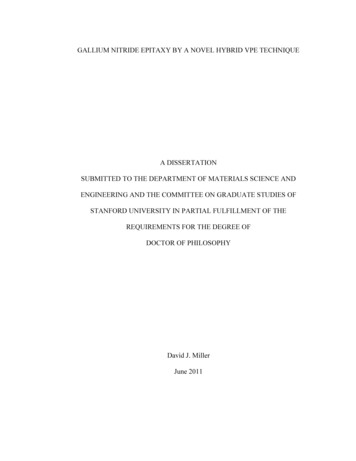
Transcription
GALLIUM NITRIDE EPITAXY BY A NOVEL HYBRID VPE TECHNIQUEA DISSERTATIONSUBMITTED TO THE DEPARTMENT OF MATERIALS SCIENCE ANDENGINEERING AND THE COMMITTEE ON GRADUATE STUDIES OFSTANFORD UNIVERSITY IN PARTIAL FULFILLMENT OF THEREQUIREMENTS FOR THE DEGREE OFDOCTOR OF PHILOSOPHYDavid J. MillerJune 2011
2011 by David J. Miller. All Rights Reserved.Re-distributed by Stanford University under license with the author.This work is licensed under a Creative Commons AttributionNoncommercial 3.0 United States 3.0/us/This dissertation is online at: http://purl.stanford.edu/hz462yv9251ii
I certify that I have read this dissertation and that, in my opinion, it is fully adequatein scope and quality as a dissertation for the degree of Doctor of Philosophy.James Harris, Primary AdviserI certify that I have read this dissertation and that, in my opinion, it is fully adequatein scope and quality as a dissertation for the degree of Doctor of Philosophy.Michael McGeheeI certify that I have read this dissertation and that, in my opinion, it is fully adequatein scope and quality as a dissertation for the degree of Doctor of Philosophy.GLENN SOLOMONApproved for the Stanford University Committee on Graduate Studies.Patricia J. Gumport, Vice Provost Graduate EducationThis signature page was generated electronically upon submission of this dissertation inelectronic format. An original signed hard copy of the signature page is on file inUniversity Archives.iii
GALLIUM NITRIDE EPITAXY BY A NOVEL HYBRID VPE TECHNIQUEDavid J. Miller, Ph.D.Stanford University, 2011Advisors: Glenn S. Solomon & James S. HarrisGallium nitride is an important material for the production of next-generationvisible and near-UV optical devices, as well as for high temperature electronicamplifiers and circuits; however there has been no bulk method for the production ofGaN substrates for device layer growth.Instead, thick GaN layers areheteroepitaxially deposited onto non-native substrates (usually sapphire) by one of twovapor phase epitaxy (VPE) techniques: MOVPE (metalorganic VPE) or HVPE(hydride VPE). Each method has its strengths and weaknesses: MOVPE has precisegrowth rate and layer thickness control but it is slow and expensive; HVPE is a lowcost method for high rate deposition of thick GaN, but it lacks the precise control andheterojunction layer growth required for device structures. Because of the large (14%)lattice mismatch, GaN grown on sapphire requires the prior deposition of a lowtemperature MOVPE nucleation layer using a second growth process in a separatedeposition system. Here we present a novel hybrid VPE system incorporatingelements of both techniques, allowing MOVPE and HVPE in a single growth run. Inthis way, a thick GaN layer can be produced directly on sapphire. GaN growthcommences as small (50-100 nm diameter) coherent strained 3-dimensional islandswhich coalesce into a continuous film, after which 2-dimensional layer growthcommences. The coalescence of islands imparts significant stress into the growingfilm, which increases with the film thickness until catastrophic breakage occurs, insitu. Additionally, the mismatch in thermal expansion rates induces compressivestress upon cooling from the growth temperature of 1025ºC. We demonstrate agrowth technique that mitigates these stresses, by using a 2-step growth sequence: aninitial high growth rate step resulting in a pitted but relaxed film, followed by a lowgrowth rate smoothing layer. As a result, thick ( 50 µm) and freestanding films havebeen grown successfully. X-ray rocking curve linewidth of 105 arcseconds and 10KPL indicating no “yellow” emission indicate that the material quality is higher thanthat produced by conventional MOVPE. By further modifying the hybrid system toinclude a metallic Mn source, it is possible to grow a doped semi-insulating GaNtemplate for use in high frequency electronics devices.iv
Acknowledgements:First and foremost, I would like to thank my advisors Glenn Solomon andJames Harris for their constant support and encouragement to finish. My parentsBarry and Barbara Miller were instrumental in helping me finally attain this goal, andI am grateful for their love and maintaining their faith in me over the years.Additional thanks go to Julie Tell who helped me prepare for my thesis defense andJody Seltzer who effectively motivated me to put forth the effort to write thisdissertation.The research for this dissertation was done at CBL Technologies, Inc. inRedwood City, CA. I would like to thank Glenn again for his role as CEO anddirector of the company in helping me define and shape this project. Our company’stechnicians Randy Carston and Rodney Worth greatly assisted me in performingnumerous crystal growth runs and constant system maintenance. The MatsushitaElectric Company of Japan gave generous financial support in the form of a jointdevelopment agreement with CBL and provided Tetsuzo Ueda and Tadao Hashimoto,two outstanding engineers who served in numerous roles at our facility. Finally, Iwould like to thank Manfred Ramsteiner, Oliver Brandt, Achim Trampert, and KlausPloog at the Paul Drude Institute for Solid State Electronics in Berlin for theirmicrostructural and optical characterization of our GaN material.v
Table of ContentsChapter 1: The Need for Gallium Nitride Substrates . 11.1 Introduction . 11.2 Properties of GaN, AlN and InN . 6Chapter 2: A New Hybrid VPE Method for GaN . 92.1 Towards a gallium nitride substrate . 92.2 Substrates for GaN heteroepitaxial growth . 142.2.1 Silicon . 142.2.2 Silicon carbide . 162.2.3 Sapphire . 162.2.4 Lithium gallate. 172.3 Summary of heteroepitaxial substrate choices . 172.4 Vapor-phase epitaxy of GaN . 192.4.1 MOVPE . 192.4.2 HVPE . 222.4.3 Hot and Cold Walled Reactors . 262.4.4 Near-equilibrium vs. far from equilibrium processes. 282.4.5 Low Temperature Nucleation layer . 302.4.6 The Hybrid VPE system . 33Chapter 3: Hybrid MOVPE/HVPE GaN process optimization . 353.1 Stress in heteroepitaxial GaN . 353.1.1 Lattice mismatch stress. 363.1.2 Coalescence stress in GaN on sapphire . 383.1.3 Thermal mismatch stress . 403.2 Effects of stress. 423.2.1 Cracking . 433.2.2 Peeling and delamination . 473.3 The surface morphology of HVPE GaN films . 483.3.1 Hillocks. 493.3.2 Pits . 523.3.3 Hexagonal pits . 533.3.4 Irregular pits . 593.3.5 Quantifiable roughness measurement. 613.4 Effects of substrate temperature, growth rate and V/III ratio . 643.5 smoothing layer growth . 673.6 The 2-step growth process . 70vi
3.7 Summary of GaN deposition process optimization techniques . 72Chapter 4: Microstructural Characterization of VPE-grown GaN . 744.1 Structure of thin GaN layers . 744.2 A 3-zone layered growth model . 774.3 Structural improvement with increasing thickness. 794.4 X-ray methods for determining approximate dislocation density . 804.41 Accounting for the effect of bowing on XRD linewidth . 814.4.2 The relationship between FWHM and dislocation density . 844.43 Reduction in the dislocation density with increased thickness . 854.5 Summary of microstructural characterization . 88Chapter 5: Photoluminescence characterization . 905.1 Photoluminescence characterization of GaN. 905.1 10K Photoluminescence . 905.1.2 Photoluminescence setup. 925.2 Photoluminescence characterization of a 12 µm sample. 935.3 Photoluminescence of 28 micron layer . 955.4 Emission from Freestanding 60 µm GaN . 965.5 Two-electron transitions . 975.6 Summary of photoluminescence results . 98Chapter 6: A semi-insulating GaN Alloy: GaMnN . 1006.1 Semi-insulating GaN for use in microwave amplifiers . 1006.2 Semi-insulating GaN through the incorporation of Mn using HVPE . 1016.3 Initial Characterization of GaMnN . 1046.4 TEM analysis: a second phase and a new crystal structure . 1076.4.1 Mn-rich second phase in GaMnN. 1086.4.2 Sublattice ordering – a new crystal structure . 1106.5 Summary: semi-insulating GaMnN . 112Chapter 7: Conclusions and future directions . 1147.1 Conclusions . 1147.2 Future directions and research . 116Chapter 8: List of References . 118vii
List of TablesTable 1.1. Room temperature band gap and lattice constants for GaN, InN andAlN . 7Table 2.1. A comparison of lattice and thermal mismatch, chemicalcompatibility issues, and cost for GaN heteroepitaxial substrates. . 18Table 6.1. Characterization summary of 5 µm thick GaMnN layers grown withvarious HCl flow ratios. . 105viii
List of FiguresFigure 2.1. Schematic diagram showing the bonding arrangement and unit cellfor GaN. . 10Figure 2.2. Bandgap vs. lattice constant for group III-nitrides . 11Figure 2.3. The Ga - N2 phase diagram. . 13Figure 2.4. Temperature variation of the thermodynamic driving force forMOVPE and HVPE. . 26Figure 2.5. Schematic diagram showing the different heating schemes used for“hot-” and “cold-” walled reactors. . 27Figure 2.6. Atomic Force Microscope images of MOVPE nucleation layerbefore and after recrystallization. . 32Figure 2.7. Model of a novel hybrid MOVPE/HVPE deposition systemfeaturing hot-walled and cold-walled heating systems. . 34Figure 3.1. A schematic drawing of a GaN (0001) unit cell overlaid onto the(0001) sapphire unit cell. . 37Figure 3.2. A schematic representation of the evolution of coalescence stress inheteroepitaxial GaN on sapphire. . 40Figure 3.3.Illustration of the effects of the 33% mismatch in thermalexpansion coefficient between sapphire and GaN. 41Figure 3.4. A comparison of tensile and compressive stress crackingmechanisms. . 45ix
Figure 3.5. Plan-view micrograph of a 10 µm thick GaN film that has crackedand buckled during the cool down process. 46Figure 3.6. 100x optical micrograph of a 2 µm film grown at 1050ºC, showingpresence of numerous hexagonal hillock-shaped prominences. 50Figure 3.7. Cross-section optical micrograph of a hexagonal-shaped pit in a 24µm HVPE GaN film. . 53Figure 3.8. The basic tetrahedral bonding arrangement between Ga and Natoms in GaN. . 54Figure 3.9. The GaN unit cell as viewed along the [1010] azimuth. . 55Figure 3.10.Schematic diagram of the distortion of hexagonal pits as amechanism for strain relief. . 58Figure 3.11. The effect of surface thermal pretreatment prior to deposition ofthe low temperature MOVPE layer. . 61Figure 3.12. Plan-view and cross-sectional micrographs of pitted and smoothHVPE GaN films. . 63Figure 3.13.The effect of substrate temperature on resulting surfacemorphology of 2 µm HVPE films. . 65Figure 3.14. The effect of the growth rate on 2 µm thick HVPE GaN filmsgrown at 1025ºC. . 65Figure 3.15. The effect of the V/III ratio on the surface morphology of 2 µmHVPE GaN films grown at 1025ºC. . 66Figure 3.16. The effect of smoothing layer regrowth on a pitted film. . 68x
Figure 3.17. The two-step growth process to achieve GaN film thickness inexcess of 15 µm. . 70Figure 3.18. 500x cross-sectional optical micrograph of a 40 µm film grown bythe 2-step method, with comb overlay showing thickness variation. . 71Figure 4.1. High-resolution X–ray diffraction (XRD) ω-scan of a 1.5 µm thickGaN film . 75Figure 4.2. High resolution (0002) XRD Gaussian curve fits to the data shownin Figure 4.1. 76Figure 4.3. Schematic and TEM bright field image of the three-zone GaNgrowth on a sapphire substrate. . 78Figure 4.4. Mosaic of images of a series of TEM micrographs taken of a 12 µmthick hybrid VPE-grown GaN film. . 79Figure 4.5. Schematic diagram of the X-ray diffraction geometry for a bowedsubstrate with bending radius r. . 81Figure 4.6. The variation in full-width half maximum (FWHM) X-raydiffraction linewidth with X-ray source slit width for a 12 µm thick GaN layer onsapphire. 83Figure 4.7. The variation of the square of the magnitude of the zero-slitextrapolation FWHM with GaN layer thickness. . 86Figure 5.1. The calculated band structure around the Γ point in wurtzite GaN. 91Figure 5.2. 10K PL spectra of a 12 µm thick HVPE-grown GaN film. . 93Figure 5.3. 10K PL spectrum of a 28 µm thick HVPE GaN layer. . 95xi
Figure 5.4. 10K PL spectra from a piece of 60 µm freestanding GaN. . 96Figure 6.1. Schematic diagram of the Ga(Mn)N deposition system. . 102Figure 6.2. The calculated MnCl2 vapor pressure as a function of temperature. 103Figure 6.3. The linear relationship between the ratio of HCl flow over Mn toHCl flow over Ga and the resulting GaMnN film’s Mn content . 104Figure 6.4. Plan-view 500x optical micrographs of 5 µm thick GaN andGaMnN alloys. . 106Figure 6.5. The relationship between ω-scan rocking curve FWHM and Mnconcentration in 5 µm thick GaMnN HVPE films. . 107Figure 6.6. Transmission-electron microscopy (TEM) images of a GaMnNsample with estimated 0.16% Mn. . 108Figure 6.7. Energy Dispersive X-ray (EDX) analysis on a TEM sample ofGaMnN . 109Figure 6.8. High resolution TEM image of GaMnN deposited on GaN onsapphire. 111xii
Chapter 1:The Need for Gallium Nitride Substrates1.1 IntroductionWithin the last twenty years, applications using gallium nitride (GaN) haveevolved from use as an obscure industrial ceramic into an economically significantsemiconductor. At room temperature GaN has a direct electronic bandgap in the nearultraviolet (360 nm or 3.4 eV), and it can be alloyed with the smaller-gap indiumnitride (InN) or the larger-gap aluminum nitride (AlN) to produce a material capableof emitting or absorbing light from the infrared part of the spectrum through the midultraviolet. In addition to its direct bandgap, GaN also has a moderate intrinsic carrierconcentration and strong resistance to thermal and radiation degradation, propertieswhich potentially have use in a wide range of applications. These include high power,high frequency, low noise microwave amplifiers for avionics and communicationssystems, LEDs that can be made to emit from red to ultraviolet, useful in videodisplays for computers, televisions and the solid-state white lighting industry, the bluelasers used in HD DVD storage systems, and solid-state detectors for ultravioletradiation, including water purification and the militarily significant solar-blind regionof the spectrum (4-6 eV).While the promise of GaN-based materials is great, there remain significanttechnical challenges that must be remedied before this materials system can be fullycommercialized. Specifically, there are currently no native substrates of moderate size( 2”) available for device layer growth. Bulk methods for GaN growth are stillsomewhat experimental and difficult to reproduce on an industrial scale; this results in1
the necessity for heteroepitaxial growth methods to deposit layers that simulate anative substrate. Often, it is desirable to fabricate a freestanding GaN layer – one thathas been removed from the heteroepitaxial substrate – especially in circumstanceswhere features such as backside electrical contact or effective heat sinking for highpower devices are necessary. In other cases when a thick heteroepitaxial layer willsuffice, it may not be necessary to undergo the difficulty in creating a freestandingsubstrate. This is often the case with LED production for instance, where contacts canbe fabricated on the top surface only; but even here, using a thick doped buffer layercould serve the dual purpose of improving the epitaxial quality while furnishing abottom electrical contact.Regardless of whether a layer is freestanding or not, heteroepitaxially grownGaN layers have high defect densities, primarily in the form of threading dislocationsoriginating at the heteroepitaxial interface. These defects can have damaging effectson devices, by reducing the luminescence efficiency for LEDs and laser diodes,increasing noise and leakage current in high frequency amplifiers, and increasing theseries resistance, leading to excessive heat generation and early device failure. It haslong been known that thicker heteroepitaxial layers can have reduced defect densities,owing to the effects of defect entanglement and annihilation as the film is grown.Thus, the need for a thick GaN layer is driven not just from the desire for improvedheat sinking, and backside contacts, but also for the general improvement of all sortsof electronic and optical devices gained by using a lower-defect density substratelayer.2
In this dissertation, I will present a novel, robust and economical method forproducing thick high quality low defect density heteroepitaxial GaN films for use assubstrates for subsequent device layer growth.This new method combines twopreviously incompatible growth techniques, hydride vapor phase epitaxy (HVPE) andmetalorganic vapor phase epitaxy (MOVPE) into a single growth system. This allowsfor the first time the direct growth without interruption of thick (greater than 20 µm)GaN layers onto a heteroepitaxial substrate by using MOVPE to provide the bufferlayer and HVPE for the rapid growth of high quality material. I will demonstrate thatthe quality of the GaN grown is extremely high, with low levels of impurityincorporation, improved dislocation density, and fine detail structure observed in thephotoluminescence spectra. In the subsequent chapters I will address aspects of thisnew growth technique, from the fundamentals of the two growth methods, effects ofthe growth parameters on film quality, material characterization, and further systemmodifications that resulted in the first recorded HVPE growth of semi-insulating GaN.In chapter 2, I will describe the current state of the art of GaN growth,comparing and contrasting the chemistry and thermodynamics of HVPE and MOVPEgrowth. Put briefly, until now the methods have been incompatible because theyrelied on entirely different substrate heating methods; HVPE has always relied on anexternal heater (hot wall system) while MOVPE has always utilized internal heating(cold wall system). I will describe the physical and chemical reasons why this is so,and present the hybrid HVPE system that incorporates an internal heating scheme toallow MOVPE in the same growth chamber.3
Chapter 3 provides details on the optimization of the hybrid VPE growthprocess. To do this, I will discuss the gross film quality metrics required for a devicequality substrate, specifically the surface morphology and its effects on film stress andcracking. The origins of stress in heteroepitaxially grown GaN will be described, fromthe effects of island coalescence, to lattice mismatch, to differences in the thermalcoefficient of expansion between the heterosubstrate and the GaN film. Growthparameters such as temperature, growth rate, type of surface pretreatment, and ratio ofgroup V to group III species (V/III ratio) all have their effect on film quality, andfinding the optimum combination to maximize surface flatness, minimize stresses toprevent cracking, while growing sufficiently thick films to have reduced dislocationdensity is a complex problem. I will show that a thermal surface pre-cleaning step iscritical for obtaining high quality deposition, and that high growth rates yield lowstress films with rough pitted morphology, while low growth rates produce smoothfilms that are stressed and frequently crack. Using the two growth regimes, by firstgrowing a pitted high rate layer followed by a smoothing low rate layer, producesthick smooth layers of good quality with manageable residual stress. Smoothing layergrowth over a pitted layer may be done at any time, immediately after deposition ofthe pitted layer or in a second growth operation following heterosubstrate removal.In chapter 4 the microstructure of the hybrid MOVPE-HVPE films arecharacterized using X-ray diffraction (XRD) and transmission-electron microscopy(TEM). I will show that the film evolves as it grows away from the interface in threeroughly defined zones: interfacial, transition, and bulk. In the interfacial zone themicrocrystalline islands coalesce and the disorder is greatest at their grain boundaries.4
In the transition zone, the material rapidly becomes more ordered, from highlyoriented polycrystalline to a single crystal, leading to the onset of the bulk zone wherethreading dislocations continue to entangle and annihilate. The correlation betweenthreading dislocation density and X-ray rocking curve linewidth will be discussed, andI will show that there is a quantifiable improvement as film thickness increases out to50 µm and beyond.The optical properties of as-grown and freestanding GaN are characterized viaphotoluminescence in Chapter 5.I will show that the material quality is very goodwith no mid-gap yellow luminescence and the near band-edge luminescence isdominated by donor-bound and free exciton emission profiles. The narrow spectrallines show that the material is highly uniform and with a relatively low donorconcentration.By adding manganese (Mn), a mid-gap dopant, to the hybrid growth system itis possible to produce for the first time semi-insulating GaN. In Chapter 6, I willdemonstrate how I have done this, and how the growth parameters affect theincorporation of the Mn into the GaN. From X-ray and TEM characterization results,I will show that at low levels (less than 0.1%) the Mn is incorporated as alternatingMn-rich and Mn-poor crystal planes in the growth direction. As the Mn concentrationincreases, phase segregation occurs and MnN crystallites are observed.Finally, I will summarize and present my conclusions in Chapter 7. I will offersuggestions for further areas of research and development for this new hybrid growthtechnique, including proposing system modifications and improvements to allow forthe production of thick alloy layers, as well as high-temperature MOVPE growth. In5
this way it may be possible to produce a complete device structure, from nucleationlayer to thick GaN (or alloy) HVPE buffer to the final MOVPE device layers all in asingle growth system at one time.1.2 Properties of GaN, AlN and InNGaN occurs in two polytypes, hexagonal (wurtzite) and cubic (zincblende). Ofthe two forms, hexagonal is the more stable version and is most commonly used forsemiconductor devices.1Unlike cubic materials with a single lattice constant, thewurtzite structure has two lattice constants: an “a” lattice constant associated with thespacing within the (0001) basal plane, and a “c” lattice constant associated with theunit cell spacing normal to the (0001) plane (along the [0001] crystal direction). Atroom temperature, GaN has the lattice constants a 3.189 Å and c 5.185 Å.Hexagonal GaN has a room temperature band gap of 3.43 eV, corresponding toa wavelength of 361 nm, in the near ultraviolet part of the spectrum. As with the III-Varsenide system, GaN can be alloyed with InN (bandgap 0.75 eV) and AlN (bandgap6.2 eV) to produce direct-gap alloys with an emission spectra ranging from theultraviolet to infrared, although the issue of lattice mismatch between relatedcompounds is more severe with nitrides than for arsenides (see Table 1.1 below,comparing the band gap and lattice constants for the group-III nit
growth technique that mitigates these stresses, by using a 2-step growth sequence: an initial high growth rate step resulting in a pitted but relaxed film, followed by a low growth rate smoothing layer. As a result, thick ( 50 µm) and freestanding films have been grown successfully