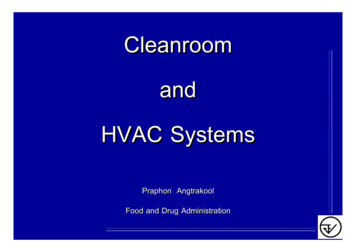
Transcription
CleanroomandHVAC SystemsPraphon AngtrakoolFood and Drug Administration
Some PIC/S GMP Deficiencies Recently ObservedXXXXXXXXXInadequate air filtration to manufacturing areasY No knowledge of grade of filters usedPotential for penicillin/cephalosporin cross contaminationY from environment and personnelChange area without mirrors/visual gowning instructionsPoorly controlled water treatment systemsEndotoxins in steriles APIsR W TribeNo cleaning validationChief GMP AuditorPoorly defined “release for supply” proceduresTGA, AustraliaJune 2002QC test data not genuineEffectiveness of GMP training not assessed1
Australia (TGA)Critical deficiency : deficiency that has produced, or may result in asignificant risk of producing, a product which is harmful to the user.Examples of critical deficiencies include : no or inadequate air filtration to minimise airbornecontaminantslack of sterilisation (or other complex process for criticalproducts) validationinadequate segregation of manufacturing of high riskproducts, such as penicillins, cephalosporins,antineoplastics, steroids, hormones, resulting in a risk ofcontamination2
Health Canada (HPFB)Critical observation : Observation describing a situation that islikely to result in a non-compliant product or a situation that mayresult in an immediate or latent health risk and any observationthat involves fraud, misrepresentation or falsification of productsor data.Premises C.02.004¡ No air filtration system to eliminate airbornecontaminants that are likely to be generated duringfabrication or packaging.¡ Generalized malfunctioning of the ventilation system (s)with evidence of widespread cross-contamination.¡ Inadequate segregation of manufacturing or testingareas from other manufacturing areas for high riskproducts.3
Health Canada (HPFB)Major observation : Observation that may result in the productionof a drug not consistently meeting its marketing authorization.Premises C.02.004 Malfunctioning of the ventilation system that couldresult in possible localized or occasional crosscontamination. Maintenance / periodic verification such as air filterreplacement, monitoring of pressure differentials notperformed. (8) Accessory supplies (steam, air, nitrogen, dustcollection, etc.) not qualified. Heat Ventilation Air Conditioning (HVAC) and purifiedwater (PW) system not qualified.4
Production Area (WHO) (1)12.30 Production areas should be effectively ventilated, with aircontrol facilities (including filtration of air to a sufficient levelto prevent contamination and cross-contamination, as wellas control of temperature and, where necessary, humidity)appropriate to the products handled, to the operationsundertaken and to the external environment. These areasshould be regularly monitored during both production andnon-production periods to ensure compliance with theirdesign specifications.12.31 Premises for the packaging of pharmaceutical productsshould be specifically designed and laid out so as to avoidmix-ups or cross-contamination.5
Production Area (PIC/S)(2)3.3 Lighting, temperature, humidity and ventilation shouldbe appropriate and such that they do not adverselyaffect, directly or indirectly, either the medicinalproducts during their manufacture and storage, or theaccurate functioning of equipment.3.12 Production areas should be effectively ventilated, withair control facilities (including temperature and, wherenecessary, humidity and filtration) appropriate both tothe products handled, to the operations undertakenwithin them and to the external environment.3.15 Premises for the packaging of medicinal productsshould be specifically designed and laid out so as toavoid mix-ups or cross-contamination.6
Questions & answers on the Australian GMP code12 The new Code does not reference a specific standard for airquality for non-sterile manufacturing areas. Could you pleaseadvise the relevant Australian or ISO standard, and thecorrect area designations and standards we should apply?There are no standards specific to non-sterile medicinemanufacture. The various grades of air quality for theproduction of non-sterile medicines will require furtherconsultation with industry before a TGA policy is issued onthis topic.7
International Society for Pharmaceutical Engineering (ISPE)¡The ISPE OSD Baseline Guide further states that there are noparticulate classification requirements for OSD facilities, such asthose that exist for aseptic processing. The level of protectionand air cleanliness for different areas should be evaluated basedon the product being manufactured, the process and theproduct’s susceptibility to degradation.XThe most common applied classification for open product zonesin a solid dosage plant is a grade D classification. This equatesto particulate level classification of ISO 14644-1 Class 8, “atrest”, measured against particles size of 0.5 µm and 5 µm8
Factors that contribute to quality productsStarting materials and packaging materials¡ Validated processes¡ Personnel¡ Procedures¡ Equipment¡ Design and quality of premises¡ Manufacturing environmentInadequacies in the above factors will lead tosub-standard products.¡9
Factors contributing to quality productsPersonnelValidated processesProceduresStarting materialsEquipmentPacking materialsPremisesEnvironment10
The manufacturing environment is critical for product quality¡¡¡¡¡¡¡LightTemperatureHumidityAir movementMicrobial contaminationParticulate contaminationUncontrolled environment can lead to product degradation product contaminationloss of product and profit11
What are contaminants ?Contaminants are¡Products or substances other than product manufactured¡Foreign products¡Particulate matter¡Micro-organisms¡Endotoxins (degraded micro-organisms)Cross-contamination is a particular case of contamination12
Cross-Contamination (1)What is Cross-Contamination ?Definition of Cross-Contamination:Contamination of a starting material, intermediate product,or finished product with another starting material or productduring production.(WHO) Annex 1, Glossary13
Cross-Contamination (2)From where does Cross-Contamination originate?¡Poorly designed air handling systems and dust extractionsystems¡Poorly operated and maintained air handling systems anddust extraction systems¡Inadequate procedures for personnel and equipment¡Insufficiently cleaned equipment14
Cross-Contamination ( 3 torsCrossContaminationProductfromEquipment15
Cross-Contamination (4)Cross-contamination can be minimized by :¡Personnel procedures¡Adequate premises¡Use of closed production systems¡Adequate, validated cleaning procedures¡Appropriate levels of protection of product¡Correct air pressure cascade16
Level of Protection ConceptDefines environmental requirements¡Helps prevent contamination and cross-contamination¡Allows production under optimal hygiene conditions¡Takes into account product sensitivity to contamination therapeutic risk17
Therapeutic risksCleanroom Class A / BCleanroom Class C18Cleanroom Class DOthersManufacturing EnvironmentrequirementsTherapeutic risks
Levels of ProtectionParameters to be defined :¡Air cleanliness requirements (filters type and position, air flowpatterns, air changes, pressure differentials, contaminationlevels by particulate matter and micro-organisms)¡Personnel and material transfer methods¡Permitted operations¡Building design and finishes19Annex 1, 17.3, 17.4
Dust classificationDust can be roughly classified by size according to :XCoarse dust with size range of 50 to 500 µm (settles rapidly)XFine dust with size range of 1 to 50 µm (settles slowly)XUltra fine dust with size range 0.5 µm to 1.0 µm (remainsconstantly suspended)XParticles 0.05 µm are considered to vapors and not dustOnly dust particles that are greater than 10 µm are visible to thenaked eye with good lighting and good eyesight20
Sources of Contamination (General information only)Type ofcontaminationExampleDerived from(Examples)Dealt with by(Examples)- Non-viable(particulate)- Metal specks- Clothing fiber- Equipment- People’s clothing- Outside air- Water supply- Airborne particles are HEPA filtered- Contact part are cleaned andsterilized- Water purification systems- Viable(micro-organism)- Bacteria- Yeast molds- People- Water- Outside air- Equipment, tools- Excipients- Active ingredients- Limit aseptic core interventions- Airborne particles are HEPA filtered- Sterile filtration of solutions (0.2 µm)- Steam sterilization or irradiation ofcomponents- Endotoxins(not normallyassociated withairborne bacteria)- Arising from cellwall debris fromcertainorganisms (oftenwater borne)- Wet equipmentchange parts, orcontainer/closureafter a period oftime exposure- Caustic soda solution with heat- High temperature ( 200 0C) timedependent21
Particles SheddingNo. of particlegenerated/minActivitySitting or standing stillSitting, Small movement of arms or headSitting, moving arms , legs or headStanding upWalking slowlyWalking normallyWalking with speed (2.5m/s)Performing 07,500,00010,000,00015-30 x 1,000,000
Hand & NeckBacterial skin populationsContact plate methodSiteForeheadTempleNoseUpper lipCheekneckPlate count348560TNTCTNTC58431623
Bacterial skin populationsContact plate methodUpper trunkand armsSiteUpper armElbowForearmWristhand24Plate count42841TNTC224
Bacterial skin populationsContact plate methodLower Trunkand ArmsSiteShoulderBreastPerineumHipInner thighPlate count4350TNTC104TNTC25
What is Cleanroom ?XFederal Standard 209 E“A room in which the concentration of airborne particles iscontrolled and which contains one or more clean zone”XISO 14644-1“A room in which the concentration of airborne particles iscontrolled, and which is constructed and used in a manner tominimize the introduction, generation, and retention of particlesinside the room and in which other relevant parameters, e.g.temperature, humidity, and pressure, are controlled as necessary”26
What is Clean area ?XWHO TRS 908, 2003, Annex 4“An area with defined environmental control of particulate and microbialcontamination, constructed and used in such a way as to reduce theintroduction, generation, and retention of contaminants within the area”XPIC/S (1 July 2004)“An area with defined environmental control of particulate and microbialcontamination, constructed and used in such a way as to reduce theintroduction, generation, and retention of contaminants within the area”Note : The different degree of environmental control are defined in theSupplementary Guidelines for the Manufacture of sterile medicinalproducts27
Airborne particulate classification for manufacture ofsterile pharmaceutical preparation (WHO)GradeAt restIn operationMaximum number of particlespermitted/m 3Maximum number of particlespermitted/m 30.5 – 5.0 µm 5.0 µm0.5 – 5.0 µm 5.0 µmA3500035000B35000350 0002000C350 00020003 500 00020 000D3 500 00020 000Not definedNot definedWHO Technical Report Series, No. 902, 2002 Annex 6Good manufacturing practices for sterile pharmaceutical products28
ISO airborne particulate cleanliness classesMaximum permitted number of particles/m3 equal to or aboveISO 14644-1ClassAt restIn operation0.5 µm5 µm0.5 µm5 µmClass 5 (LF)3 500303 50030Class 5 (Tur.)3 5003035 000300Class 635 000300350 0003 000Class 7350 0003 0003 500 00030 000Class 83 500 00030 00035 000 000300 000Class 935 000 000300 000Not definedNot definedLF uni-directional flow or laminar air flow ; Tur. turbulent or non uni-directional flow29
ISO airborne particulate cleanliness classes for cleanroom and clean zonesClassificationnumbers (N)Maximum concentration limits (particles/m3 of air) for particles equal to andlarger than the considered sizes shown below0.1 µm0.2 µm0.3 µm0.5 µm1 µm5.0 µmISO Class 1102ISO Class 210024104ISO Class 31000237102358ISO Class 410 0002370102035283ISO Class 5100 00023 70010 200352083229ISO Class 61 000 000237 000102 00035 2008320293ISO Class 7352 00083 2002930ISO Class 83 520 000832 00029 300ISO Class 935 200 0008 320 000293 00030
ISO classification is based on the equation :N2.08Cn 10 [0.1/D]Cn represents the maximum permitted concentration (in particle/m3 of air) ofairborne particles that are equal to or larger than the considered particle size;Cn is rounded to the nearest whole numberN is the ISO classification number, which shall not exceed the value of 9.Intermediate ISO classification numbers may be specified, with 0.1 thesmallest permitted increment of ND is the considered particle size in µm0.1 is a constant with a dimension of µm31
International Standard : ISO 14644ISO 14644 consists of the following parts, under the generaltitle Cleanrooms and associated controlled environments :¡ Part 1 : Classification of air cleanliness¡ Part 2 : Specifications for testing and monitoring toprove continued compliance with ISO 14644-1¡ Part 3 : Metrology and test methods32
International Standard : ISO 14644¡ Part 4 : Design, construction and start-up¡ Part 5 : Operation¡ Part 6 : Term and definitions¡ Part 7 : Separative devices (clean air hoods, gloveboxes,isolators and mini-environments)¡ Part 8 : Classification of airborne molecular contamination33
Comparison of different airborne particulate classification systemfor clean areasWHOUnited StatesUnited StatesISO/TCEECGMP(209E)(Customary)(209)GMPGrade AM 3.5class 100ISO 5Grade AGrade BM 3.5class 100ISO 5Grade BGrade CM 5.5class 10 000ISO 7Grade CGrade DM 6.5class 100 000ISO 8Grade DEEC : European Commission;ISO/TC : International Organization for Standardization Technical CommitteeWHO Technical Report Series, No. 902, 2002 Annex 6Good manufacturing practices for sterile pharmaceutical products34
Comparison of ISO 14644-1 and some replaced US StandardsSome standard replaced by EN ISO 14644-1 : 1999ISO 999Classesper m 3 1997CleanlinessAFNOR1989ClassesVDI 20831990ClassesBS 52951989ClassesJIS B 99201989Classes123456783.510M135M 1.5100M2352M 2.51 000M33 520M 3.510 000M435 200M 4.5100 000M5352 000M 5.51 000 000M63 520 000M 6.510 000 0009100 000 000021131024100A B*4 0001 0003E or F54G or H610 000C*400 0005J7100 000D*4 000 0006K8L9M7M 7.51 000 00040 000 00035
Type of Clean Areas (1)High efficiency air filterProductionequipmentAir extract1. Conventional (non-unidirectional flow or turbulently ventilated) the air beingsupplied by air supply diffusers or filters in the ceiling36
Conventionally ventilated clean roomAIR CONDITIONINGPLANTFRESH S-OVERBENCHPASS-THROUGH GRILLES37CLEANROOM
Type of Clean Areas (2)Cleanroom differs from an ordinary ventilated room in a number of ways :X Increased air supply- office or shop (2 - 10 air change per hours)- cleanroom (20 - 60 air change per hours)XHigh Efficiency Filter- High Efficiency Particle Air (HEPA) 99.97 % efficient in removing particlesgreater than 0.3 µmX Terminal air filterXRoom pressurization and pass-though grilles- pass-through grilles or dampers will usually be seen at a low level on walls ordoors38
Type of Clean Areas (3)High efficiency air filterProductionequipmentAir extract2. Unidirectional flow (laminar flow) clean air is supplied from a bank of highefficiency filters and passes in a unidirectional manner though the room39
Type of Clean Areas (4)High efficiency air filterProductionequipmentAir extract3. Mixed flow clean room with non- unidirectional flow in the room andunidirectional air flow protection the critical processing area40
Type of Clean Areas (5)High efficiency air filterProductionIsolator used toprotect processareaequipmentAir extract4. Isolators :(microenvironment) these are used within a cleanroomto give the highest level of protection against contamination.41
Cleanroom conditionXas built : condition where the installation is complete with allservices connected and functioning but with no productionequipment, materials, or personnel presentXat rest : condition where the installation is complete withequipment installed and operation in a manner agree upon bythe customer and supplier, but with no personnel presentXoperational : condition where the installation is functioning inthe specified manner, with the specified number of personneland working in the manner agreed upon42
Definition of Conditionsas builtat restin operationairairair43
Cleanroom classification standards can be divided into the followingsubgroups given belowEngineering ClassesThese originate from Federal Standard 209,and are based on inanimate particles in airBiocontamination(Pharmacy) ClassesThese were originally based on FederalStandard 209 but developed to include livingmicroorganisms. These standards are requiredfor hygenic or sterile production. Guide to GoodManufacturing Practice and the CEN/ISObiocontamination standards cover this field.Containment ClassesThese are for areas where hazardouscontaminants are used or can occur.44
Type of Pharmaceutical ProcessesXInjectablesAqueous productsY Freeze-dried productsY Powder productsY- % RH- high potencyXTopicalsYXclass 100 000Oral ProductsPharmaceutical manufacturing facilities where productsare exposed to the environment should be classified as“cleanrooms”Y cross-contamination between products or betweenproduct and peopleY45
Level of Protection (Oral solid dosage form) (1)XLevel 1 (General) : An area with normal housekeeping and maintenance.(e.g. Warehousing, Secondary Packing)XLevel 2 (Protected) : An area in which steps are taken to protect theexposed drug substance from contamination or degradation. (e.g.Manufacturing, Primary Packing, Dispensing, etc.)XLevel 3 (Controlled) : An area in which specific environmental conditionsare defined, controlled and monitored to prevent contamination ordegradation of the drug substance.46
Level of Protection (Oral solid dosage form) (2)XLevel 1 protection and Pharmaceutical conditions can beequated with an ISO Class 9 condition.XThe most common applied classification for openproduct zones in a solid dosage plant is a grade Dclassification.XGrade D equates to particulate level classification ofISO 14644-1 Class 8, at rest, measured against particlessize of 0.5 µm and 5 µm47
Level of ProtectionTypical ZoneGMP GuidesISO Class EquivalentTypical Dress CodeStreet, canteenExternalExternalOutdoor clothesReceipt & dispatchLevel 1 or UnclassifiedISO Class 9Appropriate to areaWarehousing, officesLevel 1 or UnclassifiedISO Class 9Appropriate to areaWeighing & dispensingLevel 2 – backgroundLevel 3 – open productISO Class 8 – backgroundISO 6 or 7 – open productClean garmentsBlendingLevel 2 or 3ISO Class 8 or 7Clean garmentsGranulationLevel 2 or 3ISO Class 8 or 7Clean garmentsMillingLevel 3ISO Class 8 or 7Clean garmentsEncapsulation &compressionLevel 2ISO Class 8Clean garmentsCoatingLevel 2ISO Class 8Clean garmentsPrimary packingLevel 2 or 3ISO Class 8 or 7Clean garmentsSecondary packingLevel 1 or PharmaceuticalISO Class 9Captive coat, hat andovershoesNon-sterile processingControlled or Class 100000(in operation)ISO Class 8Clean garmentsRooms where filling takesplaceClean or Class 10000(in operation)ISO Class 6 or 7Sterile garmentsPoint of fill or other asepticoperationsCritical or Class 100(in operation)ISO Class 5Sterile garmentsChange rooms & airlocksThe same classification as thearea they serveThe same classification as thearea they serveChange to garments for thehigher classification48
Parameters influencing Levels of Protection (1)Number of particles in the airX Number of micro-organisms in the air or on surfacesX Number of air changes for each roomX Air velocityX Air flow patternX Filters ( type, position )X Air pressure differentials between roomsX Temperature, humidityX49
Parameters influencing Levels of Protection (2)Air handling systems:Are the main tool for reaching required parametersX But are not sufficient as suchX Need for additional measures such asXYYYappropriate gowning (type of clothing, proper changing rooms)validated sanitationadequate transfer procedures for materials and personnelAnnex 1, 17.10 to 17.1650
Main subsystemsExhaust air treatmentSilencer Flow rate controller FanFresh air treatment(make-up air) FilterTerminal air treatmentat production room levelProduction RoomCentral air handling unit51
Overview componentsExhaust Air GrilleFlow rate controllerSilencerWeather louvreHumidifierCooling coilwith dropletseparatorHeatingcoilFilterControl damperHeaterPrefilterFan Terminal filterSecondary FilterRe-circulated air52Production Room
Characteristics of air handling systemsIn the following slides, we will study alternatives inair handling systemsX Turbulent or uni-directional airflowsX Filter positionX Air re-circulation vs fresh airX Return air systems (positions)X Overpressure requirements53
Air flow patterns (1)Turbulentdilution of dirty airUni-directional / laminardisplacement of dirty air0.45 m/sAnnex 1, 17.354
Air flow patterns (2)Filtered air entering a production room or covering aprocess can beX turbulentX uni-directional (laminar)YGMP aspecteconomical aspectNew technologies: barrier technology/ isolator technology.YAnnex 1, 17.3, 17.455
Air flow patterns (3)PrefilterAHUMain filter12TurbulentUni-directionalAnnex 1, 17.3563Turbulent
Positioning of filters (1)PrefilterAHUMain filterCeilingexhausts21Low level exhausts573
Positioning of filters (2)Final filterAHUPrefilter1258
Air re-circulationThe filtered air entering a production room can beX100% exhausted orXa proportion re-circulatedQ GMP aspectQ Economical reasonsAnnex 1, 15.10, 17.2459
Ventilation with 100% fresh air(no air re-circulation)Washer (optional)Exhaust UnitWCentral Air Handling UnitProduction RoomsAnnex 1, 17.2460
Ventilation with re-circulated air make-up airExhaust UnitCentral Air Handling UnitReturn air61
Central Air Handling UnitControl damper for air flowHumid room airAdsorber wheelRegeneration airDry airAHU with fan VariableSpeed ControllerHumid room airFilter PressureGaugesAir heaterDe-humidificationAir handling unit62
HumidifierSilencer63Heating andcooling units
Air flow patternsXSupply air diffusers of the high induction type should notbe used in a cleanroomXAir should be exhausted from rooms at a low level.XRecommended supply air diffuserYPerforated plate diffuserYSwirl diffuser64
Induction diffuser (not recommended)High induction office type diffuser(avoid)Induced room airmixing with supply airReturn AirReturn Air65
Perforated plate diffuser (recommended)Perforated PlatediffuserReducedInductionof airReturn AirReturn Air66
Swirl diffuser (recommended)SwirldiffuserReducedInductionof airLow induction swirl diffuser(preferred)Return AirReturn Air67
Swirl Type air diffusers with terminal filters12341 Filter2 Tightening frame3 Register outlet4 Screw fixation for register68
Components (1)¡Weather louvre9To prevent insects, leaves, dirt andrain from entering¡Silencer9To reduce noise caused by aircirculation¡Flow rate controller9Automated adjustment of volume ofair (night and day, pressure control)¡Control damper9Fixed adjustment of volume of air69
Components (2)¡Heating unit9To heat the air to the proper temperature¡Cooling unit/dehumidifier9To cool the air to the required temperature or to¡Humidifier9To bring the air to the proper humidity, if too low¡Filters9To eliminate particles of pre-determinedremove moisture from the airdimensions and/or micro-organisms¡Ducts9To transport the air70
Problems with components¡Flow rate controllerÊBlocked¡Control damperÊPoorly adjusted, bad pressure differential system¡HumidifierÊBad water/steam quality/poor drainage¡Cooling batteryÊNo elimination of condensed water/poor drainage¡FiltersÊIncorrect retention rate/damaged/badly installed¡DuctsÊInappropriate material/internal insulator leaking71
The Containment ClassesClassExplanationExampleBL 1Normal laboratory standardOrdinary biochemistrylabs, School anduniversity labsBL 2Special training and routines to prevent lab infections.Appropriate waste handlingDiagnostic labsHealth labBL 3Special lab with negative pressureAir locks for people and materialAutoclave in the roomAll work done in safety cabinetSpecial decontamination of wasteSpecial safety labsTuberculosis labsBL 4Special labs with total separation between humansand microorganism in every respect, negativepressure, sterilizationHigh risk labs72
Reference1. Good manufacturing practices for biological products. In : WHO Expert Committee on BiologicalStandardization. Forty-second report. Geneva, World Health Organization, 1992, Annex 1 (WHOTechnical Report Series, No. 822)2. Good manufacturing practices for pharmaceutical products : main principles. In : WHO ExpertCommittee on Specification for Pharmaceutical Preparations. Thirty-seventh report. Geneva, WorldHealth Organization, 2003, Annex 4 (WHO Technical Report Series, No. 908)3. Good manufacturing practices for sterile pharmaceutical products. In : WHO Expert Committee onSpecification for Pharmaceutical Preparations. Thirty-sixth report. Geneva, World HealthOrganization, 2002, Annex 6 (WHO Technical Report Series, No. 902)4. Deryck S. Supplementary guidelines on Good manufacturing practices for Heating, Ventilation andAir Condition (HVAC) Systems. Working document QAS/02.048. Geneva, World HealthOrganization, 2003 (unpublished document)5. W. Whyte. Cleanroom Design, 2nd ed. Wilshire (England), Antony Rowe Ltd., 19996. Pharmaceutical Engineering Guides for New Renovated Facilities Volume 3 Sterile ManufacturingFacilities, First Edition. International Society for Pharmaceutical Engineering, 199973
XInadequate air filtration to manufacturing areas YNo knowledge of grade of filters used XPotential for penicillin/cephalosporincross contamination Yfrom environment and personnel XChange area without mirrors/visual gowning instructions XPoorly controlled water treatment systems XEndotoxins in steriles APIs XNo cleaning validation XPoorly defined "release for supply" procedures