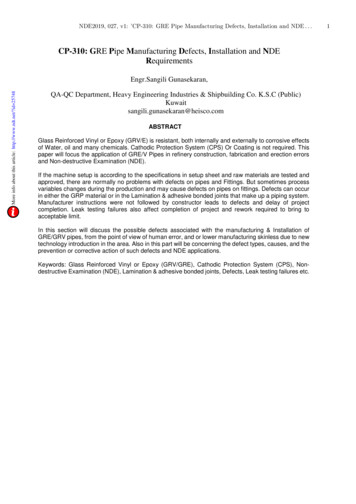
Transcription
NDE2019, 027, v1: ’CP-310: GRE Pipe Manufacturing Defects, Installation and NDE . . .CP-310: GRE Pipe Manufacturing Defects, Installation and NDERequirementsMore info about this article: http://www.ndt.net/?id 25748Engr.Sangili Gunasekaran,QA-QC Department, Heavy Engineering Industries & Shipbuilding Co. K.S.C CTGlass Reinforced Vinyl or Epoxy (GRV/E) is resistant, both internally and externally to corrosive effectsof Water, oil and many chemicals. Cathodic Protection System (CPS) Or Coating is not required. Thispaper will focus the application of GRE/V Pipes in refinery construction, fabrication and erection errorsand Non-destructive Examination (NDE).If the machine setup is according to the specifications in setup sheet and raw materials are tested andapproved, there are normally no problems with defects on pipes and Fittings. But sometimes processvariables changes during the production and may cause defects on pipes on fittings. Defects can occurin either the GRP material or in the Lamination & adhesive bonded joints that make up a piping system.Manufacturer instructions were not followed by constructor leads to defects and delay of projectcompletion. Leak testing failures also affect completion of project and rework required to bring toacceptable limit.In this section will discuss the possible defects associated with the manufacturing & Installation ofGRE/GRV pipes, from the point of view of human error, and or lower manufacturing skinless due to newtechnology introduction in the area. Also in this part will be concerning the defect types, causes, and theprevention or corrective action of such defects and NDE applications.Keywords: Glass Reinforced Vinyl or Epoxy (GRV/GRE), Cathodic Protection System (CPS), Nondestructive Examination (NDE), Lamination & adhesive bonded joints, Defects, Leak testing failures etc.1
2NDE2019, 027, v1: ’CP-310: GRE Pipe Manufacturing Defects, Installation and NDE . . .CP-310: GRE Pipe Manufacturing Defects, Installation and NDERequirementsEngr.Sangili Gunasekaran,Unit Head-Quality Operations, ASNT NDT Level-3 (RT/UT/MT/LT/VT), ASNT Section Officer, QA-QCDepartment, Heavy Engineering Industries & Shipbuilding Co. K.S.C (Public)Kuwaitsangili.gunasekaran@heisco.com1.0 IntroductionGlass Reinforced Vinyl or Epoxy (GRV/E) is resistant, both internally and externally to corrosive effectsof Water, oil and many chemicals. Cathodic Protection System (CPS) Or Coating is not required.If the machine setup is according to the specifications in setup sheet and raw materials are tested andapproved, there are normally no problems with defects on pipes and Fittings. But sometimes processvariables changes during the production and may cause defects on pipes on fittings. Defects can occurin either the GRP material or in the Lamination & adhesive bonded joints that make up a piping system.Manufacturer instructions were not followed by constructor leads to defects and delay of projectcompletion. Leak testing failures also affect completion of project and rework required to bring toacceptable limit.2.0 Body of Knowledge2.1 Table -1 Glass Reinforced Plastic Pipes – Manufacturing defects and installation defectsDefinitionSurface Void: Small air pocketsor voids beneath the surfacemat. Air pockets can be brokenwith ball pen.CausesCuring speed is too high(styrene is entrapped insurface).ConsequencesWeep age failureCorrective actionSingle void: If 1.5mmdeep or 15mm diam.,then repair. Group ofvoids: Only repair ifthere are more than 4voids per 0.1m2 and dia 15mm and depth 1.5mm:Cracks/ Delamination: Brightsolid” area in laminate due tolack of bond between resin andfibers. Separation of layers(plies) within laminate.PoormanufacturequalityWeep age failureRejectMissing Fiber: Broken or cutouter Roving's.Scraping, scuffing ormanufacturingprocessReducedpressure to causeWeep age.Accept
NDE2019, 027, v1: ’CP-310: GRE Pipe Manufacturing Defects, Installation and NDE . . .Surface Pits : Small crater in theinner surface of the laminate,with width (max. diameter)similar to or smallerthan depthResin drops in pipes throughoutPoormanufactureResin Pin holes during windingWeep age failurefor large pitsReject/Major Repair asper project specificationResin flow is too high/Improper removing ofexcess resinMinor effect onPerformance.Minor Repair above 3mm heightas perproject specificationResin flow is too lowand lack of top coat.PoorQualityManufactureWeep age failurefor large pitsReduce the JointStrengthandfeasibilityforLeakageorWeep ageReject/Major Repair asperProjectSpecificationReject and instructMachine operator tokeep the socket build upthickness uniformity asperprojectspecification.Foreign objects: Black spotsinside the pipesForeignmandrelonWeep age failureBefore winding cleanmandrel properly.Resin Rich : Excess resin outsideExcess resin is notremoving properly /Remove excess resinproperly by wiping.Minor effect onperformanceMinor Repair as perproject specification.Air pockets: Voidage withinlaminate or outer gel coatcaused by entrapped airPoormanufacturequalityMinor effect onperformanceMinor repair if withinouter gel coat.Cutting damageLackofworkmanshipGoodWeep age failureBonder should Confirmpipe completely cut bythecutterbeforeremoving the cutterform the pipeEnd DamageDuetohandlingimproperWeep age failureDamaged area to be cutand removed.Dry Joint: Area of incompletesurface film where thereinforcement has not beenwetted by resin, leaving bareexposed fibers.Poor quality BondingMajor effect onperformanceReject/Major repair asper project specificationAir pockets : Voidage withinlaminate or outer gel coatcaused by entrapped airPoor quality BondingMinor effect onperformanceApply serrated layuproller on intervals oflaminationBurned Laminate : Thermaldecomposition evidenced bydistortion or discoloration ofthe laminate surfaceInteraction withexternal heat source.Reducedpressure to causeWeep age.Minor Repair as perprojects specification.Non Uniform Socket build upqualityObjects3
4NDE2019, 027, v1: ’CP-310: GRE Pipe Manufacturing Defects, Installation and NDE . . .Lack of adhesive: Unbondedarea of joint face.Too little adhesive ornot applied uniformlyMovement duringCuring.Weakened jointor Leakage.RejectRupture of laminate withcomplete penetration.Majority of fibers broken.Visible as lighter coloured areaof inter laminar separation.StrengthreducedWeep age failureRejectofjoint2.2 GRV /GRE Application steps:It will vary manufacturer to manufacturer. The manufacturer instructions shall be followed at site works. Check Surface Temperature, Relative Humidity, avoid direct sun light/dust during the jointing.Marking and cuttingMachining- Minimum .Grinding -0.5 MM and chambering (1: 6 slope)Wedging-Pipes/Fittings – 3 MM (max. Gap)Building up the jointsFit layers & curing (0.5 Hours : 130 to 160 Deg.C)Main reinforcement , Top layer & curingFinal curing (1.5 to 3 Hours : 130 to 160 Deg.C)Visual inspection and hardness test
NDE2019, 027, v1: ’CP-310: GRE Pipe Manufacturing Defects, Installation and NDE . . .2.3 Application Precautions5
6NDE2019, 027, v1: ’CP-310: GRE Pipe Manufacturing Defects, Installation and NDE . . .Fig. 1 Improper preparation of chemicals &shortage of belts for latching/BlanketFig.2 Shortage of thermometer ProbeFig.3 Chemical storage in proper way
NDE2019, 027, v1: ’CP-310: GRE Pipe Manufacturing Defects, Installation and NDE . . .Figure .4 Curing not done more than 24 Hours –Crack on lamination jointsFig.5 Improper end cap provided –sandcleaning is requiredFig.6 Direct sun light & no dust proof shelter duringjointingFig. 7 handling of woven materials at siteTable-2 Non Destructive Testing Methods requirements:a) Visual Testing Deformation and dimensional deviations. Surface cracks & micro cracks. Near surface delamination's, inclusions & airentrapments.b) Pressure Testing (Leak Testing) Adhesive bonded joints lacking adhesive orimproperly prepared and assembled. Inadequate cured adhesive in the bondedjoints.7
8NDE2019, 027, v1: ’CP-310: GRE Pipe Manufacturing Defects, Installation and NDE . . . Impact damageBlisters.Internal excessive of adhesive (Internalinspection).Corrosion and Erosion (Internal inspection )c) Ultrasonic Testing ( Pulse Echo)-UTAreas in bonded pipe joints lacking adhesive.Delamination's, voids.Deviations in Wall thickness(WT)- 20 %Effective WT : 8 TO 25 MM( Test Frequency : 0.25 TO 2.25 MHz)e) IRT- Infrared Thermal TestingScale build upMajor deviations in WTAreas in the joint lacking adhesive.Standard calibration blocks: Demerit and isunder R&D. Demerits : a) Cost of blinding off system b) any corrective action can causecommissioning delaysd) Radiological Testing (RT)-10 to 50 Kev Incorrect WT up to 20% deviation. Some voids, delamination’s and lack ofadhesive up to 5% deviations. Axial misalignment Excessive adhesive on inner wall of pipe atjoint. Scale build up on inside pipe. Incorrect insertion of pipes in adhesivesocketsDemerit :a) poor adhesion not detected in RTf) g) Differential Scanning calorimetry – Glasstransmission temperature measurementand Barcol hardness test ( Indirect ofmeasuring the degree of cure in Vinylester and polyester laminates andlaminated joints) Improperly mixed or cured adhesive inbonded joints. Improperly mixed or laminated joints.Figure-8 & 9 Surface Pits and Surface Void:Manufacturing defects in GRP materials.Leaking JointsAcoustic emission testing (AET)Growing crack/propagation defect detectionIn adequate structural integrityGrowth of delamination crackCrack growth in matrix materialFiber fracture and pull outInadequate curing, leading to excessivestrainsLeakage
NDE2019, 027, v1: ’CP-310: GRE Pipe Manufacturing Defects, Installation and NDE . . .Figure -10 & 11: Scratch mark in liner and Forging objects:Figure -12 & 13: End Damage and Dry joint:Figure -14 & 15: Fracture due to impact and Lack of adhesive9
10NDE2019, 027, v1: ’CP-310: GRE Pipe Manufacturing Defects, Installation and NDE . . .Figure-16 & 17 Sample failure joints at site2.4 Legends: Glass Reinforced Vinyl or Epoxy (GRV/GRE), Cathodic Protection System (CPS), Nondestructive Examination (NDE), Radiological Testing (RT), WT-Wall thickness ,3.0 ConclusionThe possible defects associated with the manufacturing & Installation of GRE/GRV pipes, fromthe point of view of human error, and or lower manufacturing skinless due to new technologyintroduction in the area. Also in this part will be concerning the defect types, causes, and theprevention or corrective action of such defects and NDE applications.Defects can occur in either the GRP material or in the Lamination & adhesive bonded joints thatmake up a piping system. Manufacturer instructions were not followed by constructor leads todefects and delay of project completion. Leak testing failures also affect completion of project andrework required to bring to acceptable limit.Effective inspection and follow the manufacturing instruction will lead to good workmanship andtimely completion of the project.4.0 References4.1 DEP 31.40.10.19 Glass –Fiber reinforced plastic pipeline and piping systems.4.2 ISO 14692 Part-4 Petroleum and Natural gas industries-Glass Reinforced Plastics (GRP)piping: Fabrication, installation & operation.4.3 Manufacturers recommendation
paper will focus the application of GRE/V Pipes in refinery construction, fabrication and erection errors and Non-destructive Examination (NDE). If the machine setup is according to the specifications in setup sheet and raw materials are tested and approved, there are normally no problems with defects on pipes and Fittings. But sometimes process