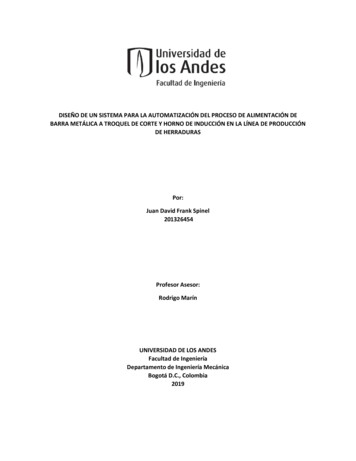
Transcription
DISEÑO DE UN SISTEMA PARA LA AUTOMATIZACIÓN DEL PROCESO DE ALIMENTACIÓN DEBARRA METÁLICA A TROQUEL DE CORTE Y HORNO DE INDUCCIÓN EN LA LÍNEA DE PRODUCCIÓNDE HERRADURASPor:Juan David Frank Spinel201326454Profesor Asesor:Rodrigo MarínUNIVERSIDAD DE LOS ANDESFacultad de IngenieríaDepartamento de Ingeniería MecánicaBogotá D.C., Colombia2019
2
Contenido1.Introducción . 42.Objetivos. 42.1.Objetivo general . 42.2.Objetivos específicos . 43.Condiciones actuales en la línea de producción . 54.Propuesta general para la disposición de la etapa dentro de la línea de producción . 105.Alimentador del troquel . 125.1.5.1.1.Precedentes. 125.1.3.Propuesta . 155.2.6.Toma de la materia prima . 12Alimentador de barra. 215.2.1.Precedentes. 215.2.2.Análisis de los precedentes . 245.2.3.Propuesta . 25Transporte y clasificación de blancos a la salida del troquel de corte . 716.1.Propuesta general . 716.2.Banda transportadora . 756.3.Alimentador del horno. 767.Conclusiones . 788.Bibliografía . 793
1. IntroducciónEn el marco de la optimización de la manufactura masiva de productos, han surgido situaciones enlas que los operarios son expuestos a condiciones inseguras durante el desarrollo de su labor. Porlo que, con el tiempo, se desarrollaron lineamientos que buscan regular las prácticas en plantas deproducción de forma que se garantice la seguridad de sus empleados.Como parte de una actualización de la NR-12, la norma de seguridad en el trabajo en maquinaria yequipos que regula la operación de maquinaria en Brasil, una de las fábricas de herradurasperteneciente al grupo Mustad debe realizar modificaciones a su línea de producción. Sin embargo,las modificaciones implican una importante inversión y una posible disminución en la capacidadproductiva, por lo cual la empresa ha optado por realizar la inversión en automatizar la línea conmiras a ampliar su capacidad productiva en un futuro.Como parte de dicha automatización, el presente proyecto se plantea como el diseño ydocumentación completa de un sistema que permita la automatización de la primera etapa delproceso, comprendida entre la toma de la materia prima desde su espacio de almacenamiento y supaso por un troquel de corte, hasta su alimentación a un horno de inducción.2. Objetivos2.1. Objetivo generalGenerar una propuesta detallada de modificaciones a la primera etapa de la línea de producción deherraduras que permitan automatizarla, aumentar su capacidad productiva, cumplir con lanormativa de seguridad y, en un futuro integrarse con la solución de automatización implementadapara las etapas siguientes de la línea de producción. El presente proyecto no abarca el desarrollo deun sistema de control para el sistema diseñado.2.2. Objetivos específicos Proponer modificaciones a la línea de producción que permitan el procesamiento de 30blancos (cortes que sirven de materia prima para las herraduras) por minuto en la primeraetapa de esta. Proponer un diseño de detalle para la automatización de la primera sección de la línea deproducción. Garantizar el cumplimiento de la normativa vigente (NR-12). Garantizar un mínimo de consistencia dimensional de los blancos a la salida de la secciónmodificada, según los criterios establecidos por control de calidad. Proponer un diseño que permita realizar operaciones de mantenimiento con facilidad. Proponer modificaciones para que el sistema se adapte a los diferentes tamaños de materiaprima y herraduras a procesar. Estos pueden ser operados de forma manual. Especificar una propuesta para clasificar y separar los retazos sobrantes del proceso decorte de los blancos a procesar.4
3. Condiciones actuales en la línea de producciónActualmente, la línea de producción tiene capacidad para la fabricación de herraduras de diferentestamaños a partir de barras de acero ASTM A-36. Estas barras, que son la materia prima, se conocencon el nombre de blancos y se manejan en longitudes que van desde los 220 hasta los 420 mm ysecciones con un rango desde los 5 hasta los 10 mm de espesor y desde los 16 hasta los 21 mm deancho. La línea opera en dos turnos para un total de entre 20 y 22 horas diarias, y está en capacidadde producir entre 11 y 12 herraduras por minuto. El proceso se encuentra dividido en 5 etapas comose puede ver en la Ilustración 1 y, a continuación, se describe cada una de ellas:Ilustración 1. Esquema actual de la línea de producción5
Ilustración 2. Rack de almacenamiento.1. Etapa de Cortado: en esta etapa un operario toma una de las barras del rack de almacenamiento(Ilustración 2) y la introduce en el troquel de corte (Ilustración 3) hasta llegar a un tope, y loacciona mediante pedal. En esta etapa se cortan los blancos que sirven de base para lasherraduras (Ilustración 4). Una vez troquelados, los blancos y los retazos de material sobranteson depositados en una mesa al ser empujados por la siguiente sección de barra a cortar.Ilustración 3. Troquel de corte.6
Ilustración 4. Proceso de corte de los blancos.2. Etapa de calentamiento: a continuación, un segundo operario toma los blancos de la bandeja ala salida de la primera etapa, los separa de los retazos, y los ubica en otra bandeja al lado delhorno de inducción, luego toma un grupo de blancos, los apila y los introduce en un buffer parala alimentación automática de este (Ilustración 5 e Ilustración 6). Allí se llevan a una temperaturaentre los 900 y los 1000 C como preparación para la siguiente etapa que corresponde a unforjado en caliente. En caso de que los operarios no logren tomar el blanco próximo a salir atiempo, el horno lo expulsa a una canasta donde posteriormente puede ser tomado. Los blancosson alimentados sobre tuberías de acero inoxidable por las que circula refrigerante a fin depoder introducirlas al horno sin que la temperatura afecte el funcionamiento.Ilustración 5. Alimentación del horno de inducción.7
Ilustración 6. Vista lateral horno de inducción.3. Etapa de forjado en caliente: a partir de este punto, la línea de producción se bifurca en tramossimétricos (ver Ilustración 1). Un operario toma uno de los blancos del horno de inducciónhaciéndolo salir con un pedal y lo introduce en una prensa, accionada mediante un pulsador(ver Ilustración 7). En esta etapa, se generan las ranuras y agujeros para los clavos, cada uno conun accionamiento de la prensa y, posteriormente, el operario retira el material y lo introduce aun canal de alimentación que, mediante gravedad lo lleva a la siguiente etapa.Ilustración 7. Forjado en caliente.8
4. Etapa de doblado: la dobladora se activa automáticamente cuando detecta la presencia de unblanco y genera la forma curva de la herradura para luego dejar deslizar la pieza por un canalhasta una bandeja de recolección donde se acumulan las herraduras. En la Ilustración 8 se puedever como uno de los blancos está siendo doblado, mientras que uno nuevo llega por la canaldesde la etapa de forjado en caliente.Ilustración 8. Dobladora.5. Etapa de prensado: finalmente, un cuarto operario toma la herradura que sale de la etapa dedoblado y la introduce en una prensa (ver Ilustración 9). Esta es accionada mediante un pulsadora fin de garantizar que la herradura salga plana de la línea de producción, pues durante elproceso de manufactura se pueden dar distorsiones geométricas. La herradura es tomada de laprensa por el mismo operario y se arroja en una canasta de donde es tomada posteriormentepara su empaquetado y comercialización.Ilustración 9.Prensado9
4. Propuesta general para la disposición de la etapa dentro de la línea de producciónComo se evidencia en la Ilustración 1, El rack donde se almacena la materia prima, está justo al ladodel troquel de corte, lo cual facilita el proceso de alimentación, por lo que no se plantea ningunamodificación en su posición. Por otro lado, se observa que el horno de inducción se ubica de formaque los blancos que salen del troquel de corte deben realizar un giro de 90 para entrar al buffer delhorno.Esto complejiza el transporte de los blancos, por lo cual se consideró la posibilidad de alinear laentrada del horno modificando la disposición de la línea de producción como se puede ver en laIlustración 10. Si bien esta disposición permite una alimentación del horno más sencilla, implica quelas dos líneas de producción que surgen después del horno se deban redistribuir de forma que dejende ser simétricas.Ilustración 10. Esquema alternativo de la línea de producción.Lo anterior implica que, en un futuro cuando se quiera automatizar dichas etapas, deberá diseñarseuna solución particular para cada línea. Por lo que se optó por continuar con la distribuciónexistente, modificando ligeramente los espacios para acomodar el sistema propuesto que seexplicará más adelante. La distribución definitiva se puede observar en la Ilustración 11.10
Ilustración 11. Disposición seleccionada de la línea de producción.La solución propuesta finalmente se compone de dos sistemas: por un lado, está el sistema dealimentación del troquel de corte, que se encarga de tomar la materia prima del rack dealmacenamiento, alinearla con el troquel y alimentarla de forma controlada. Y por el otro lado seencuentra el sistema de alimentación del horno de inducción, que se encarga de tomar los blancosque salen del troquel de corte, separarlos de los retazos del proceso de corte y alimentarlos al hornode inducción.11
5.Alimentador del troquelEste sistema se dividió en dos subsistemas, uno encargado de tomar la materia prima del rack dealmacenamiento y otro que se encarga de la alimentación de forma controlada. A continuación, sediscute el proceso de diseño de cada uno y la propuesta desarrollada:5.1. Toma de la materia prima5.1.1. Precedentes5.1.1.1. Mecanismos de alimentación de barrasComo parte de procesos de automatización en otras plantas de producción del grupo Mustad, sedesarrolló un sistema que permite la toma de las barras desde el rack de almacenamiento encondiciones similares a las de la planta a modificar. Este, se prototipó y ha dado resultadossatisfactorios. Sin embargo, cabe resaltar que las barras utilizadas en esa planta tienen muy bajasvariaciones dimensionales, por lo que son prácticamente rectas, lo cual no se sucede en esteproyecto, pues la materia prima tiende a tener dichas variaciones.El sistema prototipado se encuentra montado sobre la estructura del rack que se usa para elalmacenamiento de las barras metálicas, en este caso apiladas de forma diagonal, como se puedever en la Ilustración 12 para disminuir el efecto del peso de las barras. En la parte inferior de laestructura se encuentra ubicada una serie de actuadores lineales neumáticos con una platina sujetaen su extremo (ver Ilustración 13) que empujan la barra inferior del arreglo.Ilustración 12. Rack de almacenamiento.12
Ilustración 13. Actuador lineal con platina.A fin de que solo se desplace la barra inferior, se utiliza una serie de topes ajustables (Ilustración 14)de forma manual, de tal manera que impiden el movimiento de las barras del arreglo cuando elactuador lineal se activa para mover la primera barra. Estos topes son graduables, debido a que elproceso hace uso de barras de diferentes espesores según el tipo de herradura a procesar. Los topesconsisten en una platina ranurada que se sujeta en un solo punto, mediante perno, a la estructuradel rack de almacenamiento. Esto permite tanto un movimiento rotacional como uno lineal a fin deubicar el tope.Ilustración 14. Tope ajustable en rack de almacenamiento.13
Cuando la barra es empujada, sale del arreglo de forma perpendicular a este y es detenida por topespivotados (Ilustración 15) de forma que detienen la barra y cuando esta cae, los hace rotardejándolos de forma horizontal, con lo cual la barra toma la misma orientación (Ilustración 16). Estopermite que la barra quede alineada con el plano sobre el cual debe deslizarse para entrar al troquelde corte. Junto a estos topes, se ubican sensores a fin de detectar la presencia de la barra una vezha sido tomada del arreglo.Ilustración 15. Tope pivotado.Ilustración 16. Funcionamiento del tope pivotado.14
Una vez la barra a cortar se encuentra en posición, es desplazada desde su extremo posterior porun actuador lineal de forma que se ubica sobre el mecanismo responsable por la alimentación deltroquel de corte.5.1.2. Análisis del precedenteComo se mencionó anteriormente, el prototipo estudiado ha dado buenos resultados y,adicionalmente, puede adaptarse de forma sencilla a la línea de producción existente y es de fácilmontaje y mantenimiento. Por esto, se decidió emplear el mismo diseño analizado. Sin embargo,en el marco del proyecto, la materia prima tiene cierta variación dimensional, por lo cual se modificóligeramente a fin de garantizar el correcto funcionamiento del subsistema con barras que no soncompletamente rectas.5.1.3. PropuestaEn la Ilustración 17 se observa el rack de almacenamiento con el subsistema de toma de las barrasensamblado. El troquel de corte y el alimentador se encuentran ubicados en el costado izquierdode la imagen. La barra sale del rack por ese lado, a la misma altura a la que se encuentra la entradadel alimentador, de forma que puede ingresar directamente en este.Ilustración 17. Rack de almacenamiento, alimentador de barra y troquel de corte.15
El rack, que ya existe en la planta, es una estructura de perfiles tubulares cuadrados 50x50x4 mmsoldados y láminas de 3mm de espesor (ver Ilustración 18). Dicha estructura genera un planohorizontal sobre el cual se depositan los atados de barras a procesar y un plano inclinado sobre elcual reposan las barras una vez son extraídas del atado y organizadas por un operario. La estructurase encuentra anclada al suelo mediante pernos ubicados en platinas soldadas a sus patasIlustración 18. Estructura del rack de almacenamiento.A lo largo del rack se ubican varios actuadores lineales y topes, como se puede ver en la Ilustración19 y en la Ilustración 20. El primer actuador, de referencia Festo DSBC-63-40-PPVA-n3 [1] seencuentra sujeto a la estructura del rack y tiene acoplada una platina en su extremo. Con ella, seencarga de empujar la barra que se encuentra en la parte inferior del arreglo mientras que elmovimiento de las demás barras es restringido por un tope. Este se encuentra montado sobre laestructura y permite graduar su posición y de forma manual. Consta de una platina ranurada que sesujeta mediante perno a una segunda platina acoplada a la estructura del rack. Adicionalmente, hayuna lámina que se sujeta a los extremos móviles de todos los actuadores de forma que se vincula sumovimiento. El funcionamiento de estos elementos se puede observar en la Ilustración 21.16
Ilustración 19. Actuadores instalados en el rack de almacenamiento.Ilustración 20. Actuadores instalados en el rack de almacenamiento.17
Ilustración 21. Funcionamiento de actuador y tope para la toma de barras.Un segundo tope se encarga de detener el avance de la barra empujada por el actuador lineal, comose observa en la Ilustración 22, este tope se encuentra en el extremo de un balancín calibrado pararotar con el peso de la barra, de forma que esta queda ubicada horizontalmente. Un segundoactuador de referencia Festo ADN-40-30-A-P-A [2], sujeto a la estructura del rack y con una láminaacoplada en su extremo móvil empuja la barra de forma que se alinea contra el tope del balancín,como se puede ver en la Ilustración 23.Ilustración 22. Funcionamiento balancín.18
Ilustración 23. Funcionamiento del segundo actuador lineal.En el extremo del rack se instala un actuador neumático de referencia Festo DSBC-50-500-PPVA-n3[1] que se acopla a una platina a la que se le sujetan los ejes de cuatro rodillos de guía que sedesplazan horizontalmente siguiendo la estructura del rack. En la parte superior de la platina sesujeta un ángulo en acero AISI 1020 que es el encargado de empujar la barra a procesar cuando seactiva el actuador mencionado, como se aprecia en la Ilustración 24 e Ilustración 25.Ilustración 24. Actuador que empuja la barra hasta la entrada del alimentador.19
Ilustración 25. Actuador que empuja la barra hasta el alimentador.A la salida del rack se instala un pisador para garantizar el control de la posición vertical de la barraalimentada. Este se compone de una lámina doblada de 3mm de espesor a la que se sujete mediantepernos un actuador lineal de referencia Festo ADN-40-60-PA [2] que tiene acoplada una rueda deguía en su extremo, que gira de forma libre mientras la barra es alimentada, pero la presionaverticalmente contra la estructura, como se puede ver en la Ilustración 26 e Ilustración 27.Ilustración 26. Pisador y tope a la salida el rack.20
Ilustración 27. Pisador y pieza para alinear barras a la salida del rack.Para garantizar que las barras entren rectas al alimentador, se adiciona una pieza en acero 1020sujetada mediante pernos a la estructura del rack, como se puede ver en la Ilustración 27. Esta piezase encarga de alinear la barra que entra al alimentador, permitiendo que las barras a procesartengan una desviación horizontal de 1.5 cm, por lo tanto, barras con una variación dimensionalmayor no podrán ser procesadas.5.2. Alimentador de barra5.2.1. Precedentes5.2.1.1. Prototipo desarrollado en una de las plantas del grupo MustadEste mecanismo, presentado en la Ilustración 28, se conforma por un piñón y seguidor conectadospor medio de una cadena de transmisión y ubicados bajo la barra a alimentar. El piñón recibe supotencia de un motor eléctrico. Adicionalmente, un grupo de dos rodillos desplazables en el ejevertical se ubica sobre la barra para generar una fuerza normal sobre esta y poder ajustarse a losdiferentes espesores de las barras a procesar.Ilustración 28. Mecanismo de alimentación del troquel de corte.21
Un actuador lineal ubicado de forma perpendicular a la barra que va a ser alimentada se activa,haciendo descender un rodillo sobre la barra (Ilustración 29). Este rodillo garantiza una fuerzanormal que impide que la barra se mueva de forma vertical.Ilustración 29. Rodillo.Cuando la barra es introducida en el troquel una distancia apropiada para cortar el blanco deseado,activa un sensor de fin de carrera (Ilustración 30), activando el troquel. El sensor puede desplazarselinealmente mediante la activación de un actuador lineal. Este movimiento cumple un doblepropósito: por un lado, el sensor se retrae cuando el blanco es cortado para que caiga en una bandatransportadora (Ilustración 31) que lo lleva a la siguiente etapa, y por otro lado, permite ubicarlo endiferentes posiciones a fin de variar la longitud de los blancos que se cortan en función del tipo deherradura a producir.Ilustración 30. Sensor de final de carrera.22
Ilustración 31. Salida de la etapa de corte.5.2.1.2. Alimentador de alambreSe tomó como referencia el alimentador de alambre modelo NAD desarrollado por Wittels-Albert[3], presentado en la Ilustración 32. Se puede ver en la Ilustración 33 que el alimentador tiene unpar de rodillos móviles que se ubican en la parte inferior del sistema, a fin de ajustar el calibre dealambre a procesar. Por otro lado, la transmisión se realiza mediante un sistema de poleas. Estemecanismo, a pesar de no ser para la misma aplicación del presente proyecto, sirve como referenciapara la configuración general del sistema diseñar.Ilustración 32. Alimentador de alambre Witels-Albert.23
Ilustración 33. Planimetría de alimentador de barra [4].5.2.2. Análisis de los precedentesComo se observa en la Ilustración 30, la operación del troquel de corte está determinada por unsensor de fin de carrera activado por la barra que va a ser procesada. Sin embargo, por lasdimensiones de las barras utilizadas en la línea a automatizar, no es viable replicar dicho sistema.Esto, pues las barras más cortas no sobresalen de la bancada lo suficiente como para alcanzar aactivar el sensor, lo cual implica buscar una alternativa para el control de la alimentación.Adicionalmente, el alimentador empleado en el prototipo cuenta con tracción únicamente en labanda inferior mientras que la superior únicamente ayuda a generar una fuerza normal, lo cualocasiona deslizamientos relativos entre las barras y las bandas de forma esporádica, condición nodeseable.Por otro lado, se puede ver en la Ilustración 32 que el alimentador de alambre utiliza un sistema derodillos en lugar de bandas. Esto es deseable desde el punto de vista del mantenimiento ya quepermite la intervención independiente de cada rodillo y no se debe asegurar una tensión adecuadade la banda que, para fines prácticos tiene poca influencia sobre la tracción en el espacio entre losrodillos.El mecanismo utiliza un sistema de poleas para la transmisión de potencia desde un motor eléctrico.Esto tiene la ventaja de que la cadena permite el movimiento relativo de los ejes motrices de formaque se puede ajustar la altura de los rodillos para procesar alambres de diferente calibre. Sinembargo, cuenta con la desventaja de una baja eficiencia en comparación con otros mecanismos detransmisión como, por ejemplo, los engranajes.Finalmente, se descartó la opción de tener rodillos desplazables en la mitad inferior del sistema puesse debe garantizar que estos se encuentren alineados permanentemente con la entrada del troquelde corte. Para permitir el ajuste a los diferentes espesores de barra a procesar se optó por dejarfijos los rodillos inferiores y desplazar los superiores.24
5.2.3. PropuestaTras el análisis anterior, se optó por realizar el control de la alimentación a partir de la posiciónangular de los rodillos del alimentador. Esto permite, por un lado, simplificar el sistema dealimentación al eliminar la necesidad de instalar un subsistema con sensores adaptables a variasposiciones y, por otro lado, garantiza que se puedan procesar todas las longitudes de blanco querequiere la línea de producción.Debido a esta decisión, se optó por un sistema de rodillos similar al del alimentador de alambre [4],con tracción en todos los rodillos, de forma que se garantice la eliminación del deslizamientoesporádico entre los rodillos y las barras alimentadas. También se optó por el uso de rodillos enlugar de bandas por la facilidad de mantenimiento y las demás razones expuestas en el análisis.Adicionalmente, se optó por un sistema de transmisión de piñón y engranaje en lugar de piñón ycadena, de forma que se maximice la eficiencia de transmisión. Esto implicó el diseño de unmecanismo que permita variar la posición de los rodillos a fin de ajustarse a los diferentes espesoresde barra a procesar, teniendo en cuenta que la variación de espesores es únicamente de 5mm.Esquema generalIlustración 34 se presenta una vista general del sistema propuesto. La potencia es suministrada porun motorreductor al eje b, mediante un acople flexible. Esta es transmitida mediante engranajes alos ejes a, a’, d y e. Siendo fijos los dos primeros mientras que los dos últimos pueden rotar alrededordel eje b. Este, cumple dos propósitos: por un lado, permite la inversión del sentido de giro de losejes d y e y, por el otro lado, sirve como pivote para que estos puedan girar sin desacoplarse delsistema de transmisión.Ilustración 34. Esquema general del alimentador.25
Un mecanismo de biela-manivela-pistón se utiliza para convertir el movimiento rotacional de losejes d y e alrededor del eje b en un movimiento lineal, de forma que se puede ubicar un par deactuadores lineales en la parte superior del sistema para controlar la posición de estos ejes ypermitir que se ajusten a los diferentes espesores de barra a procesar. Esto es posible debido a quelos espesores varían únicamente 5 mm, con lo cual pueden rotar los ejes sin que su posiciónhorizontal con respecto a los ejes a y a’ varíe de forma considerable. El funcionamiento de estemecanismo puede apreciarse en la Ilustración 35.Ilustración 35. Funcionamiento del mecanismo de ajuste.Adicionalmente, se consideraron dos disposiciones posibles para el alimentador, como se pude veren la Ilustración 36. La primera opción cuenta con la ventaja de que se disminuyen los momentosflectores a los que se someten los rodillos y los protege del exterior. Sin embargo, dicha opcióndificulta el mantenimiento del sistema. Esto, pues implica el desmonte de la bancada y los ejes cadavez que se desee tener acceso a los rodillos. Por lo anterior, se optó por la segunda opción puesfacilita el acceso a los rodillos en caso de ser necesario. Cabe aclarar que esta opción se escogió apesar de que implica mayores momentos flectores, puesto que las cargas de operación sonrelativamente bajas en comparación con las que podría soportar el sistema como se verá másadelante. A continuación, se discutirá la metodología empleada para el diseño de los elementos quecomponen el alimentador.26
Ilustración 36. Alternativas consideradas para la disposición del alimentador.27
5.2.3.1.1. Determinación de requerimientos del nNúmero de barras para cortar 30 blancos [-]Cadencia objetivo [blancos/min]Distancia de puntas [mm]Fuerza normal en cada rodillo [N]Número de golpes por barra [-]Longitud de barra [mm]Distancia por alimentar para cortar 30 blancos [mm]Longitud del blanco [mm]Longitud del retazo [mm]Número de blancos que se sacan por barra [-]Potencia máxima por rodillo [W]Torque de entrada de los rodillos [Nm]Aceleración/Desaceleración de la barra [mm/s2]Distancia entre blancos [mm]Fuerza de tracción sobre la barra [N]Fuerza de tracción sobre cada rodillo [N]Masa de la barra (supone sección máxima) [kg]Tiempo para procesar una barra [min]Tempo por ciclo de la prensa [min]Tiempo consumido en corte por barra [min]Tiempo disponible entre cortes [s]Tiempo para movimiento por barra [min]Tiempo para movimiento por blanco [min]Ancho de rodillos [mm]Velocidad máxima de la barra [mm/s]Velocidad media de la barra [mm/min]Peso de cada rodillo [N]Diámetro de rodillos [mm]Aceleración angular del rodillo [rad/s 2]Coeficiente de fricción estática A36/caucho [-]Densidad de las barras [kg/m3]Velocidad angular máxima rodillo [rad/s]Velocidad angular media rodillo [rad/s]Tabla 1. Nomenclatura empleada para los cálculos generales.28
Lo primero que se necesita conocer son las condiciones a las que deben operar los rodillos delalimentador. Estas son impuestas por la cadencia a la que se deben procesar las barras y fuerondeterminadas según el siguiente procedimiento (ver Ilustración 37 y Tabla 1).Ilustración 37. Nomenclatura de parámetros geométricos de barras y blancos.Para cada una de las longitudes de los blancos a procesar se halló el número de blancos que puedensacarse de cada barra de 6 metros de largo utilizadas como materia prima. Con esta información secalculó el número de golpes que debe dar el troquel y la longitud que tienen los retazos resultantesdel procesamiento de las barras, según la Ecuación 1.𝐿𝑟 𝐿𝐵 𝐷 𝑑 𝑁𝑏(𝐿𝑏 𝑑)Ecuación 1. Longitud de los retazos de corte.También se halló el tiempo necesario para procesar una barra, 𝑡𝐵 , sabiendo que se deben cortar 30blancos cada minuto y conociendo el número de blancos que pueden cortarse por cada barraprocesada. Con este tiempo, y sabiendo que el tiempo que toma cada corte de la prensa, 𝑡𝑐𝑖𝑐𝑙𝑜 , sehalló el tiempo disponible para el movimiento de la barra, 𝑡𝑚𝐵 , según la Ecuación 2.𝑡𝑚𝐵 𝑡𝐵 𝑡𝑐𝑜𝑟𝑡𝑒 𝑡𝐵 𝑡𝑐𝑖𝑐𝑙𝑜 𝐺𝐵Ecuación 2. Tiempo disponible para el movimiento de la barra.Para cumplir con la cadencia objetivo, es necesario considerar que no solo se debe alimentar unacantidad de barra cuya longitud sea equivalente a la de 30 blancos, sino que se debe alimentar deforma adicional la Distancia D, necesaria para garantizar que el troquel de corte quedacompletamente apoyado sobre la barra y la distancia d, correspondiente a la separación entre cadauno de los blancos cortados. Con estas distancias, y sabiendo cuantas barras son necesarias paraobtener 30 blancos, se halló la distancia a alimentar, 𝐿𝑎𝑙 , para cada tipo d
del troquel de corte, lo cual facilita el proceso de alimentación, por lo que no se plantea ninguna modificación en su posición. Por otro lado, se observa que el horno de inducción se ubica de forma que los blancos que salen del troquel de corte deben realizar un giro de 90 para entrar al buffer del horno.