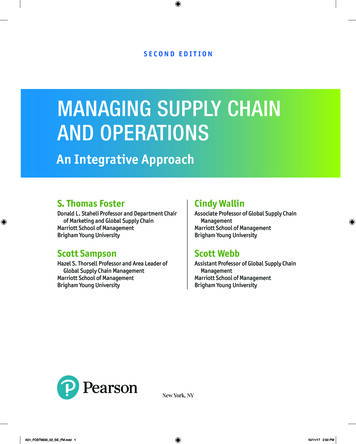
Transcription
SECOND EDITIONMANAGING SUPPLY CHAINAND OPERATIONSAn Integrative ApproachS. Thomas FosterCindy WallinDonald L. Staheli Professor and Department Chairof Marketing and Global Supply ChainMarriott School of ManagementBrigham Young UniversityAssociate Professor of Global Supply ChainManagementMarriott School of ManagementBrigham Young UniversityScott SampsonScott WebbHazel S. Thorsell Professor and Area Leader ofGlobal Supply Chain ManagementMarriott School of ManagementBrigham Young UniversityAssistant Professor of Global Supply ChainManagementMarriott School of ManagementBrigham Young UniversityNew York, NYA01 FOST9830 02 SE FM.indd 110/11/17 2:50 PM
Vice President, Business, Economics, and UK Courseware: DonnaBattistaDirector of Portfolio Management: Stephanie WallEditorial Assistant: Linda Siebert AlbelliVice President, Product Marketing: Roxanne McCarleySenior Product Marketer: Product Marketer: Kaylee CarlsonProduct Marketing Assistant: Marianela SilvestriManager of Field Marketing, Business Publishing:Adam GoldsteinExecutive Field Marketing Manager: Field MarketingManager: Nicole PriceVice President, Production and Digital Studio, Arts andBusiness: Etain O’DeaDirector of Production, Business: Jeff HolcombManaging Producer, Business: Melissa FeimerContent Producer: Yasmita HotaOperations Specialist: Carol MelvilleDesign Lead: Kathryn FootManager, Learning Tools: Brian SuretteContent Developer, Learning Tools: Lindsey SloanManaging Producer, Digital Studio and GLP, MediaProduction and Development: Ashley SantoraManaging Producer, Digital Studio: Diane LombardoDigital Studio Producer: Regina DaSilvaDigital Studio Producer: Alana ColesDigital Content Project Lead: Courtney KamaufProject Management: Thistle Hill Publishing ServicesInterior and Cover Design: Cenveo Publisher ServicesCover Art: Steve Vidler/Alamy Stock Photo; Wavebreakmedia/Shutterstock; Daryl Benson/Photodisc/Getty Images; PixieMe/Shutterstock; Foodcollection/Getty Images; Ixefra/Getty Images;Wavebreakmedia/ShutterstockPrinter/Binder: LSC Communications, Inc./ KendalvilleCover Printer: Phoenix Color/HagerstownMicrosoft and/or its respective suppliers make no representations about the suitability of the information contained in the documents and related graphicspublished as part of the services for any purpose. All such documents and related graphics are provided “as is” without warranty of any kind. Microsoftand/or its respective suppliers hereby disclaim all warranties and conditions with regard to this information, including all warranties and conditions ofmerchantability, whether express, implied or statutory, fitness for a particular purpose, title and non-infringement. In no event shall Microsoft and/orits respective suppliers be liable for any special, indirect or consequential damages or any damages whatsoever resulting from loss of use, data or profits,whether in an action of contract, negligence or other tortious action, arising out of or in connection with the use or performance of information availablefrom the services.The documents and related graphics contained herein could include technical inaccuracies or typographical errors. Changes are periodically added to theinformation herein. Microsoft and/or its respective suppliers may make improvements and/or changes in the product(s) and/or the program(s) describedherein at any time. Partial screen shots may be viewed in full within the software version specified.Microsoft and Windows are registered trademarks of the Microsoft Corporation in the U.S.A. and other countries. This book is not sponsored or endorsedby or affiliated with the Microsoft Corporation.Copyright 2019, 2016 by Pearson Education, Inc. or its affiliates. All Rights Reserved. Manufactured in the United States of America. This publication is protected by copyright, and permission should be obtained from the publisher prior to any prohibitedreproduction, storage in a retrieval system, or transmission in any form or by any means, electronic, mechanical, photocopying, recording, or otherwise. Forinformation regarding permissions, request forms, and the appropriate contacts within the Pearson Education Global Rights and Permissions department,please visit www.pearsoned.com/permissions/.Acknowledgments of third-party content appear on the Credits page, which constitutes an extension of this copyright page.PEARSON, ALWAYS LEARNING, and MYLAB are exclusive trademarks owned by Pearson Education, Inc. or its affiliates in the U.S. and/or other countries.Unless otherwise indicated herein, any third-party trademarks, logos, or icons that may appear in this work are the property of their respective owners, and anyreferences to third-party trademarks, logos, icons, or other trade dress are for demonstrative or descriptive purposes only. Such references are not intended toimply any sponsorship, endorsement, authorization, or promotion of Pearson’s products by the owners of such marks, or any relationship between the ownerand Pearson Education, Inc., or its affiliates, authors, licensees, or distributors.Library of Congress Cataloging-in-Publication DataNames: Foster, S. Thomas, author.Title: Managing supply chain and operations : an integrative approach / S. Thomas Foster, Brigham Young University, Scott Sampson, Brigham Young University,Cindy Wallin, Brigham Young University, Scott Webb, Brigham Young University.Description: Second Edition. New York : Pearson, NY. [2017] Revisededition of the authors’ Managing supply chain and operations, [2016] Includes bibliographical references and index.Identifiers: LCCN 2017050842 ISBN 9780134739830 (hardcover) ISBN0134739833 (hardcover)Subjects: LCSH: Production management. Production control. Business logistics—Management. Industrial management.Classification: LCC TS155 .F67 2017 DDC 658.5—dc23LC record available at https://lccn.loc.gov/2017050842117ISBN 10: 0-13-473983-3ISBN 13: 978-0-13-473983-0A01 FOST9830 02 SE FM.indd 210/11/17 2:50 PM
For Camille—T. F.For Kristen—S. S.For David and Joyce Wallin—C. W.For my best friend, Mary—S. W.A01 FOST9830 02 SE FM.indd 310/11/17 2:50 PM
About the AuthorsS. Thomas Foster is the Donald Staheli Professor and department chair of marketing andglobal supply chain management at Brigham Young University’s Marriott School of Management. He is an internationally recognized expert in quality and global supply chain management and has experience in manufacturing, financial services, and international oil exploration.He has consulted for more than 30 organizations, including Eaton/Cutler Hammer, HewlettPackard, Heinz Frozen Foods, Hyundai Corporation, and the U.S. Department of Energy.Foster has served on the editorial boards of the Journal of Operation Management and DecisionSciences and is Editor in Chief of the Quality Management Journal. He has published more than 80articles in journals such as Decision Sciences, Journal of Operations Management, International Journalof Production Research, and Quality Management Journal. His book Quality Management: Integratingthe Supply Chain is an international best seller. He recently served on the Malcolm BaldrigeBoard of Overseers and was awarded the prestigious Instructional Innovation Award fromthe Decision Sciences Institute.Scott Sampson is the Hazel S. Thorsell Professor of global supply chain management with theMarriott School of Management at Brigham Young University. He teaches MBA, executive MBA,and undergraduate courses in services management and customer relationship management.Sampson is the author of the books Understanding Service Businesses and Essentials of ServiceDesign and Innovation. His award-winning research involves service design paradigms, servicequality measurement, and service supply chains. He has published research in leading academic journals, including Management Science, Production and Operations Management, OperationsResearch, Decision Sciences, and Journal of Operations Management. He received his MBA and PhDdegrees from the University of Virginia and taught at Florida State University prior to joiningthe Brigham Young University faculty.Cindy Wallin is an associate professor of global supply chain management at Brigham YoungUniversity’s Marriott School of Management. She earned her PhD in supply chain management from the W. P. Carey School of Business at Arizona State University. Wallin’s researchfocuses on buyer-supplier interfaces in the form of trust-based relationships, informationsharing, collaboration, and collaborative inventory management approaches. Her researchhas been published in various journals, including Decision Sciences Journal, Journal of Supply ChainManagement, Quality Management Journal, and Journal of Business Logistics.Before pursuing her doctoral studies, Wallin was a commodity team manager for IntelCorporation. During her eight years at Intel, she also held the positions of senior buyer,purchasing manager, stores manager, and commodity manager. Before her graduate studies,Wallin also worked as an auditor for the Defense Contract Audit Agency.Scott Webb is an associate professor of global supply chain management at Brigham YoungUniversity and specializes in logistics management. He received his PhD in logistics and operations management from the Eli Broad College of Business at Michigan State University. Inaddition to his PhD, he earned an MS degree in logistics management from the Air ForceInstitute of Technology and a BA in experimental psychology from the College of Idaho.During his Air Force career, Webb worked on both base- and Pentagon-level assignments. He separated from active duty military service in 2008 at the rank of major and afterearning both AF Commendation Medals and the AF Meritorious Service Medal.ivA01 FOST9830 02 SE FM.indd 410/11/17 2:50 PM
Brief Contents1Integrating Supply Chain and Operations ManagementChapter 1Chapter 22Chapter 3Chapter 547Product and Process Design and Mapping 48Service Design 92Customer Relationship Management 120Impacting Supply Chain and Operations PerformanceChapter 6Chapter 7Chapter 8Chapter 9Chapter 10Chapter 114Introduction to Supply Chain and Operations Management 2Supply Chain and Operations Strategy 21Innovating Supply Chain and OperationsChapter 431141Strategic Sourcing 142Supplier Management 166Demand Management and Forecasting 195Inventory Management Fundamentals andIndependent Demand 242Sales and Operations Planning and EnterpriseResource Planning 273Logistics 305Improving Supply Chain and Operations Management PerformanceChapter 12Chapter 13Chapter 14Chapter 15Project Management 340Supply Chain Quality Management 381Statistical Process Control 409Lean and Six Sigma Management and Leading Change339452vA01 FOST9830 02 SE FM.indd 510/11/17 2:50 PM
ContentsPreface1xviIntegrating Supply Chain and Operations Management1Chapter 1 Introduction to Supply Chain and OperationsManagement21 Understand Why You Are Studying Supply Chain and Operations ManagementProcesses 4Supply Chain Globalization352 Define, Understand, and Apply the Components of Supply Chain and OperationsManagement 8Supply Chain Management 9Supply Chain Flows 10Service Supply Chains 11Operations Management 11Combining Supply Chain and Operations ManagementDeveloping Skills for Your Career 14123 Explain the Integrative Model for Supply Chain and Operations ManagementThe Operating Core 15Upstream Collaboration 16Downstream Collaboration 16Logistics, Analytics, and Quality ManagementStrategic Integration 1715174 Explain the Four I’s17Impacting 17Improving 17Innovating 17Integrating 18Supplier Responsibility at Apple18Summary 18 Key Terms 19 Integrative LearningExercise 19 Integrative Experiential Exercise 19 DiscussionQuestions 19 Case: Williamston Manufacturing20Chapter 2 Supply Chain and Operations Strategy1 Understand and Use Generic SC&O StrategiesGeneric Strategies 22Alignment 23Assessing Customer Value2122252 Explain How to Apply SC&O Strategy Process and ContentHoshin Kanri Strategic PlanningSC&O Strategy Content 273 Supply Chain Strategy262730viA01 FOST9830 02 SE FM.indd 610/11/17 2:50 PM
viiContentsChanges in Strategy 30Types of Relationships 314 Execute Strategy32Aligning Strategic Levels 32Aligning Incentives 33Focusing on Process 345 Understand and Apply Strategic Metrics and Measurements36Correct Strategic Behavior 36Actionable and Predictive Metrics 36Commonly Used Supply Chain Metrics 37Systems Thinking 376 Describe the Changing Strategic Environment38Analytics 38Globalization 38Sustainability 39Innovation 40Summary 43 Key Terms 44 Integrative LearningExercise 44 Integrative Experiential Exercise 45 DiscussionQuestions 45 Case: Zara246Innovating Supply Chain and Operations47Chapter 3 Product and Process Design and Mapping1 Understand and Explain the Steps of Process DesignProcesses and Extended ProcessesProcess Choice 50The Process Continuum 51Break-Even Analysis 54484949SOLVED PROBLEM 3.1 Using Break-Even Analysis to Evaluate an Investmentin Processes and Equipment552 Understand and Explain the Steps of Process Mapping and Layout PlanningExtended Process Maps for Supply ChainsHybrid Layouts 57Line Balancing 61SOLVED PROBLEM 3.2 Line Balancing in ActionDesigning Functional Layouts56576265SOLVED PROBLEM 3.3 Load-Distance Model in ActionSOLVED PROBLEM 3.4 Muther’s Grid in Action66683 Illustrate the Different Elements of Product Design69Product Life Cycle 70Research and Development 71Product Design Process 714 Understand and Employ Quality Function DeploymentConcurrent Design Teams 75Design for Manufacture MethodDesign for Maintainability 76Designing for Reliability 7775SOLVED PROBLEM 3.5 Series ReliabilityA01 FOST9830 02 SE FM.indd 7747910/11/17 2:50 PM
viiiContentsSOLVED PROBLEM 3.6 Reliability Measurement Failure RatesSOLVED PROBLEM 3.7 System Availability79805 Apply Green Design to Your Process and Product DesignDesign for Reuse 81Other Green Design Concepts8181Summary 82 Key Terms 83 Integrative LearningExercise 83 Integrative Experiential Exercise 84 DiscussionQuestions 84 Solved Problems 84 Problems 87 Case: Hamilton ElectronicsChapter 4 Service Design90921 Understand the Relationships between Services and Tangibles2 Identify and Apply the Key Elements of Service Design9394Designing for Service Quality 95Designing for Service Recovery 96B2B versus B2C Services 96Customer-Interactive Processes 97Offerings and Experiences 973 Understand and Apply the Process Chain Network (PCN) Toolfor Service Design 98Process Chain Networks 99Process Positioning 100Three Process Principles 101Steps in Developing a PCN Diagram102SOLVED PROBLEM 4.1 PCN Diagrams in Action1024 Describe and Use the Planning Service Capacity for Uncertain Demand103Capacity Components 103Capacity Planning Tools 105SOLVED PROBLEM 4.2 The Newsvendor Problem in Action1065 Apply Queuing Theory107Queuing Psychology 107Queue Systems and Service StationsWait Times 108107SOLVED PROBLEM 4.3 Model I in Action for a Single-Phase Queue with a Single Serverand Exponential Service Times110SOLVED PROBLEM 4.4 Model II in Action for a Single-Phase Queue with a Single Serverand Constant Service Times110SOLVED PROBLEM 4.5 Model III in Action for a Multiserver System with Exponential ServiceTimes111Summary 113 Key Terms 114 Integrative LearningExercise 114 Integrative Experiential Exercise 114 DiscussionQuestions 114 Solved Problems 115 Problems 116 Case: XLG Enterprises118Chapter 5 Customer Relationship Management1201 Understand and Apply Customer Relationships and SystemsCustomer Relationship Management SystemsCustomer Relationships 123CRM Processes 126A01 FOST9830 02 SE FM.indd 812112210/11/17 2:50 PM
ixContents2 Learn the Techniques to Improve Customer ServiceUnderstanding and Meeting Customer ExpectationsProviding Fail-Safe Services 128Providing Service Guarantees 128Measuring Service Performance 129Managing Customer Complaints 131SOLVED PROBLEM 5.1 Net Promoter Scores in ActionRecovering from Service Failures1271271311323 Change Relationships through Servitization4 Manage Service Supply Chains134135Summary 137 Key Terms 138 Integrative LearningExercise 138 Integrative Experiential Exercise 138 DiscussionQuestions 138 Solved Problem 139 Problems 139 Case: Can CRM Help a New Start-Up Business?3140Impacting Supply Chain and Operations PerformanceChapter 6 Strategic Sourcing1411421 Understand the Origins of the Purchasing Profession2 Describe the Effect of Strategic Sourcing on a FirmReducing the Cost of Purchased Products and ServicesSOLVED PROBLEM 6.1 Economics of PurchasingThe Quality of Purchased Goods and ServicesCost of Development and Design 1481451451461473 Apply the Portfolio Approach to Strategic SourcingCategory SegmentationRoutine Items 151Leverage Items 151Bottleneck Items 152Critical Items 1521441491494 Master the Tools of Strategic Cost Management152Spend Analysis 153Price Analysis 154SOLVED PROBLEM 6.2 Price Analysis in ActionCost Analysis 155Total Cost of Ownership Analysis154155SOLVED PROBLEM 6.3 Total Cost of Ownership156Total Cost of Ownership and Outsourcing Decisions158SOLVED PROBLEM 6.4 Total Cost of Ownership and Outsourcing158Summary 159 Key Terms 160 Integrative LearningExercise 160 Integrative Experiential Exercise 160 DiscussionQuestions 160 Solved Problems 161 Problems 163 Case: Hazeltonn Industries164Chapter 7 Supplier Management1661 Understand the Importance of Identifying and Applying the Correct Specificationfor Materials, Services, and Type of Business RelationshipA01 FOST9830 02 SE FM.indd 916810/11/17 2:50 PM
xContentsIdentifying the Need for Materials 168Identifying the Need for Services 169Identifying the Need for a Type of Relationship1692 Make Informed Supplier Selection Decisions171Identifying Supplier Requirements with Weighted-Factor AnalysisSOLVED PROBLEM 7.1 Creating a Weighted-Factor AnalysisSearching for Potential SuppliersSupplier Evaluation 176172174175SOLVED PROBLEM 7.2 Supplier Evaluation Using Weighted-Factor AnalysisNegotiating the Agreement1761783 Create and Develop Constructive Supplier Relationships179Identifying Suppliers to Develop 179Forming a Cross-Functional Team 180Involving Top Management 180Identifying Opportunities 180Defining Key Metrics and Cost Sharing 181Agreeing on Projects and Resources 181Monitoring Status and Modifying 1814 Provide Constructive Supplier Feedback183Designing and Implementing the Supplier ScorecardSOLVED PROBLEM 7.3 Supplier Scorecard DesignDelivery and Cost AssessmentSupplier Awards 187183184186Summary 188 Key Terms 189 Integrative LearningExercise 189 Integrative Experiential Exercise 189 DiscussionQuestions 189 Solved Problems 190 Problems 191 Case: Rockhurst Company194Chapter 8 Demand Management and Forecasting1 Apply the Fundamentals of Demand Management2 Understand and Apply Time Series ForecastingComponents of a Time Series 200Forecasting and Bullwhips 201Types of Forecasting Models 202Judgmental or Experiential Forecasting1972002023 Understand and Apply Naive Forecasting MethodsSimple Moving Average205205SOLVED PROBLEM 8.1 Using the Moving AverageWeighted Moving Average195205206SOLVED PROBLEM 8.2 Weighted Moving AverageSingle Exponential Smoothing206207SOLVED PROBLEM 8.3 Single Exponential SmoothingDouble Exponential SmoothingSOLVED PROBLEM 8.4 Double Exponential SmoothingMeasures of Forecasting Error208209209210SOLVED PROBLEM 8.5 Measures of Forecasting Error2114 Understand and Apply Time Series Forecasting Using RegressionTime Series Forecasts Using Simple Linear RegressionSOLVED PROBLEM 8.6 Using Simple Linear RegressionA01 FOST9830 02 SE FM.indd 1021221321410/11/17 2:50 PM
ContentsLinear Regression with Seasonalityxi216SOLVED PROBLEM 8.7 Deseasonalizing a Time SeriesEconometric and Multiple Regression Models218222Summary 226 Key Terms 227 Integrative LearningExercise 227 Integrative Experiential Exercise 227 DiscussionQuestions 227 Solved Problems 228 Problems 234 Case: Demand Planning at BIOCNG241Chapter 9 Inventory Management Fundamentalsand Independent Demand2421 Define the Roles and Types of Inventory243The Role of Inventory 243Types of Inventory 2452 Understand Important Inventory ConceptsInventory Velocity247247SOLVED PROBLEM 9.1 Computing Inventory Turnover247Consignment Inventory 248Vendor-Managed Inventory 249Inventory and Bullwhips 2493 Understand, Perform, and Apply Demand AnalysisDependent versus Independent DemandABC Analysis 250SOLVED PROBLEM 9.2 Performing ABC Inventory AnalysisReview Systems2502502512544 Explain and Apply Inventory Models256The Basic Economic Order Quantity Model 256SOLVED PROBLEM 9.3 Total Annualized Inventory Costs256SOLVED PROBLEM 9.4 The Economic Order Quantity in ActionQuantity DiscountsSOLVED PROBLEM 9.5 Using EOQ with Quantity DiscountsReorder Points257258259260SOLVED PROBLEM 9.6 Computing a Reorder Point with Deterministic Lead Time260SOLVED PROBLEM 9.7 Reorder Point with Stochastic Demand during Lead Time261Periodic Review Inventory Models 262A Finite Replenishment Rate Inventory Model262SOLVED PROBLEM 9.8 Using the Periodic Review Inventory ModelA Finite Replenishment Rate Inventory Model262262SOLVED PROBLEM 9.9 Using the Finite Replenishment Rate Model263Summary 264 Key Terms 265 Integrative LearningExercise 265 Integrative Experiential Exercise 265 DiscussionQuestions 266 Solved Problems 266 Problems 269 Case: Managing Inventory at Nordstrom272Chapter 10 Sales and Operations Planning and EnterpriseResource Planning2731 Apply Sales and Operations PlanningProduction Planning 275Performing Sales and Operations PlanningA01 FOST9830 02 SE FM.indd 1127427710/11/17 2:50 PM
xiiContentsSOLVED PROBLEM 10.1 A Chase Plan in Action278SOLVED PROBLEM 10.2 A Level Plan in Action 2792 Define and Explain How Capacity Functions in Operations ManagementBottlenecks 282Best Operating Level2812823 Understand and Apply Capacity PlanningCapacity Planning ProcessModeling Capacity 285283284SOLVED PROBLEM 10.3 Modeling Capacity Measures286SOLVED PROBLEM 10.4 Rough-Cut Capacity Planning in ActionRough-Cut Capacity Planning2862864 Understand the Main Functionality of an Enterprise ResourcePlanning System2875 Understand and Apply Material Requirements Management288MRP Inputs 288MRP Record 290SOLVED PROBLEM 10.5 MRP Record ComputationsMRP Logic290291SOLVED PROBLEM 10.6 Rolling Cart MRP LogicMRP Outputs292294Summary 295 Key Terms 296 Integrative LearningExercise 296 Integrative Experiential Exercise 296 DiscussionQuestions 296 Solved Problems 297 Problems 301 Case: Montclair State UniversityChapter 11 Logistics3033051 Understand the Strategic Importance of LogisticsCost 307Flow 308Access 309Sustainability3063102 Understand and Apply Fundamental Logistics Trade-OffsCost-to-Cost Trade-Offs312312SOLVED PROBLEM 11.1 Cost-to-Cost Trade-Off CalculationsModal Trade-Offs 312Cost-to-Service Trade-OffsLanded Cost 313312313SOLVED PROBLEM 11.2 Landed Cost Trade-Off Calculations3 List and Apply the Five Logistics Processes314315Demand Processing 315Inventory Management 317Transportation 318Warehousing 320SOLVED PROBLEM 11.3 Warehousing Square Root Rule in ActionSOLVED PROBLEM 11.4 Weighted Center of Gravity in ActionTransportation Method321323323SOLVED PROBLEM 11.5 The Transportation Method in Action324Configuring Logistics 326Structural Network 329Reverse Logistics 329A01 FOST9830 02 SE FM.indd 1210/11/17 2:50 PM
ContentsxiiiSummary 330 Key Terms 330 Integrative LearningExercise 330 Integrative Experiential Exercise 331 DiscussionQuestions 331 Solved Problems 331 Problems 333 Case: Brentward Logistics4336Improving Supply Chain and Operations Management PerformanceChapter 12 Project Management3393401 Understand Project ManagementThe Human Element in ProjectsQualifying Projects 346Project Charters 348341342SOLVED PROBLEM 12.1 Project Charters in Action3502 Utilize Project Planning Tools350Estimating Task Completion Times 350SOLVED PROBLEM 12.2 Computing Task Times352SOLVED PROBLEM 12.3 Computing Task Variance352SOLVED PROBLEM 12.4 Putting It Together: Task Times and VariancesManaging Multiple Projects3533543 Plan and Control Projects Using PERT/CPMSOLVED PROBLEM 12.5 Drawing AON NetworksFinding the Critical Path 356Computing Early Times 357Computing Late Times 358Computing Slack and the Critical Path355356358SOLVED PROBLEM 12.6 Finding the Critical PathUsing PERT/CPM in Delegation DecisionsProbabilistic PERT 361360361SOLVED PROBLEM 12.7 Computing Required Project Completion Times364SOLVED PROBLEM 12.8 The Other Side of the Coin: Determining the Probabilityof Completing a Project in a Given Time3654 Learn How to Manage Costs of Projects through Gantt ChartsManaging Costs and Expediting ProjectsExpediting or Crashing Tasks 368SOLVED PROBLEM 12.9 Crashing Projects366366369Summary 370 Key Terms 371 Integrative LearningExercise 371 Integrative Experiential Exercise 371 DiscussionQuestions 371 Solved Problems 372 Problems 377 Case: Getting the Ducks in a Row for Project ManagementChapter 13 Supply Chain Quality Management3803811 Understand the Importance of Product Quality Dimensions3822 Discuss the Basics of Quality Management as Espoused by Deming, Juran, Crosby,and Ishikawa 384W. Edwards Deming 384Joseph Juran 385A01 FOST9830 02 SE FM.indd 1310/11/17 2:50 PM
xivContentsPhilip Crosby 387Kaoru Ishikawa 3873 Understand Supply Chain Quality ManagementForming Collaborative Relationships 389ISO 9000 and Industry-Specific Standards3894 Understand and Apply Quality in ServicesService Quality DimensionsSERVQUAL 391387390391SOLVED PROBLEM 13.1 SERVQUAL “Minding the Gap” ExerciseCustomer-Driven Excellence3933935 Understand and Apply Quality Tools and ApproachesSeven Basic Quality Tools 394The Malcolm Baldrige National Quality Award (MBNQA)Benchmarking 401394400Summary 403 Key Terms 404 Integrative LearningExercise 404 Integrative Experiential Exercise 404 DiscussionQuestions 405 Solved Problems 405 Problems 406 Case: Corporate Universities: Teaching the Tools of QualityChapter 14 Statistical Process Control4074091 Articulate the Purposes of Statistical Quality Control and Statistical Thinking2 Understand Process Stability410412Sampling and Inspection 413Types of Samples 413Inspection Methods 413SOLVED PROBLEM 14.1 Computing Inspection Ratios4153 Explain and Use Variables and Attributes Process Control ChartsUnderstanding Control Charts 416A Generalized Procedure for Developing Process ChartsVariables Control Charts 418SOLVED PROBLEM 14.2 Developing Charts418422SOLVED PROBLEM 14.3 Using Excel to Develop X Control ChartsSOLVED PROBLEM 14.4 Developing R Charts423425SOLVED PROBLEM 14.5 Developing R Charts in ExcelAttributes Control Charts415426428SOLVED PROBLEM 14.6 Developing p Charts4304 Apply Control Charts432Interpreting Control Charts 432SOLVED PROBLEM 14.7 Interpreting Control ChartsCorrective Action 434Tampering with the ProcessControl Charts and Services4334344345 Perform Process Capability Analysis434SOLVED PROBLEM 14.8 Capability Analysis435Summary 437 Key Terms 437 Integrative LearningExercise 438 Integrative Experiential Exercise 438 DiscussionQuestions 438 Solved Problems 438 Problems 444 Case: Meeting Standards in Software QualityA01 FOST9830 02 SE FM.indd 1445110/11/17 2:50 PM
ContentsChapter 15 Lean and Six Sigma Management and Leading Change1 Define Six Sigma and Explain Its Various RolesSix Sigma RolesDMAIC 456Business Casesxv4524534554562 Understand and Use Lean459Lean Solutions 459Lean Viewpoints 460Lean Philosophy 4603 Apply Lean Practices461Practicing Lean Production 462SOLVED PROBLEM 15.1 Determining the Number of Kanban Cards NeededLean Workforce Practices 465Systemwide Solutions 467Lean Supply Chain Management4644684 Familiarize Yourself with Change Management468Summary 469 Key Terms 470 Integrative LearningExercise 470 Integrative Experiential Exercise 470 DiscussionQuestions 470 Solved Problem 471 Problems 471 Case: Automotive Resources471Appendix A-1Glossary G-1Name Index I-1Subject Index I-3Photo Credits C-1A01 FOST9830 02 SE FM.indd 1510/11/17 2:50 PM
PrefaceNEW TO THIS EDITIONWith this edition of Managing Supply Chain and Operations: An Integrative Approach, we wanted toup our game. Every new edition of a textbook must represent a step forward. We feel like wemet that goal with this edition. At the same time, you will see that this edition maintains thestrengths of the first edition with additional features.79Understand and Employ Quality Function DeploymentSeries Reliability SOLVED PROBLEM 3.5Problem: Your manager has asked you to compute reliability for the following system.A0.98B0.99C0.90D0.97Solution: The overall reliability for this system isR 0.98 * 0.99 * 0.90 * 0.97 0.847MEASURING RELIABILITY In addition to the series reliability function we have discussed,there are other ways to evaluate reliability. These models take into account historical data andare helpful in evaluating the efficacy of products. Let’s discuss some basic reliability functions. Failure rate is measured asfailure rate number of failuresunits tested * number of hours testedf(x) Analytics Emphasis We have addedanalytics to the core model in the book.We have also honed our focus on analytics. For every quantitative example inthe text, we have added analytics iconsto show students that they are learning tools they can use in their careers.We have also included discussion ofthe importance of analytics in the earlyparts of the book.(3.13)Some care should be exercised in using Equation 3.13 because there is no distinctionbetween continuous hours of testing or testing performed at separate times. For example,there is no difference in testing hours if five units are tested for 100 hours each or if one unit isteste
Integrating Supply Chain and Operations Management 1, Chapter 1 Introduction to Supply Chain and Operations Management 2, 1Understand Why You Are Studying Supply Chain and Operations Management 3, Processes 4 Supply Chain Globalization 5, 2Define, Understand, and Apply the Components of Supply Chain and Operations Management 8,