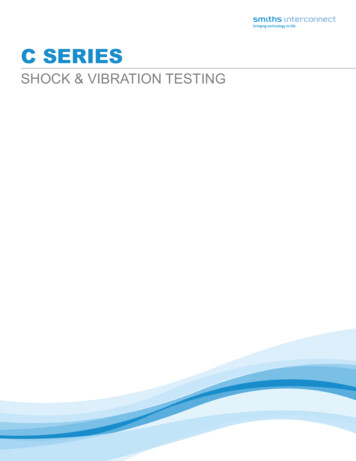
Transcription
C SERIESSHOCK & VIBRATION TESTING
CONTENTS1PERFORMANCE2TEST REPORT OVERVIEW3CONTACT DESCRIPTION4TEST SET UP DESCRIPTION5NANO INTERRUPTION DETECTION6DYNAMIC CONTACT RESISTANCE7VISUAL INSPECTION AFTER TEST8CONCLUSION9CONTACTin shock and vibrationin shock and vibrationbias ball and bias plungerINTERCONNECT DEVICES, INC.5101 Richland Ave. Kansas City, KS 66106 USAT: 1 913 342 5544F: 1 913 342 7043info@idinet.comwww.idinet.com
PERFORMANCE
TEST REPORT OVERVIEWMilitary air, sea, and land applications present unusually severe requirements for durability andstability to the connectors that unite their electrical systems. Extreme conditions of shock, vibrationand acceleration can cause issues with electrical stability and contact degradation over time.IDI’s advanced C Series contacts offer exceptional compliance, modularity, and design flexibility ina wide range of applications. Electrical performance of contacts designed for power applicationsis assured using a proven ‘bias plunger’ design. To enhance the capability of the series in militaryapplications, IDI has developed a version which uses a ‘bias ball’ device to guarantee electricalperformance especially in terms of vibration and shock. This paper is an exploration of the contrastingcapabilities of each type. To quantify this difference, the bias ball and bias plunger versions of IDI’sC Series Spring Probes were rigorously tested using the full capabilities of IDI’s highly regarded testlaboratory.Characteristics tested included endurance vibration and shock tests along several axes on a widefrequency range. The survivability of the contacts was examined, as well as electrical stability throughstatic and dynamic contact resistance measurements. Extensive testing according to the ANSI/EIA-364 standard was performed to quantify the technology’s performance to these standards. Theresults of those tests are captured in this document.C SERIES PROBESFeaturing three primaryterminations: surface mount,thru hole and solder cupINTERCONNECT DEVICES, INC.5101 Richland Ave. Kansas City, KS 66106 USAT: 1 913 342 5544F: 1 913 342 7043info@idinet.comwww.idinet.com
CONTACT DESCRIPTIONThe samples subjected to this test plan were two versions of the IDI 2.54mm C Series Family. This series of contacts isdesigned for maximum application flexibility. IDI offers two mated heights, four and six millimeter; two plunger extensionvalues, to permit easy hot-swap capability through extended grounding contacts; and three termination variants, for surfacemount, thru hole and cable attachment. The probes are also offered in power, signal and ground configurations, with eachhaving different electrical performance versus cost. The creation of the bias ball version of the contact is an extension of thecapability of the power variants, and this paper contrasts bias plunger versus bias ball designs to evaluate their suitabilityto that task.BIASED PLUNGERBIASED PLUNGERWITH BIAS BALLFigure 1aFigure 1bProbes are ‘biased’ to ensure solid contact between theprobe’s plunger and its barrel. If the current can easily travelbetween these two components, it avoids the relatively highresistance path of the spring. Non-axial force delivered tothe plunger causes greater intimacy of contact betweenthe plunger and the barrel; thus, side force is inverselyproportionate to contact resistance.direction. By interposing a ball between the spring and theplunger, this tendency can be enhanced, and a backupcurrent path is created. By contrast, space for the ball giventhe same overall probe length must be taken from either thespring, limiting travel or the plunger, reducing the bearingsurface length that guides the plunger and forms the currentpath.While the application may be expected to deliver a degreeof non-axial force, bias designs build this tendency into theinner workings of the probe. By creating an angle on thebottom of the plunger, as is the case with the bias plungerdesign, the spring delivers some of its force in a non-axialEach basing technique has significant merit in conditions ofshock and vibration. Both greatly enhance the stability ofcontact resistance in these extremes, and can mechanicallystabilize the position of the plunger through side force tolimit the possibility of internal fretting.INTERCONNECT DEVICES, INC.5101 Richland Ave. Kansas City, KS 66106 USAT: 1 913 342 5544F: 1 913 342 7043info@idinet.comwww.idinet.com
TEST SET UP DESCRIPTIONTwo sets of connectors were created with two rows of sixteen contacts soldered by thru hole termination into plated throughholes in a printed circuit board and connected in a series circuit. The connectors were then compressed to their nominalvalue onto an antagonist gold plated PCB and tested in conditions of vibration and shock at different levels across multiplefrequencies.C Series Probes @ 2.54mm pitchzxyCONTACT CONNECTORFigure 2aTEST FIXTURE FOR Z-AXIS TESTFigure 2bINTERCONNECT DEVICES, INC.5101 Richland Ave. Kansas City, KS 66106 USAT: 1 913 342 5544F: 1 913 342 7043info@idinet.comwww.idinet.com
NANO INTERRUPTION DETECTIONVIBRATIONDuring this monitoring, No Nano interruption 2ns was found clearly demonstrating thatIDI C Series Probes, both bias plungerand bias ball designs, exhibit remarkableperformance even in the most severeenvironments.140ACCELERATION LEVEL (G)Acceleration at plunger/topPCB interface 120 GFIXTURE X (input)120FC3Top 60018002000FREQUENCY (Hz)RESONANCE FREQUENCIES OF THE SYSTEM ALONG XGraph 1140FIXTURE Z (input)120ACCELERATION LEVEL (G)Nano interruption detection was performedcontinuously during characterization andendurance tests at different input levels upto 15G. The total test time is more than 4hours per axis where the frequency wassweeping from 20 to 2000Hz with 1 Oct/min change rate. The resulting frequencybehavior of the system is presented belowfor each axis. It shows that the completesystem has several resonance frequenciesthat correspond to the worst case scenariosin terms of vibration. Indeed the 15G inputhas been measured on the vibration tablebut, due to the resonance of the system,the acceleration measured at the interfacebetween the spring probes and the top PCBis much higher at resonance frequenciesand can reach up to 120G (X axis) and 60G(Z axis).Top PCB10080Acceleration at plunger/topPCB interface 60 NCY (Hz)1400160018002000RESONANCE FREQUENCIES OF THE SYSTEM ALONG ZGraph 2SHOCKIn addition to the endurance vibration, thesamples were submitted to shock testsfor each axis at different levels up to 50G(11ms impulse as shown below). Onceagain, no Nano interruption 100 ns wasfound during the tests both for the biasplunger and bias ball designs.SHOCK IMPULSEGraph 3INTERCONNECT DEVICES, INC.5101 Richland Ave. Kansas City, KS 66106 USAT: 1 913 342 5544F: 1 913 342 7043info@idinet.comwww.idinet.com
DYNAMIC CONTACT RESISTANCEThis dynamic contact resistance monitoringwas completed on each axis duringfrequency sweeping but also for eachresonance frequency of the system toensure that even at these critical frequenciesthe contact resistance remains stable over along period of time. Stability is defined as 5min per resonance frequency.Below are the resulting illustrations of thecontact resistance for both the bias plungerand bias ball designs. The resonancefrequencies of the system have beenreported for information. Stability of contactresistance of IDI spring probes is clearlydemonstrated with the bias ball designoffering superior contact resistance and aneven greater stability.BIASED PLUNGERFc1Fc2Fc3Fc47CONTACT RESISTANCEThrough IDI’s expertise in testing and dataacquisition, a test methodology was createdallowing for dynamic monitoring of thecontact resistance of a single contact duringvibration with an acquisition rate up to 20Hz.BIAS QUENCY (Hz)DYNAMIC CONTACT RESISTANCE DURING FREQUENCY SWEEPING: X AXIS -15G INPUTGraph 4BIAS BALLBIASED PLUNGERFc1Fc2Fc3Fc48CONTACT RESISTANCEProviding contact continuity during vibrationand shock is critical for harsh environmentapplications but it may not be sufficient ifthe quality of the transmitted signal is notadequate. The contact resistance of thespring probes must therefore be kept asstable as possible to guarantee a constantand reliable 0FREQUENCY (Hz)DYNAMIC CONTACT RESISTANCE DURING FREQUENCY SWEEPING: Z AXIS -15G INPUTGraph 5BIAS BALLBIASED PLUNGER8CONTACT RESISTANCE (mohm)NOTESAfter investigation, the CRES variationsat low frequency are induced by testset up frequency (displacement of theaccelerometers 0205:46TIME (min)DYNAMIC CONTACT RESISTANCE AT WORST RESONANCE FREQUENCYFC 1550Hz - X-AXIS -15GGraph 6INTERCONNECT DEVICES, INC.5101 Richland Ave. Kansas City, KS 66106 USAT: 1 913 342 5544F: 1 913 342 7043info@idinet.comwww.idinet.com
VISUAL INSPECTION AFTER TESTAfter the rigorous vibration and shock test sequences, accounting for a total test time of more than 10 hours, a visualinspection of the probe interface (plunger and mating PCB) was performed to ensure there was no fretting corrosion or wearconcerns. Both the bias plunger and bias ball connectors illustrate excellent surface finish with minimal indentation marksas shown below:BIAS BALLPHOTO OF CONTACT SURFACES AFTER TESTING FOR BIAS BALL CONFIGURATIONFigures 3a and 3b*BIAS PLUNGERPHOTO OF CONTACT SURFACES AFTER TESTING FOR BIAS PLUNGER CONFIGURATIONFigures 3c and 3d**Scratches on the pad area occur during system alignment not vibration testing.INTERCONNECT DEVICES, INC.5101 Richland Ave. Kansas City, KS 66106 USAT: 1 913 342 5544F: 1 913 342 7043info@idinet.comwww.idinet.com
CONCLUSIONThorough and exhaustive testing performed in the course of this exercise demonstrates that all C SeriesSpring Probes passed the vibrations tests 15G and shock tests 50G regardless of the internal biasingtechnology. They are therefore compliant with Mil-Aero standard requirements and can safely be used forharsh environment applications.Looking more closely at the test results, it is revealed that the C Series Probes actually passed tests withhigher acceleration levels. During the resonance frequencies testing, the 15G input resulted in levels up to120G (Radial direction) and 60G (Axial direction) at the interface between PCB and spring probe plunger.Comparing the different biasing techniques we can see that bias ball offers better results and CRES stabilitythan the bias plunger technology.After more than 10 hours of vibration and shock testing, the contact surfaces of the spring probe tip andPCB are still free of any wearing or fretting corrosion with near perfect surface finish.
SHOCK & VIBRATION TESTING. INTERCONNECT DEVICES, INC. 5101 Richland Ave. Kansas City, KS 10 USA T: 1 1 42 5544 F: 1 1 42 04 ino@idinet.com .idinet.com PERFORMANCE TEST REPORT OVERVIEW CONTACT DESCRIPTION TEST SET UP DESCRIPTION in shock and vibration NANO INTERRUPTION DETECTION in shock and vibration .