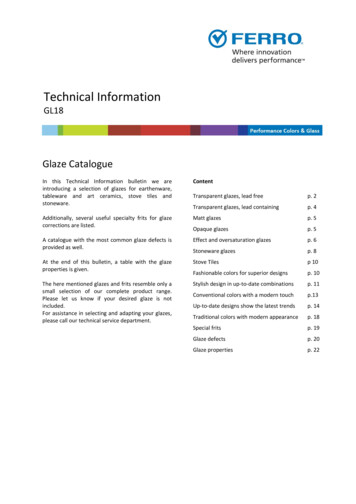
Transcription
Technical InformationGL18Performance Colors and GlassGlaze CatalogueIn this Technical Information bulletin we areintroducing a selection of glazes for earthenware,tableware and art ceramics, stove tiles andstoneware.Additionally, several useful specialty frits for glazecorrections are listed.A catalogue with the most common glaze defects isprovided as well.At the end of this bulletin, a table with the glazeproperties is given.The here mentioned glazes and frits resemble only asmall selection of our complete product range.Please let us know if your desired glaze is notincluded.For assistance in selecting and adapting your glazes,please call our technical service department.ContentTransparent glazes, lead freep. 2Transparent glazes, lead containingp. 4Matt glazesp. 5Opaque glazesp. 5Effect and oversaturation glazesp. 6Stoneware glazesp. 8Stove Tilesp 10Fashionable colors for superior designsp. 10Stylish design in up‐to‐date combinationsp. 11Conventional colors with a modern touchp.13Up‐to‐date designs show the latest trendsp. 14Traditional colors with modern appearancep. 18Special fritsp. 19Glaze defectsp. 20Glaze propertiesp. 22
page 2/22Transparent Glazes, Lead FreeVTR 40 539 Ftransparent, glossytemperature range: 1040 to 1100 CThe glaze VTR 40 539 F is a universally suitable glaze forearthenware, tableware and art ceramics.It develops colors well, including pink stains (CaSnSiCr) andinclusion pigments, also with coloring oxides. Granulated glazesand stains can be stirred in.Interesting crystalline eliminations can be achieved with theaddition of 248 030 (0.6 to 2.0 g for 100 g of glaze).VTR 166transparent, glossytemperature range: 1040 to 1100 CThe glaze VTR 166 is an economic alternative to the glaze VTR 40539 F, but more viscous.It shows a good development of colors as well with almost allstains and inclusion pigments, but only limited with cobaltaluminate blue and not with pink (CaSnSiCr).Specialty: together with the glaze 40 660 F or the frit 90 710,good results are obtained for the inclusion pigments 270 547 and270 548.VTR 320transparent, glossyespecially low temperature range: 920 to 980 CThe color development of this glaze is good, although at 920 C itreaches its limits.The glaze VTR 320 is only partially suitable for the inclusionpigments 270 547 and 270 548. Pink stains (CaSnSiCr) turnbrown.
page 3/22VTR 102transparent, glossytemperature range: 980 to 1070 CThe glaze VTR 102 is a soft glaze for earthenware, tableware andart ceramics. It can be blended especially well with the glazeVTR 166, with a recommended ratio of 30:70.The color development is excellent with all stains, especially inthe low temperature range.VTR 102 is recommended for pink stains (CaSnSiCr). It is notsuitable for CoAl blue and has only limited suitability for cobaltsilicate blue and the inclusion pigments 270 547 and 270 548.VTR 40 271 TMtransparent, glossytemperature range: 1060 to 1100 CThe glaze VTR 40 271 TM is the best choice for pink stains. It issuitable for earthenware, tableware and stove tiles.The color development of stains is good, but not with coloringoxides.Specialty: The addition of 6 to 8 g alumina to 100 g of glazeresults in a matt glaze that may be colored with all kinds ofstains.
page 4/22Transparent Glazes, Lead ContainingVTR 40 134 Ftransparent, glossyPbO 39 weight %temperature range: 950 to 1040 CThe glaze VTR 40 134 F isa typical glaze for pink stains. It can beeasily colored with stains, especially with pink (CaSnSiCr).VTR 40 134 F is a perfect choice in underglaze painting.VTR 17transparent, glossyPbO 43 weight %temperature range: 950 to 1040 CThe glaze VTR 17 is usable for art ceramics and stove tiles,especially for raw bodies.It may be colored with stains and oxides, but not with pink(CaSnSiCr).The color development in a gas kiln is better than in the electricalkiln.VTR 39transparent, glossyPbO 2 weight %temperature range: 980 to 1020 CThe glaze VTR 39 is suitable for earthenware and art ceramics.It may be colored with stains, except with pink.VTR 40 5245 Ftransparent, glossyPbO 14 weight %temperature range: 1040 to 1080 CThe glaze VTR 40 5245 F is universally suitable transparent glazefor earthenware, art ceramics and stove tiles.It is especially suitable for raw bodies in gas kilns. With stains andcoloring oxides it shows a good color development. Granulatedglazes and stains may be stirred in.
page 5/22Matt GlazesVTR 40 525 Fmatt, colorless, lead freetemperature range: 1020 to 1100 CThe glaze 40 525 F is a universally suitable matt glaze forearthenware, tableware, art ceramics and stove tiles.It develops color stains nicely, even pink (CaSnSiCr) and allinclusion pigments. Additionally, granulated glazes and stainsmay be used.In the upper temperature range (1080 to 1120 C) the surface issilk‐matt.Specialty: the addition of 15 % zircon silicate results in a smooth,white matt surface.VTR 40 545 TMcolorless, silk‐matt, lead freetemperature range: 1020 to 1080 CThe glaze 40 545 TM is a matt basic glaze for effect‐buildingcomponents, suitable for earthenware, art ceramics and stovetiles.It is perfect for color stains.Interesting oversaturation effects are created by the addition ofall kinds of granulated glazes, stains and frits. These effects areenhanced by additions of 248 030, 238 512 or 298 026.Opaque GlazesVBC 13opaque, glossy, lead freetemperature range: 980 to 1060 CThe glaze VBC 13 is suitable for earthenware, tableware and artceramics.It fires well on raw bodies in gas kilns.At firing temperatures higher than 1020 C it may be used formajolica painting.
page 6/22Effect and Oversaturation GlazesVBC 43 554 TMbeige, silk‐matt, low degree of crystalline eliminations,lead freetemperature range: 1020 to 1140 CThe glaze VBC 43 554 TM is ideal for earthenware, stove tiles andart ceramics.It can be colored with stains and is suitable for granulates.The addition of 248 030 and 298 026 enhances the effects.VBC 43 556 TFbeige, slight silk‐matt effects, lead freetemperature range: 1020 to 1080 CThe glaze VBC 43 556 TF is a versatile earthenware glaze, idealalso for stove tiles.The coloring with stains is limited, but the coloring with frits andoxides is possible.The addition of all kinds of granitis enhances the oversaturationeffects. 248 030, 238 512 and/or 298 026 also show interestingeffects.Specialty: the use of a base glaze 43 556 TF, colored with stains,together with a top glaze of VTR 166 with 40 660 F or of 40 539F, also colored with oxides, creates a very interestingappearance.Example 1Base glaze:43 556 TF240 9421008Top glaze:VTR 16640 660 TF270 54870308The red is very similar to a selenium red, but this special effectcannot be achieved with a selenium glaze.Example 2Base glaze:43 556 TF220 9461005Top glaze:40 539 F270 96810015The base glaze may preferably be colored dark. The top glazemay be colored as pleases, but preferentially in contrastingcolors to the base glaze.
page 7/22Fine or strong effects are created whenusing different layer thicknesses of baseand/or top glaze. They can be adjustedindividually according to demand.
page 8/22VBC 49 872 TMopaque, silk‐matt, lead freetemperature range: 1000 to 1080 CThis is a silky‐elegant effect glaze for earthenware, stove tiles andart ceramics.The glaze is suitable for creating pastel shades by the use of colorstains.A surface refinement is achieved by the addition of 2 % 248 030.Granitis enhance the eliminations significantly.Example for a very elegant surface:49 872 TM248 030zircon silicateStir into the glaze slip:50 559 GY59 570 GY100281515
page 9/22Stoneware GlazesVTR 40 581 Etransparent, glossy, lead freetemperature range: normal firing 1190 to 1250 C, fastfiring 1260 C (4 hours)The glaze VTR 40 581 E is a versatile stoneware glaze, easy tocolor with stains, with high brilliance and perfectly suitable fortableware.The addition of granitis, like 248 030, results in nice effects.Blended with 10 % aluminium oxide, a colorless matt glaze isobtained, whereas 15 % zircon silicate create a glossy whiteglaze.Specialty: the addition of 5 to 15 % of the frit FTR 90 023 F lowerthe melting point of the glaze VTR 40 581 F to 1140 to 1180 C.CrystalsThe glaze 40 581 E as base glaze in combination with a top glazeand with 248 030 develops crystals of different sizes.Example:Base glaze:40 581 E, with zircon and stainsTop glaze:kaolin103238 495103lithium carbonate52zinc oxide, lead free52alumina31FTR 90 564 M175FTR 90 5158 M484When adding 1 to 2 % of 248 030 to the top glaze, interesting„dissolutions“ and crystalline effects are created. The addition of3 to 5 % of 248 030 to the top glaze cause the formation ofcrystals.The size and intensity of the crystals can be influenced by thequantity of 248 030 added to the top glaze and/or by the layerthickness of the top glaze. Depending on the body and on thefiring conditions, the effects have to be adjusted individually.
page 10/22VTRS 115transparent, glossy, lead freetemperature range: 1150 to 1200 CThe glaze VTRS 115 is a basic glaze for stoneware, for fired andfor raw bodies.It is well suitable for ZrSiV and ZrSiPr stains and commoninclusion pigments.VTRS 115 with raw material mixture andFTR 90 564 Mtemperature range: 1150 to 1220 CDifferent blending ratios show a fired surface from matt toglossy.Slight effects may be combined with all kinds of stains.270 547 and 270 548 develop nicely in the glossy version up to1180 C.Examples:glossy:VTRS 115FTR 90564 Mraw material mixture251758matt:VTRS 115FTR 90 564 Mraw material mixture152362strongly matt:VTRS 115FTR 90 564 Mraw material mixture51085Raw material mixture for the glaze VTRS 115:238 495zinc oxide, lead freesilicakaolincalc sparsodium feldspar99123148173210247The addition of 2 % 248 030 to the blends shows slight crystallineeliminations in the case of the glossy version and interestingeliminations in the matt versions.The exchange of the more viscous frit 90 564 with the frit11.37048.09 is possible. The eliminations are then decreased ortotally avoided. The firing temperature may then be increased to1250 C.
page 11/22Stove TilesFashionable colors for superior designsVariation 1:Brown wipedUnderglaze40 525 FZrSiO4230 967260 952260 954260 955Decorating glaze100,02,01,01,00,63,040 525 FZrSiO4250 942260 946260 952100,02,00,67,01,0sprinkle thickly and wipe with asponge immediatelyspray evenlyVariation 2:Red wipedUnderglaze40 525 F260 952270 944Decorating glaze100,04,05,0spray evenly40 525 F100,0230 9425,0260 9520,5270 9461,0sprinkle thickly and wipe with asponge immediatelyVariation 3:Dark brown wipedUnderglaze40 525 F240 942260 955Decorating glaze100,02,08,0spray evenly40 525 F100,0230 9462,0230 9672,0260 9462,0260 9520,4270 9462,0sprinkle thickly and wipe with asponge immediatelyVariation 4:Dark red wipedUnderglaze40 525 F260 952270 944Decorating glaze100,04,05,0spray evenly40 525 F100,0240 9422,0260 9558,0sprinkle thickly and wipe with asponge immediately
page 12/22Stylish design in up‐to‐date combinationsOrange in combination with chocolate brownOrangeUnderglaze; evenly sprayed40 525 F238 512SnO2ZnO 1100,06,05,07,0Stippling glaze 1Stippling glaze 240 525 F230 944230 967270 946100,05,01,01,0VTR 102100,0Chocolate brownUnderglaze; evenly sprayed40 525 FZrSiO4230 967260 952260 954260 955100,02,01,01,00,63,0Stippling glaze 140 525 F240 942260 955Stippling glaze 2100,02,08,0VTR 102100,0Yellow ‐ orange in combination with sandYellow ‐ orangeGlaze, evenly sprayed40 545 TM100,0230 9677,5270 9462,0248 0302,0248 030, only stirred inSandUnderglaze; evenlyFCM 61094100,0Decorating glaze; sprinkeled40 545 TM230 944230 967260 946100,04,01,04,0
page 13/22Rosé in combination with dark brownRosé underglaze40 525 F230 942Rosé stippling glaze100,01,540 525 F230 942260 946270 944100,02,02,01,0Dark brownUnderglaze, evenly sprayed40 525 F240 942260 955100,02,08,0Stippling glaze 140 525 FZrSiO4230 967260 952260 954260 955Stippling glaze 2100,02,01,01,00,63,0VTR 102100,0Sunny yellow in combination with blueSunny yellow underglaze40 525 F230 967Sunny yellow stippling glaze100,02,040 525 F230 967100,08,0BlueUnderglaze, evenly sprayed40 525 F220 946240 942100,05,02,0Stippling glaze 140 525 F250 946Stippling glaze 240 525 F250 946100,06,0Stippling glaze 3100,06,0VTR 102100,0
page 14/22Conventional colors with a modern touchVariation 1Black ‐ blue marbledUnderglaze, evenly sprayed40 525 F230 942100,05,0Stippling glaze 140 525 F250 946Stippling glaze 2100,06,040 525 F250 946CK‐15063100,06,00,4Variation 2Black ‐ grey marbledUnderglaze, evenly sprayed40 525 F230 942100,05,0Stippling glaze 140 525 F250 942Stippling glaze 2100,06,040 525 F250 946100,06,0
page 15/22Up‐to‐date designs show the latest trendsCombination A43 554 TM100,0230 9446,0230 9674,0270 9440,5stir into the ready to use glaze slip279 992 GR2,040 525 F100,0260 9524,0270 94410,0stir into the ready to use glaze slip43 557 GR4,047 319 GR4,0Combination B43 554 TM100,0ZrSiO410,0230 9670,6259 9690,2260 9541,0stir into the ready to use glaze slip50 559 GY5,059 570 GY5,040 525 F100,0ZrSiO45,01,2210 9603,8259 9691,6260 954stir into the ready to use glaze slip269 984 GR 12,01H phrase 412
page 16/22Combination C43 554 TM100,0ZrSiO45,0210 9600,8250 9423,0260 9522,0stir into the ready to use glaze slip50 559 GY5,059 570 GY5,040 525 F100,0270 56112,0stir into the ready to use glaze slip50 559 GY5,059 570 GY5,0Combination D43 554 TM100,0ZrSiO45,0210 9601,2259 9693,8260 9541,6stir into the ready to use glaze slip50 559 GY5,059 570 GY5,043 554 TM100,0270 56112,0stir into the ready to use glaze slip50 559 GY5,059 570 GY5,0
page 17/22Combination E43 554 TM100,0250 9466,0240 9420,2stir into the ready to use glaze slip50 559 GY5,059 570 GY5,043 554 TM100,0230 9446,0230 9674,0270 9440,5stir into the ready to use glaze slip50 559 GY5,059 570 GY5,0Combination F43 554 TM100,0250 9466,0240 9420,2stir into the ready to use glaze slip42 246 GR4,045 164 GR4,043 554 TM100,0230 9466,0230 9674,0270 9440,5stir into the ready to use glaze slip279 992 GR2,0
page 18/22Combination GFCM 61094100,0stir into the ready to use glaze slip279 992 GR2,043 554 TM100,0220 946 25,0stir into the ready to use glaze slip50 559 GY5,059 570 GY5,0Combination H43 554 TM100,0stir into the ready to use glaze slip279 992 GR2,043 554 TM100,0CK‐150636,0220 9463,0250 9462,0stir into the ready to use glaze slip42 246 GR4,045 164 GR4,0
page 19/22Traditional colors with modern appearance40 5245 FIron oxide100,04,040 5245 FCopper oxideIron oxide1100,03,01,040 5245 FCopper oxideIron oxide1100,04,01,040 5245 FIron oxideManganese oxide40 5245 FIron oxideManganese oxide40 5245 FCopper oxideIron oxideCobalt oxide40 5245 FCobalt oxide23100,02,032GHS symbol 09, H phrase 400GHS symbol 07, H phrases 302, 3323GHS symbol 08, H phrases 334, 4122100,04,03,0100,04,01,00,5140 5245 FManganese oxide12100,04,02,0100,04,0
page 20/22Special FritsFTR 90 255lead free; frit with a c.t.e. of 40 (*10‐7/K); for correction of hair cracksFTR 90 710lead free; an alternative to lead frits (up to 30 % lead); in combination with kaolin and silicasuitable as a top coat for traditional firing; for earthenware and tablewareFTR 90 427lead free; lithium frit; for correction of surface tension; causes effects and crystals; forearthenware and stonewareFTR 90 428lead free; together with the frit FTR 90 420 used as a base for effect glazes;for earthenwareFTR 90 420lead free; ZnBa frit, base for matt elimination glazes; for earthenwareFTR 90 368lead free; base for calcium containing glazes; for earthenware and tablewareFTR 90 564lead free; barium frit; to be used instead of barium silicate; causes effects; for earthenwareand stonewareFTR 90 51231lead mono silicateFTR 90 352lead containing frit with 21.0 weight‐% lead;zinc base for silk‐matt effect glazesCE119201000lead free; barium frit1GHS symbol 07, 08, 09, H phrases 302, 332, 360Df, 373, 410Glaze Defects
page 21/22Why do glaze defects occur? In the followingchapter the most common defects and hints toavoid them are given.Overfiring or UnderfiringThe most common reasons for glaze defects areunderfiring or overfiring.Underfiring causes a dry, scratchy surface. Oftenthis can be cured by a second firing at a highertemperature.Overfiring causes the glaze to flow. The glaze isthen thinner at the top and thicker at the bottom.Sometimes it even drops from the body. Stronglyoverfired ceramics may also show pinholes andpitting, if the glaze reaches its evaporationtemperature. Overfiring cannot be corrected.Differing Coefficients of Thermal ExpansionThe body and the glaze may have very differentcoefficients of thermal expansion (c.t.e.). If thec.t.e. of the glaze is too high, it might lead to theformation of cracks. If it is too low, it might causechipping.A too low c.t.e. might be adjusted by adding 2 to 7% of the frit 90 167. If the c.t.e. is too high, 5 to 10% of the frit 90 255 might correct this.Application Problems and Adhesion of theUnfired GlazeWrong application of the glaze is the reason forseveral glaze defects. A too thin application mightresult in rough surfaces and also influence theglaze color. A glaze application that is too thickpromotes running and blistering. Unevenapplication causes stains and stripes, in the coloras well as in the surface structure.Mistakes during application also influence theadhesion of the glaze to the body. The body mustbe clean and dry before the glaze is applied. If asecond glaze should be applied on top, the firstmust be dried completely before doing so.Adhesion problems often cause a rolling off of theglaze.Adhesion problems might be avoided by testingthe glaze slip before application. The weight perlitre and the viscosity should be measured.To keep the glaze slip from settling, a suspendingagent should be used. When glazing raw bodies,adhesive should always be used.Hair Cracks, Chipping and PeelingHair crack formation means the formation of anetwork of finer or thicker cracks in the fired glaze,sometimes directly after firing, sometimes later.Except in some special glazes, the formation ofcracks is not desired.There are several reasons for the formation of haircracks. Normally cracks are occuring if thecoefficient of thermal expansion of the glaze is toohigh. Due to the tension during cooling the glaze iscrazing. The addition of the frit 90 255 and/orkaolin might help.Cracks can also be caused by thermal shock due toa too fast temperature change. Longer soakingtimes and slower cooling help to avoid thesecracks. A thinner layer of glaze or the addition ofsilica to the body are also advantageous.In case of porous bodies with unglazed areas,moisture might be absorbed, which may lead to anexpansion of the body. Then the body should befired at a higher temperature or more calc sparshould be added to the body.Peeling and chipping is caused by a glaze c.t.e. thatis too low. In this case the frit 90 167 should beadded to the glaze.Firing at lower temperatures and faster coolingcould help. Perhaps also the feldspar and/or claycontent of the body may be increased.Very important is the formation of a goodintermediate layer, that means the adhesion of theglaze to the body. A good intermediate layer isable to equalize the tension between glaze andbody. Longer firing cycles and a sufficient soakingtime enhance the formation of the intermediatelayer.Rolling off or Contraction of the Glaze after FiringWhen rolling off or contracting, the glaze leavesempty areas on the body after firing.Rolling off occurs if the glaze is not sticking to thebody correctly. This might be the case if the bodywas not completely free of grease, dirt ormoisture, or if the surface of the body is toosmooth. Also a too thick layer of glaze can causeadhesion problems. Sometimes a glaze that ismilled too fine can be the reason for rolling off.Rolling off also occurs if the raw glaze was notdried long enough.Too much opacifier may also lead to rolling off.Matt glazes with a high content of clay tend torolling off, like too viscous glazes do.
page 22/22If the surface tension is too high, the glazes mightcontract to droplets. This can be cured byadditions of lithium, alkali or lead, which lower thesurface tension.Blistering and PinholesBlisters and pinholes are often formed byevaporating gas from the body or from the glazewhile melting during the firing.In most cases the outgassing process leavesenough time for the glaze to flow back and form aneven surface. If there is too much gas or the glazeis too viscous, the glaze might solidify although thegas has not evaporated completely. After firing,blisters and pinholes remain.Outgassing may have different reasons. Air in thebody is often already formed during processing ordue to the degradation of finished body material.In order to reduce air bubbles in the body, openingmaterials can be used.In the glaze, the formation of blisters is enhancedby too thick glaze layers or too high surfacetension or viscosity.Mistakes during firing also increase the formationof blisters: too high temperature, a reductive kilnatmosphere at the beginning, too short firingcycles or too short soaking times. The kiln shouldbe well ventilated at all times.Matt Stains, Glossy Areas and DiscolorationsOne can distinguish between matt areas in a glossyglaze and glossy areas in a matt glaze. Additionally,discolorations or traces on fired pieces may occur.There are several reasons for matt stains. Amongthem are inhomogenious glaze applications or toolow firing temperatures. The evaporation of fluxes,e.g. lead, during firing leaves no damage if theventilation flaps of the kiln are left open. If there isexcess water during heating, a good ventilationalso helps.Glossy areas often are caused by too thin glazelayers or temperatures that are too high. The kilnatmosphere may be improved by sufficient airsupply while heating and slow cooling.Discolorations often are formed by evaporatedmetal oxides, which were added to the glaze inpure form or as part of a color stain, e.g.chromium, copper or cobalt oxide. If theevaporation is very high without properventilation, even tiny crystals may occur. Only asufficient ventilation of the kiln may solve theproblem.
page ingtemperature Cmatttransparent glazetransparent glazetransparent glazetransparent glazetransparent glazetransparent glazetransparent glazetransparent glazetransparent glazematt glazematt glazematt glazeopaque glazeopaque glazeeffect glazeeffect glazeeffect glazestoneware glazestoneware glazeC.T.E.[10‐7/K]glossyVTR 40 539 FVTR 166VTR 320VTR 102VTR 40 271 TMVTR 40 5245 FVTR 40 134 FVTR 17VTR 39VTR 40 525 FVTR 40 545 TMFCM 61094VBC 49 7654VBC 13VBC 43 554 TMVBC 43 556 TFVBC 49 872 TM 1VTR 40 581 EVTRS 115% PbOArt ceramics/stove tilesTypeTableware/stonewareProduct no.Tableware/earthewareGlaze Propertiesxxxxxxxxxxxxxxxxxxx1040 ‐ 11001040 ‐ 1100920 ‐ 980980 ‐ 10701060 ‐ 11001040 ‐ 1080950 ‐ 1040950 ‐ 1040980 ‐ 10201020 ‐ 11001020 ‐ 10801040 ‐ 1100980 ‐ 1050980 ‐ 10601020 ‐ 11401020 ‐ 10801000 ‐ 10801190 ‐ 12601150 ‐ 12001GHS symbol 09, H phrase 411Limitation of Warranty and LiabilityFerro believes that the information contained in this document is accurate at the time of its publication. Ferro makes no warranty with respectto the information contained in this document. The information in this document is not a product specification, either in whole or in part. Youruse of the information contained in this document and your purchase and use of this Ferro product are at your sole discretion. Downstreamusers are responsible for determination of the suitability of this product and for testing in specific applications. Nothing in this document shallbe construed as a license for use that infringes upon any property rights of any third party. Please refer to the Safety Data Sheet (SDS) for safeuse, handling and disposal information. All sales by Ferro to you are subject to Ferro’s Terms and Conditions of Sale, as amended from time totime and available at www.ferro.com. In the event this document conflicts with Ferro’s Terms and Conditions of Sale, Ferro’s Terms andConditions of Sale shall control.FERRO GmbH I Gutleutstrasse 215 I Postbox 110403 I D‐60039 Frankfurt/Main GermanyP 49 6927116.0 F 049 6927116.321 E info‐pcg@ferro.com W ferro.compage 23 of 23STRF GL18 09, 2017
zinc oxide, lead free 52 alumina 31 FTR 90 564 M 175 FTR 90 5158 M 484 When adding 1 to 2 % of 248 030 to the top glaze, interesting „dissolutions“ and crystalline effects are created. The addition of 3 to 5 % of 248 030 to the top glaze cause the formation of crystals. The si