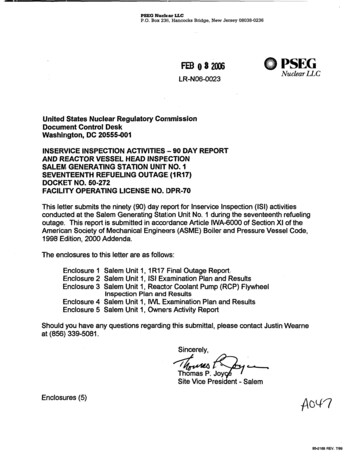
Transcription
PSEG Nuclear LLCP.O. Box 236, Hancocks Bridge, New Jersey 08038-0236FEBO PSEGNuclearLLC@8 2006LR-N06-0023United States Nuclear Regulatory CommissionDocument Control DeskWashington, DC 20555-001INSERVICE INSPECTION ACTIVITIES - 90 DAY REPORTAND REACTOR VESSEL HEAD INSPECTIONSALEM GENERATING STATION UNIT NO. ISEVENTEENTH REFUELING OUTAGE: (1R17)DOCKET NO. 50-272FACILITY OPERATING LICENSE NO. I)PR-70This letter submits the ninety (90) day report for Inservice Inspection (ISI) activitiesconducted at the Salem Generating Station Unit No. 1 during the seventeenth refuelingoutage. This report is submitted in accordance Article IWA-6000 of Section Xi of theAmerican Society of Mechanical Engineers (ASME) Boiler and Pressure Vessel Code,1998 Edition, 2000 Addenda.The enclosures to this letter are as follows:Enclosure 1 Salem Unit 1, 1R1 7 Final Outage Report.Enclosure 2 Salem Unit 1, ISI Examination Plan and ResultsEnclosure 3 Salem Unit 1, Reactor Coolant Pump (RCP) FlywheelInspection Plan and ResultsEnclosure 4 Salem Unit 1, IWL Examination Plan and ResultsEnclosure 5 Salem Unit 1, Owners Activity ReportShould you have any questions regarding this submittal, please contact Justin Wearneat (856) 339-5081.Sincerely,Thomas P. Joys1Site Vice President - SalemEnclosures (5)A04 795-2168 REV. 7/99
LR-N06-0023Document Control DeskC:2Mr. S. Collins, Administrator - Region ILU. S. Nuclear Regulatory Commission475 Allendale RoadKing of Prussia, PA 19406Mr. S. Bailey, Project Manager - SalemU.S. Nuclear Regulatory CommissionMail Stop 08B1Washington, DC 20555-0001USNRC Senior Resident Inspector - Salem (X24)Mr. K. Tosch, Manager IVBureau of Nuclear EngineeringP. O. Box 415Trenton, NJ 08625Mr. Milton WashingtonChief InspectorNJ Department of LaborDivision of Public Safety, Occupational Safety and HealthBureau of Boiler and Pressure Vessel ComplianceP. O. Box 396101 South Broad StreetTrenton, NJ 08625-0392
LR-N06-0023Enclosure 1Salem Unit 1, I RI7 Final Outage Report
SALEM UNIT IINSERVICE INSPECTION PROGRAMFINAL OUTAGE REPORT3rd INTERVAL / 2nd PERIOD /Ist OUTAGEREFUELING OUTAGE 1R17Fall 2005FINAL REPORT1
ABSTRACTThis report represents an accumulation of information pertaining to the IS In-Servicesactivities conducted during Salem Unit 1 Refueling Outage 1RI 7.PSEG Nuclear LLC (PSEG), Framatome - ANP (FTI), Magnaflux Quality Services (MQS),and Wesdyne, personnel performed an inservice examination (ISI) of selected Class 1,Class 2, Class 3, and CLASS MC, components PSEG Salem Generating Station, Unit 1(Salem 1), during October 11, 2005 - November 6, 2005 (25 days). These examinationsconstituted the Seventeenth (2nd Period, 1st Outage) refueling outage at Salem Unit 1.This Final Report covers the time period (approximately 18 months) between breakerclosures after I RI 6 through breaker closure after 1RI 7.PSEG Nuclear submitted documentation to the NRC and updated the Salem Unit 1 CodeEdition from the 1995 Edition, 1996 Addenda to the 1998 Edition, 2000 Addenda in order toalign Salem Units 1 and 2 and Hope Creek; to the same Edition and Addenda of the Code.NDE exams were performed in accordance with the ASME Section Xl 1998 Edition 2000Addenda. Appendix VIII exams were performed to the 1998 Edition 2000 Addenda asamended by Final Rule and 1998 Edition, IIWE / IWL 1998 Addenda of ASME Section Xland the Salem Inservice Inspection Program Long Term Plan.ISI was performed utilizing visual (VT), magnetic particle (MT), liquid penetrant (PT),manual ultrasonic (UT), and radiography (RT) nondestructive examination techniques.This report also contains augmented examinations required by the Salem TechnicalSpecifications, and Regulatory Commitments, Circulars and Bulletins issued by the UnitedStates Nuclear Regulatory Commission.
1. SUMMARY REPORTDuring the Fall 2005 refueling outage (1R1 7), PSEG, MQS, FTI, and Wesdyne personnelperformed nondestructive examinations (NDE) of selected Salem Generating Station, Unit1 Class '1,Class 2, Class 3 and Class MC components. These examinations constitutedthe Seventeenth (2r'd Period,1 st Outage) In-service Inspection (ISI) during the Third TenYear Inspection Interval, of commercial operation.A.Applicable DocumentsThe ISI was conducted in accordance with the following documents:Section XI of the American Society of Mechanical Engineers (ASME) Boiler andPressure Vessel (B&PV) Code, "Rules for Inservice Inspection of NuclearPower Plant Components", 1998 Edition 2000 addenda, and IWE / IWL to the1998 Edition, 1998 addenda.*10-Year Inservice Inspection Program for Salem Nuclear GeneratingStation Unit 1 (Third Interval) Initial Issue.*PSEG's Salem Nuclear Generating Station Unit 1, Outage ISI ExaminationPlan (Rev. 0), Third Interval, Second Period, First Outage (10/11/2005through 11/06/2005).* ASME Section Xl Appendix Vil examinations were performed inaccordance with ASME Section Xl, Div. 1,1998 Edition, and 2000 AddendaAppendix Vil, as amended by the Federal Register Notice 67FR60520 through67FR60542 dated September 26, 2002.B.ISI Section XI examinations performed.Framatome - ANP (FTI) under the direction of PSEG Nuclear's ISI Group, conductedzero mechanized ultrasonic, 48 manual ultrasonic, 6 liquid penetrant, II magneticparticle examinations.During 1R1 7, PSEG Nuclear implemented Risk Informed Inservice Inspection(RI-ISI) of Nuclear Class 1 and 2 Piping Welds, formerly known as ASME Section XlExam Category B-F, B-J, C-F-1 and C-F-2. The bases of the Salem Unit I RI-ISIProgram are documented in the Salem Nuclear Generating Station - Final Report Risk Informed Inservice Inspection Application (VTD-326046).Examinations were performed of the following components and systems.
Class IVessels* Reactor Pressure Vessel* Steam Generators* PressurizerPiping* Reactor Coolant* Safety Injection* Residual Heat Removal* Chemical Volume ControlClass 2Vessels* Steam Generator* Boron Injection Tank* Residual Heat ExchangersPiping* Boiler Feed* Main Steam* Chemical Volume Control* Containment Spray* Auxiliary Feed* SamplingClass 3Piping* Service Water* Auxiliary Feedwater* Component CoolingC.ISI Section Xi Visual examinations on valves and boltingPSEG's ISI Group conducted zero Class 1 Exam Categories B-G-2 bolting exams orB-M-2 valve internal exams during this outage.
D.ISI Section Xl Visual examination of components supportsPSEG conducted one hundred and twenty-five (125) Class 1, 2 & 3 componentsupport visual VT-3 examinations,ISI Section XI examinations were conducted on the following systems:Auxiliary FeedResidual Heat RemovalChemical VolumeMain SteamComponent CoolingSafety InjectionContainment SprayReactor CoolantService WaterThe following components were observed possessing indications that requiredfurther evaluation.Sum#Component I.D.DescriptionRemarksHANGERSpring Can Setting High20256926 Generated1A-11RHRH-016HANGERSpring Can Setting High1A-11 RHRH-017HANGERSpring Can 20256926Setting ication 20256926 Generated5056251A-11RHRH-018HANGERSpring Can Setting High5056301A-1 I RHRH-020HANGERSpring Can Setting High1A-12RHRH-014HANGERHAGERSpringCan Setting HighNotification 20256926 cationSpring Can 20256926Setting HighGenerated.5056855059201A-505695Notification 20256926 GeneratedNotification 20256926 Generated5056951A-12RHRH-017HANGERSpring Can Setting High5059201A-12RHRH-024HANGERSprdng Can Setting High1A-12RHRH-026HANGERSpring Can Setting HighHANGERSpring Can Setting ion514651-CCE5HEATEXCHANGERSUPPORTNotification 20256926 GeneratedNotification 20256926 Generated20256926 Generated20256926 GeneratedConcrete Building StructurePedestal Cracked Notification20257792 Generated
There were zero unacceptable conditions observed during the conduct of othercomponent supports visual examinations.E.RCP Flywheel Examination per USNRC Regulatory Guide 1.14Framatome-ANP completed required ultrasonic and surface examinations of # 12reactor coolant pump flywheel (Serial # 2S75P790) in accordance with stationtechnical specification requirements.There were zero unacceptable indications identifiedF.ISI Section Xi System Leakage ExaminationsPSEG's ISI Group conducted thirty-four (34) System Pressure Tests during aSystem Leakage or on Nuclear Class 1, 2 and 3, in accordance with ASMESection Xl.A system leakage exam was performned in accordance with ASME Section Xl on allClass 1 Systems. The system leakage test was performed with the Reactor CoolantSystem in Mode 3 (normal operating temperature and pressure) with the insulationinstalled. No pressure boundary leakage was detected.Notifications were initiated to correct minor mechanical leakage that was notcorrected during the system walkdowns, but was subsequently corrected.Class 2 and 3 System Pressure Tests were conducted on the following systems:Chemical Volume & ControlResidual Heat RemovalComponent CoolingSafety InjectionContainment SpraySamplingDemineralized WaterService WaterReactor CoolantStation AirThere were zero unacceptable indications identified.G.Augmented Volumetric Examinations of High Energy Piping Welds per RiskInformed Break Exclusion Region (RI-BER) Branch Technical Position MEB3-1PSEG Nuclear implemented Risk Informed Break Exclusion Region (RI-BER) ofNuclear Class 1 and 2 Piping Welds, formerly known as MEB-3-1 Program. Thebases of the Salem Unit 1 RI-BER Program are documented in the Salem Nuclear
Generating Station - Final Report -- Risk Informed Inservice Inspection Application(VTD-326046).There was one (1)weld examined, during this outage to comply with the RiskInformed Break Exclusion Region (IRI-BER). Sum#230600 Component LD32-MS-2121-4 DescriptionElbow to Pipe There were no unacceptable indications identified.H.Augmented System Leakage tests per NUREG 0578 "TMI Lessons Learned"PSEG's ISI Group conducted twenty-eight (28) system leakage tests in accordancewith NUREG 0578 on the following systems:Chemical Volume & ControlResidual Heat RemovalContainment SpraySafety InjectionLiquid RadwasteSamplingWaste LiquidWaste GasThere were zero unacceptable indications identified.I.Augmented Bolted Connection Exams per ISI Code Case N-533-1PSEG's ISI Group conducted sixty-1:hree (63) Class 1 bolted connection VT-2's inaccordance with the ISI Long Term Plan Program Code Case N-533-1.There were zero unacceptable indications identified.J.Preservice Examinations on Various Bolting Material ReplacementsThere was one (1) pre-service examinations of bolting performed during thisoutage. Sum# 032850Component L.D4-PS-1 131-10QB DescriptionTFlange BoltingThere were no unacceptable indications identified.
K.Pre-Service Examination Other than BoltingThere were seven (7) pre-service examinations other than bolting performed thisoutage.Component LD4-PS-I 131 -22A4-PS-1I 31 -22B4-PS-11231-22C4-PS-Il 31-22DCRD Housing Surface1-CRDUHRPV New Upper DescriptionPipe to TeeTee to PipeTee to ValveValve to FlangeCRD HousingNew RPV headNew RPV head There were zero unacceptable indications identified.L.Erosion / Corrosion UT Thickness ProgramIn response to NRC Bulletin 87-01 and PSEG Engineering Directive MEC-941071, one hundred and six (106) components were scheduled for examination.The following components were replaced in 1RI 7 due to the results of the flowaccelerated corrosion exams from the previous outage (1R16):SystemDescrilptionHeater Drain30' of 6" pipingSFAC l.D. Included inReplacementAl 2, Al 3, A79stemHeater DrainSystem105' of 6" pipingGland SealSteamA81, Al 0220' of 5" pipeB10MSR Drain40' of 4" pipeC61, C92, C-99System20' of 3n pipeC87Cold ReheatWeld Build up 62" x 54" TeeE12Cold ReheatSupplyWeld Build uip 54"x X42"ReducerE14SGF12" x 14" Expander and 3" pipeN14SGF3' of 8" pipeN46SystemsupplyAl 5, Al 6, A76, A77,
FeedwaterFeedwaterSGeF5' of 113" pipe(2) 14" elbowsN56N59, N63There were two (2) contingency planned replacements that materialized dueexamination results from 1R1 7. They were as follows:SystemHeater VentsSystemSystemSGFFeedwaterDescription20' of 3" pipingFAC l.D. Included in ReplacementH13, H15Description12" x 14" Expanderand 3" pipeFAC l.D. Included in ReplacementN27ITwenty (20) of the components examined were evaluated due to minimummeasured thickness readings below 87.5% of nominal wall. All were evaluatedas acceptable for continued operation. Also planned and executed as a result ofthe 1R1 6 exam results was an exiemal weld build-up of the 16A FeedwaterHeater Shell including D74.There were no other deficiencies identified.M.Technical Specification 4.7.9 (c) Functional Testing of Selected Hydraulic andMiechanical Snubbers.Hydraulic Snubbers (First Test Sample)One MSIV 200 Kip Paul Monroe Large Bore Hydraulic snubber was tested inaccordance with the station 10% sample plan by Wyle Laboratories AutomatedProducts Incoporated (API) in-place snubber test machine. This snubber wasreplaced due to end of seal life. The old snubber was tested and foundsatisfactory. No further sampling was required.Two Lisega small hydraulic snubbers were also tested in accordance with thestation 10% sample plan using the Wyle Laboratories Model 150 Snubber TestMachine.Tests completed were found satisfactory there was no sample expansionrequired in accordance with Technical Specifications for either test samplepopulation.
Mechanical Snubbers (First Test Sample)Mechanical snubbers were tested in accordance with Salem TechnicalSpecification (TS) 4.7.9(c), 10% sample plan on the Wyle Laboratories Model150 Snubber Test Machine as follows:1- Mechanical large (PSA-35)10- Mechanical medium (PSA-1, 3 and 10's)1- Mechanical small (PSA-I/4 and 1/2's)1- Mechanical medium (PS;A-1) non-TS.All snubbers were tested and found within acceptable standards.N.ISI Section Xi Visual Examination for Containment Integrity.There were zero IWE visual exam
PSEG Nuclear LLC P.O. Box 236, Hancocks Bridge, New Jersey 08038-0236 FEB @ 8 2006 LR-N06-0023 O PSEG NuclearLLC United States Nuclear Regulatory Commission Document Control Desk Washington, DC 20555-001 INSERVICE INSPECTION ACTIVITIES -90 DAY REPORT AND REACTOR VESSEL HEAD INSPECTION SALEM GENERATING STATION UNIT NO. I