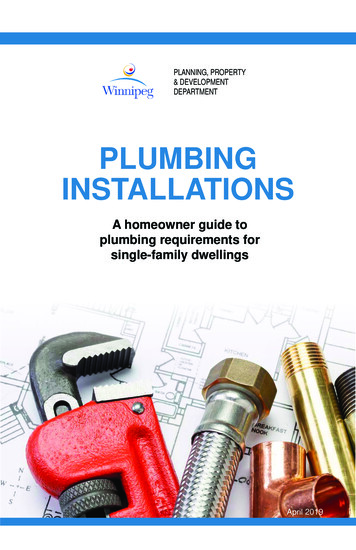
Transcription
PLANNING, PROPERTY& DEVELOPMENTDEPARTMENTPLUMBINGINSTALLATIONSA homeowner guide toplumbing requirements forsingle-family dwellingsApril 2019
contentsPermit Requirements .3Inspection Requirements .4Plumbing Code Requirements .4New Drain and Vent Installations .5Potable Water Systems . 16Protection From ContaminationBy Cross Connections . 17Note:This booklet has been written to:1) Provide homeowners with a summary of some morecommon plumbing regulations; and2) Provide information on the extent to which theplumbing work must be completed before requestingan inspection.It is recommended that the applicable sections of thisbooklet be reviewed before commencing the project.Please note that this booklet is not intended to cover all ofthe plumbing regulations. Complete plumbing requirementsare covered in the Manitoba Plumbing Code.2Every effort has been made to ensure the accuracy ofinformation contained in this publication. However, in theevent of a discrepancy between this publication and thegoverning City of Winnipeg By-law, the By-law will takeprecedence.
A plumbing permit must be obtained from the City of WinnipegPlanning, Property and Development Department, Unit 31 - 30Fort Street whenever:a) a plumbing system is constructed, extended, altered,renewed or repaired, andb) water supply lines in a building are replaced.A plumbing permit is not required when:a) a stoppage in the drainage system is cleared;b) a leak is repaired in a water distribution system;c) a fixture is replaced (like for like) without any change to thedrainage system; ord) a replacement is made to existing faucets, or servicewater heaters.Plumbing permits can be issued only to:a) a person who holds a valid plumbing contractor’s licensefrom the City of Winnipeg authorizing that person to carry outbusiness or trade in the City of Winnipeg, orb) a person who owns and resides at the single family dwellingwhere the work is being done. The owner must personally dothe work. The permit would be issued to the owner providedthe Manager of Development & Inspections is confident thework will be done competently.permit requirementsPermit RequirementsA plumbing permit is not transferable.3
permit requirementsInspection RequirementsBefore calling for the initial inspection, all drains, vents and watersupply lines must be completely roughed in. The work must notbe covered or concealed before inspection. If any part of theplumbing work is found deficient during inspection, alterationsor replacement must be made as necessary. You must call for are-inspection of corrected defects within 30 days of the originalinspection.Prior to covering any new work, you must schedule an inspectionby completing the housing inspection request form online foundat www.winnipeg.ca/housinginspection or by calling theHousing Inspection office at 204-986-5300 between 8:30 am and4:00 pm, Monday to Friday. Please be aware that wait times varyfor phone-in requests.Before calling for a final inspection, all fixtures and equipmentmust be installed, operational and ready for use. If a fixture drainhas been roughed-in for future use, it must be sealed with anapproved plug or cap.Plumbing Code RequirementsSlope of drainsAll drains must be installed to provide a minimum slope awayfrom the fixture of at least 6 mm (1/4 in.) for every 300 mm (1ft)of pipe length. See FIGURE 1.FIGURE 1 - Minimum Slope of Drains368 mm(14.5 in)3000 mm(10 ft)4300 mm(12 in)
Underground drains must be supported by a full firm base andany supports used to support the drain prior to the installation ofgranular material must remain in place.Above ground horizontal pipes shall be supported every 1,200mm (4 ft).Trap armsExcept for a water closet (maximum 1000 mm), the total fall fromthe trap to the vent must not exceed the diameter of the fixturedrain. See FIGURE 2.FIGURE 2 - Fall of a Trap Armvent pipe* See TABLE 1trap armDeveloped length “A” must be at least twice the size of the trap arm.Fall ”B” must not be greater than the size of the trap arm.The maximum distance between a vent pipe and a fixture trapmust not exceed the distances shown in TABLE 1.See FIGURE 3.new drain & vent installationsSupport of drains5
new drain & vent installationsTABLE 1 - Trap Arm Slope (see Figure 2)Pipe Size (B)Slope(in.)1 1/41/501 1/21/5021/5031/50Total AllowableLength (A)1500 mm (5 ft.)1800 mm (6 ft.)2400 mm (8 ft.)3600 mm (12 ft.)FIGURE 3 - Lengths of Fixture Drainsand Expansion Joint12341. Length must not exceed 1200 mm(4 ft.)2. Minimum length is twice the diameterof the fixture drain. Maximum lengthis as shown in TABLE 13. Maximum length is 1000 mm (39 in.).4. Maximum length is 3000 mm (10 ft.).5. Expansion joint - size of a soil orwaste stack.6. Cleanout.56Expansion joints6The design and installation of every piping system must, wherenecessary, include means to accommodate expansion andcontraction of the piping system caused by temperature changeand soil movement. Therefore, expansion joints must be installedat the base of every soil or waste stack. See FIGURE 3.
new drain & vent installationsApproved cleanout fittings must be installed at the followinglocations:a) as close as practicable to the point where the building drainleaves the building;b) at the base of every soil or waste stack;c) to permit the cleaning of a fixture drain from the trap to thevent.d) at every change of direction of more than 45 degrees in sinkdrains. See FIGURE 4.FIGURE 4 - Building Drainage System WithCleanout .C.O.BasinC.O.W.C.Building DrainC.O.Backwater ValveShowerFloor DrainUse of “TY”and “Y”fittingsTee fittings or 90 degree elbows must not be used in thehorizontal portion of a drainage system. All changes of directionmust be made with the use of “Y” and 45 degree bends. Exceptthat a 90-degree elbow or “TY” fittings may be used to changethe direction of horizontal drains when the direction of flow isdown to the vertical. “TY” fittings may be used to make theconnections to vent pipes. See FIGURE 5 and FIGURE 6.(Exceptions see FIGURE 7).7
new drain & vent installationsFIGURE 5 - Permitted Use of Sanitary “TY”Fittings - Part 1Dry VentVentSanitary “T”TRAP ARMDrains8
TRAP ARMTRAP ARMPERMITTEDNOT PERMITTEDTRAP ARMTRAP ARMPERMITTEDNOT PERMITTEDFIGURE 7 - Permitted Use of Sanitary “TY”Fittings - Exceptionsnew drain & vent installationsFIGURE 6 - Permitted Use of Sanitary “TY”Fittings - Part 2PERMITTEDPERMITTEDTYPICAL INSTALLATIONFixtureFixtureNOTPERMITTEDPERMITTED9
new drain & vent installationsPiping in exterior wallsWhere piping may be exposed to freezing conditions, it must beprotected. No drainage or water system can be installed in anyexterior wall of a building. Vent pipes are permitted in exteriorwalls provided they are protected from frost.Wet ventingA soil or waste pipe may serve as a wet vent if:a) the number of water closets does not exceed two;b) water closets are installed downstream of all other fixtures;c) if two water closets are installed on the same wet vent adouble “TY” fitting must be used for a vertical installation anda double “Y” fitting for a horizontal installation;d) trap arms and fixture drains connected to the wet ventcannot exceed 2” except for emergency floor drains;e) where a wet vent extends through more than one storeythe discharge from any one storey above the first does notexceed 4 fixture units (see TABLE 2 on page 15), andf) a wet vent cannot be reduced in size except for anemergency floor drain portion.See FIGURES 8, 9, 10A & 10B.FIGURE 8 - One Storey Venting (Back to Back)Stack Vent 3 in.Wet VentBasin 11/4 in.Water ClosetShower11/2 in.Basin 11/4 in.Water ClosetBathtub11 /2 in.3 in.3 in.10Soil - Waste Stack3 in.
3 in.1 1/2 in.Basin1 1/4 in.Water Closet1 1/2 in.3 in.SECONDFLOORBasin1 1/4 in.AutomaticWasher2in.FIRSTFLOOR3 in.3 in.Showernew drain & vent installationsFIGURE 9 - Two Storey Venting3 in.1 1/2 in.3 in.HeatDuctWater Closet3 in.3 in.3 in.3 in. Wet Vent11
new drain & vent installationsBackwater valvesAll fixtures installed below street level must be protected bya backwater valve arranged to prevent sewer back-up. Thebackwater valve must be installed to protect the branch drainserving below grade fixtures only.See FIGURES 4, 10A, & 10B.FIGURE 10A - Typical Basement PlumbingInstallation Showing Venting Method,Backwater Valve & Attachment to“Cast-Iron” PipingSee “Vent Pipe Connections”Page 143 in.11/2 in.11/4 in.BasinTo install new rough-in “plastic” basementplumbing to existing “cast-iron” piping — useplastic to cast-iron approved adaptor4 in.Building Drain4 in.2 in.AutomaticWasher3 in.Water ClosetBranch DrainShower orBath Tub3 in.3 in.Approved “Backwater Valve” must beinstalled on branch drain to protect all“new” plumbing that is “below grade”.3 in.11/2 in.3 in.3 in. Wet VentFIGURE 10B - If the washer drain will not be installedon the wet vent with the bathroom groupthe size of the wet vent can be reducedto 2”2 in.AutomaticWasherSeparatelyVented3 in.To install new rough-in “plastic” basementplumbing to existing “cast-iron” piping — useplastic to cast-iron approved adaptorSee “Vent Pipe Connections”Page 1411/2 in.11/4 in.Basin4 in.2 in.Building Drain4 in.Water Closet2 in.Shower orBath Tub2 in.3 in.12Approved “Backwater Valve” must beinstalled on branch drain to protect all“new” plumbing that is “below grade”.Branch Drain3 in.2 in.11/2 in.2 in. Wet Vent
Max. fall of trap arm is equal to pipe sizeMax. developed length must not exceed distances shown in TABLE 1Min. Developed length is two times pipe size90 degreeSanitary TeeWet Vent45 degreeFDY45 degree45 degreeTotal change in direction is 135 degrees45 degreeChange in direction between trap and ventThe cumulative change of direction between a fixture trap and avent must not exceed 135 degrees except for a water closet traparm which cannot exceed 225 degrees.See FIGURE 11.new drain & vent installationsFIGURE 11 - Location of Vent Pipes CumulativeChange in DirectionVentinga) Where a vent pipe passes through the roof, it must beprotected from frost closure by increasing the pipe sizeto at least 75 mm (3 in.) in diameter immediately beforepenetrating the roof.b) A vent located in attic spaces must be insulated.c) Vent pipes must be installed without depressions in whichmoisture can collect.d) A vent pipe must extend vertically above the flood level rimof every fixture that it serves before being connected toanother vent pipe.See FIGURE 12.13
new drain & vent installationsFIGURE 12 - Vent Pipe ConnectionsVent terminated through roofto be increased to 75 mm (3 in.)Vent to connect aboveflood level rim of fixtureVent connected tostack vent in atticspaceAbove RimFlood Level RimDrain pipe sizingThe sizes of all fixture outlet pipes must comply with TABLE 2.See FIGURE 13. Loop required perDishwashingKitchen sinkmanufacturer’sinstructionsmachineMay connect directlyto food waste grinderKitchen sink14Loop required permanufacturer’sinstructionsBranch tail piece ordishwasher tail pieceto receive dishwasherwaste connectionDishwashingmachine
MIN. SIZE OF FIXTUREOUTLET PIPES (inches)FIXTUREBathtub (with or without shower) . 11/2Bidet . 11/4Clothes Washer .2Dishwashers (no load when connected to agarbage disposal unit or a kitchen sink trap . 11/2Garbage disposal units - residential type . 11/2Laundry sinks . 11/2Lavatories (basin) . 11/4Shower Drain (with one shower head) . 11/2Shower Drain (with two or three shower heads) .2Shower Drain (with more than three shower heads) .3Sink - one and two compartments . 11/2Water Closet .3FIGURE 13 - Typical Drainage & Vent Sizing11/2 in.3 in.Main VentKitchen SinkBasin11/2 in.11/4 in.3 in.Water Closet3 in.11/2 in.new drain & vent installationsTable 2 - Fixture Size RequirementsBathtub1 /2 in.13 in.3 in.Expansion FittingExpansionJointBuilding SewerCleanout 4 in.(to street)Building Drain4 in.Building DrainCleanout4 in.Floor Drain11/2 in.3 in. Backwater Valve3 in.4 in.Note: Every building drain must be at least 100 mm. (4 in.) in sizeand must be terminated by a vent at least 75 mm (3 in.) in size.15
potable water systems16Potable water systemAll potable water systems must meet the following standards:a) Every water service pipe must be provided with a shut-offvalve where the pipe enters the building.b) A water distribution system must be installed so that thesystem can be drained or blown out with airc) Every fixture supplied with hot and cold water controls musthave the hot water control on the left and the cold watercontrol on the right.d) Every water closet must be provided with a shut-off valve onthe water supply pipe.e) Every pipe that passes through an exterior wall to supplywater (i.e., lawn service) must be provided with a frost-proofhydrant with vacuum breaker or a stop-and-waste valveplaced inside the building close to the outside wall or otherapproved location. Also, a hose bib vacuum breaker mustbe installed on a hose bib located outside a building or insidea garage to protect against backflow.f) All shower valves must be pressure-balance or thermostaticmixing valves conforming to CSA B125, “Plumbing Fittings”.
A hose bib vacuum breaker must be installed on every hosebib located outside a building or in a garage
The design and installation of every piping system must, where necessary, include means to accommodate expansion and ; contraction of the piping system caused by temperature change and soil movement. Therefore, expansion joints must be installed at the base of every soil or waste stack. See ; FIGURE 3. Approved cleanout fittings must be installed at the following locations: a) as close as .