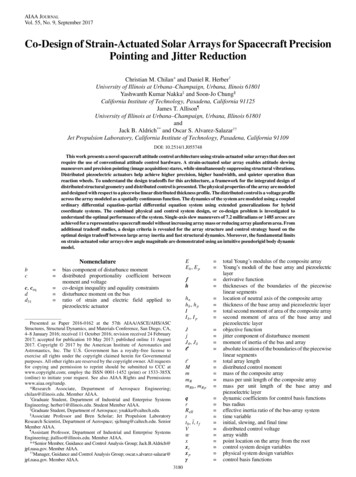
Transcription
AIAA JOURNALVol. 55, No. 9, September 2017Co-Design of Strain-Actuated Solar Arrays for Spacecraft PrecisionPointing and Jitter ReductionChristian M. Chilan and Daniel R. Herber†University of Illinois at Urbana–Champaign, Urbana, Ilinois 61801Yashwanth Kumar Nakka‡ and Soon-Jo Chung§California Institute of Technology, Pasadena, California 91125James T. Allison¶University of Illinois at Urbana–Champaign, Urbana, Illinois 61801andJack B. Aldrich** and Oscar S. Alvarez-Salazar††Jet Propulsion Laboratory, California Institute of Technology, Pasadena, California 91109DOI: 10.2514/1.J055748This work presents a novel spacecraft attitude control architecture using strain-actuated solar arrays that does notrequire the use of conventional attitude control hardware. A strain-actuated solar array enables attitude slewingmaneuvers and precision pointing (image acquisition) stares, while simultaneously suppressing structural vibrations.Distributed piezoelectric actuators help achieve higher precision, higher bandwidth, and quieter operation thanreaction wheels. To understand the design tradeoffs for this architecture, a framework for the integrated design ofdistributed structural geometry and distributed control is presented. The physical properties of the array are modeledand designed with respect to a piecewise linear distributed thickness profile. The distributed control is a voltage profileacross the array modeled as a spatially continuous function. The dynamics of the system are modeled using a coupledordinary differential equation–partial differential equation system using extended generalizations for hybridcoordinate systems. The combined physical and control system design, or co-design problem is investigated tounderstand the optimal performance of the system. Single-axis slew maneuvers of 7.2 milliradians or 1485 arcsec areachieved for a representative spacecraft model without increasing array mass or reducing array planform area. Fromadditional tradeoff studies, a design criteria is revealed for the array structure and control strategy based on theoptimal design tradeoff between large array inertia and fast structural dynamics. Moreover, the fundamental limitson strain-actuated solar arrays slew angle magnitude are demonstrated using an intuitive pseudorigid body dynamicmodel.Nomenclaturebc c, ceqdd31 bias component of disturbance momentdistributed proportionality coefficient betweenmoment and voltageco-design inequality and equality constraintsdisturbance moment on the busratio of strain and electric field applied topiezoelectric actuatorPresented as Paper 2016-0162 at the 57th AIAA/ASCE/AHS/ASCStructures, Structural Dynamics, and Materials Conference, San Diego, CA,4–8 January 2016; received 11 October 2016; revision received 24 February2017; accepted for publication 10 May 2017; published online 11 August2017. Copyright 2017 by the American Institute of Aeronautics andAstronautics, Inc. The U.S. Government has a royalty‐free license toexercise all rights under the copyright claimed herein for Governmentalpurposes. All other rights are reserved by the copyright owner. All requestsfor copying and permission to reprint should be submitted to CCC atwww.copyright.com; employ the ISSN 0001-1452 (print) or 1533-385X(online) to initiate your request. See also AIAA Rights and Permissionswww.aiaa.org/randp.*Research Associate, Department of Aerospace Engineering;chilan@illinois.edu. Member AIAA.†Graduate Student, Department of Industrial and Enterprise SystemsEngineering; herber1@illinois.edu. Student Member AIAA.‡Graduate Student, Department of Aerospace; ynakka@caltech.edu.§Associate Professor and Bren Scholar; Jet Propulsion LaboratoryResearch Scientist, Department of Aerospace; sjchung@caltech.edu. SeniorMember AIAA.¶Assistant Professor, Department of Industrial and Enterprise SystemsEngineering; jtalliso@illinois.edu. Member AIAA.**Senior Member, Guidance and Control Analysis Group; Jack.B.Aldrich@jpl.nasa.gov. Member AIAA.††Manager, Guidance and Control Analysis Group; oscar.s.alvarez-salazar@jpl.nasa.gov. Member AIAA.3180EEb , Ep fh hnhb , hpIIb , Ip JjJθ , Jδl lMmmRmRb , mRp qrRefftt0 , t , tfVwxxcxpγ total Young’s modulus of the composite arrayYoung’s moduli of the base array and piezoelectriclayerderivative functionthicknesses of the boundaries of the piecewiselinear segmentslocation of neutral axis of the composite arraythickness of the base array and piezoelectric layertotal second moment of area of the composite arraysecond moment of area of the base array andpiezoelectric layerobjective functionjitter component of disturbance momentmoment of inertia of the bus and arrayabsolute location of the boundaries of the piecewiselinear segmentstotal array lengthdistributed control momentmass of the composite arraymass per unit length of the composite arraymass per unit length of the base array andpiezoelectric layerdynamic coefficients for control basis functionsbus radiuseffective inertia ratio of the bus-array systemtime variableinitial, slewing, and final timedistributed control voltagearray widthpoint location on the array from the rootcontrol system design variablesphysical system design variablescontrol basis functions
CHILAN ET AL.δη θμξϵρb , ρpϕ array displacement angle at the rootdynamic coefficients for Galerkin approximatingfunctionsbus angledamping coefficient of the composite arraydistributed array displacement, or co-design statedistributed array straindensity of the base array and piezoelectric layerGalerkin approximating functionsI.AIntroductionDVANCEMENTS in spacecraft technology accelerate discovery in Earth and space sciences; faster reorientation and ultraquiet jitter-free operation for space observatories and optical linkshave the potential to transform the rate and quality of data obtainedfor scientific investigation [1,2]. Scientific needs drive exceptionallystringent spacecraft pointing and control requirements, which inturn demand new strategies for space vehicle design and control[3,4]. Traditionally, reaction wheel assemblies (RWAs)—momentumexchanging flywheels—have been used for attitude control but theyhave been deemed problematic for many science missions because ofRWA disturbances and reliability concerns [5]. One alternativecontrol strategy intended to overcome some of these problems usedrobotic appendages with rigid links [6]. The strategy proposed hereuses existing appendages (solar arrays) with distributed actuation toachieve high-precision attitude control. Strain-actuated solar arrays(SASAs), which employ distributed piezoelectric material actuators,provide high accuracy and bandwidth for spacecraft attitude control,thereby supporting quiet operation for high-precision scientificinstruments. Additionally, the dual use of the same spacecraftcomponent, i.e., solar arrays, for power generation and precisionattitude control reduces payload delivery costs.A unique capability of the proposed SASA pointing architecture isto perform attitude slewing maneuvers in addition to suppressingstructural vibrations. Although the current bending limit of the arraysbounds the magnitude of the attitude maneuvers to the order ofmilliradians or arc minutes, these advancements are important forhigh-precision pointing, and when combined with other actuationtechnology for large reorientations may provide a feasiblereplacement for RWAs to improve pointing accuracy and reliability.Thus, the SASA control system is proposed as part of a hierarchicalattitude control system where large-scale reorientations are carriedout by magnetorquers or microthrusters. After the pointing target hasbeen acquired, the SASA control system performs small-scalereorientations and pointing stability in the presence of jitterdisturbances.SASAs for precision pointing will require the arrays to behavemore like a flexible structure than a rigid one. Space structures bynecessity are extremely lightweight and flexible but vibrations fromRWAs, reorientation maneuvers, and other disturbances degradeperformance. These factors have given rise to the extensively studiedtopic of control–structure interaction (CSI). Most CSI literature hasconcentrated on reducing structural vibration through active damping[4,7], i.e., using control systems to actively damp lower-frequencystructural vibration modes without exciting higher-frequency modes[8–10]. This design paradigm has led to design rules, such as placingactuators according to locations of high strain for important structuralmodes [8,11]. If the design objective is different from vibrationreduction alone (e.g., more sophisticated motion control), then CSIrules may produce suboptimal results. As an illustrative example,consider Skylab, where part of the control effort goes to reducingvibration and getting flexible bodies to behave as rigid bodies,leaving only the remaining control effort for productive tasks [9].Instead of using the proxy control objective of eliminating flexiblebehavior, a more elegant solution would be to improve overall systemperformance by working with elastic dynamics rather than fightingagainst them. In the integrated design and control study presentedhere, we seek to use the flexible body dynamics to our advantage toprovide new levels of system performance. Instead of usingdistributed actuation of solar arrays to damp out vibration as the3181primary objective, it is used to control the spacecraft orientation as theprimary objective.Piezoelectric material actuators (PEMAs) [12–14] are a provensolution for distributed actuation [15,16]. Applying voltage acrossPEMAs bonded to or embedded within structures induces strain,causing the structure to deform (bend, twist, elongate, or contractdepending on design). PEMA-based intelligent structures outperform conventional point-actuated structures [4,17] in terms ofmass, fast dynamic response, and high precision [18]. Althoughpiezoelectric actuators have been used for structural active damping,they have not been used for slewing control of structures due to theirsmall stroke. The proposed SASA architecture, however, does notslew the array structure about a revolute joint, but bends it to slew thebus using conservation of angular momentum. In this way, the SASAsystem implements the novel functionality of small-scale attitudecontrol. Because there are small strain limits on array bending, thesmall PEMA stroke does not limit this application. Furthermore, theuse of piezoelectric actuators allows for quiet operation for sensitiveinstruments.The distributed actuation of intelligent structures providestremendous design flexibility. This opens up new opportunities forsystem performance, but also increases design difficulty [18,19].Although CSI has studied the problem of actuator and sensorplacement for the controls of structures [8,11], the co-design workpresented here considers not only the design of the actuator systembut also of a distributed structure for optimal active performance.Furthermore, the use of open-loop distributed control allows us toobtain insights for actuator placement and to investigate limits ofperformance.Intelligent structures are highly coupled systems, yet structural andcontrol aspects are typically designed in sequence [8,20,21],motivated by the need to simplify the design problem and to fit thestructure of existing design organizations [9]. Sequential methodscannot fully exploit synergy between structural and control design[22,23]. More recently, co-design (combined physical and controlsystem design) has been introduced as a more general methodologythat simultaneously optimizes structures and controls without theneed for major simplifying assumptions. Co-design aids engineersin treating the intelligent structure design problem in a morecomprehensive manner [22,23]. For example, co-design has beenused in the exploration of tradeoffs between plant redesign cost andsystem performance (energy consumption) in applications involvingcounterbalanced robotic manipulators [24]. Furthermore, it hasbeen shown that co-design can yield solutions with significantperformance improvements [25,26] and at lower costs than CSIiterated sequential methods [23,27,28]. This type of method typicallyperforms optimization of the design vector at one level whileperforming system analysis, i.e., finding a feasible solution, in asecond (lower) level. If the system analysis problem does not have aunique solution, the CSI iterated sequential method may converge toa suboptimal solution [28]. In contrast, nested co-design methodsmay define convex optimization problems in a second level for thecontrol design of certain systems, e.g., dynamical systems that arelinear in the states and the controls, that yield solutions that are notonly feasible but also globally optimal [23,29].In most previous co-design studies, the physical aspects of thesystem design have been managed in a very simplified manner. Forexample, physical system (plant) design decisions have often beenlimited to actuator placement [30,31]. Many co-design studies haveused simplified plant models [9,17,24,32] that do not supportexploration of changes to distributed geometric structural design,preventing full exploitation of the design synergy between structuraltailoring and distributed control system design. A more ideal codesign method supports changes to distributed structural properties(e.g., changing structural shape affects how inertial and stiffnessproperties vary spatially). Structural tailoring coupled with controldesign has long been recognized as an important, yet formidable,problem [33]. Although there are examples of tailoring passivesystem dynamics to work optimally with active control using lumpedplant stiffness, damping, and mass parameters as design variables [9],these methods cannot be extended to distributed parameter systems.
3182CHILAN ET AL.To summarize, much is known regarding the design of controlsystems and actuators for intelligent structures, but only if thestructural design is held fixed. A few examples of fully integrateddesign exist, but only with simplified treatment of structural design.Because the proposed SASA pointing architecture involves inherentdynamic coupling between control actuation and flexible structuraldynamics, it is a good case for a co-design study. In this work,distributed geometry—specifically, distributed array structurethickness—is optimized simultaneously with distributed momentcontrol of the array structure.An initial study of the SASA concept was performed previously,focusing on attitude control, to demonstrate its feasibility. It wasshown that the spacecraft bus orientation can be controlled by theappropriate bending of the arrays using a pseudorigid body dynamicmodel (PRBDM). A more recent study has further developed realisticfeedback control systems suitable for SASA architectures [34–36].Underactuated control of a flexible array has been demonstrated byapplying an external moment to the bus [37]. An earlier version [38]of this work introduced the use of Euler–Bernoulli beam theory for aphysically consistent description of the array dynamics, and thenonlinear partial differential equation (PDE) model is implementedusing Galerkin approximating functions [39–41]. In the model,piezoelectric actuation is represented by a distributed moment on thearray. The model also accounts for the elastic and inertial propertiesof the actuators. In the spacecraft slewing and pointing maneuversconsidered here, the array bending displacement is small. Thisenables reasonable accuracy when using a linearized bus-arraymodel. Based on this linear model, we present parametric studies that1) help determine performance limits, and 2) provide insight into theresulting array designs.The use of open-loop controls and distributed optimizationparameters, e.g., voltage and array thickness, allows for solutions thatmake limited assumptions on the control or physical architecture.This aids in the exploration of ultimate system performance limits[23]. Although there may be practical constraints for feedbackcontrol system implementation, the resulting co-design solutions canprovide important insights into how to design the physical arraystructure such that it performs optimally as an actively controlledsystem, capitalizing on synergy between physical- and controlsystem design [42].The primary objectives of this work are to demonstrate thefeasibility of the SASA attitude control architecture on arepresentative spacecraft system, to determine the optimal designsof the distributed array structure and controls, and to revealqualitative design insights for intelligent structures with distributedgeometric design. The contributions of this work are as follows. First,we develop a coupled ordinary differential equation (ODE)–PDEmodel of the bus-array system based on extended generalization forhybrid coordinate systems. The elastic and inertial properties of thepiezoelectric layer are included in the model. Second, wedemonstrate bus attitude control using SASAs with slewingmaneuvers on the order of milliradians or arc minutes for precisionpointing and jitter reduction achieved in simulations. Third, wepresent a framework for the optimal integrated design of distributedstructural geometry and distributed control systems. Fourth, wederive maximum bus slew limits achievable through SASA controlusing PRBDM analysis and co-design studies. Finally, we presentdesign guidelines, based on design optimization studies, for thedistributed array structure and distributed control for the SASAsystem.This paper is organized as follows. The models for the busarray system, distributed composite array structure, distributedcontrol, and PRBDM are presented in Sec. II. The formulationfor the combined design of the distributed array structure anddistributed control is presented in Sec. III. Analytical resultsbased on PRBDM theory and numerical results of the co-designstudies are discussed in Sec. IV. Results include the analysis ofthe optimal design tradeoff for the array structure, the optimalplacement of segmented piezoelectric actuators, and parametricstudies on passive damping and jitter disturbance. Finally, theconclusions are discussed in Sec. V.II.Modeling of the SASAs and Rigid Spacecraft BusOur modeling approach is based on the recent work on aircraftdynamics with flexible, articulated wings [43] (see [44] fordetails). The spacecraft motion is modeled as an ODE of asimple cylinder, and the solar array structure is modeled as aPDE of a composite beam with thickness that can vary along itslength.A. PDE ModelHere we assume that actuation is effected only through solar arraystrain actuators that produce strain at the solar array structure surface,resulting in array bending and a distributed moment due to strainactuator surface forces. The strain actuators do not interact withanything external to the spacecraft system, so the total systemmomentum must be conserved. Therefore, for a generallycounterclockwise (CCW) movement of the solar array, the bus (θ)will rotate in the opposing clockwise (CW) direction allowing forattitude changes. This is evident in both the illustration of the beamtheory coordinate system in Fig. 1a and its comparable PRBDMlumped parameter model in Fig. 1b.1. Coupled ODE–PDE Dynamic ModelThe coordinate systems used for the derivation of the Lagrangianof the system are shown in Fig. 1a. The model has two arrays withasymmetric actuation. Let the radius of the spacecraft body be r, andthe spacecraft body rotation angle about origin O be θ. In deriving theequations of motion, it is assumed that the deflections ξ x; t due tobending are small and the beam has no longitudinal velocity.The mass moment of inertia of the spacecraft bus is J θ . The totallength and width of the solar array are represented by l and w. Themass per unit length of the composite beam is denoted mR x and thetotal rigidity is E x I x . Further details of the str
A strain-actuated solar array enables attitude slewing . Distributed piezoelectric actuators help achieve higher precision, higher bandwidth, and quieter operation than reaction wheels. To understand the design tradeoffs for this architecture, a framework for the integrated design of . placement for the