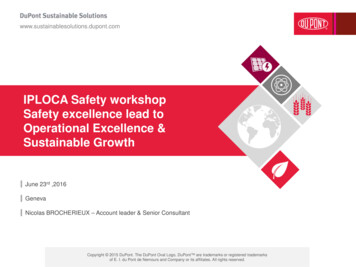
Transcription
www.sustainablesolutions.dupont.comIPLOCA Safety workshopSafety excellence lead toOperational Excellence &Sustainable GrowthJune 23rd ,2016GenevaNicolas BROCHERIEUX – Account leader & Senior ConsultantCopyright 2015 DuPont. The DuPont Oval Logo, DuPont are trademarks or registered trademarksof E. I. du Pont de Nemours and Company or its affiliates. All rights reserved.
Agenda1.2.3.DuPont Sustainable SolutionsDuPont approach to safety culture & safety excellenceQuestions & answersCopyright 2015 DuPont. All rights reserved.2
E.I Du Pont de Nemours Core values: Safety, ethics and respect forpeople and the environment 25 Billion global revenues in 2015 DuPont Sustainable Solutions is theConsulting Business 240 operating facilities in 45 countries with60,000 employees Worldwide reputation for industrial safety DuPont applies a single RC/PSMmanagement system worldwideCopyright 2015 DuPont. All rights reserved.3
DuPont Core Values Safety & Health Environmental Stewardship Highest Ethical Standards Respect for People“Our commitment is Zero”Copyright 2015 DuPont. All rights reserved.4
Safety contactDriving is a very demanding taskRoads are dangerousRoad traffic injuries represent almost a quarter of all injury mortality,standing as the leading cause.When entering your car, you are entering a risky environmentTo face this situation, you need to be100% focused on drivingCopyright 2015 DuPont. All rights reserved.5
Safety contactDriver Distractions A driver’s primary responsibility is the safe operation of the vehicle, andno activity (distraction) should interfere with that responsibility. Driver distractions come in many forms: Visual distractions outside the carReaching for objects in the carEating, drinkingSmokingChanging the radio or CD playerTexting or talking on a mobile phoneSetting the navigation systemTalking with a passengerReading a mapFatigueMany others .Copyright 2015 DuPont. All rights reserved.6
Safety contactFatigue Fatigue often leads to driver inattention (distraction) and increasedreaction time, which increases the risk of a collision. The driver should do whatever is appropriate to allow himself or herselfto complete the trip safely. The following list includes some causes of driving fatigue: Driving after consuming a large meal. Driving long distances at highway speeds (i.e., highway hypnosis). Driving long distances without getting proper breaks (Some expertssuggest breaks every two hours.) Driving several hours after a full day of work. Driving without adequate ventilation and temperature control. Ingesting various medications or controlled substances. Insufficient rest or sleep. Maintaining an improper driving position behind the wheelCopyright 2015 DuPont. All rights reserved.7
Consulting SolutionsApplying over 200 years of real-world experienceand science-driven innovation to deliver integratedsolutions for safety, productivity, and environmentalperformance improvementOPERATIONALRISK MMUNICATION &CULTURALTRANSFORMATIONCopyright 2015 DuPont. All rights reserved.8
DuPont Operational ExcellenceImplementing an Integrated Approach withPeople as the FoundationDuPont Production System FrameworkMANAGINGPROCESSESTo keep focus on what reallymatters with the right peopleTECHNICALMODELCAPABILITIESENGINESMINDSETS &BEHAVIORSStandard tools andpractices to drivefocused operationalrisk reductionTo ensure theright skills andeffective coaching onoperational risksTo align organizationon the purpose andobjectives ofoperational riskreductionEXPECTEDBUSINESSOUTCOMECopyright 2015 DuPont. All rights reserved.9
Agenda1.2.3.DuPont Sustainable SolutionsDuPont approach to safety culture & safety excellenceQuestions & answersCopyright 2015 DuPont. All rights reserved.10
DuPont recognises that there are four keycomponents for achieving Safety Excellence A(how risks are understood by people and systematically addressed) BOperational Discipline(how following the rules is transformed into organisational pride) DCulture of Openness and Collaboration(how people work together and support each other) CCulture of AnticipationIntegrated Management System(cultural and risk based elements meshing together)Understanding the relative performance of theorganisation in relation to these Key Ingredients.This is central to designing an intervention thatwill bring about sustainable improvement.11Copyright 2016 E. I. Du Pont De Nemours And Company. All Rights Reserved. The DuPont Oval Logo and DuPont are Registered Trademarks OrTrademarksOf DuPontOrreserved.Its Affiliates.11Copyright 2015 DuPont.All rights
ACulture of AnticipationMultiple FatalitiesCatastrophicCatastrophic IncidentIncidentAssess the effort toeliminate bothbehavioral and processsafety hazardsMultiplefatalityFatalityFatalityMajor loss incident - public impactMajorIncidentLost time injurySerious IncidentsSerious InjuryReportable InjuriesLossIncidentIncidents with significant lossNearMissFirst-aid IncidentFirst Aid/Incidents with minor lossIncident with no lossUnsafe Acts and DecisionsUnsafe Acts and ConditionsPeople risksObservable behaviourWorkplace SafetyMan-Machine RisksUnseen behaviourUnsafe SituationsIntegrity RisksUnderstanding assetsProcess SafetyCopyright 2015 DuPont. All rights reserved.12
BBuilding a Safety Culture is a journeyExternal MotivationCOMPLIANCEFelt Leadership, Role Modeling,Influencing EngagementINJURY RATESRules, Procedures, ProtocolsInternal MotivationCOMMITMENTThe Cultural ent Safety by natural Instinct. Personal knowledge,commitment & standards. Internalisation. Personal value. Care for self. Practice & habits. Individual recognition. Help others conform. Compliance is the goal. Delegated to safety manager Lack of managementinvolvementManagement commitment.Condition of employment.Fear / Discipline.Rules / Procedures.Supervisor control, emphasisand goals. Value all people. Training.“I follow the rules because I have to” Being others keeper. Networking contributor. Care for others. Organizational pride.“I follow the rules because I want to”Copyright 2015 DuPont. All rights reserved.13
BCulture of Openness and CollaborationCoaching & FeedbackBeing willing and open to give and receive feedback, listen to ideasand concerns and coach people to reach their potentialare key traits to embed.Copyright 2015 DuPont. All rights reserved.14
CCreate organization ownershipOperational DisciplineIndividualOrganizationalEveryoneDoes It RightOrganizationalPersonalEvery Time IndividualI am knowledgeable and aware ofthe risks associated with myactivities, and I’m committed toperform each task, the right way,every time.OperatingandSHEExcellence OrganizationalThe total dedication and commitmentby every member of an organizationto establish the correct workpractices and to carry out each task,the right way, every time.Copyright 2015 DuPont. All rights reserved.15
COperational DisciplineManagementStandards70%xState of SafetyStandardsOperationalDiscipline (OD)40% State ofImplementationEffectiveImplementation28%State of OperationalEffectivenessCopyright 2015 DuPont. All rights reserved.16
DDuPont Safety excellence elements12 Cultural foundations elementsWhat does management do to leademployees to safety excellence?LeadershipWhat are theorganizational structuresthat enable the pursuit ofsafety excellence?Management Commitment Policies & Principles Goals, Objectives, & Plans Procedures & Performance Standards StructureLine Management Accountability& Responsibility Safety Personnel Integrated Organization Structure Motivation & Awareness What actions does theorganization take on aregular basis to increasesafety performance?Processes & Actions Effective Communication Training & Development Incident Investigation Observations & AuditsCopyright 2015 DuPont. All rights reserved.17
DDuPont Integrated Management system –22 Elements of safety for achieving Safety excellenceCultural ElementsRisk Based Elements Leadership Facilities Structure Personnel Process &Actions TechnologyCopyright 2015 DuPont. All rights reserved.18
Our safety journey for a sustainable safety culturetransformationCopyright 2015 DuPont. All rights reserved.19
3. PSM IMPLEMENTATION APPROACHCulture TransformationThe focus on culture will deliver activities that develop the threecultural ingredients together with compelling communication.Risk Anticipation Sharing industry incidentsInvolvement in risk profileEngage in risk perception discussionsEncourage application of risk mitigation ideasCoaching and Feedback Reinforcement of new skills acquired Building in feedback and reflection Encouraging open reporting of concernsOperating Discipline Visualisation of controls Engagement to observe and discuss deviations Role modelling and leadership dialoguesCommunication High Impact Affective ReinforcingCopyright 2015 DuPont. All rights reserved.20
Capability BuildingTraining and qualification planCustomizedTrainingLearning byListeningCoachingLearning byDoingSitessupervisionLeadsCoachingLearning orkshopWorkshopSafety standardReferents LeadsSitessupervision &employeesParticipatesLearning ng ModuleBuilding CompetenciesSkilledMentoringLearning byCoachingCopyright 2015 DuPont. All rights reserved.21
Du Pont Safety leading practicesJob Cycle CheckA Job Cycle Check (JCC) is a cooperative, supervisor-employee analysisof the employee’s performance on some part of a job or task.JCC BenefitsHelps to determine whether Procedures are current and complete. Employees know procedures. Employees are following procedures as theyperform jobs. All aspects of the job have been included in thecurrent procedure.JCC Planning Identify jobs and people to check. Make a formal plan for conducting JCCs. Keep records for each employee. Do one JCC with each employee quarterly. Review JCC records annually. Training is effective.Job Cycle Checks allow you to determineinconsistencies in your standard procedures andtraining so that you can prevent injuries!Copyright 2015 DuPont. All rights reserved.22
Agenda1.2.3.DuPont Sustainable SolutionsDuPont approach to safety culture & safety excellenceQuestions & answersCopyright 2015 DuPont. All rights reserved.23
Task Risk assessment1.2.3.Value & BenefitsPlanning & preparationOverall processCopyright 2015 DuPont. All rights reserved.24
Benefits & Strengths: Elimination of the most significant hazardsFulfill Regulatory & Policy requirementsInvolves employees from all levelsIs focused on the actual work activityImproved awareness of hazards and/ or identify new ones.Ensure the correct “control measures” are in place and reflected in jobprocedures, Continuously improve Safety systems and conditions of work Reduce incidentsCopyright 2015 DuPont. All rights reserved.25
Planning and preparation stage includes: Organising and coordinating the assessment Involving management and encouraging the participation of theworkforce Appointing competent people to make the assessment Internal / External Multi functional Consulting workers representatives on the arrangements forappointing the people who will carry out the assessments Providing the necessary information, training, resources, time andsupport to assessors Ensuring there is adequate coordination between assessorsCopyright 2015 DuPont. All rights reserved.26
When it is required: Proper safety procedures are identified as not being in placeExisting procedures are not adequateNew job, task, chemical, machine has been introducedExisting task has been significantly changedNew/ different people doing the taskSpecific Regulatory or Company requirementChange in standardsChanges in technologyUnplanned workTo continue work after an incident or injury has occurredResult of medical surveillanceCopyright 2015 DuPont. All rights reserved.27
Overall process:Identify task and sub-tasksIdentification op people exposedIdentification of hazards and associated risksEvaluate initial Risk scoreDefine measure(s)Include standard and additional measures.Always take prevention hierarchy into accountNAcceptable?Evaluate actual Risk scoreYAssigning priority to the measure(s)Copyright 2015 DuPont. All rights reserved.28
5. Prevention Hierarchy for control measures :1. Elimination: Eliminate Risk2. Substitution: Reduce Risk at source or remove source3. Engineering Control: Take collective measures4. Personal Protection: Make people wear PPE5. Administrative Control: Training procedures instructionsCopyright 2015 DuPont. All rights reserved.29
Copyright 2015 E. I. du Pont de Nemours and Company. All rights reserved. The DuPont OvalLogo, DuPont are registered trademarks or trademarks of DuPont or its affiliates.
DuPont Operational Excellence Implementing an Integrated Approach with People as the Foundation . EXPECTED . BUSINESS OUTCOME . MANAGING PROCESSES. . DuPont Integrated Management system - 22 Elements of safety for achieving Safety excellence Cultural Elements Leadership Structure Process &