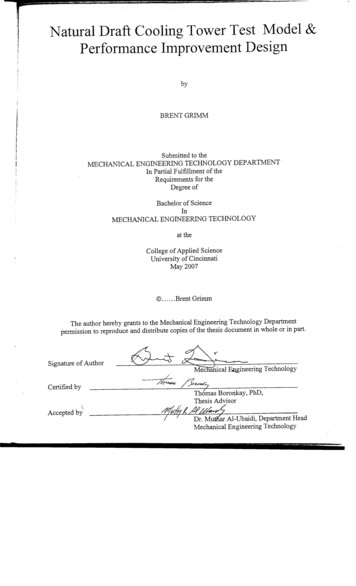
Transcription
Natural Draft Cooling Tower Test Model &Performance Improvement DesignbyBRENT GRIMM!!i'Submitted to theMECHANICAL ENGINEERING TECHNOLOGY DEPARTMENTIn Partial Fulfillment of theRequirements for theDegree ofBachelor of ScienceInMECHANICAL ENGINEERING TECHNOLOGYat theCollege of Applied ScienceUniversity of CincinnatiMay 2007 . Brent GrimmThe author hereby grants to the Mechanical Engineering Technology Departmentpermission to reproduce and distribute copies of the thesis document in whole or in part.Signature of Author eringCertified byThomas Boronkay, PhD,Thesis Advisor\Accepted by·41 /ltt.411 Technology
Natural Draft Cooling Tower Test Apparatus&Heat Load Improvement DesignBrent GrimmJune 6, 2007
NATURAL DRAFT COOLING TOWER TEST MODEL & RETROFIT DESIGN TESTBRENT GRIMMABSTRACTCurrently many power generation plants using a natural draft cooling tower are subject to a decreasein power production, and a loss of profits during hot summer months due to high condenser vacuumpressure. While products exist to test different types of fill, none exist that will test the entire systemand utilize the natural draft as the air mover, instead of a blower. A fully functional model of anatural draft cooling tower will be constructed with necessary data collection and logging capabilities.The model will then be tested extensively in order to develop a set of performance curves. Afterperformance curves have been established a design for a product that will increase the capability ofthe tower can be installed and tested to determine if the product is successful. This can be used sothat a person can test their product and eliminate some of the possibility that the product will notwork on a full scale natural draft cooling tower.1
NATURAL DRAFT COOLING TOWER TEST MODEL & RETROFIT DESIGN TESTBRENT GRIMMTABLE OF CONTENTSABSTRACT .1TABLE OF CONTENTS .2LIST OF FIGURES .3LIST OF TABLES .3LIST OF EQUATIONS .3PRELIMINARY ENGINEERING .4PROBLEM STATEMENT.4BACKGROUND RESEARCH .4VOICE OF THE CUSTOMER .7QUALITY FUNCTION DIAGRAM.8PRODUCT DESIGN . 10SELECTED DESIGN & ALTERNATIVES . 10LOADING CONDITIONS . 11TECHNICAL DRAWINGS . 12Cooling Tower Shell & Collecting Basin . 12Reheat Basin & Pump Stand . 13Fill & Fill Support . 14Water Distribution . 15Assembly Views . 16DESIGN ANALYSIS . 17COMPONENT SELECTION . 20USB I/O Module. 20Thermocouples . 21Cooling Tower Fill . 22Water Heater Element. 23Water Spray Nozzles . 24Water Pump . 25BILL OF MATERIALS . 25FABRICATION & ASSEMBLY . 26SYSTEM BASE . 26WATER DISTRIBUTION SYSTEM. 27TOWER SHELL . ERROR! BOOKMARK NOT DEFINED.METHOD OF TESTING. 32PROOF OF DESIGN . 33PROJECT MANAGEMENT . 34CONCLUSIONS & RECOMMENDATIONS . 35APPENDIX A – BILL OF MATERIALS .1APPENDIX B – CUSTOMER SURVEY RESULTS .1APPENDIX C – QFD MATRIX.1APPENDIX D - SCHEDULE .1APPENDIX E – ESTIMATED BUDGET .12
NATURAL DRAFT COOLING TOWER TEST MODEL & RETROFIT DESIGN TESTBRENT GRIMMLIST OF FIGURESFigure 1 – PVC Fill Sample .5Figure 2 – Plant Layout .5Figure 3 - Forced Draft Unit.6Figure 4 – Forced Draft System .6Figure 5 – Mechanical Draft Model . 10Figure 6 - Measurement Computing USB I/O Module . 20Figure 7 - Thermocouple. 21Figure 8 - Brentwood Industries Fill . 22Figure 9 - Digg Corp. Misting Nozzles . 24Figure 10 - Drill Powered Water Pump . 25Figure 11 - Base Frame . 26Figure 12 - Finished Base . 26Figure 13 - Drill Pump Installed . 28Figure 14 - Hot Water Riser / Cold Water Drain . 28Figure 15 - Water Distribution Header . 29Figure 16 - Reheat Basin . 30Figure 17 - Total Assembly . 31LIST OF TABLESTable 1- Design Load Conditions . 11Table 2 – Characteristic Coefficient Calculation . 18LIST OF EQUATIONSEquation 1: Characteristic Coefficient .7Equation 2: Simplified Characteristic Coefficient .73
NATURAL DRAFT COOLING TOWER TEST MODEL & RETROFIT DESIGN TESTBRENT GRIMMPRELIMINARY ENGINEERINGPROBLEM STATEMENTA common problem encountered at an electric power plant occurs during the summer when theair temperature and humidity are very high. Any plant using a natural draft cooling tower often lacksthe necessary cooling capacity during these periods forcing the plant to reduce their total poweroutput. It is also during these periods in which electricity is at its peak demand and price due toHVAC systems operating almost constantly. Not only does the reduced power output reduce totalprofits, it also creates the possibility of rolling black outs. Natural draft cooling towers are in need ofa system that would provide the additional cooling capacity necessary for the plant to operate at 100%output. The ideal system would run only when necessary and have the capability to be taken out ofservice when the tower is able of adequately reducing water temperature without assistance. Anotherproblem arises after an improvement design is complete, and that is available test methods. Currentlyseveral test devices are in use, but these test specific sub-systems of a tower rather than the tower as awhole. These methods generally eliminate conditions that are seen in an operating tower and in orderto appropriately evaluate the effectiveness of a design the conditions would need to be very similar.In order to effectively evaluate an improvement design a new method of testing is needed that iscapable of accurately recreating conditions seen in an operating natural draft cooling tower.BACKGROUND RESEARCHThere are many power generating stations currently operating that utilize a natural draft coolingtower as means of reducing the temperature of the circulating water after absorbing heat from thecondensers and other heat exchangers. A natural draft cooling tower is a very simple means ofcooling off water and popular among large circulating water systems because no input power isrequired. A natural draft tower utilizes the principle of natural convection as a means of circulatingair through the tower. When looking at a natural draft tower an opening at the bottom near theground can be seen, this is the air inlet. Inside the tower around 30-50 ft above the air inlet is a largewater distribution system that sprays water on top of a fill system. The fill system is simply acollection of PVC sheets that slow air and water as the two come in contact with each other in orderto maximize the amount of heat transferred. It is important that the nozzles break the stream of waterup in to small droplets because this creates a greater amount of contact area which again furthermaximizes the amount of heat transferred.4
NATURAL DRAFT COOLING TOWER TEST MODEL & RETROFIT DESIGN TESTBRENT GRIMMFIGURE 2 – PLANT LAYOUTFIGURE 1 – PVC FILL SAMPLEAs the air travels through the fill it absorbs heat from the water and rises due to the lower density ofhotter air. The hot air exits the tower drawing in cold air through the inlet.Natural draft cooling towers are a great method of cooling the water in a circulating system,especially if it is being used in a large plant with high circulating water flow rates. This is becausethis style of tower does not need a power source like its counterpart the mechanical draft tower. Theinput requirement for a mechanical draft tower is proportional to the amount of heat transferred, andbecause large volumes of water require large amounts of transferred energy to reduce the averagetemperature it becomes economical to use a natural draft tower instead. The natural draft tower isoften called, “free cooling”; however, there are several downsides to the natural draft cooling tower.The first problem is the physical size of the tower compared to the size of a mechanical draft tower.The picture in Figure 2 shows the size of a natural draft tower relative to the entire plant. A mediumsized tower will be almost 500 ft. tall, and 400 ft. in diameter at the base of the tower. Anotherproblem with the natural draft tower is testing and determining the performance of the tower. Theperformance test that is approved by the Cooling Tower Institute is the standard test used by everymanufacturer to guarantee the performance of their product. This test must be conducted in nearperfect conditions with very little change in any of the process parameters, and it can only produceresults with an error of 5%. There is no accurate means of measuring the air flow rate, nor is therean easy means of calculating because of the complex heat transfer and mass transfer processes thattake place as the air and water travel through the fill. There are also many factors such as theposition of the sun, season, wind velocity and direction, and many more, that seem to affect everytower differently. The last major problem is the lack of products available to provide a significantincrease in the cooling capacity of the tower. Small gains can be obtained by fixing damaged fillcells, replacing broken nozzles, and flow balancing. These improvements can slightly increase thecooling capacity of a tower, but with innovations being made in turbines and other components, a5
NATURAL DRAFT COOLING TOWER TEST MODEL & RETROFIT DESIGN TESTBRENT GRIMMgreater increase in cooling capacity will be required. Currently if you want a large increase incapacity there are two options. The first option is to install mechanical draft towers in series with thenatural draft tower and only use the mechanical draft when it is needed. Figure 3 shows a picture ofa mechanical draft tower that would be used along side of the natural draft. The second option is todemolish the tower and install a system of mechanical draft towers (shown in Figure 4) or a largernatural draft tower.FIGURE 3 - FORCED DRAFT UNITFIGURE 4 – FORCED DRAFT SYSTEMThere have been several attempts at designing an addition for the natural draft tower that havebeen unsuccessful. See Appendix A for several examples of other ideas. Most involve the use offans at the air inlets attempting to force air into the tower. These types of systems have not beensuccessful because the resistance to the air traveling up through the fill is high enough that it requiresless energy to cause air to spill out of the inlet than forcing it through the fill. A problem that ariseswith developing a solution is that there is no real method of testing besides installing the proposedidea on an operating tower; this is a risk very few plant managers are willing to take. There areseveral test apparatus’ currently in use; however each device is for testing a specific sub-system ofthe tower, not the system as a whole. This eliminates a lot of the conditions that are seen by anoperating tower. The best way to recreate the conditions of an operating tower is to create a workingmodel of the tower. Once the model is created the performance curves could be developed by testingin various conditions. Design ideas could then be built, installed, and tested on the model todetermine if the projected improvement can be achieved. By comparing the operating curves beforeand after installing the design the actual improvement could be determined. However it cannot beassumed that the same magnitude of improvement would be seen by the actual tower that was foundin model tower, because the model would not be a scale version of the real tower.6
NATURAL DRAFT COOLING TOWER TEST MODEL & RETROFIT DESIGN TESTBRENT GRIMMThe actual design process for determining the size of a needed tower has been made into a fairlysimple process by the Cooling Tower Institute. The first step is determining the temperature dropneeded in the circulating water and the temperature of the air that will be entering the tower in orderto calculate the characteristic coefficient of the tower. Equation 1 is the formula for the coefficient,which is the relationship between the physical dimensions of the tower and the thermodynamiccharacteristics of the tower.t widt wKaV cwt woLi ' s iaEQUATION 1- CHARACTERISTIC COEFFICIENTK Mass Transfer Coefficienta contact area / tower volumeV Total Fill HeightL Water Flow LoadingCw Specific Heat of Waterdtw Change in Water Temp.twi Temp. of Water Intwo Temp. of Water Outi s Enthalpy of Saturated Air at Water Temp. twia Enthalpy of Moist AirSolving the integration for that equation would be difficult because the temperature of the air andwater are constantly changing, so by using the Merkel Model for Counter-flow recommended by CTI,the right side of the equation can be simplified. The simplified equation is shown in Equation 2.dt w t wi t wo 4 1 two i' s ia 4 j 1 i j i1 [Enthalpy of saturated air @ t wot wicw111 t wi t wo 1 * 4 i1 i2 i3 i4 .1 * (t wi t wo )] [i1 .1 * (i2 i1 )] i2 [Enthalpy of saturated air @ t wo .4 * (t wi t wo )] [i1 .4 * (i2 i1 )] i3 [Enthalpy of saturated air @ t wo .6 * (t wi t wo )] [i1 .6 * (i2 i1 )] i4 [Enthalpy of saturated air @ t wo .9 * (t wi t wo )] [i1 .9 * (i2 i1 )]EQUATION 2- SIMPLIFIED CHARACTERISTIC COEFFICIENTAfter calculating the value of the characteristic coefficient the designer would then refer to a coolingtower design standards books which provides many different possible dimensions of a tower whilemaintaining the characteristic coefficient. Using the operating specifications, the correct set ofphysical dimensions are selected which provides all other necessary information.VOICE OF THE CUSTOMERIn order to determine the strength of the market in a new natural draft cooling tower test device,7
NATURAL DRAFT COOLING TOWER TEST MODEL & RETROFIT DESIGN TESTBRENT GRIMMas well as the importance of different aspects of the device, a survey was distributed to engineers,consultants, and technicians in the cooling tower industry. An example of the survey with the resultscan be found in Appendix B. The first question was to gauge the level of interest to ensure that thiswas a product that people would consider purchasing. The average answer for the first question was athree on a scale of 1-5, indicating that people were moderately interested in a new test device. Thiswas about the interest level that was expected. The customer was then asked to rank five features ona scale of 1-5 where 1- not important and 5-very important. The first feature the customer ranked wasthe importance of the aesthetic accuracy of the model compared to the full scale version. We neededto know if the customer wanted the model to look exactly like the existing tower or if it was not afactor that concerned them. We found that the physical similarity between the model and full scaleversion was not something that most customers were concerned about. The next question asked themto rank the importance of the ability of the test device to produce thermodynamic results similar tothose seen in the full scale tower. This was the number one most important factor that the consumerwas concerned with. The third feature the customer ranked was the level of automation. We wantedto know if customers want this device to operate safely with no human supervision, or would theyrather a human be responsible for the controls. The fourth factor was one of the concerns for thisproject and that is the mobility of the device. It was expected that the tower would be too large andbulky to easily maneuver around, however the customer did indicate that some level of mobility isdesired. The final feature ranked was the accuracy of the instrumentation which received an averagerating of four. We know for sure that this is the second most important factor of this system, so it willbe vitally important to include reliable data collection hardware and software, as well as accuratethermocouples. Next we wanted to know how often their plant must reduce load due to highcirculating water temperatures. We found the average answer to be between two and three meaningthat it doesn’t occur often but it is not a rare event either. Even though the frequency of this event isnot very large, it is a consistent problem that occurs on a regular basis. For the last question wewanted to know what level of cooling capacity increase was necessary for the customer to giveserious consideration into installing a cooling capacity improvement device. The average range ofimprovement was 5%-15%. Next a list of engineering features were developed that would addressthe product specifications.QUALITY FUNCTION DIAGRAMAfter the customer needs had been established the next step was to develop engineering featuresthat would address those needs. The first feature is that the model will have a characteristic8
NATURAL DRAFT COOLING TOWER TEST MODEL & RETROFIT DESIGN TESTBRENT GRIMMcoefficient of 1.5768 which is the same as the full scale tower. By setting the value of this coefficientequal to the real tower’s coefficient and working backwards through the calculations we insured thatthe test model performed similar to the existing tower. The next feature that was determined was thetemperature drop which is the difference between the temperature of the hot water and thetemperature of the cold water. This was set at a range of 15-30 degrees. A ratio called the L/G ratiowill be equal to the full scale tower’s L/G ratio. It was also decided that the fill would be about 6”deep. Next the accuracy of the thermocouples and USB IO module was determined as well as thesample rate of the USB IO module in order to address the issue of accuracy of instrumentation. Thetotal number of thermocouples needed to accurately conduct performance tests was determined asanother feature to address accuracy of instrumentation as well as level of automation. Keeping inmind the safety of the test device it was decided that one emergency button would be installed thatwould allow the user to cut power to all components. Locking casters were selected to address theneed for mobility. These factors as well as the customer needs were inserted in to a quality functiondiagram allowing the importance of features to be evaluated. The completed QFD matrix can be seenin Appendix C.9
NATURAL DRAFT COOLING TOWER TEST MODEL & RETROFIT DESIGN TESTBRENT GRIMMPRODUCT DESIGNSELECTED DESIGN & ALTERNATIVESBefore a working model of a natural draft tower was decided upon as being the test apparatus,several other methods of testing were considered. The first option was building a small test cell thatuses a fan to circulate the air through the test cell similar to test apparatus shown in Figure 5. Therewere several issues that ruled this out as our design. The primary reason it was ruled out was becausewe want to see how the natural draft reacts to proposed upgrades, and a fan does not reproduce anatural draft flow. A second reason for ruling this out was that we wanted to incorporate all theunknown factors that are involved with the towers currently in service. A mechanical draft towereliminates many of the unsure factors that act on a natural draft tower. The final reason we did not dothis was because it would not be a new product. Many people have constructed a mechanical draftcooler of some sort so we would not be creating anything original. The number one goal of thismodel is to recreate the conditions seen by a natural draft tower, and you cannot do this using withouta natural draft flow. The natural draft is a very unique flow and the best way to study it is to create it.FIGURE 5 – MECHANICAL DRAFT MODELA second idea that wasconsidered was creating a modelingprogram for the computer. The biggestproblem there is that the program is onlycapable of calculating what you haveprogrammed it to calculate. If theprogrammer overlooks some outsideforce acting on the system then theresults produced by the model would beinaccurate. It would also be verydifficult to identify every force andquantify it so that it could be calculatedand modeled. The final reason foreliminating this as a possibility wasbecause in the mixing region as both the air and water fall through the fill, there is heat transfer takingplace as well as mass transfer as some of the water is turned to vapor and exits with the air. The levelof programming that would be necessary to solve the differential equations was beyond our skilllevel.After looking at all of our ideas for a test device it was decided that a working model of a naturaldraft tower was the only option that provided all of the features that are needed. We did decide that a10
NATURAL DRAFT COOLING TOWER TEST MODEL & RETROFIT DESIGN TESTBRENT GRIMMlaptop would be used to monitor the performance of the system, as well store all of the data points sothat accurate performance curves can be generated. Thermocouples will be used to measure thetemperature of the inlet and outlet air as well as the inlet and outlet water. This will insure that thecustomer is able to collect accurate consistent data. The test model will be designed based on thenatural draft cooling tower at Duke Energy’s Zimmer Station. This will allow us to compare resultsof the test model to the performance curves of the Zimmer Station tower to see how close we couldrecreate the operating tower’s conditions.LOADING CONDITIONSIn Table 1 the load conditions decided upon are displayed. These were developed using datafrom a CTI performance test that was performed on the Zimmer tower. The water flow rate wasscaled down by a scale of 100 3 because the linear scale used to determine physical dimensions was100:1, and the flow is directly related to the physical dimensions.TABLE 1- DESIGN LOAD CONDITIONSDesign Load Conditions for ModelHot Water Temperature107.0 oFCold Water Temperature80.0 oFWater Flow Rate0.45 GPMDry Bulb Temperature33.0 oFRelative Humidity50.0 %Heat Load6231.0 btu/hr11
NATURAL DRAFT COOLING TOWER TEST MODEL & RETROFIT DESIGN TESTBRENT GRIMMTECHNICAL DRAWINGSCOOLING TOWER SHELL & COLLECTING BASIN12
NATURAL DRAFT COOLING TOWER TEST MODEL & RETROFIT DESIGN TESTBRENT GRIMMREHEAT BASIN & PUMP STAND13
NATURAL DRAFT COOLING TOWER TEST MODEL & RETROFIT DESIGN TESTBRENT GRIMMFILL & FILL SUPPORT14
NATURAL DRAFT COOLING TOWER TEST MODEL & RETROFIT DESIGN TESTBRENT GRIMMWATER DISTRIBUTION15
NATURAL DRAFT COOLING TOWER TEST MODEL & RETROFIT DESIGN TESTBRENT GRIMMASSEMBLY VIEWS16
NATURAL DRAFT COOLING TOWER TEST MODEL & RETROFIT DESIGN TESTBRENT GRIMMDESIGN ANALYSISThe limiting factor for this model will be the physical size, so the dimensions of the tower weredetermined by using a scale of 1/100 of the natural draft cool
NATURAL DRAFT COOLING TOWER TEST MODEL & RETROFIT DESIGN TEST BRENT GRIMM 1 ABSTRACT Currently many power generation plants using a natural draft cooling tower are subject to a decrease in power production, and a loss of profits during hot summer months due to high condenser vacuum pressure.