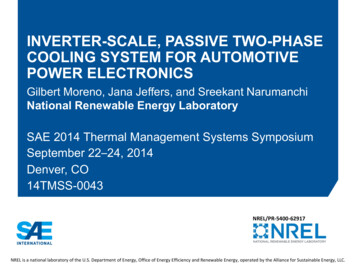
Transcription
INVERTER-SCALE, PASSIVE TWO-PHASECOOLING SYSTEM FOR AUTOMOTIVEPOWER ELECTRONICSGilbert Moreno, Jana Jeffers, and Sreekant NarumanchiNational Renewable Energy LaboratorySAE 2014 Thermal Management Systems SymposiumSeptember 22–24, 2014Denver, CO14TMSS-0043NREL/PR-5400-62917NREL is a national laboratory of the U.S. Department of Energy, Office of Energy Efficiency and Renewable Energy, operated by the Alliance for Sustainable Energy, LLC.
OutlineI.Project Motivation and ObjectivesII.Why Two-Phase Cooling?III. ApproachIV. Experimental Apparatus DescriptionV. Thermal Performance ResultsVI. ConclusionsVII. Future WorkSAE INTERNATIONAL2
MotivationOn-road 80 kW Manufactured Cost: 1,092Heat sink Current Assemblyand housing sensor4%2%5%Bus %Source: Susan Rogers (U.S. DOE) 2013 AMR PresentationSAE INTERNATIONALAccelerate the adoption of electric-drivevehicles to reduce our nation’sdependence on oilThe Problem: High cost of electric-drivevehicles Power electronics are a big contributorto the overall costImproved thermal management enablescost reductions3
Project ObjectiveSignificantly improve thermalmanagement of automotive powerelectronics by utilizing the high heattransfer rates of two-phase cooling Design and build an inverter-scalepassive two-phase cooling systemDemonstrate that the systemdissipates automotive heat loads andprovides superior thermalperformanceDemonstrate more than 60% reduction in thermal resistance viatwo-phase immersion cooling. (Credit: Gilbert Moreno, NREL)SAE INTERNATIONAL4
Why Two-Phase Cooling?10,000Adapted from: Mudawar, I., 2001, "Assessment of High-Heat-flux Thermal Management Schemes," Components and PackagingTechnologies, IEEE Transactions on, 24(2), pp. 122-141.Experimentally measured heat transfercoefficients of 20 W/cm2-K using passivetwo-phase cooling (R-134a)q″ (W/cm2)1,0001001010.10.011101001,000 T ( C) Two-phase cooling provides the highest heat transfer rates compared to othermethods of cooling Near-isothermal system characteristics reduce temperature gradientsSAE INTERNATIONAL5
When Does Two-Phase Cooling Make Sense?Total thermal resistance: Rth (K/W)Cold-plate cooled Package resistancedominates Thermal grease is amajor contributor toresistance1.0Direct-bond-coppersubstrate cooled0.11001,00010,000100,000Heat transfer coefficient (W/m2-K)SAE INTERNATIONAL Lower packageresistance, more suitedfor high performancecooling strategies (i.e.,two-phase)6
Challenges and BarriersTwo-phase cooling is not used to cool automotive power electronics. There arereliability and cost concerns associated with the technology.Strategy: Propose a simple two-phase cooling solution (indirect cooling, passive, lowcost materials, minimize refrigerant requirements) Propose solution with pressures equivalent or lower than those used in vehicleair-conditioning systems Two-phase cooling technology is used in the vehicle air-conditioning systems.Technology is available to develop reliable refrigerant-based cooling systems.SAE INTERNATIONAL7
Two-Phase Cooling Concept Indirect-cooled: Easier to implement, electronicsnot in contact with refrigerantAir-cooledcondenser Passive: Increased efficiency through a passive(no pump or compressor) two-phase coolingapproach Decrease the condenser size using a liquidcooled condenser. Liquid-cooled condenser mayallow use of waste heat for cabin heating(integrated thermal management)EvaporatorPower electronicsmodulesIntegrated condenser(liquid-cooled) andevaporatorPower electronicsmodulesSAE INTERNATIONAL8
Refrigerant SelectionHFO-1234yf: Potential next generation airconditioning refrigerant Qualified for automotive use Environmentally friendly (GWP 4)oLower critical temperature (95 oC)oMildly flammable1000R-134aHFC-245fa:oC) Higher critical temperature (150 Non-flammable Lower pressure as compared withHFO-1234yfoHigher GWP 985oNot used in automotive applicationsPressure (psia)HFO-1234yfHFC-245fa100HFE-7000HFE-710014.7 psia10P vs T1-40-20020406080100Temperature ( C)– Evaluating two refrigerants, but the cooling concept can work with other refrigerantsGWP global warming potentialSAE INTERNATIONAL9
ApproachFundamentalResearch(Credit: Gilbert Moreno, NREL)Characterized performance of HFO1234yf and ration(Credit: Gilbert Moreno, NREL)Demonstrate two-phase immersioncooling of a power moduleDesign a system to dissipate therequired heat loads(Credit: Bobby To, NREL)VaporLiquidEvaporatorEvaluate techniques to enhance twophase coolingSAE INTERNATIONALQuantified refrigerant volumerequirementsDemonstrate improvements overconventional cooling systems10
Experimental System: Designed and Fabricated a Proof-ofConcept Two-Phase Cooling System Refrigerant charge: 250 mL (280 g – 330 g)o Comparison: 2010 Toyota Camry airconditioning system uses 510 g of R-134a25.4 cm (10 in.)4.5 cm(1.75 in.) Maximum operating pressure:1 MPa (150 psi) Automotive fan: 17.8 cm (7 in.) diameter,38 W, 12 VTa, inletTa, outlet20.5 cm(8.1 in.)T v,PvØ 6.98 cm(2.75 in.)Tl25.4 cm (10 in.)SAE INTERNATIONALThtr11
Experimental System: Designed and Fabricated a Proof-ofConcept Two-Phase Cooling System25.4 cm (10 in.)Evaporator cross-sectional view4.5 cm(1.75 in.)Ta, inletTa, outlet20.5 cm(8.1 in.)Interchangeable coldplate designDelphi discrete power module:Image courtesy of DelphiT v,PvØ 6.98 cm(2.75 in.)Tl25.4 cm (10 in.)SAE INTERNATIONALThtr12
Experimental System: Designed and Fabricated a Proof-ofConcept Two-Phase Cooling SystemObjectives Dissipate inverter-scale ( 3.5 kW for a 55-kW system) heat loads with a smallamount of refrigerant without reaching critical heat flux (dry-out)(Credit: Gilbert Moreno, NREL)(Credit: Gilbert Moreno, NREL)R-134aNucleate boilingCritical heat flux(low heat transfer) Measure the condenser thermal resistance to size the condenser for automotiveapplicationsSAE INTERNATIONAL13
Test Procedures Initial test conducted using six ceramic heaters attachedto evaporator using thermal grease Six heaters represent six power switches (inverter-scale).Evaporator thermal resistance:𝑇𝑇 � ��𝑙𝑅𝑅𝑅𝑡𝑡𝑡 Total heater area𝐻𝐻𝐻𝐻𝐻𝐻𝐻𝐻 ��𝑑𝑑𝑑𝑑𝑑𝑑𝑑Condenser thermal �𝑣𝑣 𝑇𝑇 𝑖𝑖𝑖𝑖𝑖𝑖𝑖𝑖𝑖𝑖 𝑎𝑎𝑎𝑎𝑎𝑎𝑅𝑅𝑅𝑡𝑡𝑡 Condenser frontal area𝐻𝐻𝐻𝐻𝐻𝐻𝐻𝐻 ��𝑑𝑑𝑑𝑑𝑑𝑑𝑑SAE INTERNATIONALT vaporP vaporT air, outletT air, inletFanpowerT liquidT heatersHeaterpower25 mm15 mm(Credit: Gilbert Moreno, NREL)14
Evaporator Thermal PerformanceNon-coated/plain evaporatorHFC-245fa (250 mL, 330 g)1.00HFC-245fa Dissipated 3.5 kW of heat insteady-state conditions with a 250mL charge Increase heat dissipation anddecrease thermal resistance usingenhanced surfacesR"th (cm2-K / W) Limited by the heater powercapacity0.753M microporouscoating0.50HFC-245fa: Tsat 75 CPsat 0.7 MPa (106 psia)0.250.0001,0002,0003,0004,000Heat Dissipated (W)(Credit: Bobby To, NREL)SAE INTERNATIONAL15
Evaporator Thermal PerformanceNon-coated/plain evaporatorHFO-1234yf (250 mL, 280 g) HFO-1234yf’s higher heat transfercoefficients resulted in lowerevaporator thermal resistanceHFC-245faHFO-1234yf0.75R"th (cm2-K / W) Prototype limited heat dissipation to1.3 kW with HFO-1234yf because ofhigher pressures. Expect we coulddissipate more heat by increasingsystem pressure capacity1.000.500.25HFO-1234yf: Tsat 42 CPsat 1.1 MPa (154 psia)0.0001,0002,0003,0004,000Heat Dissipated (W)SAE INTERNATIONAL16
Advanced Evaporator DesignIdentified techniques to increaseperformance and reduce the size of theevaporator Designed to cool six Delphi powermodules Increased evaporation surface areato improve thermal performance Fabricated from low-cost materials(aluminum) using low-costmanufacturing techniques2.54 cm(1 in.)17.8 cm (7 in.)7 cm (2.75 in.) Reduced refrigerant requirements to180 mL, (HFO-1234yf 200 g,HFC-245fa 240 g)SAE INTERNATIONAL17
Advanced Evaporator PerformanceNon-coated/plain evaporator Dissipated 3.5 kW of heat with only180 mL of HFC-245fa1.00Proof-of-concept (copper - 250 mL)2nd generation (aluminum - 180 mL) Reduced thermal resistance withimproved designR"th (cm2-K / W)o Smaller aluminum evaporatoroutperforms copper evaporator0.750.500.25copperaluminum Pressure–temperature fluctuationsat higher power levels ( 3 kW)0.0001,0002,0003,0004,000Heat Dissipated (W)o Microporous coating mayeliminate/reduce fluctuationsSAE INTERNATIONAL18
Advanced Evaporator Performance: Power Module CoolingDouble-sidecooledinverterImage courtesy of Oak Ridge National LabLexus Hybrid (2008) double-sidecooled modulesTwo-phase: aluminum evaporator7 cm (2.75 in.)2.54 cm(1 in.)Length:17.8 cm (7 in.)Indirect twophase cooling(aluminumevaporator)Powerdevices7 cm (2.75 in.)2.54 cm(1 in.)Length:17.8 cm (7 in.)PowerdevicesIndirect twophase cooling(copperevaporator)(finite element analysis results)Two-phase: copper evaporator(finite element analysis results)R”th(mm2K/W)% R”thReduction33.2*-13.958%11.565%based on diefootprint Reduced thermal resistance by 58% to65% with the advanced evaporator designcompared with state-of-the-art cooling system Increased device heat flux by as much as189%* Calculated using one side of the die (12.78 mm 12.78 mm)* Performance from: Sakai, Yasuyuki, Hiroshi Ishiyama, and Takaji Kikuchi. Power control unit for high power hybrid system. No. 2007-01-0271. SAE Technical Paper, 2007.SAE INTERNATIONAL19
Condenser Thermal PerformanceR”th (cm2- K/W) [ 250 cfm, 38 W fan]RefrigerantPlain TubesRifled TubesReduced R”thwith Rifled 𝑅𝑅𝑡𝑡𝑡 𝑇𝑇𝑣𝑣𝑣𝑣𝑣𝑣𝑣𝑣𝑣𝑣 𝑇𝑇 𝑖𝑖𝑖𝑖𝑖𝑖𝑖𝑖𝑖𝑖 𝑎𝑎𝑎𝑎𝑎𝑎 Condenser frontal area𝐻𝐻𝐻𝐻𝐻𝐻𝐻𝐻 ��𝑑𝑑𝑑𝑑𝑑𝑑𝑑Rifled Tube(Credit: Gilbert Moreno, NREL) Rifled tubes enhance condensation heat transfer and thus reduce condenserthermal resistance by 18% and 25% for HFC-245fa and HFO-1234yf, respectively HFO-1234yf provides lower condenser thermal resistance values compared withHFC-245fao13% plain tubeso20% rifled tubesSAE INTERNATIONAL20
Condenser Frontal Area (cm2)Condenser Size versus System Temperature(Finned-Tube Condenser)2,000 Estimated condenser frontalarea/size requirements at variousrefrigerant temperatures for theoperating condition:HFC-245faHFO-1234yf1,500o 3.3 kW of total heat, 43oC inlet air Higher refrigerant temperaturesenable a more compact condenser1,000 HFO-1234yf’s higher performanceallows for a smaller condenser500Condenser depth 4.4 cm (1.75 in.)05060708090100System Liquid/Vapor Temperature ( C)SAE INTERNATIONAL21
Condenser Size versus System Temperature(Folded-Fin Condenser)2,000HFO-1234yfCondenser Frontal Area (cm2) Estimated the size requirements for abrazed folded-fin condenser matchedair-side surface area (assumed air-sidewas the dominant thermal resistance)Conditions:3.3 kW of totalheat, 43 C inletairHFC-245faBarnes and Tuma (2009)1,500Finned-tubeFolded-finfinned tube1,0002.54 cm2.54 cmfolded-fin 36% more air-sidesurface area for foldedfin condenser5000(Credit: GilbertMoreno, NREL)Condenser depth 4.4 cm (1.75 in.)5060708090100System Liquid/Vapor Temperature ( C)SAE INTERNATIONAL22
Conclusions Demonstrated that a passive, two-phase cooling system can dissipateinverter-scale head loads (3.5 kW) with only 180 mL of refrigerant Improved the evaporator design to increase its performance and reduce itssizeo Evaporator features enabled the aluminum evaporator to outperformthe copper evaporatoro Increase power module heat flux by as much as 189% as comparedwith state-of-the-art automotive systems Measured the condenser thermal resistance and conducted analysis tosize the condenser at various operating temperaturesSAE INTERNATIONAL23
Future Work Evaluate the effect of cooling system inclination/orientationon thermal performance Experimentally quantify key system metrics (thermalresistance, coefficient of performance, volume, weight) andcompare against conventional cooling systems Develop industry partnerships to demonstrate a two-phasecooled inverter systemSAE INTERNATIONAL24
Acknowledgments:For more information, contact:Susan Rogers and Steven Boyd, U.S.Department of EnergyPrincipal InvestigatorGilbert MorenoGilbert.Moreno@nrel.govPhone: (303) 275-4450Team Members:APEEM Task Leader:Jana Jeffers (NREL)Charlie King (NREL)Sreekant Narumanchi (NREL)Sreekant NarumanchiSreekant.Narumanchi@nrel.govPhone: (303) 275-4062
SAE INTERNATIONAL Approach . Fundamental Research . Module-Level Research . Inverter-Scale Demonstration . Vapor Liquid Evaporator. Characterized performance of HFO-1234yf and HFC -245fa . Evaluate techniques to enhance two-phase cooling . Demonstrate two- phase immersion cooling of a power