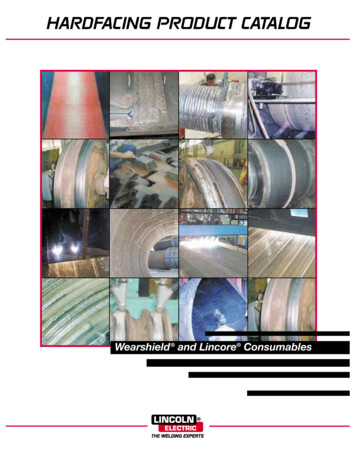
Transcription
HARDFACING PRODUCT CATALOGWearshield and Lincore Consumables
About The LincolnElectric CompanyLincoln Electric is the world’s premiermanufacturer of welding equipmentand consumables. No company onearth is more focused on the everchanging needs of the weldingprofessional. Our business is all abouthelping companies make their weldingoperations more effective, moreefficient, more profitable.Lincoln is truly your “One Source”when it comes to welding. We’re acompany that continually rededicatesitself to the equally important goals ofexceptional quality, and exceptionalservice. Our field support team –– withhundreds of field sales engineers andthousands of knowledgeable andresponsive Lincoln distributors in countries all over the world –– is thelargest in the industry.Innovative thinking. A quality andservice-first attitude. Freshapproaches to design, manufacturing,and packaging. Worldwide strength.That’s Lincoln Electric.What is Hardfacing?The American Welding Society defines hardfacing as "A surfacing variation inwhich surfacing material is deposited to reduce wear." The term surfacing isdefined as "The application by welding. . . of a layer, or layers, of material to asurface to obtain desired properties or dimensions, as opposed to making ajoint."AWS A3.0 Standard Welding Terms and DefinitionsWhat that means to you is that you can use hardfacing consumables fromLincoln Electric to: Get new life out of old parts Hardface new parts (such as on an OEM basis) to get better performancefrom new assemblies Hardface rather than replace partsAnd that extends the service life of your equipment subject to wear, saves youmoney, and sometimes, even makes a service part better than new!What are the benefits of Lincoln Hardfacing consumables? Frequently, the resulting deposit exhibits superior wear-resistant comparedto the original material. Often, the resulting deposit is harder than the original material. When properly applied, the hardfacing or build-up deposit will last longerthan the original material. Lincoln hardfacing and build-up deposits go on smoothly and exhibit betterwear characteristics than many competitive products intended for the sameapplication.Wide Range of Hardfacing ConsumablesWearshield Stick ElectrodesSelect a Wearshield electrode from a broadselection – one for almost any application. Deliver maximum welding application flexibility inremote locations. Compared to other welding processes, requiresthe least amount of equipment. Many Wearshield Stick Electrodes can be usedin all welding positions.Lincore Open Arc Self-Shielded and Gas-Shielded Wire Electrodes andSubmerged Arc Wire ElectrodesChoose a Lincore wire for maximum productivity, especially useful on multiplelayer or repetitive applications. Many alloys, sizes and packages are available. Produces a higher deposition rate than stick. Automatic welding, typically 1/8” (3.2 mm) electrode diameter and greater,requires the greatest amount of set-up, while delivering the highestdeposition rates and maximum productivity.Hardfacing2www.lincolnelectric.com
Lincolnweld Neutral and Alloy Submerged Arc FluxesUse a particular flux to tailor the resulting wear characteristicsfor your particular application. Neutral fluxes do not significantly change weld metalcomposition. Alloy fluxes are used with mild steel wire to make alloyweld deposits. Choosing the right flux can be simple with help from theWelding Experts at Lincoln Electric.Superior FeedabilitySet it and forget it! Lincore wire feeds beautifully, so your hardfacingoperators can concentrate on getting your equipmentback in service instead of on adjustments and restarts.Backed by the best welding company in the worldWearshield, Lincore and Lincolnweld hardfacing productsare designed, manufactured and supported by LincolnElectric – The world’s most respected name in welding.We asked welding professionals what they expect.Then we exceeded those expectations.Why? Total process capability – We understand weldingconsumables – and the equipment and systems used toapply them. Local support – Our sales engineers and hardfacingspecialists in the field are located at an office near you. Technical support – Part analysis and other applicationengineering services are available. Training – The world’s oldest welding school trainsindividuals or teams in standard or customized classesjust for you.Industry-leading consistencyConsistency matters to you, and it matters to us. We go toincredible lengths to ensure that our hardfacing products arethe most consistently performing consumables in theindustry. We check and re-check every pound of raw steel and fluxingredients. Our manufacturing processes are the most meticulouslydesigned, diligently monitored and technically advanced inthe industry, relying on Six Sigma process controls,optical emissions spectometry, x-ray analysis and our ownlong-studied Performance Development System. Diameter and chemical composition are verified at 19individual points throughout manufacturing.Contents . . . . . . . . . . . . . . . . .PageProduct Introduction . . . . . . . . 2-3Electrode SelectionGuide . . . . . . . . . . . . . . . . . . . . . 4-8Wearshield Stick Electrode . . 9-22Bare Rod for Oxy-Fuel andTIG Hardfacing andCoated Electrode forStick Welding . . . . . . . . . . . . 23-25Lincore Self-Shielded andGas-Shielded Wires . . . . . . . 26-42Lincore Submerged ArcWires . . . . . . . . . . . . . . . . . . . 43-48Precautions . . . . . . . . . . . . . . . . .49Lincore Submerged ArcWires for Roll Rebuilding . . . 50-52Lincolnweld Fluxes . . . . . . . . . . 53Packaging . . . . . . . . . . . . . . . . . . 54Exceptional Composition ControlIn test after test, Lincoln’s composition control systems haveshown to be significantly superior to that of other electrodesand wires on the market. Incredibly tight tolerances – means better and moreconsistent wear, less procedural adjusting, less waste andincreased efficiency.Outstanding Arc Stability Consistent and stable arcbehavior makes all thedifference in cutting time fromprocedural set-up and gettingthe hardfacing deposit andappearance characteristicsyou expect.Hardfacing3www.lincolnelectric.com
WEARSHIELD STICK ELECTRODE SELECTION GUIDEElectrodeNameRockwellHardness (Rc)GeneralDescriptionPolarityPageNo.Stick Electrode - Build-UpWearshield BU20 - 25DC ACBuild-up with moderate hardness to resist shock andmetal-to-metal wear, as in rolling and sliding. Can be usedas underbase for other hardfacing deposits or as finaloverlay on parts to be machined or forged. Use on mildand low alloy steels.9Wearshield BU-3031 - 38DC ACBuild-up with slightly higher hardness than Wearshield BU.Machinable deposit for build-up on medium carbon and lowalloy materials, or final overlay of medium hardness.10Stick Electrode - Metal-To-Metal WearWearshield MM45 - 58DC ACHigh hardness level for metal-to-metal wear with mild abrasion. 11Weld metal is heat treatable. Provides a martensiticwear-resistant steel deposit.Wearshield T&D58 - 65DC ACDeposit similar to Type M-1 tool steel, to resist metal-to-metalwear. Rebuilds dies and cutting edges of high speed tool steel.12Wearshield MI50 - 54DC ACResists metal-to-metal wear, mild abrasion and moderateimpact. Provides a martensitic deposit with considerableretained austenite. General purpose electrode, a goodcompromise of metal-to-metal wear, moderate impact andmild abrasion.13Wearshield Mangjet40 - 47(1)DC ACFor building up austenitic manganese steel and cladding carbon 14steels. Produces an austenitic manganese deposit that will workharden in service. Lowest cost austenitic manganese material.Wearshield 15CrMn40 - 50(1)DC ACProvides a premium austenitic chromium manganese deposit.Resists severe impact or gouging even in a single layer overcarbon steel. Used to join Hadfield manganese steel to itself orto carbon steel.Wearshield Frogmang 45 - 55(1)DC Designed specifically for building up manganese frogs and16manganese crossing diamonds in the railroad industry. Providesa high strength high alloy austenitic manganese deposit tohandle the increased loading of railroad cars.Wearshield ABR24 - 55DC ACProvides good resistance to abrasion, impact and some17metal-to-metal wear. Good hot forging properties. Hardness willvary based on cooling rate. Use on carbon, stainless andmanganese steels. Low cost general purpose abrasion andimpact product.DC ACModerate hardness to resist abrasion with impact up to 1100 F 18(593 C). Higher alloy results in improved spalling resistance thanWearshield ABR.Stick Electrode - Impact15Stick Electrode - Abrasion Plus ImpactWearshield 4442 - 48(1) The values shown are for work-hardened ranges. As-welded hardness ranges will be much lower.Hardfacing4www.lincolnelectric.com
WEARSHIELD STICK ELECTRODE SELECTION GUIDEElectrodeNameRockwellHardness (Rc)GeneralDescriptionPolarityPageNo.Stick Electrode - Metal-To-Earth WearWearshield ME49 - 59DC ACDesigned for metal-to-earth abrasion. High alloy produceschrome carbides and austenite. Provides greater abrasionresistance than Wearshield ABR or Wearshield 44.19Stick Electrode - AbrasionWearshield 6057 - 62DC ACWearshield 60 is designed to resist severe abrasion. It exhibitshigher alloy and higher abrasion resistance than WearshieldABR, Wearshield 44 or Wearshield ME.20Wearshield 7065 - 70DC ACResists very severe abrasion at temperatures up to 1400 F(760 C). Exhibits the highest abrasion resistance of theWearshield stick electrodes. Premium complex carbidedeposit.21Wearshield SM8045 - 60DC ACDesigned specifically for surfacing crushing rolls in the sugarcane industry. Chrome carbide deposit resists abrasive wear.22Stick Electrode - High Temperature Non-Ferrous (Cobalt)WearshieldC1 & C1 Bare50DC ACHighest abrasion resistance of the cobalt alloys. Resists23abrasion at room temperatures and when temperaturesexceed the limits of iron base alloys [1000-1800 F (538-982 C)].Can be used on screw conveyors moving hot minerals (coke)in a corrosive environment. Available as a coated electrode forstick welding and bare rod for TIG or oxy-fuel applications.WearshieldC6 & C6 Bare40DC ACResists metal-to-metal wear with mild abrasion and erosion atroom temperatures and when temperatures exceed the limitsof iron base alloys [1000-1800 F (538-982 C)]. Used for valveseats any where galling is a problem. Coated electrode for arcwelding or bare rod for TIG or oxy-fuel applications.WearshieldC21 & C21 Bare25DC ACResists metal-to-metal wear in severe corrosive environments 25at room temperatures and when service temperatures exceedthe limits of iron based alloys [1000-1800 F (538-982 C)].Used for high temperature impact cavitation and gallingresistance. Coated electrode for stick welding or bare electrodefor TIG welding. Oxy-fuel is not recommended.24Hardfacing5www.lincolnelectric.com
LINCORE WIRE SELECTION GUIDEElectrodeNameRockwellHardness (Rc)GeneralDescriptionPolarityPageNo.Self-Shielded and Gas-Shielded Cored Wires - Build-UpLincore BU78 - 98 RbDC Self-shielded, flux-cored wire provides a tough machinabledeposit for build-up or final overlay. Lincore BU deliversnon-severe metal-to-metal wear with outstanding crack resistance.26Lincore BU-G21 - 33DC Gas-shielded, metal-cored wire delivering deposits with moderatehardness for build-up or as final overlay. Lincore BU-G does providesome resistance to metal-to-metal wear and moderate impact.Can be used for the matrix with the Bulk Tungsten Carbide process.27Lincore 3314 - 34DC Self-shielded, flux-cored wire delivers tough machinable depositsfor build-up or final overlay intended for metal-to-metal wear.Use for build-up of steel mill parts such as rougher couplings.Also can be used as build-up under harder materials.28Self-Shielded and Gas-Shielded Cored Wires - Metal-to-Metal WearLincore 40-O36 - 41DC Self-shielded, flux-cored wire produces a deposit which resistsmetal-to-metal rolling or sliding wear as well as mild abrasion.Produces a martensitic deposit.29Lincore 5550 - 60DC Self-shielded, flux-cored wire with higher hardness for metal-to-metalwear and mild abrasion. Used on transfer rollers and guides, cranewheels and shafts.30Lincore 55-G50 - 57DC Gas-shielded, metal-cored wire produces a deposit which resistsmetal-to-metal wear and mild abrasion. The deposit results in an evenharder material when used with the Bulk Tungsten Carbide process.31Self-Shielded and Gas-Shielded Cored Wires - ImpactLincore T&D48 - 55DC Self-shielded, flux-cored wire delivers a deposit similar to H12 tool steel.For build-up of tool steel dies and edges, or applying wear resistancesurface on carbon or low alloy steels.32Lincore M30 - 48(1)DC The deposit of this self-shielded, flux-cored wire resists severe impactas well as moderate abrasion. Produces an austenitic manganesedeposit that work-hardens. Recommended for build-up and repairof Hadfield-type austenitic manganese materials as well as carbonand low alloy steels.33Lincore M-130 - 48(1)DC This self-shielded, flux-cored wire is recommended for the sameapplications as Lincore M. However, M-1 produces less slag.34Lincore 15CrMn44 - 55(1)DC This self-shielded, flux-cored wire deposits an austenitic manganesedeposit which exhibits very good crack resistance. Work-hardens foroverlay or joining austenitic manganese steel to itself or to carbon steel.Can be used as a build-up layer before capping with abrasionresistant alloys.35Lincore15CrMn LS44 - 55(1)DC This self-shielded, flux-cored wire is intended for the same applicationsas Lincore15CrMn. However, 15CrMn LS produces a lighter slag.36LincoreFrogmang40 - 50(1)DC Self-shielded, flux-cored wire designed for repair of manganese frogsand manganese crossing diamonds in the railroad industry. High alloyaustenitic manganese deposit.37(1) The values shown are for work-hardened ranges. As-welded hardness ranges will be much lower.Hardfacing6www.lincolnelectric.com
LINCORE WIRE SELECTION GUIDEElectrodeNameRockwellHardness (Rc)GeneralDescriptionPolarityPageNo.Self-Shielded and Gas-Shielded Cored Wires - Abrasion40 - 50(1)DC Gas-shielded, metal-cored wire, designed for repair of manganesefrogs and manganese crossing diamonds in the railroad industry.High alloy austenitic manganese deposit.38Lincore 5034 - 52DC Self-shielded, flux-cored wire delivers an abrasion resistantdeposit, even under conditions of moderate impact. Larger wirediameter sizes may be used for the submerged arc process.39Lincore 60-O55 - 60DC This self-shielded, flux-cored wire features higher alloy levels thanLincore 50. Its deposits resist both abrasion and moderate impact.Lincore 60-O can be used at temperatures up to 1300 F (704 C).40Lincore 60-G57 - 61DC This gas-shielded, metal-cored wire features higher alloy levels thanLincore 50. The deposits resist both higher levels of abrasion andmoderate impact. Lincore 60-G can be used at temperatures up to1300 F (704 C).41Lincore 65-O57 - 64DC Deposits of this self-shielded, flux-cored wire resist severe abrasionand light impact. These deposits include higher carbon and chromelevels than Lincore 60-O. It is recommended for use on wear plate,coal pulverizer rolls, earth engaging tools, and on slurry pipeand elbows.42LincoreFrogmang-GMetal-Cored Submerged Arc Wires - Build-UpLincore 30-S26 - 30DC This metal-cored wire is intended for build-up before final overlay,and as a final surface for metal-to-metal wear with moderate impact.Lincore 30-S is recommended for use with Lincolnweld 801 flux.43Lincore 32-S28 - 32DC This metal-cored wire is designed for build-up on 4140 drill stemsin the deep hole drilling industry. It is recommended for use withLincolnweld 802 flux.44Lincore 35-S33 - 39DC This metal-cored wire is intended for rolling and sliding metal-to-metalwear with moderate impact and abrasion. Use on crane and minecar wheels, rollers and shafts. Also can be used for build-up oncontinuous caster rolls prior to a stainless overlay.Recommended flux is Lincolnweld 801.45Metal-Cored Submerged Arc Wires - Metal-To-Metal WearLincore 40-S39 - 42DC This metal-cored wire is designed for rebuilding heavy equipmentundercarriages. The deposit resists rolling and sliding metal-to-metalwear. It is also machinable and hot forgeable.Recommended flux is Lincolnweld 801.46Lincore 42-S39 - 42DC This metal-cored wire is designed for rebuilding heavy equipmentundercarriages. The deposit exhibits enhanced crack resistanceand toughness compared to Lincore 40-S. It is intended to resistrolling and sliding metal-to-metal wear.Recommended flux is Lincolnweld 801.47Metal-Cored Submerged Arc Wires - Severe AbrasionLincore 60-S55 - 60DC Metal-cored wire which resists severe abrasion with mild impact. Can 48be used on carbon, low alloy, manganese and stainless steels, as wellas cast iron. Many layers can be applied using high travel speeds andsmall bead sizes, to promote close spaced cross check cracks.Recommended flux is Lincolnweld 803.(1) The values shown are for work-hardened ranges. As-welded hardness ranges will be much lower.Hardfacing7www.lincolnelectric.com
LINCORE WIRE AND LINCOLNWELD FLUX SELECTION GUIDEElectrodeNameRockwellHardness (Rc)GeneralDescriptionPolarityPageNo.Metal-Cored Submerged Arc Wires for Roll Rebuilding - Build-UpLincore 2023 - 28DC Metal-cored wire with moderate hardness for build-up beforefinal overlay. Good crack resistance and high compressivestrength. Recommended flux is Lincolnweld 801.Lincore 862016 - 20DC Metal-cored wire for build-up on worn or undersize rolls. A littlesofter than Lincore 20, for easier machining. Recommended fluxis 801.Lincore 413017 - 21DC Metal-cored wire for general build-up. Can be flame hardened to38 Rc. Also used on mining components such as cable drums,sheaves, gears and shafts. Recommended flux is 801.50 - 52Metal-Cored Submerged Arc Wires for Roll Rebuilding - Metal-to-Metal WearLincore 41027 - 32DC Metal-cored wire with a 410 martensitic stainless steel deposit. Lowcarbon content and corrosion resistant deposit. Soft and easilymachined. Flux recommendation is 801.Lincore 410NiMo32 - 40DC Metal-cored wire with low carbon deposit, which forms softer,tougher martensite than other roll alloys. Recommended flux is 801.Lincore 424A36 - 42DC Metal-cored wire with higher nickel content than 410NiMo alloy.Flux recommendation is 801.Lincore 423L41 - 47DC Metal-cored wire which provides a softer weld deposit than Lincore420, with more resistance to softening during tempering above 900 F(482 C). Recommended flux is 802.Lincore 423Cr41 - 47DC Metal-cored wire with a higher chrome deposit than Lincore 423Lfor improved corrosion resistance. Recommended flux is 802.Lincore 42046 - 50DC Metal-cored wire that is most widely used for caster roll rebuilding.Flux recommendation is 801.Lincore 96S48 - 54DC Metal-cored wire with a high carbon, 420 stainless steel deposit. Usewhere a higher hardness is required. Can be used on work rolls andbackup rolls, when water spray causes pitting on tool steel deposits.Flux recommendation is 801.Lincore 102W48 - 54DC Metal-cored wire which produces a tool steel deposit that retainshardness at high working temperatures. Used for guide rolls, and workrolls. Can also be used as the seat on blast furnace bells and hoppers.802 flux is recommended.Lincore 102HC54 - 60DC Metal-cored wire with a higher carbon content than Lincore 102W.Will give a higher hardness tool steel deposit. Deposit is “hot” [above400 F (204 C)] machinable, for easy sizing after welding.Recommended flux is 802.Lincolnweld Hardfacing FluxesH535Good metal-to-metal wear. Allows for some machinability.53A-96SType 420 stainless deposit with a carbon content near the high side foras-welded hardness.H560High alloy flux, excellent for severe abrasion.801, 802, 803, 860 & 880Lincolnweld neutral fluxes do not significantly change deposits composition,rather welding characteristics.Hardfacing8www.lincolnelectric.com
WEARSHIELD BUHardfacing Stick ElectrodeBuild-up and ModerateHardness to Resist Shock andMetal-to-Metal WearBuild-up with moderate hardness toresist shock and metal-to-metalwear, as in rolling and sliding. Canbe used as underbase for otherhardfacing deposits or as finaloverlay on parts to be machined orforged. Use on mild and low alloysteels.TYPICAL APPLICATIONS Low spatter gives Wearshield BUa high operator appeal.FOR BUILD-UP Welds in the flat and horizontalpositions as well as horizontalbeads on a vertical surface. Slag removes easily and cleanly. Unlimited layers with properpreheat, interpass temperaturesand procedures. Manufactured under a qualitysystem certified to ISO 9001requirements.ADVANTAGE LINCOLN Easy restrike and good arc action.Bucket Teeth Crusher HammersShovel and Bucket LipsPump Impellers and HousingsPulverizer PlowsMill HammersFOR HARDFACINGDEPOSIT COMPOSITION (1)On CarbonSteel%C%Mn%Si%Cr%S%P2 or moreLayers.141.15.601.40.025.015IdlersMine Car Wheels Trunnions/Shafts Tractor Rolls and Links Cranes GearsCOMPETITIVE PRODUCTSMECHANICAL PROPERTIES1 LayerRockwellHardness (Rc)2 Layers3 Layers15 - 2018 - 2323 - 28Stoody Buildup(1)NOTESUsing a short arc with a slight weave motion,deposit beads about 1/2” - 3/4” (13-19 mm)wide with the 5/32” and 3/16” (4.0 - 4.8 mm)electrode diameters, and about 1”(25 mm)wide with the 1/4” (6.4 mm) diameter.However, on edges and corners, fast-movingstringer beads or very narrow weaved beadsare usually preferred. The exact width andthickness of the bead will depend on themass of the piece being welded.Work-hardened base or weld metal shouldbe removed before applying Wearshield BU,since such areas are more prone toembrittlement and possible cracking.The part should be preheated to at least 70 F(21 C). Preheating above 100 F (40 C) isusually not required. Preheating dependslargely on the base metal composition. Onlarge, complex, or restrained parts, a preheatof 300 - 500 F (150 - 260 C) may benecessary.(1) Composition and properties depend upon dilution.Single layer deposit properties depend upon basemetal and/or build-up material.DIAMETERS / PACKAGINGDiameterInches (mm)5/323/161/410 Lb. (4.5 kg)Carton(40 Lb. Master)(4.0)(4.8)(6.4)ED021991ED021993McKay 3250 Lb. (22.7 kg)CartonED021992ED021994ED021995TYPICAL OPERATING PROCEDURESIMPORTANT: SPECIAL VENTILATION AND/OREXHAUST REQUIREDPolarity5/32” (4.0mm)Current (amps)3/16” (4.8mm)DC 145 - 210180 - 280230 - 360AC155 - 225200 - 290255 - 3751/4” (6.4mm)Fumes from the normal use of certain hardfacing weldingproducts contain significant quantities of componentssuch as chromium and manganese which can lower the5.0 mg/m3 maximum exposure guideline for general welding fume.BEFORE USE, READ AND UNDERSTAND THEMATERIAL SAFETY DATA SHEET (MSDS) FOR THISPRODUCT AND SPECIFIC INFORMATION PRINTED ONTHE PRODUCT CONTAINER.Preferred polarity is listed first.Hardfacing9www.lincolnelectric.com
WEARSHIELD BU-30Hardfacing Stick ElectrodeBuild-up and ModerateHardness to Resist Shock andMetal-to-Metal WearBuild-up with slightly higherhardness than Wearshield BU.Machinable deposit for build-up onmedium carbon and low alloymaterials, or final overlay of mediumhardness. High operator appeal, with easyrestrike and slag removal.ADVANTAGE LINCOLN Manufactured under a qualitysystem certified to ISO 9001requirements.TYPICAL APPLICATIONSFOR BUILD-UP Welds in the flat and horizontalpositions as well as horizontalbeads on a vertical surface. Unlimited layers with properpreheat, interpass temperaturesand procedures. Use on mild, medium carbon, lowalloy and high tensile steels.Pump Impellers Crusher HammersShovel and Bucket LipsPump HousingsDredge and Shovel Bucket TeethMill HammersFOR HARDFACINGDEPOSIT COMPOSITION (1)On CarbonSteel1 Layer2 Layers4 1.231.491.63.48.58.56Stoody Buildup1 LayerRockwellHardness (Rc)2 Layers4 Layers313538A preheat and interpass temperature of300 - 500ºF (150 - 260ºC) is necessary toprevent cracking, especially on large,complex or restrained parts.For most overlay applications, a weavingdrag technique on beads of about 1/2” (13mm) with all three diameter sizes can beused. Stringer beads can be used whenwelding on edges or around corners.For ease of machining, the following procedures should be adopted while welding: Preheat temperature should be in the300 - 500ºF (150 - 260ºC) range. Maintain interpass temperature of300 - 500ºF (150 - 260ºC). Use the largest diameter electrodepossible for the application, at the highestcurrent in the typical operating procedurerange. Anneal or normalize after welding. Heattreat after machining.layer deposit properties depend upon base metal and/orbuild-up material.DIAMETERS / PACKAGING3.24.05.0(1/8)(5/32)(3/16)McKay32NOTES(1) Composition and properties depend upon dilution. Single10 Lb. (4.5 kg)Carton(40 Lb. Master)IdlersCrane and Mine Car WheelsTrunnions and ShaftsChurn Bit PointsGears Cable DrumsSprockets Clutch JawsCOMPETITIVE PRODUCTSMECHANICAL PROPERTIES (1)Diametermm (Inches)Tractor Rolls Chain Links 50 Lb. (22.7 kg)CartonED024943ED024944ED024945Manufactured in metric diameters, U.S. customary sizes are approximate.TYPICAL OPERATING PROCEDURESPolarity3.2mm (1/8”)Current (amps)4.0mm (5/32”)5.0mm (3/16”)DC 90 - 130140 - 180170 - 220AC100 - 140150 - 200190 - 240IMPORTANT: SPECIAL VENTILATION AND/OREXHAUST REQUIREDFumes from the normal use of certain hardfacing weldingproducts contain significant quantities of componentssuch as chromium and manganese which can lower the5.0 mg/m3 maximum exposure guideline for general welding fume.BEFORE USE, READ AND UNDERSTAND THEMATERIAL SAFETY DATA SHEET (MSDS) FOR THISPRODUCT AND SPECIFIC INFORMATION PRINTED ONTHE PRODUCT CONTAINER.Preferred polarity is listed first.Hardfacing10www.lincolnelectric.com
WEARSHIELD MMHardfacing Stick ElectrodeResists Metal-to-Metal Wear andMild AbrasionHigh hardness for metal-to-metalwear with mild abrasion. Weld metalis heat treatable. Provides a martensitic wear-resistant steel deposit. Restrike is easy, slag removesvery easily and cleanly.TYPICAL APPLICATIONS Spatter is low, which gives it ahigh operator appeal. Unlimited layers with proper preheat, interpass temperatures andprocedures.ADVANTAGE LINCOLN Use on carbon steel and low alloysteel applications. Manufactured under a qualitysystem certified to ISO 9001requirements. Designed for all-position weldingexcept vertical-down.Cable Sheaves SprocketsCrane wheelsSkip wheelsCamsGear teethTransfer tablesCOMPETITIVE PRODUCTSDEPOSIT COMPOSITIONOn CarbonSteel%C2 Layers0.55(1)Stoody Multipass 22%Mn%Si%Cr%Mo0.51.44.50.5RockwellHardness (Rc)2 or more Layers45 - 5552 - 58(1) Composition and properties depend upon dilution. Singlelayer deposit properties depend upon base metal and/orbuild-up material.DIAMETERS / PACKAGINGDiametermm L PROPERTIES (1)1 LayerMcKay Hardalloy 5810 Lb. (4.5 kg)Carton(40 Lb. Master)ED021986ED02198850 Lb. (22.7 kg)CartonED021987ED021989ED021990Manufactured in metric diameters, U.S. customary sizes are approximate.0.5In welding with Wearshield MM, a short arc ispreferred. After welding is completed, theweldment should be covered and allowed tocool very slowly to near room temperature.Then, once cooled, postweld heat treatmentcan be used to temper martensite andtoughen the deposit.As deposited, Wearshield MM weld metal isnot machinable, although the deposit can beshaped by grinding. Tempering to toughenthe deposit is typically accomplished atabout 800 F (427 C), which will leave theweld metal near 50 Rockwell C. It can beannealed by heating to about 1400 F(760 C) for several hours, followed by slowcooling. Its hardness will then be less than 30Rockwell C. In this condition, it can be easilymachined.To fully re-harden, it is best to reheat toabout 1750 F (954 C) and hold for severalhours to dissolve all carbides and homogenize the steel. Then it can be water or oilquenched (thin sections can be air cooled) toharden, followed by tempering.A preheat and interpass temperature of300-500 F (149-260 C) is usually sufficientto prevent cracking. Higher temperaturesmay be necessary in cases of severerestraint and heavier thicknesses.IMPORTANT: SPECIAL VENTILATION AND/OREXHAUST REQUIREDTYPICAL OPERATING PROCEDURESPolarity3.2mm (1/8”)Current (amps)4.0mm (5/32”)DC 100 - 130140 - 170170 -220AC100 - 130140 - 170170 -2205.0mm (3/16”)Fumes from the normal use of certain hardfacing weldingproducts contain significant quantities of componentssuch as chromium and manganese which can lower the5.0 mg/m3 maximum exposure guideline for general welding fume.BEFORE USE, READ AND UNDERSTAND THEMATERIAL SAFETY DATA SHEET (MSDS) FOR THISPRODUCT AND SPECIFIC INFORMATION PRINTED ONTHE PRODUCT CONTAINER.Preferred polarity is listed first.Hardfacing11www.lincolnelectric.com
WEARSHIELD T&DHardfacing Stick ElectrodeResists Metal-to-Metal WearSimilar deposit to Type M-1 toolsteel to resist metal-to-metal wear.Rebuilds dies and cutting edges ofhigh speed tool steel.ADVANTAGE LINCOLN For building up worn tool steeldies or applying a wear resistantsurface to carbon steel or lowalloy steel parts. Welds in the flat and horizontalpositions as well as horizontalbeads on a vertical surface. Unlimited layers with proper preheat, interpass temperatures andprocedures. Manufactured under a qualitysystem certified to ISO 9001requirements.TYPICAL APPLICATIONSDie CastGuides Punch dies Trimmers Forging diesCOMPETITIVE PRODUCTS Restrike is easy, spatter is lowand slag removes easily andcleanly.Stoody 102EMcKay Hardalloy 61NOTESDEPOSIT COMPOSITION(1)On CarbonSteel%C%Mn%Si%Cr%Mo%W%V2 Layers0.650.40.73.756.01.81.1MECHANICAL PROPERTIES (1)RockwellHardness (Rc)As WeldedTempered58 - 6263 - 65(1) Composition and properties depend upon dilution. Singlelayer deposit properties depend upon base metal and/orbuild-up material.DIAMETERS / PACKAGINGDiametermm (Inches)2.53.24.010 Lb. (4.5 kg)Carton(40 Lb. Master)(3/32)(1/8)(5/32)ED021972ED0
Wearshield Stick Electrodes Select a Wearshield electrode from a broad selection – one for almost any application. Deliver maximum welding application flexibility in remote locations. Compared to other welding processes, requires the least amount of equipment. Many Wearshield Stick Electrod