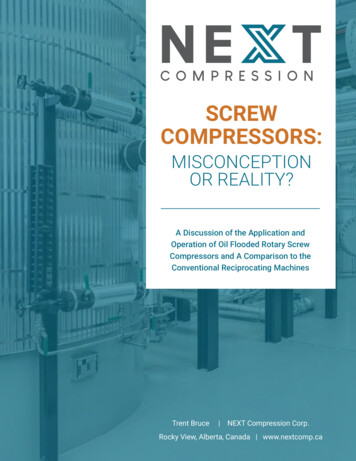
Transcription
SCREWCOMPRESSORS:MISCONCEPTIONOR REALITY?A Discussion of the Application andOperation of Oil Flooded Rotary ScrewCompressors and A Comparison to theConventional Reciprocating MachinesTrent Bruce NEXT Compression Corp.Rocky View, Alberta, Canada www.nextcomp.ca
TABLE OF CONTENTSABSTRACT. 3INTRODUCTION. 4APPLICATIONS. 5FEATURES OF THE SCREW COMPRESSOR. 6BASIC OPERATING PRINCIPLES. 7The Compression Process. 7Volume Ratio. 9Capacity Control. 11Screw Compressor Package Components. 14CONCLUSION. 15AcknowledgmentsNEXT Compression would like to thank Frick and Ariel Corporation for their cooperation in providing some of the graphics and information presented in thispaper. Their assistance in building this paper is greatly appreciated.2ScrewCompressors
ABSTRACTScrew compressors have been used on air and variousrefrigeration and process applications for a great numberof years. In the past 20 years the machines have becomevery popular in the natural gas industry in booster and gasgathering applications with additional growth in the solutiongas market in recent years. Declining field pressures areforcing the industry to look at more flexible alternatives to theconventional reciprocating compressor. In addition to this,many governments and environmental groups in North Americaand around the world are pushing the industry to conservegases that have typically been vented into the atmosphere in avariety of solution gas applications.This paper will discuss specific applications where screwcompressors are used and the advantages of the rotary screwto conventional reciprocating machines. We will look at somespecific features of the screw compressor, which make itthe machine of choice for many applications requiring highreliability, low maintenance costs and a very wide overalloperating range.We will look at a graphic model of a typical process flowdiagram and review the components required to make up arotary screw compressor package. We will also take a detailedlook at the internals of the machine to better understand theoverall operation, capacity control system, and the associatedpower savings that go with it.It some cases it is extremely important to optimize adiabaticefficiencies in order to provide reduced power costs. On rotaryscrew compressors this is done using a feature called Vi,or internal volume ratio. The Vi can be changed on differentmachines using a couple of different methods. We will compareboth these methods and their associated advantages.Project economics always play an important role in anyequipment selection. With the proper flexibility built intothe initial package, these units can be used on numerousapplications.In review, this paper will provide a detailed look at screwcompressors, where they are applied and exactly how theyoperate. We will compare the rotary screw to other types ofmachines for similar applications and show the benefits inusing this type of machine.3ScrewCompressors
INTRODUCTIONOil flooded rotary screw compressors have been widely used on variousair and refrigeration applications for over fifty years. These machines didnot make a significant presence in the natural gas industry until the early1990’s. Until this time, reciprocating compressors had been used almostexclusively for natural gas compression. As gas fields have matured andfield pressures have dropped, screw compressors have become a veryattractive alternative and supplement to reciprocating machines.This paper will discuss some of the applications and features of screwcompressors, basic operating principles and the advantages of therotary screw over conventional reciprocating compressors for the naturalgas compression industry. We will look at the machine itself, as wellas the overall compression system and the components required in ascrew compressor package. The screw compressors we will focus onare the oil flooded, heavy duty process gas machines rather than the airderivative types. We will provide numerous illustrations to help betterunderstand the screw machine.Figure 1 shows the basic geometry of the rotary screw compressor.View (A) is a simple representation of the actual rotors. We have labeledthe male rotor lobe and the female rotor flute. As the rotors turn in anoutward direction, the male lobe will unmesh from the female flute on thetop of the rotors forming an area for the gas to enter. The gas becomestrapped in the machine and compression occurs when the lobes of therotors begin to mesh together again along the bottom. The shaded arearepresents the pocket of gas that occurs within a specific flute. View (B)is a representation of the side view inside the machine. The same fluteis shaded for comparison. Here we see the suction port in the upperleft corner and the discharge port in the lower right corner. The rotorswill turn in an outward direction forcing the male and female flutes tounmesh, allowing process gas to enter the top of the machine. The gaswill travel around the outside of the rotors until it reaches the bottomwhere the compression actually occurs. Gas will be discharged in thelower right corner of the picture.Figure 14ScrewCompressors
APPLICATIONSAs compressor manufacturers continue to increase the operating ranges oftheir machines, many heavy duty screw compressors built today are capableof suction pressures around 150 psig and discharge pressures up to 450 psig.There are some screw compressors capable of operating at much higherpressures by using cast steel casings but these are not commonly used in thenatural gas industry due to capital cost and availability so they will not the focusof this discussion.Screw compressors are commonly used in a variety of process gas, processrefrigeration and natural gas applications, including individual wellheadboosters, low pressure gathering systems, low stage boosters to existingreciprocating machines, fuel gas compression, solution gas and vapor recoverycompression systems. They have been used on sweet and sour gas as well asacid gas applications with H2S and/or CO2 concentrations in excess of 80%.Although most conventional natural gas applications are based on a specificgravity of 0.57 – 0.65, screw compressors can be used on very light gasessuch as hydrogen and very heavy mole weight gases with specific gravitiesapproaching 2.0.Until quite recently, many people considered screw compressors limited tosweet, dry natural gas applications. With changing regulations around theWorld, we have seen screw compressors become much more common for theunconventional gases because of their wide operating range and turndowncapability as well as the reduced maintenance costs. The biggest concernpeople have is potential oil contamination when screw compressors are appliedin heavy, hot and sour applications. A simple process simulation to review theworst case suction and discharge pressures, maximum inlet temperature andthe gas analysis can determine if a screw compressor can be applied in theseapplications. The biggest issue is the need to ensure we operate the screwcompressor at a higher discharge temperature than the water and hydrocarbondewpoints. If our discharge temperature drops below the dewpoint temperature,water and/or condensate will drop out during the compression cycle anddilute the oil. Over time, this will eventually cause a catastrophic failure. Dueto the evolution of lubricants and a better understanding of screw compressoroperations, we can now provide machines that meet almost all of the lowpressure solution and treater gas applications we see.The most common applications for screw compressors in natural gas servicerange in horsepower from roughly 50 to 1,500 and are available in both engineand electric drive. Screw compressors were originally developed to operate withelectric drive two pole motors at 3,550 rpm at 60Hz. As they have become morepopular in the natural gas industry, engine drive applications have become muchmore common.5ScrewCompressors
FEATURES OF THE SCREW COMPRESSORThe rotary screw compressor is a positive displacement machine that operateswithout the need for suction or discharge valves. It has the ability to automaticallyvary suction volume internally while reducing part load power consumption. Screwcompressors provide a much wider operating range and lower maintenance costs thanconventional reciprocating compressors. The machines are much smaller and createmuch lower vibration levels than piston machines as well.Reduced MaintenanceThe only significant moving parts in a screwcompressor are the male and female rotors.There are no valves, pistons, piston rings,or connecting rods that require regularmaintenance. With the elimination of the pistons,rings and valves, annual maintenance costsare reduced. It is not uncommon to operatescrews for several years without ever performingany significant maintenance or repairs. Whencomparing screw compressors and reciprocatingmachines, it is important to considermaintenance costs in the overall project cost.Turn DownScrew compressors offer turn down capabilitiesup to 90% of full load with very good partload power requirements. This turn downcapability occurs within the machine and isindependent of external driver speed or gasrecycle controls. This makes the machine anattractive alternative for areas where flow ratesand operating conditions are not constant.The capacity control can be handled manuallyor automatically to meet the exact demandsof the overall system. Controlling the flowrate or volume of gas through the machinesignificantly reduces the need for an externalsuction pressure control, discharge to suctionrecycle or automatic driver speed control. Theseare the most common means of automaticcapacity control on reciprocating machines asinternal capacity control is much more complex6to do automatically and therefore very seldomused. Using an external bypass valve or asuction pressure control valve consumes morepower than reducing the flow rate of gas withinthe machine. The ability to adjust capacitywithin the screw compressor is comparable tovarying the stroke length and suction volumeon a reciprocating machine. However, thescrew can vary capacity automatically wherethe reciprocating machine generally usesvariable volume pockets that are adjustedmanually while the machine is shut down andde- pressurized. The turndown capability usingvariable volume pockets is less than using theslide valve in the screw compressor.High Compression RatiosScrew compressors can operate from roughly2 to 20 ratios of compression on a single stagewhile maintaining high volumetric efficiencies.These efficiencies are achieved by injecting largequantities of lube oil into the machine during thecompression process. Oil is typically injectedinto the machine at an approximate rate of 10-20USGPM per 100 HP, which significantly reducesthe discharge temperature of the process gas.The oil is discharged with the process gas andwill be removed later from the gas stream.Reciprocating machines can operate at muchhigher pressures than screw machines, butare typically limited to roughly 4 ratios ofcompression per stage. Multi-staging and intercooling these machines is required to preventIn general, screwcompressorsare consideredto provide veryhigh reliability,resulting in lowermaintenance costsand reduced downtime comparedto reciprocatingmachines.poor volumetric efficiencies, rod loading andexcessive discharge temperatures. In applicationswhere the system compression ratio exceedsfour, multi-stage reciprocating machines willoffer better adiabatic efficiencies, or powerrequirements, than the single stage screwcompressors. In this case the user must weigh theadvantages of the screw machine to the powersavings of the reciprocating compressor.Accommodates Wide Operating RangesThe screw compressor can operate over a verywide range with little or no changes required tothe machine. This makes it very well suited tothe natural gas industry where flow rates andoperating conditions are often changing. Overtime, as reservoir pressures decline, reciprocatingcompressors encounter rod loading or dischargetemperature limits and require costly retrofits.This entails changing cylinders, changing coolersections and re-staging the machine.Smaller Package SizesRotary screws provide high capacities with minimalinstallation space compared to reciprocatingmachines. Based on a full speed design of 3,600rpm, a very large screw machine can provide over80 MMSCFD of gas based on a 100 psig suctionpressure. The physical size of the compressor ismuch smaller than a comparable reciprocatingmachine which will require numerous cylinders tomove the same amount of gas.Lower VibrationWith only two major moving parts operating ina circular motion, screws create much lowervibration levels than reciprocating machines.With lower vibration levels, screw compressorsdo not require the same type of foundation as thereciprocating machines, which can result in lowerinstallation costs.In general, screw compressors are consideredto provide very high reliability, resulting in lowermaintenance costs and reduced down timecompared to reciprocating machines.ScrewCompressors
BASIC OPERATING PRINCIPLESA rotary screw compressor is very simple in design. Some of the majorcomponents include one set of male and female helically groovedrotors, a set of axial and radial bearings and a slide valve, all encasedin a common housing. Figure 2 represents a typical cutaway of a rotaryscrew compressor. The slide valve can not be seen in this pictu
screw compressor package. The screw compressors we will focus on are the oil flooded, heavy duty process gas machines rather than the air derivative types. We will provide numerous illustrations to help better understand the screw machine. Figure 1 shows the basic geometry of the rotary screw compressor.