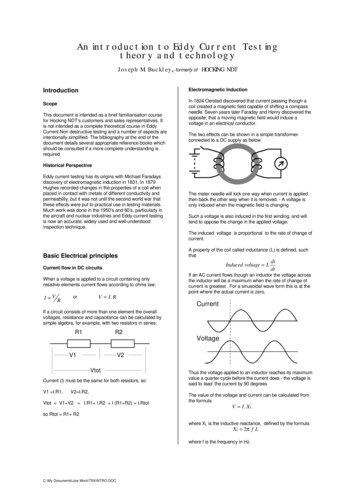
Transcription
An introduction to Eddy Current Testingtheory and technologyJoseph M. Buckley, formerly of HOCKING NDTElectromagnetic InductionIntroductionScopeThis document is intended as a brief familiarisation coursefor Hocking NDT’s customers and sales representatives. Itis not intended as a complete theoretical course in EddyCurrent Non destructive testing and a number of aspects areintentionally simplified. The bibliography at the end of thedocument details several appropriate reference books whichshould be consulted if a more complete understanding isrequiredIn 1824 Oersted discovered that current passing though acoil created a magnetic field capable of shifting a compassneedle. Seven years later Faraday and Henry discovered theopposite; that a moving magnetic field would induce avoltage in an electrical conductor.The two effects can be shown in a simple transformerconnected to a DC supply as belowHistorical PerspectiveEddy current testing has its origins with Michael Faradaysdiscovery of electromagnetic induction in 1831. In 1879Hughes recorded changes in the properties of a coil whenplaced in contact with metals of different conductivity andpermeability, but it was not until the second world war thatthese effects were put to practical use in testing materials.Much work was done in the 1950’s and 60’s, particularly inthe aircraft and nuclear industries and Eddy current testingis now an accurate, widely used and well-understoodinspection technique.The meter needle will kick one way when current is appliedthen back the other way when it is removed. - A voltage isonly induced when the magnetic field is changingSuch a voltage is also induced in the first winding, and willtend to oppose the change in the applied voltage.The induced voltage is proportional to the rate of change ofcurrent.Basic Electrical principlesA property of the coil called inductance (L) is defined, suchthatInduced voltage LCurrent flow in DC circuitsWhen a voltage is applied to a circuit containing onlyresistive elements current flows according to ohms law:I V RorV I. RdidtIf an AC current flows though an inductor the voltage acrossthe inductor will be a maximum when the rate of change ofcurrent is greatest . For a sinusoidal wave form this is at thepoint where the actual current is zero,CurrentIf a circuit consists of more than one element the overallvoltages, resistance and capacitance can be calculated bysimple algebra, for example, with two resistors in series:R1R2VoltageV1V2VtotCurrent (I) must be the same for both resistors, so:V1 I.R1,V2 I.R2,Vtot V1 V2 I.R1 !.R2 I (R1 R2) I.RtotThus the voltage applied to an inductor reaches its maximumvalue a quarter-cycle before the current does - the voltage issaid to lead the current by 90 degreesThe value of the voltage and current can be calculated fromthe formulaV I . XLso Rtot R1 R2where XL is the inductive reactance, defined by the formulaXL 2π f Lwhere f is the frequency in HzC:\My Documents\Joe Work\TEKINTRO.DOC
Current flow in AC Circuits - ImpedanceLRVRVLBasic Eddy Current TestingSimple Coil above a metal surfaceWhen an AC current flows in a coil in close proximity to aconducting surface the magnetic field of the coil will inducecirculating (eddy) currents in that surface. The magnitudeand phase of the eddy currents will affect the loading on thecoil and thus its impedance.VtotAs we saw above, for series DC circuits calculation of totalresistance is simply a matter of adding the individualresistance values.For an AC circuit things are not so simple, but the samebasic principles apply: The current though both elementsmust be the same, and at any instant the total voltage acrossthe circuit is the sum of the values across the elements,however the maximum voltage across the resistancecoincides with zero voltage across the inductor and viceversa.VLAs an example, assume that there is a deep crack in thesurface immediately underneath the coil. This will interrupt orreduce the eddy current flow, thus decreasing the loading onthe coil and increasing its effective impedance.VRV totWe can represent this graphically using a Vector DiagramThis is the basis of eddy current testing, by monitoring thevoltage across the coil in such an arrangement we candetect changes in the material of interest.The Impedance of the circuit is therefore given by theformulaZ (X2L R2)and the phase angle between voltage and current is given by( )Θ sin 1 XL ZNote that cracks must interrupt the surface eddy current flowto be detected. Cracks lying parallel to the current path willnot cause any significant interruption and may not bedetectedCrack parallel to eddycurrents - not detectedCrack interrupts eddycurrents - detectedFactors affecting eddy current responseA number of factors, apart from flaws, will affect the eddycurrent response from a probe. Successful assessment offlaws or any of these factors relies on holding the othersconstant, or somehow eliminating their effect on the results.It is this elimination of undesired response that forms thebasis of much of the technology of Eddy current inspection.The main factors are:C:\My Documents\Joe Work\TEKINTRO.DOC
Material conductivityThe conductivity of a material has a very direct effect on theeddy current flow: the greater the conductivity of a materialthe greater the flow of eddy currents on the surface.Conductivity if often measured by an eddy current technique,and inferences can then be drawn about the different factorsaffecting conductivity, such as material composition, heattreatment, work hardening etc. Decreases with an increase in frequency Decreases with an increase in conductivity Decreases with an increase in permeability - This can bevery significant - penetration into ferrous materials atpractical frequencies is very small.Depth (in)Depth (mm)PermeabilityThis may be described as the ease with which a material canbe magnetised. For non-ferrous metals such as copper,brass, aluminium etc., and for austenitic stainless steels thepermeability is the same as that of ‘free space’, i.e. therelative permeability(mr) is one. For ferrous metals howeverthe value of mr may be several hundred, and this has a verysignificant influence on the eddy current response, inaddition it is not uncommon for the permeability to varygreatly within a metal part due to localised stresses, heatingeffects requencyAs we will discuss, eddy current response is greatly affectedby the test frequency chosen, fortunately this is one propertywe can control.GeometryIn a real part, for example one which is not flat or of infinitesize, Geometrical features such as curvature, edges,grooves etc. will exist and will effect the eddy currentresponse. Test techniques must recognise this, for examplein testing an edge for cracks the probe will normally bemoved along parallel to the edge so that small changes maybe easily seen. Where the material thickness is less than theeffective depth of penetration (see below) this will also effectthe eddy current MHzFrequencyThe graph above shows the effect of frequency on standarddepth of penetration .It is also common to talk about the “effective depth ofpenetration” usually defined as three times the standarddepth, where eddy current density has fallen to around 3% ofits surface value. This is the depth at which there isconsidered to be no influence on the eddy current field.The impedance planeProximity / Lift-offThe closer a probe coil is to the surface the greater will bethe effect on that coil. This has two main effects: The “lift-off” signal as the probe is moved on and off thesurface. A reduction in sensitivity as the coil to product spacingincreases.Eddy current responses of a single coil may be convenientlydescribed by reference to the “impedance plane”. This is agraphical representation of the complex probe impedancewhere the abscissa (X value) represents the resistance andthe ordinate (Y value) represents the Inductive reactance.XLFerriteCrack in SteelDepth of PenetrationThe eddy current density, and thus the strength of theresponse from a flaw, is greatest on the surface of the metalbeing tested and declines with depth. It is mathematicallyconvenient to define the “standard depth of penetration”where the eddy current is 1/e (37%) of its surface value.Steel MAGNETICProbe inAirTitanium NON-MAGNETICCrack in AluminiumLift-OffAluminiumIncreasing conductivity of TestSampleCopperPROBE COIL IMPEDANCE - ZThe standard depth of penetration in mm is given by theformula:δ 50 ρ ( f . µ r )where r is resistivity in mW.cm and f is frequency in Hzfrom this it can be seen that depth of penetration:C:\My Documents\Joe Work\TEKINTRO.DOCRNote that, while the general form of the impedance planeremains the same, the details are unique for a particularprobe and frequency.The display of a typical CRT display eddy current instrumentrepresents a ‘window’ into the impedance plane, which canbe rotated and “zoomed” to suit the needs of the application.For example in the above impedance plane diagram a rotateddetail of the “probe on aluminium” area would appear asbelow:
“cracks”The characteristic “figure of eight” response as first oneprobe element, then the other, move over the defect. Ingeneral the closer the element spacing the wider the “loop” inthe signal.Lift-off should be cancelled out assuming that the probe isperfectly balanced, but there will still be a “wobble” responseas the probe is moved and tilted slightly.Lift-OffThis shows the display when moving over a series ofsimulated cracks of varying depths Note that, in the exampleshown both the amplitude and the phase of response fromthe different sized cracks varies.Reflection or Driver/pickup probes have a primary windingdriven from the oscillator and one or more sensor windingsconnected to the measurement circuit. Depending on theconfiguration of the sensor windings reflection probes maygive response equivalent to either an absolute or differentialprobe.Coil ConfigurationsAppropriate coil selection is the most important part ofsolving an eddy current application, no instrument canachieve much if it doesn’t get the right signals from theprobe.Coil designs can be split into three main groups:Surface probes used mostly with the probe axis normal tothe surface, in addition to the basic ‘pancake’ coil thisincludes pencil probes and special-purpose surface probessuch as those used inside a fastener hole.Encircling coils are normally used for in-line inspection ofround products, The product to be tested is inserted thougha circular coil.ID probes are normally used for in-service inspection of heatexchangers. The probe is inserted into the tube. Normally IDprobes are wound with the coil axis along the centre of thetube.These categories are not exhaustive and there are obviouslyoverlaps, for example between non-circumferential wound IDprobes and internal surface probes.To this point we have only discussed eddy current probesconsisting on a single coil, These are commonly used inmany applications and are commonly known as absoluteprobes because they give an ‘absolute’ value of the conditionat the test point.Absolute probes are very good for metal sorting anddetection of cracks in many situations, however they aresensitive also to material variations, temperature changesetc.Another commonly used probe type is the ‘differential’ probethis has two sensing elements looking at different areas ofthe material being tested. The instrument responds to thedifference between the eddy current conditions at the twopoints.Differential probes are particularly good for detection of smalldefects, and are relatively unaffected by lift-off (although thesensitivity is reduced in just the same way), temperaturechanges and (assuming the instrument circuitry operates ina “balanced” configuration) external interference.“cracks”“wobble”The diagram shows a typical response from a differentialprobe. Note:C:\My Documents\Joe Work\TEKINTRO.DOC"Absolute"reflection probe“Differential”reflection probeMain advantages of reflection probes are:Driver and pickup coils can be separately optimised for theirintended purpose.Wider frequency range than equivalent bridge connectedprobesThe larger driver coil gives a more even field, resulting inbetter penetration and lift-off characteristics.
Typical Coil Connections.BridgeDifferential AmplifierPhase Sensitive Detector &balance circuitryMain AmplifierThe two coils (Differential or Absolute plus balancing coil)form the ‘legs’ of a bridge. When the bridge is balanced themeasured voltage will be zero, Any change in the condition ofeither coil will resulted in an unbalanced bridge, the degreeof imbalance corresponds to the change in coil impedance.Driver pickup.Differential AmplifierPhase Sensitive Detector &balance circuitryMain AmplifierNormally have some means of compensating for lift-off(e.g. phase rotation and/or fine frequency adjustment) sothat only crack-like indications give a reading on themeter or bargraph. An alarm threshold is usuallyincluded.Portable impedance plane Eddy current Flaw detectorsGive a real impedance plane display on a CRT or otherelectronic display (LCD, plasma etc.) Generally havefairly extensive capabilities: Wide frequency ranges fromaround a hundred hertz to several megahertz, extensivealarm facilities, general purpose units may have ratefiltering (see below) some instruments may be capableof multifrequency operation, allowing combination ofresults at two or more test frequencies in order to reduceor eliminate specific interfering effects.“Systems” eddy current units.Intended for factory operation, often in Automatic orSemi-Automatic inspection machines. Generally similaroperation to impedance plane portables but usually haveextensive input and output facilities such as relays andphotocell inputs. May be custom built for a specificpurpose, in which case features not needed for theintended application are often omitted.Meter/CRT InstrumentsTypical examples (simplified).As can be seen the essential elements are the same for adriver/pickup configuration as for a bridge, the necessarychanges can be achieved by simple switching or probeconnection changes.Hocking NDT Locator UHPractical TestingAny practical Eddy current test will require the following: A suitable probe An instrument with the necessary capabilities. A good idea of size, location and type of the flaws it isdesired to find A suitable test standard to set up the equipment andverify correct operationTypical Application: A procedure or accept/reject criteria based on the above.Surface crack detection in aircraft parts using absoluteprobe. The necessary operator expertise to understand andinterpret the results.Typical InstrumentationThere are a number of basic groups of eddy currentinstrumentationSpecial purpose equipment:Coating thickness meters, conductivity meters (e.g.Hocking AutoSigma) Generally designed to give a digitalreadout without the operator needing to understandmuch about the internal technology, except as needed togive reliable test conditions)“Crack detectors”fairly simple equipment, generally operates at arestricted number of frequencies typically severalhundred kHz, Meter or Bar-graph display. Suitable forsurface crack detection and simple sorting applicationsonly. e.g. Hocking Locator and QuickCheckC:\My Documents\Joe Work\TEKINTRO.DOCControlsMeter display indicates ‘crack severity’ - imbalance from zeropoint.Zero - balance internal circuitryZero Offset - shift zero point, useful for sorting/materialverification applications.
Train - zero and set lift-off compensation circuitry.Frequency - choice of three operating frequencies:500kHz for Aluminium and carbon steel,2 MHz for small cracks in Al Stainless & carbon steels,6 MHz for low conductivity Alloys, Titanium etc.Metal type - optimises lift-off compensation circuitry andadjusts sensitivity to match response curves from particularmetals.Alarm Level - sets meter indication at which the alarm willlight/sound.Phasec 1.1flaw signals in the presence of other variables which mayaffect the test.ApplicationsSurface crack detection.Normally carried out with pencil probes or ‘pancake’ typeprobes on ferrous or non-ferrous metals. Frequencies from100 kHz to a few MHz are commonly used. Depending onsurface condition it is usually possible to find cracks as smallas 0.1 mm or so deep.Differential probes are sometimes used, particularly inautomated applications, care must be taken to ensure thatthe orientation of flaws is correct for detection.Non-ferrous metal sortingThis is essentially conductivity testing and for dedicatedapplications a conductivity meter may be a better choice.From the impedance plane diagram it will be seen that theindication from a conductivity change is essentially the sameas from a crack, and both meter and impedance plane typecrack detectors can be successfully used to sort similarmetals using a suitable absolute probe. It should beremembered that widely different metals may have similarconductivity and that the allowable values for similar alloysmy overlap, so conductivity measurement should only beused as an indication that a metal is of correct compositionor heat-treatment.Sub-surface crack/corrosion detection.Typical Applications:Surface crack detection, weld inspection, bolthole inspectionwith rotating probe drive, metal sorting, tube inspection etc.etc.Controls:Primarily used in Airframe inspection. By using a lowfrequency and a suitable probe eddy currents can penetratealuminium or similar structures to a depth of 10mm or so,allowing the detection of second and third layer cracking,which is invisible from the surface, or thinning of any of thedifferent layers making up the structure.Heat exchanger tube testingHeat exchangers used for petrochemical or power generationapplications may have many thousands of tubes, each up to20m long. Using a differential ID ‘bobbin’ probe these tubescan be tested at high speed (up to 1 m/s or so withcomputerized data analysis.) and by using phase analysisdefects such as pitting can be assessed to an accuracy ofabout 5% of tube wall thickness. This allows accurateestimation of the remaining life of the tube allowing operatorsto decide on appropriate action such as tube plugging, tubereplacement or replacement of the complete heat exchanger.Single buttons forZero, Screen clear, print,Menu commands forFrequency, Gain, Phase, Display storage persistence, Highand low pass filters, Preamplifier sensitivity, Spot position,Timebase, Rotating drive speed and Alarm parameters.also facilities for internal trace and parameter storage andprinting, computer interfacing etc.The operating frequency is determined by the tube materialand wall thickness, ranging from a few kHz for thick-walledcopper tube up around 600 kHz for thin-walled titanium.Tubes up to around 50mm diameter are commonly inspectedwith this technique. Inspection of ferrous or magneticstainless steel tubes is not possible using standard eddycurrent inspection equipment.Dual or multiple frequency inspections are commonly usedfor tubing inspection. In particular for suppression ofunwanted responses due to tube support plates. Bysubtracting the result of a lower frequency test (which givesa proportionately greater response from the support) a mixedsignal is produced showing little or no support plateindication, thus allowing the assessment of small defects inthis area.Operating frequencyIn-Line inspection of Steel tubingSelection of operating frequency is the primary eddy currenttest parameter under operator control. Frequency selectionaffects both the relative strength of response from differentflaws and the phase relationship, Thus selection of operatingfrequency is very important in obtaining good resolution ofAlmost all high-quality steel tubing is eddy current inspectedusing encircling coils . When the tube is made of a magneticmaterial there are two main problems:C:\My Documents\Joe Work\TEKINTRO.DOC
Because of the high permeability there is little or nopenetration of the eddy current field into the tube atpractical test frequencies. Variations in permeability (from many causes) causeeddy current responses which are orders of magnitudegreater than those from defects.These problems may be overcome by magneticallysaturating the tube using a strong DC field. This reduces theeffective permeability to a low value, allowing effectivetesting.Tubes up to around 170mm diameter are commonly testedusing magnetic saturation and encircling coils.For example, if an absolute probe with diameter 2mm movesover a narrow crack at a speed of 1 m/s the resultingindication will last for approximately 2 milliseconds. If thematerial composition or thickness is also varying graduallyover a distance of say 50 cm the indication from this willchange much more slowly. Therefore a high-pass filter set toa frequency around 100Hz or so will pass the rapidlychanging signal from the defect but not the slower indicationfrom the material changes.Unfiltered SignalWhen tubes are welded this is usually where the problemsoccur, and so welded tubes are commonly tested in-lineusing sector coils which only test the weld zone.Ferrous weld inspectionThe geometry and heat-induced material variations aroundwelds in steel would normally prevent inspection with aconventional eddy current probe, however a special purpose“WeldScan” probe has been developed which allowsinspection of welded steel structures for fatigue-inducedcracking, the technique is particularly useful as it may beused in adverse conditions, or even underwater, and willoperate through paint and other corrosion-preventioncoatings.Cracks around 1mm deep and 6mm long can be found intypical welds.Instrument set-upWhile the precise details of setting up an instrument will varydepending on the type and application the general procedureis usually the same, obviously one the application has beentried the required values for many test parameters will beknown, at least approximately,Connect up the appropriate probe and set any instrumentconfiguration parameters.(mode of operation, display typeetc.)Set the frequency as required for the test.Set gain to an intermediate value,Move the probe on/on/over the calibration test piece and setphase rotation as desired (e.g. lift-off or wobble horizontal ona CRT)Move over the defects and adjust gain (andhorizontal/vertical gain ratio if fitted) to obtain the desiredtrace size/meter indication. It may be necessary to rebalance after changing gain.Further optimise phase rotation as required.Use filters etc. to further optimise signal to noise ratio.Set alarms etc. as required.Run over the calibration test piece again and verify that allflaws are clearly detected.Perform the test, verifying correct operation at regularintervals using the calibration test piece.Rate FilteringMost eddy current tests involve movement. Therefore theindications obtained will vary with time in a way which is fairlyconsistent (assuming the movement is regular) and whichcan be interpreted in terms of the speed of probe movementover various discontinuities.C:\My Documents\Joe Work\TEKINTRO.DOCHigh-pass filtered SignalEffect of rate filtering on defect resolutionBibliographyThere are a number of excellent books available on eddycurrent testing. Many are available from ASNT or othernational institutes.The following are particularly recommended to ‘fill in’ if amore complete understanding is required.Fundamentals of eddy current Testing,Donald J. Hagemaier, ASNT, 1990ISBN 0-931403-90-1Advanced Manual For: Eddy Current Test MethodCAN/CGSB-48.14-M86,Canadian General Standards BoardNDT Handbook 2nd Edition Volume 4 b,Electromagnetic Testing,Ed. Paul McIntyre/Mike Mester, ASNT, 1986ISBN 0-931403-01-04
convenient to define the "standard depth of penetration" where the eddy current is 1/e (37%) of its surface value. The standard depth of penetration in mm is given by the formula: d r m 50 (f . r) where r is resistivity in mW.cm and f is frequency in Hz from this it can be seen that depth of penetration: Decreases with an increase in .