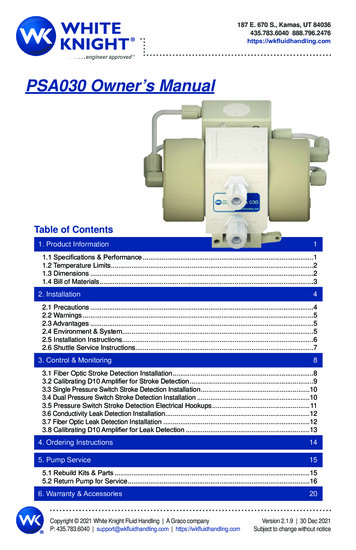
Transcription
187 E. 670 S., Kamas, UT 84036435.783.6040 888.796.2476https://wkfluidhandling.comengineer approved PSA030 Owner’s ManualTable of Contents1. Product Information11.1 Specifications & Performance.11.2 Temperature Limits.21.3 Dimensions.21.4 Bill of Materials.32. Installation42.1 Precautions.42.2 Warnings.52.3 Advantages.52.4 Environment & System.52.5 Installation Instructions.62.6 Shuttle Service Instructions.73. Control & Monitoring83.1 Fiber Optic Stroke Detection Installation.83.2 Calibrating D10 Amplifier for Stroke Detection.93.3 Single Pressure Switch Stroke Detection Installation.103.4 Dual Pressure Switch Stroke Detection Installation.103.5 Pressure Switch Stroke Detection Electrical Hookups. 113.6 Conductivity Leak Detection Installation.123.7 Fiber Optic Leak Detection Installation.123.8 Calibrating D10 Amplifier for Leak Detection.134. Ordering Instructions145. Pump Service155.1 Rebuild Kits & Parts.155.2 Return Pump for Service.166. Warranty & AccessoriesCopyright 2021 White Knight Fluid Handling A Graco companyP: 435.783.6040 support@wkfluidhandling.com https://wkfluidhandling.com20Version 2.1.9 30 Dec 2021Subject to change without notice
engineer approved PSA030 Owner’s ManualDear valued customer,Thank you for purchasing a White Knight PSA030 pump.Our dedicated team designs products to meet your exactingspecifications with a demonstrated commitment to quality thatgoes beyond mere words and fancy slogans.Our patented designs offer a variety of size and material options to meetstringent requirements of high-pressure chemical delivery systems, hightemperature re-circulation processes, chemical reclaim and bulk transportapplications, slurry systems, and more. Our safe, reliable products offersuperior performance, optimized efficiency, and simplified maintenance.White Knight is able to provide the highest quality fluid handling productsthrough controlled, consistent in-house engineering and manufacturing.Through continued significant investments in engineering andmanufacturing, we lead the industry with new technologies and products.White Knight has received numerous awards for innovation andmanufacturing programs. We rigorously manage our quality assuranceprocesses to ensure consistency and reliability. Our quality controlsinclude strict cleanliness procedures and consistent manufacturingprocesses. For example, high-purity product assembly, testing, andpackaging is performed in a Class 100 cleanroom.Please peruse this manual before installing your White Knight product.It details installation requirements and setup instructions, and providesadditional information and accessories for enhanced functionality.Our team has gone to great lengths to ensure our products serve yourneeds and meet your requirements.Further, we provide the highest quality products at the best value, andwe back them up with excellent warranties and world class support.Thank you for your confidence and trust in White Knight products.Sincerely,Brian Callahan, PresidentWhite Knight Fluid HandlingCopyright 2021 White Knight Fluid Handling A Graco companyP: 435.783.6040 support@wkfluidhandling.com https://wkfluidhandling.comVer. 2.1.9 30 Dec 2021Subject to change without notice
PSA030 Owner’s Manualengineer approved 1. Product Information1.1 Specifications & PerformanceModelPSA030PSASD030Max Flow Rate*24.7 lpm(6.53 gpm)24.2 lpm(6.4 gpm)DisplacementPer Cycle*0.074 liters(0.019 gal)0.074 liters(0.019 gal)Cycles per min333 max364 maxAir Connection1/4 in1/4 in3.3 kg (7.28 lb)3.3 kg (7.28 lb)3 m (10 ft)Flooded suctionWeightSoundSuction Lift*Pressure**74 dB(a) at 100 psi 50 CPM79.9 dB(a) at 100 psi max CPMPower**63.01 dB(a) at 100 psi 50 CPM69.9 dB(a) at 100 psi max CPMMax FluidTemperature60160 CPM60 PSI410 SCFM50200 CPM340 PSI407.5 SCFM240 CPM30220 PSI205 SCFM60PTFE, PFA, PP,CeramicFiber optic with or without D10sensor, or solid state pressureswitch (NPN or PNP)LeakDetectionFiber optic with or withoutsensor, or conductivityElectronicControlCPC, CPT, or custom.Call for details.100 PSIAir PressureAir ConsumptionCycle Rate100 CPM80 PSI160 CPM12 SCFM5200 CPM60 PSI14 SCFM4240 CPM5010 SCFM34040 PSI280 CPM307 SCFM220 PSI205 SCFM320 CPM12.5 SCFM10PSI70280 CPM178012.5 SCFMDischarge PressureDischarge Pressure70PTFE, PFAStrokeDetection680 PSI51.4 bar (20 psi)90100 CPM80Min StartupAir PressurePSASD030 Performance100Air PressureAir ConsumptionCycle Rate67 Bar (100 psi)Non-Fluid PathMaterials100 PSI90Max SupplyAir PressureFluid PathMaterialsPSA030 Performance7min: 0 C (32 F)max: 50 C (122 F)EnvironmentalTemperature* May vary by configuration or system. Suction lift diminishesover time. Recommended installation level less than 3 ft abovesource. To calculate displacement, divide flow rate by CPM.** Sound measured in accordance with ISO9614-2:1997.*** Dry-run capable PSASD030 pumps require flooded suctionand may have reduced warranty. Contact support for details.100100 C (212 F)10BarPSI5LPM3m 6. 0301.67. 01.88.0352.09.0Bar5LPMm3/hrGPM0.21.0100.42.0Liquid Flowrate150.60.83.0201.04.0251.25.01.46. 0301.67. 01.8352.08.0Liquid FlowrateHow to Read ChartsExampleDraw a horizontal line at your dischargeAt 2 Bar (30 psi) discharge pressure and 70pressure and vertical line at desired flow rate.psi air pressure, PSA030 pumps provide 15At line intersect, estimate required air pressure,lpm (4 gpm) flow rate, cycle at 220 CPM,resultant cycle rate and air consumption.and exhaust 10 SCFM of air.*Graph is for reference only. Performance was measured utilizing 1/2 in (3/8 in ID) air line and1-1/4 in (1-1/8 in ID) liquid lines with 1 ft flooded suction. Performance may vary in your system.Copyright 2021 White Knight Fluid Handling A Graco companyP: 435.783.6040 support@wkfluidhandling.com https://wkfluidhandling.comVer. 2.1.9 30 Dec 2021 P. 1Subject to change without notice9.0
PSA030 Owner’s Manualengineer approved 1.2 Temperature LimitsAir Supply Pressure7.0140 F150 F160 F170 F180 F190 F200 F210 F100956.5906.085805.55.0Bar 60 C75PSI65 C70 C75 C80 C85 C90 C95 C100 C1.3 DimensionsDimensions in [mm] in2148.4MOUNT WITH 2 EA.3/8" (10 mm) SOCKETHEAD CAP 2.61003.9CL572.221.81214.8321.3Copyright 2021 White Knight Fluid Handling A Graco companyP: 435.783.6040 support@wkfluidhandling.com https://wkfluidhandling.comVer. 2.1.9 30 Dec 2021 P. 2Subject to change without notice
PSA030 Owner’s Manualengineer approved 1.4 Bill of Materials202212231526Shuttle Assembly2114262914450-NP-000113302832411152711825 17103159191827816Body Inlet OnlyFittings (Type, Size, Option)AssembliesFlaretekCompatible14510-PF-0016 7200-PF-000114510-PF-0001 7200-PF-000214510-PF-0002 7200-PF-000314510-PF-0003 00-PF-00017300-PF-000214530-PF-0025 7400-TE-003114530-PF-0012 7400-TE-002314530-PF-0001 7400-TE-000114530-PF-0002 00-TE-000714520-TE-0009 7010-TE-000114520-TE-0001 7010-TE-000314520-TE-0002 7010-TE-000214570-PF-0013 7800-TE-001314570-PF-0014 7800-TE-001414570-PF-0001 7800-TE-000114570-PF-0002 7800-TE-00027130-TE-0001WeldablePillar S-300FNPTSynchroFlarePrimeLockPlugged6417Tube Out321/4 in.3/8 in.1/2 in.3/4 in.3/8 in.1/2 in.3/4 in.1/2 in.3/4 in.1/4 in.3/8 in.1/2 in.3/4 in.1/4 in.3/8 in.1/2 in.3/4 in.3/8 in.1/2 in.3/4 in.1/4 in.3/8 in.1/2 in.3/4 8N12S06S08S12L04L06L08L12B00(Nut not included)PSA030 BILL OF MATERIALSItem PartDescription11125-TE-0017Pump Body22127-EP-0014Head, Right32127-EP-0015Head, Left414300-MP-0013 Bellows Assembly55143-MP-0001Shaft Seal65144-PF-0024Shaft76030-NP-0002Gripper Elbow, 1/4" NPT x 1/4"86030-NP-00011/8" Npt X 1/4" Elbow96070-NP-00011/4" Female Gripper Nut1010071-PF-0009 1/4" Tubing1110071-PF-0008 1/4" Thick Wall Tubing124140-TE-0001Top Check Plug134135-MP-0006Check Seat144142-MP-0004Check Cage154100-MP-00041/2" Check Ball1610040-TE-0003 1/4" NPT Plug176080-KF-00011/4" Gripper186080-TE-00011/4" Ferrule1914200-NP-0006 Base Plate Assembly2010010-NP-0007 Shuttle MountScrew2114400-NP-0006 Shuttle Body with Sleeve226530-TE-0001Shuttle End Cap236560-CE-0001Shuttle Spool246150-NP-0004Cap, Muffler256070-NP-00041/4" Male Gripper Nut2610040-TE-0002 1/8" NPT Plug2710020-NP-0003 Shuttle Alignment Pin286140-FP-0003Baffle296140-PP-0003Baffle Spacer3010040-TE-0015 1/8" NPT Vent Plug317200-PF-00031/2" Flaretek Body327210-PF-00031/2" Flaretek NutCopyright 2021 White Knight Fluid Handling A Graco companyP: 435.783.6040 support@wkfluidhandling.com 2121243266222Ver. 2.1.9 30 Dec 2021 P. 3Subject to change without notice
engineer approved PSA030 Owner’s Manual2. Installation2.1 PrecautionsHandlingDo NOT lift pump by shuttle valve assemblynor air tubing.Installation OrientationPSA030 pumps must be installed in anupright position. The check valves areactuated by gravity and/or flow, and theywill not seat if the pump is not upright.Timer ModePSA030 pumps require an end of strokedetection mechanism (pressure switch)to prevent over stroking in timer mode.Operating a PSA030 in timer mode withoutstroke detection will void the pump warranty.Required Air Flow (Shuttle Valve)PSA030 pumps require 1/4 in minimum orificewith unrestricted air flow.Required Air Flow (Solenoid Valve)PSA030 pumps require a 0.75 Cv solenoid.Using a reduced Cv will reduce flow rates.Using a valve with more than 20% greaterCv will change operating parameters, reducepump life and void the warranty.Under Supply of AirPSA030 pumps operate erratically or stallwhen air supply is insufficient. Ensure useof air supply pressures higher than averagedair consumption lines in performance charts.Air supply lines and fittings must meetminimal inner diameter requirementsshown in the installation instructions.Air Supply PressureOperating PSA030 pumps 35% below maxair pressure may significantly extend pumplife. PSA030 pumps require 20 psi minimumair pressure. Operation above 7 Bar (100 psi)may damage the pump and void the warranty.Suction LiftPSA030 pumps have an initial suction liftcapacity of 3 ft. For best results minimizesuction lift.Liquid Inlet/Outlet ConnectionsPSA030 liquid ports are not NPT nor anyother standard. Use of connectors otherthan those supplied by White Knight willdamage the pump and void the warranty.Liquid Line RestrictionPSA030 pumps may be controlled byclosing liquid outlet lines. However,restricting liquid supply lines increaseswear and should be avoided. Do NOTpump against a closed liquid inlet. It willdamage the pump and void the warranty.Running DryPSA030 pumps use the pumped liquidto lubricate their shafts. The pumps willcycle faster and wear more than normalwhen run dry, which may cause damageand loss of self-prime abilities. Standardmodels should not be run dry after startup and are not warrantied under dry runconditions. Dry-run capable PSASD030models may run dry for short periods.Warranty of dry-run models is one-year.Extended warranties are available.Pulse Dampener with Shuttle ValveAir supply pressure to PSA030 pumpsshould be at least ten psi higher thanthe liquid line pressure when using apulsation dampener. Failure to do somay cause erratic operation.Cross ContaminationPSA030 pumps use porous material thatmay retain chemicals. Take precautionsto avoid cross contamination.Copyright 2021 White Knight Fluid Handling A Graco companyP: 435.783.6040 support@wkfluidhandling.com https://wkfluidhandling.comVer. 2.1.9 30 Dec 2021 P. 4Subject to change without notice
engineer approved 2.2 WarningsPressurized MaterialPumps in use containpressurized materials.Eliminate liquid and airpressure via shut off valvesbefore pump is serviced orremoved from the system.High TemperatureHeat may transfer to exteriorsurfaces when pumps operatewith high temperature fluids.Avoid direct contact with thepump when high temperaturefluids are present.Hazardous ChemicalUse appropriate personalprotective equipment whenhandling pump. ReferenceMaterial Safety Data Sheet(MSDS) for informationspecific to your chemicals.Loud NoisePump exhaust air contributesto work area noise levels. Onlyoperate pumps with approvedmuffler media, and use earprotection in noisy conditions.2.3 AdvantagesHead Pressure / Dead-HeadPSA030 pumps can be controlled byadjusting their liquid outlet pressures andcan be installed with head pressures upto dead-head (e.g. equal liquid and airpressures) with no damage to the pump.Thermal CyclingPSA030 pumps require no maintenancewhen operated within their performancerange, even in thermal cycling applications.PSA030 Owner’s Manual2.4 Environment & SystemOversized Inlet LinePumps operate optimally with liquid inletlines larger than the liquid outlet lines. Thisreduces strain on the bellows and mayreduce pulsation in the pump outlet.Clean Supply Air (CDA)PSA030 pumps require use of Class 2 airfor particles and moisture per ISO 8573-1.Use 10 micron filter; maintain -40 C dewpoint. A point-of-use filter is recommendedduring first six months of operation in newfabs/systems due to high risks of debristhat can damage pumps and void warranty.Flammable SolventsPSA030 pumps are not constructed fromconductive materials. System that pumpflammable solvents should be properlygrounded to avoid ignition by static charge.A River’s Edge test of isolative pumps withflammable liquids indicated that liquidsmust be grounded and other proceduresshould be followed. Copy of test available.Pumping Liquids Near Boiling PointMinimizing suction lift reduces pulsationand the potential for boiling or outgassingof liquid in the inlet of the pump. Althoughreciprocating pumps can pull suction lift,pump performance and life increase whensuction lift is minimized or eliminated.Abrasive SlurryPumping abrasive slurry may acceleratewear of components. PSA030 pumps arewarrantied when used with slurry. However,normal wear is not covered by warranty.Environmental TemperaturePSA030 pumps are rated for 0 C (32 F) 50 C (122 F) environmental temperatures.Do not freeze fluid in pump. Operationbelow 0 C may accelerate wear. Normalwear is not covered by warranty.Copyright 2021 White Knight Fluid Handling A Graco companyP: 435.783.6040 support@wkfluidhandling.com https://wkfluidhandling.comVer. 2.1.9 30 Dec 2021 P. 5Subject to change without notice
PSA030 Owner’s Manualengineer approved 2.5 Installation InstructionsPull-backdismount isstandard. Seesteps 4.1-4.3for forwarddismount.4.2.1.Move lever toup position.3.Slide base plateforward or pumpbody backward.5.6.Set pump on baseknobs; slide itforward. Set leverto down position.Attach fittingsto pump.Tighten to 20inch-lbs.Lift pump offof base plate.7.Attach tubes and fittings permanufacturer instructions.Use backer wrench to holdfitting in place at pump.4.1Push-Forward DismountConfiguration SetupReplace step 5with steps 4.1-4.3 tore-configure the baseplate to push-forwarddismount configuration.Screw base plate to surfacewith 3/8 in or 10 mm sockethead cap screws into predrilled holes.Move knobs toopposite sides.8.Affix supply air via 1/4in FNPT port on shuttlevalve. Air line must be3/16 in minimum orifice.4.24.3Set pump on baseknobs; slide it backward.Move lever downto locked position.Install with Rigid Base Plate *Requires push-forward dismount configuration (steps 4.1-4.3)1.Remove L bracket.Set lever in neutral(up) position.2.3.Slide pumpforward; lift itoff base plate.Fix base plateto work station.See step 4 above.4.5.Returnpump tobase plate.Move lock leverto down position.Reattach L bracket.Tighten to 12 in-lb.Liquid Inlet/OutletLiquid ports are not NPT nor any other standard. Use of connectorsother than those supplied by White Knight will damage the pump.Copyright 2021 White Knight Fluid Handling A Graco companyP: 435.783.6040 support@wkfluidhandling.com https://wkfluidhandling.comVer. 2.1.9 30 Dec 2021 P. 6Subject to change without notice
engineer approved PSA030 Owner’s Manual2.6 Shuttle Service InstructionsFollow instructions below to inspect or service White Knight shuttle valves. If a pumphas stopped, ensure all recommendations in this manual are followed and that thereare no air supply issues (i.e. closed air valve, damaged regulator, oil in air line, etc.).Do not lubricate or oil any of the shuttle components. White Knight shuttle valves do not require any lubrication.1. Remove nuts oneach air fitting oneach pump head.2. Unscrew both shuttlemounting bolts, and pullthe shuttle from the pump.3. Remove the airlines fromboth sides of the shuttle valveby unscrewing the air fittings.4. Unscrew topshuttle end capusing the shuttleend cap tool.5. Carefully removeceramic spool fromshuttle valve; it maybreak if dropped.Part: 12100-PV-0083If the ceramic spool in your pump has a flat feature,it is critical that it is oriented towards the bottom ofthe pump when the shuttle valve is reassembled.8. Remove muffler capfrom left side using themuffler cap tool. Removemuffler media and notethe order of the pieces.Repeat this step formuffler cap and mufflermedia on the right side.6. Unscrew bottomend cap using theshuttle end cap tool.9. Blow out shuttlevalve with CDA or N2.Ensure no residue ordebris is in any areasindicated above. Debrisor residue in theseareas may hinderpump performance.10. Cleanthe ceramicspool withIPA, and dryit using CDAor N2.Copyright 2021 White Knight Fluid Handling A Graco companyP: 435.783.6040 support@wkfluidhandling.com https://wkfluidhandling.com7. Unscrewboth 1/8 inNPT plugsthat havean orifice inthe center.11. Reassemble shuttleand reattach it to thepump by following theabove steps in reverse.If the spool in your pump hasthe flat feature, ensure it isoriented towards the bottomof the pump when the shuttlevalve is reassembled.Ver. 2.1.9 30 Dec 2021 P. 7Subject to change without notice
PSA030 Owner’s Manualengineer approved 3. Control & MonitoringProgrammable ControlWhite Knight CPT-1controllers monitor andadjust run mode, flowrate, leak detection andother pump operations.D10 Amplifier Electrical Hookups & DimensionsWhite Knight recommends Expert D10 amplifier for usewith fiber optic stroke and leak detection assemblies.Standard Models and Main UnitSub-UnitsNPN1 12-30V dc324–Load10-30V dc Standard Models12-30V dc Bussable Power Models150 mA max. loadLoad5 4Remote TeachQD hookup isfunctionally identical(Pink wire not used)5Unit BusRemote TeachPNPWire Key1 Brown2 White3 Blue4 Black5 GrayConnection– From MainLoad 12-30V dcConnection4Load5– From MainUnit BusRemote Teach10.5 0.2 mm (typ.)(0.41")14.5 mm(0.57")Single Sensor DesignPSA030 pumps can useonly a single fiber opticsensor at a time. The probemay be installed in the “F”port on either side of thepump. White Knight offersPFA, PFH, and PFU pumpsfor dual fiber optic use.35.9 mm(1.41")Mounting Bracket(included with some models)7.6 mm0.30"9.8 mm(0.39")61.3 mm(2.42")68.1 mm(2.68")3.1 Fiber Optic Stroke Detection Installation4.1.Remove strokedetect probefrom fiber opticassembly.2.Replace NPT plug in “F”port with stroke detectprobe. Hand-tighten.3.Insert the fiber opticcable until it seats atthe bottom of the probe.Lower ferrule andgripper until snugagainst probeand hand tightenfemale gripper nut.Fiber Optic SensorsFiber optic sensors melt ifused at 130 C (266 F),resulting in leak or end ofstroke detection failure.5.Open the top and slide the front face of the D10 up.Press the fiber optic ends into the holes on its front.Slide the face down to lock cables in place.Copyright 2021 White Knight Fluid Handling A Graco companyP: 435.783.6040 support@wkfluidhandling.com https://wkfluidhandling.comVer. 2.1.9 30 Dec 2021 P. 8Subject to change without notice
engineer approved PSA030 Owner’s Manual3.2 Calibrating D10 Amplifier for Stroke DetectionWhen calibrating the D10 Amplifier for stroke detection, the pump should be in the sameoperating conditions it will be in during normal operation (i.e. supply air pressure, backpressure, etc.). The Fiber Optic must be installed as per the instructions in section 3.1.Calibration:Push ButtonRemote LineResultHold Remote linelow (to ground) 2Seconds. Power LED: OFF Output LED: OFF Bar graph: LO & DOAlternately FlashingTEACHSensingConditions Hold push button. Operate pumpnormally for 15seconds. Hold remote linelow (to ground). Operate pumpnormally for 15seconds. Power LED: OFF Output LED: OFF Bar graph: LO & DOAlternately FlashingRelease buttonRelease remoteline/switchTeach AcceptedPower LED: ONBar graph: One LED flashes toshow relative contrast (successful setup requires minimumvalue of 4). Sensor returns to Run Mode with new settings.HSPress and holddynamic pushbutton 7654321HSDOLO87654321HSTeach UnacceptedPower LED: OFFBar graph: #1, 3, 5, 7 alternatelyflash to show failure to sense. Sensor returns to Run modewithout changing settings. Set up again if value shows 4.DOLOReturn toRun Mode87654321Upon completion of a successful learning cycle, the D10 Amplifier will continuously learn and self-teach tomaintain the same cycle rate count readings.Copyright 2021 White Knight Fluid Handling A Graco companyP: 435.783.6040 support@wkfluidhandling.com https://wkfluidhandling.comVer. 2.1.9 30 Dec 2021 P. 9Subject to change without notice
PSA030 Owner’s Manualengineer approved 3.3 Single Pressure Switch Stroke Detection Installation1.2.Remove plugfrom “F” port.Attach NPTgripper to“F” port.3.Attach elbow assembly to pressure switch.Loosen female gripper nuts, and insert air tubebetween them. Hand tighten gripper nuts.After your device is connected, you must set the switch point. If operating above 60 psi air supply, the set pointis 43 psi (0.296 MPa), otherwise it is 18 psi (0.124 MPa). Each system is unique so values may need to beadjusted to your specific application. As the exhaust system loads, it may be necessary to adjust the set point.3.4 Dual Pressure Switch Stroke Detection InstallationPerform all instructions to both sides of the pump.1.Attach T fittingsto the “S” ports.2.Attach mufflersto the T fittings.4.3.Attach elbow assembliesto pressure switches.5.Loosen female gripper nuts on elbowassemblies and T fittings. Inserttubing and hand-tighten gripper nuts.Affix supply air via 1/4 in FNPT QEVports on both sides. Air supply mustbe 1/4 in minimum orifice to source.After your device is connected, you must set the switch point. If operating above 60 psi air supply, the set pointis 43 psi (0.296 MPa), otherwise it is 18 psi (0.124 MPa). Each system is unique so values may need to beadjusted to your specific application. As the exhaust system loads, it may be necessary to adjust the set point.Copyright 2021 White Knight Fluid Handling A Graco companyP: 435.783.6040 support@wkfluidhandling.com https://wkfluidhandling.comVer. 2.1.9 30 Dec 2021 P. 10Subject to change without notice
engineer approved PSA030 Owner’s Manual3.5 Pressure Switch Stroke Detection Electrical HookupsNPNPNP50(1.969)35(1.378)80.315( )(0.3158 )ø3.7 ø0.146 cableCopyright 2021 White Knight Fluid Handling A Graco companyP: 435.783.6040 support@wkfluidhandling.com https://wkfluidhandling.comVer. 2.1.9 30 Dec 2021 P. 11Subject to change without notice
engineer approved PSA030 Owner’s Manual3.6 Conductivity Leak Detection InstallationLeaks are identified if conductive fluid contacts a sensor. Sensor provides a Sink (NPN)or Source (PNP) signal, depending on the wire setup. See the wiring diagrams below.1.2.Remove leakadapter fromassembly.Replace NPT plug in “L”port with probe. HandTighten. Attach cable tosignal translator (e.g. PLC).Wiring DiagramsConductive leak detection does not qualify for use in explosion-proof environments. Conductive fluid required.See below for elbowSource (PNP) Connectionout configuration.ConductivityLeak DetectWhite Power10-30White/Blue Load - VDCSink (NPN) ConnectionWhiteLoad PowerConductivity10-30Leak Detect- VDCWhite/Blue3.7 Fiber Optic Leak Detection InstallationD10 amplifier must be calibrated before attaching fiber optic probes to the pump.Fiber optic sensors can melt if used at 130 C (266 F), causing leak detect failure.See below for elbow out configuration.1.2.For straight out configurationreplace NPT plug in “L” portwith the probe. Hand-tighten.Remove leak adapter andleak detect probe fromfiber optic assembly.3.Insert the fiber opticcable until it contactsthe bottom of the probe.4.5.Lower ferrule and gripper untilsnug against the probe. Handtighten female gripper nut.Open the top and slide the front face of the D10 up.Press the fiber optic ends into the holes on its front.Slide the face down to lock cables in place.For elbow out configuration:1.1Replace NPT plug in “L”port with elbow adapter.Fiber opticConductivity1.2Attach fiber optic or conductivity leakdetect probe per instructions above.Copyright 2021 White Knight Fluid Handling A Graco companyP: 435.783.6040 support@wkfluidhandling.com https://wkfluidhandling.comVer. 2.1.9 30 Dec 2021 P. 12Subject to change without notice
PSA030 Owner’s Manualengineer approved 3.8 Calibrating D10 Amplifier for Leak DetectionStep 1: Power On D10 Amplifier & Set “Dark Operate” Mode:Press and hold bothbuttons 2seconds.Double-pulseremote lineTTTNote: Doublepulsing remote linecauses setting to“back up” one step.Sensor toggles through these setting combinations:LO - Normal Speed - No Delay (default)DO - Normal Speed - No DelayLO - High Speed- No DelayDO - High Speed- No DelayLO - Normal Speed - DelayDO - Normal Speed - DelayLO - High Speed- DelayDO - High Speed- DelayHSTT87654321Hold remote line low Green Power LED turns ON. 2 seconds. Sensor returns to Run 2 secondsmode with new settings.DOLOPress and holdboth buttons 2 seconds.87654321Pulse the remoteline until LEDs showdesired settings.TSelectSettingsReturnto RunMode Green Power LED turns OFF. Output LED remains active.2x Icons continue todisplay current setup. Bargraph turns OFF.TPress either button untilLEDs show desiredsettings.ResultHSRemote Line0.04 s T 0.8 sDOLOAccessSetupModePush Button0.04 s “Click” 0.8 sStep 2: Access “Single-Point Dark Set” ModeSingle-pulse remotelineTorHSDOLO1x87654321 Power LED: OFF. Output LED: ON (push button)OFF (remote line) Static LEDs: LO & DOalternately flashing87654321Press and hold staticbutton 2seconds.ResultHSRemote Line0.04 s T 0.8 sDOLOAccessSetModePush Button0.04 s “Click” 0.8 sStep 3: Set Sensing ConditionSet condition to “leak detection” sensing while probe tip is submerged in liquid.Then, remove the leak probe from liquid and reinserted into the “L” port.Amplifier will now signal when moisture if detected on the probe tip.Remote LineResult0.04 s T 0.8 s Present sensingcondition Five-click static buttonPresent sensing Power LED: ON.condition Output LED: ON (push button) Five-pulse remote lneOFF (remote line) Bargraph: 4 indicators flash.Sensor returns to Run mode with new settingsHS0.04 s “Click” 0.8 yright 2021 White Knight Fluid Handling A Graco companyP: 435.783.6040 support@wkfluidhandling.com https://wkfluidhandling.com87654321 Power LED: ON. Output LED: ON (push button)OFF (remote line) Bargraph: #1, 3, 5, 7 flash for failure.Sensor returns to Set sensing condition.DOLOSet Sensing ConditionPush ButtonVer. 2.1.9 30 Dec 2021 P. 13Subject to change without notice
PSA030 Owner’s Manualengineer approved 4. Ordering InstructionsRequired (Default Model)PSA0301Additional Options (Blank if not needed)- F0823- LF0 - SF0 - TF08 - VX0 4567RevOptions 1-3 are required. Leave Additional Options blank if not desired. Only add Outlet if different than Inlet.Default options are highlightedblank15 ft fiber optic cable with no amplifierLF015 ft fiber optic cable with D10 amplifierLF125 ft fiber optic cable with no amplifierLF225 ft fiber optic cable with D10 amplifierLF3blank15 ft conductivity cableLC0F25 ft conductivity cableLC1StandardPSA030Dry-RunPSA
White Knight is able to provide the highest quality fluid handling products through controlled, consistent in-house engineering and manufacturing. Through continued significant investments in engineering and manufacturing, we lead the industry with new technologies and products. White Knight has received numerous awards for innovation and