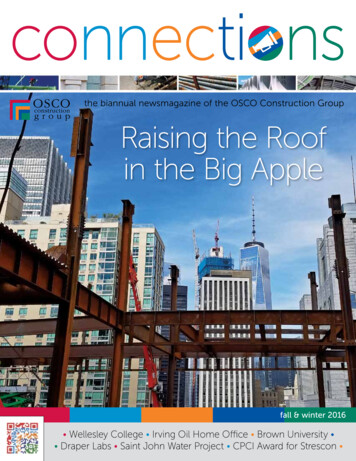
Transcription
connectionsthe biannual newsmagazine of the OSCO Construction GroupRaising the Roofin the Big Applefall & winter 2016 Wellesley College Irving Oil Home Office Brown University Draper Labs Saint John Water Project CPCI Award for Strescon
connectionsthe biannual newsmagazine ofthe OSCO Construction Groupfall & winter 2016what’s insideprojects4.180 Water Street, New York6.Wellesley College8.Aulac Big Stop9.Dolan Road Irving10.St. Stephen Circle K11.Beauty of Precast Award12.Tactile Plates13.Shediac Route 15 Underpass14.CRRC Rail Assembly15.Cellular Concrete16.Irving Oil Home Office18.Saint John Water Project20.Draper Labs21.Jones Lake Spillway21.UMass SMAST 222.Uptown ANBL Store24.667 Congress25.Around the Refinery26.Precast Infrastructure 201631.Power Dam Projects32.Brown University33.Centre Moncton Centre34.Precast Car Dealerships35.Miramichi Centennial Bridge35.Rebar Projects36.Miscellaneous Metals36.115 Hartwell Avenuepriorities37. Safety: Group Safety Awards38. Facilities: Charlottetown Upgrades40. Facilities: Canaan Mountain Sand3. Message fromthe President40. Facilities: New 38m Ready Mix Pump52.Our Locations41. Environment: Approval to Operatepublic &communitypeople42. Saint John Touch a Truck44. Employee AppreciationCelebration42. Special Olympics TruckConvoy47.OSCO Group Picnic42.Greenslade Bursary Winner43.Oromocto LAV Monument43.NSCC Bursary Winner48.Retirement Lane49.OSCO Group Bursaries50.Training & Development50.OSCO Golf Challenge51.Fresh Faces51.CongratulationsOSCOconstructiongroupon our cover.2OSCO Concrete works on 180 Water Street, onManhattan Island, in New York City.See story on page 4.CONNECTIONS is the biannual magazine of the OSCOConstruction Group, published every Spring and Fall to share newsand information with our valued customers & employeesComments and submissions are greatly appreciated and may be sent to theeditor/designer: Tammy Legacy, c/o OSCO Construction Group400 Chesley Drive, Saint John, NB Canada E2K 5L6email: p.com
message from the presidentMessage from the PresidentAs2016 comes to an end, theOSCO Group has seen thebusiness climate recover in manygeographic areas where we sellour products and services. Theonly exception has been our structural steel business. Fabricated steelcomponents can be economicallyshipped many hundreds of miles,allowing fabricators from otherinto Canada and the United States.Another factor which distinguishesOcean Steel from some other NorthAmerican fabricators is that they havechosen to source raw steel shapesfrom China, Korea and other eastern bloc countries at a significantdiscount. Quality issues have becomeapparent from these sources, makingthem less attractive going forward.In the United States,the strong NewEngland constructionmarket, centered onthe Boston metropolitan area, appears to bespreading north intoMaine and south intoRhode Island and Connecticut. Themid-Atlantic region is also showinghigher levels of commercial buildingactivity. This added demand shouldhelp to offset the added supply ofmore steel fabrication capacity.Nevertheless, as the steel marketimproves, Ocean Steel is confidentthat it will remain a viable player in itsspecialty of complex, highly engineered building frames.“As we mature and expand as a Group,we are becoming more involved withdifferent and more elaborate types ofconstruction delivery formats.”regions of North America to enterinto our traditional markets whenlocal markets have slowed down.We are currently seeing this trend onthe eastern seaboard of the UnitedStates, where some new fabricators have emerged as a result of theslowdown in energy-based construction in the oil producing states andprovinces. In addition, offshore fabricators, particularly from China, areshipping structural steel componentswww.oscoconstructiongroup.comIn the Canadian Maritimes, the citiesof Halifax and Moncton still showsigns of growth going into 2017 andbeyond. Saint John has also recovered, with more activity along theharbour waterfront, and with someheavy industrial expansion on thehorizon. Prince Edward Island shouldremain steady, with some moderategrowth, over the next few years. InNewfoundland & Labrador, we anticipate more decline of resource-basedexports and a weaker constructionmarket for the next several years.Competing in many geographic markets with a diverse group of products& services remains one of our principal strategies; another is to moveaway from the commoditization thatoccurs when you participate in only“hard-bid and build” projects. As wemature and expand as a Group, weare becoming more involved withdifferent and more elaborate typesof construction delivery formats. TheOSCO Group has recently taken arole in some Public Private Partnerships or “Triple P’s” which can includeadditional responsibilities, such as, tocontinued on page 41.connections fall & winter 20163
projects4connections fall & winter 2016www.oscoconstructiongroup.com
projects180 Water Street“Top of the House”, New York Citycontributed by: Richard HeckelThe180 Water Street - Top of theHouse project is located inthe busy financial district in downtownManhattan, at the corner of Water andJohn Streets. Collaborative Construction Management awarded Ocean SteelCorporation of Conklin, NY, a contract forthe fabrication and delivery of 400 tonsof structural steel for seven additionallevels to be added on top of an existing 26story building. In addition, reinforcementsteel was supplied to GMC Contracting& Estimating Services for the lower levelsof the existing building, including columnreinforcing plates, transfer girder and newvertical bracing from the ground up.Shop drawings for the Top of the Housestarted in December 2015 and the deliveries of steel will continue until October2016. Hache Technical Services Ltd. andOSCO’s Detailing Department providedshop drawings for this project and OSCO’sEngineering Department provided theconnection design. Detailing and Engineering groups both had to make manyadjustments as demolition progressed, asunknown details in the existing buildingwere exposed to view.GMC Contracting & Estimating Servicesfrom Newark, NJ completed the erection of the reinforcing steel. Memco, Inc.from Culpeper, Virginia erected the Topof House steel. The Erectors were verypleased with the ease and fit up of all thesteel that was provided.Renovations of existing buildings alwayshave their own challenges and 180 Waterwas not any different. The original concept was to erect the steel using a roof-mounted derrick crane that would bear onthe new level steel at the 27th floor. Hoisting steel from the ground would havebeen on the John Street side of the building. Following a recent crane accidentat another job site, the NYC Departmentof Cranes and Derricks restricted craneoperation in windy conditions. Since thissite is exposed to constant wind from theEast River, the Erector chose an alternative means to hoist the steel to the roof.An existing hoistwell was used allowingthe steel to be lifted from the ground floorup to the Top of the House. A hoist wasmounted on the roof and later repositioned to higher levels after each floorwas completed. The construction elevatorwas also utilized for pieces less than 14’-6”long. The Erector then moved/erected thesteel on the upper levels via forklift andmaterial lifts.In this older part of the city at the southerntip of Manhattan, the streets are narrow, congested, and do not follow a gridpattern. With no laydown area available,delivery of steel was a challenge thatrequired close coordination between theErectors and our shop. Loads had to becarefully planned in order to transport onstraight trucks (27’-0” long), so they couldbe off-loaded in the building’s interiorloading dock.Cliff Williams (Ocean’s Field ConstructionManager) has spent several months on topof this building, keeping watch over thisproject. The building is located one blockfrom the East River with views of BrooklynBridge, City Hall and the Freedom Tower atWorld Trade Center. The pictures used inthis article were provided by Cliff. This isanother job that required extra efforts byall involved.www.oscoconstructiongroup.comconnections fall & winter 20165
projectsWellesley CollegeStrescon Provides Custom ArchitecturalPrecast for Pendleton West Hall Renovationcontributed by: Brendan Clancy, P.Eng.Wellesley College has been aprovider of Liberal Arts basededucation to women sinceits founding in 1870 including currentPresidential Candidate Hillary RodhamClinton (prior to her attending YaleLaw). In June of 2015, they undertooka project to renovate Pendleton WestHall. These renovations will includea new Center for Creative Arts and abrand-new Music Arts Pavilion.Consigli Construction, based out ofMilford, MA, was retained by Wellesley College to manage the project.Following Strescon’s 2015 successwith Consigli on the FraminghamUniversity new residences project,Strescon and Consigli teamed up,along with Monadknock Steel &Precast Erectors LLC, to supply andinstall various precast elements forthe renovation.The architectural vision of the newrenovation was based on simulat-6connections fall & winter 2016pattern of wood boards with variousing a woodgrain appearance usingwidths, lengths, thicknesses, elevavarious products, including precasttions and finishes. These drawingsand cast-in-place concrete. Usingwere then converted into a finala combination of colored concreteshop drawing for use by Strescon’sand wood boards as a form liner,carpenters to layout Hem-Fir boards,Strescon was able to create the lookand feel the designteam desired. This“Each panel consisted of a “random” patternallowed Strescon tosecure the supplyof wood boards with various widths, lengths,and installation ofthicknesses, elevations and finishes.”24 solid precastpanels (simulatedsupplied by Consigli, onto the castingwood finish), 12 solid precast soffittable. The colored concrete was thenpanels (simulated wood finish) andpoured over the boards, providing44 stair treads and landings (coloredthe desired appearance once liftedto match the precast panels).the next day.The Architects, KieranTimberlake,This process was extremely timehad a very specific goal they wishedconsuming, and resulted in a castingto achieve with the simulated woodschedule of only one panel (or twofinish on the precast panels. Tosoffits) per day. Total production tookcreate this, the Architects usedapproximately 30 days to completeStrescon’s precast panel drawings,between April and July of 2016.and individually marked up eachpanel, showing all the locations ofThe real difficulty of the project howthe various wooden panels required.ever, was in the erection. The coreEach panel consisted of a “random”www.oscoconstructiongroup.com
projectsof the building was a full-height, cast-in-placebox, which was fully cast, and then insulated,prior to the panel erection. This resulted in blindconnections being made through small openings in the cast-in-place, with spotters on theexterior, and detailing crews on the interior ofthe cast-in-place walls. The wall panels wereinstalled between July 18th and July 26th, 2016,on schedule.Following the installation of the panels, the soffit panels were then installed. The panels weredelivered to site and placed on the ground.Using combinations of: rough terrain fork lifts;come along’s; chain falls; and automotive jacks,they were then moved into position below theceiling, and raised into their final location. Connections on the hidden, top side were made bydetailing crews in a small crawl space betweenthe underside of the cast-in-place floor, and thetop of the precast panels. While this was doneon schedule, it was only expected to install 1-2soffit pieces per day, beginning on August 9thand completing August 24th.Strescon’s scope was recently completed withthe delivery of the remaining stair treads andlandings in early October.www.oscoconstructiongroup.comconnections fall & winter 20167
projectsAulac BIGSTOPAulac, New Brunswick’s new Big Stop, opened on schedule and underbudget on May 19th, 2016. This is the 5th Big Stop FCC Construction’sCivil Division has built for Irving Oil Marketing over the past 18 years.contributed by: Dan Fox, GSCIrving Big Stops are strategicallylocated in high traffic areas, toservice the trucking industry and thetravelling public. They feature: a convenience store; restaurant; trucker’slounge with laundry and shower services; and retail and commercial fuel.Each Big Stop has its own set of challenges; Aulac needed more space fortrucks and the I-24 had no canopyover the dispensers. The building wasalso in need of significant upgrades.The solution was to acquire theadjacent property (a former Shell OilStation). The site required demolitionof existing structures and remedia-8connections fall & winter 2016tion of contaminated soils beforework could begin.the buildings had to be performedwithout disrupting business.Similar to the Enfield Big Stop, IrvingOil Marketing decided to construct anew building while keeping the Existing Big Stop fully operational. Thiscreated many challenges, includingseparating the construction workfrom the customers, with safety as aprimary concern; and removal andrework of existing sewer systems toenable construction of the New I-24,directly behind the old Big Stop. Thiswork was done through the wintermonths to minimize disruption to thecommercial truckers. The main electrical service had to be reconfigured,and shared water services betweenThis project featured the teamworkof a few OSCO Group companies, including concrete supply by Stresconand rebar by OSCO Rebar.FCC Electrical: Allelectrical work was performed by FCC Electrical,who were instrumental incompleting the project ontime. Work on site was managed by
tion of the reinforcing steel. Memco, Inc. from Culpeper, Virginia erected the Top of House steel. The Erectors were very pleased with the ease and fit up of all the steel that was provided. Renovations of existing buildings always have their own challenges and 180 Water was not any different. The original con-cept was to erect the steel using a roof-mounted derrick crane that would bear on .