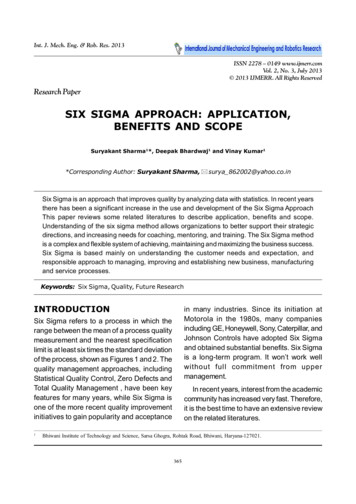
Transcription
Int. J. Mech. Eng. & Rob. Res. 2013Suryakant Sharma et al., 2013ISSN 2278 – 0149 www.ijmerr.comVol. 2, No. 3, July 2013 2013 IJMERR. All Rights ReservedResearch PaperSIX SIGMA APPROACH: APPLICATION,BENEFITS AND SCOPESuryakant Sharma1*, Deepak Bhardwaj1 and Vinay Kumar1*Corresponding Author: Suryakant Sharma, surya 862002@yahoo.co.inSix Sigma is an approach that improves quality by analyzing data with statistics. In recent yearsthere has been a significant increase in the use and development of the Six Sigma ApproachThis paper reviews some related literatures to describe application, benefits and scope.Understanding of the six sigma method allows organizations to better support their strategicdirections, and increasing needs for coaching, mentoring, and training. The Six Sigma methodis a complex and flexible system of achieving, maintaining and maximizing the business success.Six Sigma is based mainly on understanding the customer needs and expectation, andresponsible approach to managing, improving and establishing new business, manufacturingand service processes.Keywords: Six Sigma, Quality, Future ResearchINTRODUCTIONin many industries. Since its initiation atMotorola in the 1980s, many companiesincluding GE, Honeywell, Sony, Caterpillar, andJohnson Controls have adopted Six Sigmaand obtained substantial benefits. Six Sigmais a long-term program. It won’t work wellwithout full commitment from uppermanagement.Six Sigma refers to a process in which therange between the mean of a process qualitymeasurement and the nearest specificationlimit is at least six times the standard deviationof the process, shown as Figures 1 and 2. Thequality management approaches, includingStatistical Quality Control, Zero Defects andTotal Quality Management , have been keyfeatures for many years, while Six Sigma isone of the more recent quality improvementinitiatives to gain popularity and acceptance1In recent years, interest from the academiccommunity has increased very fast. Therefore,it is the best time to have an extensive reviewon the related literatures.Bhiwani Institute of Technology and Science, Sarsa Ghogra, Rohtak Road, Bhiwani, Haryana-127021.365
Int. J. Mech. Eng. & Rob. Res. 2013Suryakant Sharma et al., 2013MEASUREMENT SYSTEMANALYSISFigure 1: Illustrationof Centered 3 SigmaDiffusion of the watched commodities’parameter can be connected by the commodityitself or the system of measuring. The systemof measuring is made by operator, benchmarkand the method of measuring. MeasuringSystem Analysis (MSA) is a tool for theevaluation of accuracy and advisability of themeasuring system. It goes with testing ormeasuring the chosen parameter by theoperator. It monitors the influence ofrepeatance and reproducibility of the totalvariance. The goal of MSA is to estimate howthe system of measuring contributes to the totalvariance of watched parameter. Most of thetime, analysis of the measurement system isused in the phase of Measurements.Figure 2: Illustrationof Six Sigma processFigure 3: Measurement System AnalysisSix Sigma MethodsSix Sigma is based on six basic principles thathelp the implementation of Six Sigma methodto production companies or service industries.Six Sigma uses the base tools to improve thequality of products and processes asMeasurement System Analysis (MSA), IPODiagram (Input-process-output), Cause-andEffect diagram (CE), Histogram, Paretodiagram, Define, Measure, Analyze, Improve,Control (DMAIC), Run chart, Control chart,Scatter diagram, Regression Analysis,Designing of Experiments (DOE), FailureMode and Effect Analysis (FMEA), StandardOperating Procedure (SOP) and QualityFunction Deployment (QFD).Tolerance USL – LSL (area of matchingvalues for the customer),LSL - Lower Specification Limit,USL - Upper Specification Limit, 2 A (absolute) 2P (of product ) 2M(of measurement system), 2 – variance366
Int. J. Mech. Eng. & Rob. Res. 2013Suryakant Sharma et al., 2013ANALYSIS OF THE CAUSESAND CONSEQUENCESthe standard routine for planning andimplementation of the project.CE is a tool to solve problems through findingthe cause of their occurrence. It helps to findall possible causes, to split causes intocategories and organize their relationships andimpact on output, and to identify opportunitiesfor improvement. In general, these categoriesare commonly known as 7 M causes:Reported benefits of implementing sixsigma:MANUFACTURING SECTOR Material; andMotorola was the first organization to use theterm six sigma in the 1980s as part of its qualityperformance measurement and improvementprogram. Six sigma has since beensuccessfully applied in other manufacturingorganizations such as General Electric,Boeing, DuPont, Toshiba, Seagate, AlliedSignal, Kodak, Honeywell, Texas Instruments,Sony, etc. The reported benefits and savingsare composed and presented frominvestigating various literatures in six sigma. Mother Nature - environment.FINANCIAL SECTORHISTOGRAMIn recent years, finance and credit departmentare pressured to reduce cash collection cycletime and variation in collection performanceto remain competitive. Typical six sigmaprojects in financial institutions include improving accuracy of allocation of cash to reducebank charges, automatic payments, improvingaccuracy of reporting, reducing documentarycredits defects, reducing check collectiondefects, and reducing variation in collectorperformance . Man -people, job; Methods and mechanics, process; Machine – machines, equipment; Measurement; Management - system of organization andmanagement;Histogram is a perfect tool for visualization ofthe frequency of the watched phenomenon inprocess. It is a bar chart made from number ofcategories, showing their splitting. Customertolerance can be added (LSL, USL) to watchedprocess.PARETO DIAGRAMPareto diagram is a bar chart for discrete data,indicating the frequency of non digital data.These categories are arranged in descendingorder. The tool that allows determining theimpact of input factors to an endpoint.Bank of America (BOA) is one of thepioneers in adopting and implementing sixsigma concepts to stream-line operations,attract and retain customers, and createcompetitiveness over credit unions. It hashundreds of six sigma projects in areas ofcross-selling, deposits, and problemresolution. BOA reported a 10.4% increase incustomer satisfaction and 24% decrease inDMAICIt is the common option for the model ofimproving the process based on Deming’scircle Plan-Do-Check-Act (PDCA). DMAIC isin the Six Sigma methodology being used as367
Int. J. Mech. Eng. & Rob. Res. 2013Suryakant Sharma et al., 2013customer problems after implementing sixsigma . American Express applied six sigmaprinciples to improve external vendorprocesses, and eliminate non-receivedrenewal credit cards. The result showed animproved sigma level of 0.3 in each case.Other financial institutions including, GECapital Corp, JP Morgan Chase, and SunTrustBanks are using six sigma to focus on andimprove customer requirements andsatisfaction .world, reported savings of 200 mn with aninvestment of 30 mn in its six sigma programto identify and prevent rework and defects ineverything from design to construction to ontime delivery of employee payroll. For example,six sigma was implemented to streamline theprocess of neutralizing chemical agents, andin a national telecommunications project tohelp optimize the management of cost andschedules .HEALTHCARE SECTORRESEARCH ANDDEVELOPMENT SECTORSix sigma principles and the healthcare sectorare very well matched because of thehealthcare nature of zero tolerance formistakes and potential for reducing medicalerrors. Some of the successfully implementedsix sigma projects include improving timely andaccurate claims reimbursement, streamliningthe process of healthcare delivery, andreducing the inventory of surgical equipmentand related costs .The objectives of implementing six sigma inR&D organizations are to reduce cost,increase speed to market, and improve R&Dprocesses. To measure the effectiveness ofsix sigma, organizations need to focus on datadriven reviews, improved project success rate,and integration of R&D into regular workprocesses. One survey noted that as of 2003only 37% of the respondents had formallyimplemented six sigma principles in their R&Dorganization reported that the developmentand manufacturing of the new prototype at WR Grace (Refining Industry) was cut to 8-9months from 11-12 months by implementingThe radiology film library at the Universityof Texas MD Anderson Cancer Center alsoadopted six sigma and improved serviceactivities greatly .Also in the same institution’soutpatient CT exam lab, patient preparationtimes were reduced from 45 min to less than5 min in many cases and there was a 45%increase in examinations with no additionalmachines or shifts .Figure 4: Advantages of ApplyingSix Sigma in R&D ProjectsENGINEERING ANDCONSTRUCTION SECTORIn 2002, Bechtel Corporation, one of the largestengineering and construction companies in the368
Int. J. Mech. Eng. & Rob. Res. 2013Suryakant Sharma et al., 2013the DFSS process. Figure 4 shows theconceptual benefits and improvement ofimplementing six sigma in R&D projects.integrate six sigma with other existinginnovative management practices that havebeen around to make six sigma method evenmore attractive to different organizations thatmight have not started or fully implemented thesix sigma method. Integrating and comparingprinciples and characteristics of six sigma withTotal Quality Management, Human ResourceFunctions, Lean Production, ISO 9000 , ISO9001, the capability maturity model are all partof the quality community’s effort to maximizethe positive effect of the six sigma method.FUTURE OF SIX SIGMASix sigma is likely to remain as one of the keyinitiatives to improve the managementprocess than just being remembered as oneof the fads. The primary focus should be onimproving overall management performance,not just pinpointing and counting defects.Researchers and practitioners are trying toTable 1: Reported Benefits and Savings From Six Sigma in Manufacturing sMotorola (1992)In-process defect levels150 times reductionRaytheon/aircraft integration systemsDepot maintenance inspection timeReduced 88% as measuredin daysGE/Railcar leasing businessTurnaround time at repair shops62% reductionAllied signal (Honeywell)/laminatesplant in South CarolinaCapacity Cycle time InventoryOn-time deliveryUp 50% Down 50% Down50% Increased to near 100%Allied signal (Honeywell)/bendix IQbrake padsConcept-to-shipment cycle timeReduced from 18 months to8 monthsHughes aircraft’s missiles systemsgroup/wave soldering operationsQuality/productivityImproved 1,000%/improved 500%General electricFinancial 2 billion in 1999Motorola (1999)Financial 15 billion over 11 yearsDow chemical/rail delivery projectexpendituresFinancialSavings of 2.45 million in capitalDuPont/Yerkes plant in New York (2000)FinancialSavings of more than 25 millionTelefonica de espana (2001)FinancialSavings and increases in revenue30 million euro in the first 10 monthsTexas instrumentsFinancial 600 millionJohnson and JohnsonFinancial 500 millionHoneywellFinancial 1.2 billion369
Int. J. Mech. Eng. & Rob. Res. 2013Suryakant Sharma et al., 2013CONCLUSIONDecisions in Imaging Economics, Vol.13, No. 7.The fundamental idea of six sigma is that ifperformance is improved, quality, capacity,cycle time, inventory levels, and other keyfactors as reduction waste, energy sourcesand environment will also improve. Thus, whenthese factors are improved, both the providerand the customer experience greatersatisfaction in performing businesstransactions.6. Ettinger W (2001), “Six sigma adaptingGE’s lesson to health care”, Trustee, Vol.54, No. 8, pp. 10-16.7. General Electric (2004), What is sixsigma: the roadmap to customer impact.Available online via February 27, 2004.Successful implementation and growingorganizational interest in six sigma methodhave been exploding in the last few years. It israpidly becoming a major driving force formany technology-driven, project-drivenorganizations. Factors influencing successfulsix sigma projects include managementinvolvement and organizational commitment,project management and control skills, culturalchange, and continuous training.8. Hahn G H, Hill W, Hoerl R W and ZinkgrafS A (1999), “The impact of six sigmaimprovement: a glimpse into the future ofstatistics”, The American Statistician,Vol. 53, pp. 1-8.9. Hammer M, Goding J (2001), “Putting sixsigma in prospective”, Quality, Vol. 40,No. 10, pp. 58-62.10. Samuelson P A and Nordhaus W D(2000), Economy. Bratislava, ISBN 808044-059-XREFERENCES1. Young Hoon Kwak and Frank T Anbari(2006), “Benefits, obstacles, and futureof six sigma approach,” Technovation,Vol. 26.11. Sauer P, Livingston M (2003),Environmental economy and ecologypolice, Prague: 1996, 203 p. ISBN 80902168-0-32. Nonthaleerak and, Hendry L C (2006),“Six Sigma: literature review and keyfuture research areas,” Int. J. Six Sigmaand Competitive Advantage, Vol. 2.12. KozÁkovÁ ZELEÒÁK F (2007), Wastesand their disposal. Košice: WILLCOM,2007. 125 p. ISBN 978-80-8073-849-5.3. James E Brady and Theodore T Allen(2006), “Six Sigma Literature: A Reviewand Agenda for Future Research,”Quality and Reliability EngineeringInternational, Vol. 22.13. Králiková R and Paulíková A (2008),“Modelling and diagnosing of mechanicalengineering life cycle productionprocess”, In Chemické listy, 2008, Vol.102. ISSN 0009-27704. Tennant G (2001), Six Sigma: SPC andTQM in Manufacturing and Services,Hampshire: Gower Publishing Company.14. The RIGHT source for Six Sigma learningand application. [on-line] Available on URL: http://benchmark.groupsite.com/discussion [cit.: 2011-01-19]5. Elsberry R B (2000), “Six sigma: applyinga corporate model to radiology”,370
Six Sigma is an approach that improves quality by analyzing data with statistics. In recent years there has been a significant increase in the use and development of the Six Sigma Approach This paper reviews some related