/environmentOperating and maintaining the inventory management systemIdentification of monitoring and measuring equipment.Production and ServicesPurposeProcess OwnerTo manufacture products conforming to applicable requirements.Sub-Processes DeliveryProductionCarrying out manufacturing processesMonitoring and controlling manufacturing processesEstablishing and maintaining production documented informationTraining process operators and technicians (on-the-job)Maintaining production equipment and toolingPurposeProcess OwnerTo deliver products to customers and distributors.Sub-Processes PurposeShippingProcessing shipping ordersPackaging and labeling product for shippingDispatching or shipping productsEstablishing and maintaining shipping and distribution documented informationMonitoring, Measurement, Analysis and EvaluationTo verify conformity of products and services, evaluate the effectiveness and efficiency of thequality management system, and identification and calibration of monitoring and measuringequipment.Process OwnerQualitySub-Processes Monitoring quality performance of external providersVerifying purchased product (QC inspection)Monitoring, measuring, and testing products (in-process and final)Verifying inspection status identificationAnalyzing and evaluating results of internal, third-party and customer auditsCollecting and analyzing quality performance dataReleasing products and servicesIdentifying nonconforming products and servicesSelecting, calibrating and controlling the monitoring and measuring equipment
QUALITY MANAGEMENT SYSTEMQuality System ManualSection 4Rev.: FPg. 19 of 50MEASUREMENT AND IMPROVEMENT PROCESSES (MIPs)Control of Nonconforming OutputsPurposeProcess OwnersTo identify, control and disposition nonconforming outputs (products and services).Sub-Processesand Procedures Identifying, documenting and segregating (where applicable) nonconforming products andservices Making nonconforming products and services disposition decisions Reworking and verifying nonconforming products and servicesQuality / EngineeringInternal AuditsPurposeProcess OwnerTo verify conformity of the quality management system.Sub-Processesand Procedures PurposeQualityScheduling of internal audits.Conducting internal audits of the quality management system.Monitoring the effectiveness and efficiency of the internal audits.Conducting training of internal auditors.Nonconformities, Corrective Actions, Risk and OpportunityTo request, implement and follow up nonconformities, corrective actions, risk andopportunity.Process OwnerQualitySub-Processesand Procedures Evaluating the need for corrective actions, risk and opportunity Requesting and implementing corrective actions, risk and opportunity Verifying the implementation and effectiveness of corrective actions, risk and opportunityCustomer Complaints & SatisfactionPurposeProcess OwnerTo process customer feedback and complaints and to measure customer satisfaction.Sub-Processesand Procedures Customer ServiceReceiving and logging customer feedback and complaintsProcessing and responding to customer complaintsGathering of information and data about customer satisfactionAnalyzing, reporting and presenting customer satisfaction information and data (preparingreports, plotting charts, holding meetings, etc)MANAGEMENT RESPONSIBILITY PROCESSES (MRPs)PurposePlanning and ObjectivesTo define the quality policy and quality objectives, to plan the quality management system(QMS), and to implement management commitments.Process OwnerManagementSub-Processesand Procedures Establishing quality policyEstablishing and monitoring of quality objectivesPlanning the quality management systemDefining responsibilities and authorities Appointing Management Representative
QUALITY MANAGEMENT SYSTEMQuality System ManualPurposeSection 4Rev.: FPg. 20 of 50Management ReviewTo review the suitability and effectiveness of the quality system; to consider changes to thequality system, quality policy and quality objectives; and to identify opportunities forimprovement.Process OwnerManagementSub-Processesand Procedures Presentation, discussion and evaluation of review input information Determining changes required (if any) for the quality policy, quality objectives and thequality management system Identifying opportunities for improvement and establishing quality objectivesImprovementPurposeProcess OwnerTo continually improve the quality management system, processes, products and services.Sub-Processesand Procedures ManagementMonitoring performance of the quality management systemRequesting and implementing corrective actions, risks and opportunitiesEstablishing, reviewing and updating the quality policyEstablishing, implementing and monitoring quality objectivesImproving the Quality Management SystemRESOURCE MANAGEMENT PROCESSES (RMPs)Personnel Competence and AwarenessPurposeTo define competency requirements, provide training, and ensure awareness about qualityrelated issues.Process OwnerOperations / QualitySub-Processesand Procedures Determining competency requirements for jobs/positions affecting products and servicesquality Providing training and/or taking other actions to satisfy competency requirements Evaluating the effectiveness of training Providing awareness programs to ensure employee motivation, empowerment, andknowledge of quality-related issuesPurposeInformation, Document Control and ITTo control documented information related to products and services, manufacturing processesand the quality system; and to control quality documented information.Process OwnerTech CommSub-Processesand Procedures Establishing documented information needed by the organizationReviewing and approving documented informationControlling document revisions and distribution (availability)Managing retention, storage (electronic), and disposition of documented informationFacilities, Equipment and Work EnvironmentPurposeProcess OwnerTo ensure appropriate and adequate facilities, production equipment and supporting services.Sub-Processesand Procedures Plant, facility and equipment planning Maintaining plant, facilities and manufacturing process equipmentOperations
Quality System Manual - Section 5LEADERSHIPIssued by: Quality Assurance5.1Eff. Date: 9/17/19Rev.: FPg. 21 of 50Leadership and Commitment5.1.1General – LND, Inc. top management defines, develops and implementsthe quality management system per Operational Procedure QOP 56-01,Management Review Report.Top management demonstrates leadership and ensures that employees atall levels of the organization understand the goals and objectives of theLND, Inc. quality management system.LND, I
ISO 9001:2015 Quality Management System Manual . Quality System Manual - Section 00 QM INDEX, QMS FORMS, AND REVISION STATUS Issued by: Quality Assurance Eff. Date: 9/17/19 Rev.: N Pg. 2 of 50 Approved by/date: Spencer B. Neyland 17 September 2019 SECTION 00 – QM INDE