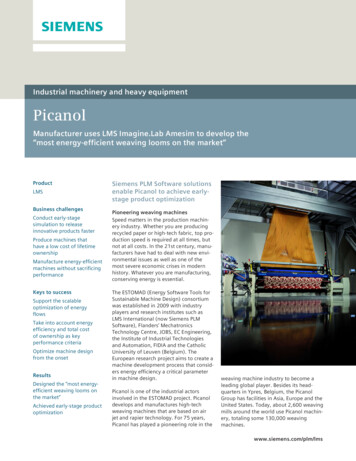
Transcription
Industrial machinery and heavy equipmentPicanolManufacturer uses LMS Imagine.Lab Amesim to develop the“most energy-efficient weaving looms on the market”ProductLMSBusiness challengesConduct early-stagesimulation to releaseinnovative products fasterProduce machines thathave a low cost of lifetimeownershipManufacture energy-efficientmachines without sacrificingperformanceKeys to successSupport the scalableoptimization of energyflowsTake into account energyefficiency and total costof ownership as keyperformance criteriaOptimize machine designfrom the onsetResultsDesigned the “most energyefficient weaving looms onthe market”Achieved early-stage productoptimizationSiemens PLM Software solutionsenable Picanol to achieve earlystage product optimizationPioneering weaving machinesSpeed matters in the production machinery industry. Whether you are producingrecycled paper or high-tech fabric, top production speed is required at all times, butnot at all costs. In the 21st century, manufacturers have had to deal with new environmental issues as well as one of themost severe economic crises in modernhistory. Whatever you are manufacturing,conserving energy is essential.The ESTOMAD (Energy Software Tools forSustainable Machine Design) consortiumwas established in 2009 with industryplayers and research institutes such asLMS International (now Siemens PLMSoftware), Flanders’ MechatronicsTechnology Centre, JOBS, EC Engineering,the Institute of Industrial Technologiesand Automation, FIDIA and the CatholicUniversity of Leuven (Belgium). TheEuropean research project aims to create amachine development process that considers energy efficiency a critical parameterin machine design.Picanol is one of the industrial actorsinvolved in the ESTOMAD project. Picanoldevelops and manufactures high-techweaving machines that are based on airjet and rapier technology. For 75 years,Picanol has played a pioneering role in theweaving machine industry to become aleading global player. Besides its headquarters in Ypres, Belgium, the PicanolGroup has facilities in Asia, Europe and theUnited States. Today, about 2,600 weavingmills around the world use Picanol machinery, totaling some 130,000 weavingmachines.www.siemens.com/plm/lms
Results (continued)Balanced performance,durability, noise and vibrationparameters while minimizingenergy consumptionImplemented advancedmodel-based systemengineering“Due to rising energy prices,low energy consumption isessential to managing operational expenses. Our products must deliver thehighest fabric quality at thelowest total cost of ownership for the weaver. Wehave focused our efforts onenergy efficiency to gain asubstantial competitiveadvantage.”Kristof RoelstraeteManagerResearch and DevelopmentPicanolGripper and follower motion.Seeking energy efficiencyStringent market regulations and a toughcompetitive environment are compellingthe production machinery industry toimprove its machine design processes.Manufacturers need to deliver top-performing machines that comply with stricthealth and safety requirements.Innovations are being introduced faster allthe time. These considerations make earlystage simulation virtually compulsory torelease innovative products faster andfaster. The industry is also experiencing arecent shift in customer expectations.“Due to rising energy prices, low energyconsumption is essential to managingoperational expenses. Our products mustdeliver the highest fabric quality at thelowest total cost of ownership for theweaver. We have focused our efforts onenergy efficiency to gain a substantialcompetitive advantage.”Supporting scalable optimizationWithin the framework of the ESTOMADproject, Picanol improves the energy efficiency of its weaving machines without“It’s not all about purchase price or performance anymore,” says Kristof Roelstraete,the research and development (R&D) manager at Picanol. “More and more customerstend to choose the machine that offers thebest deal in terms of total cost of ownership. They don’t only consider the initialinvestment price, but also maintenanceand operational costs for the completemachine lifecycle.Picanol gripper weaving machine (Optimax).
sacrificing performance. In close collaboration with the Catholic University, PicanolR&D engineers started with building themodel of the energy flows inside the maindriveline of a weaving machine. Creatingthis model is a complex task: it shouldaccurately predict all inner energy transfers as well as expose local energy leaks. Itneeds to provide a detailed representationof energy behavior for each componentwhile integrating with the globalmachine’s multiphysics environment.The ESTOMAD consortium has selectedLMS Imagine.Lab Amesim software fromSiemens PLM Software as the mechatronicsystem simulation platform to performenergy management studies on industrialmachines. LMS Amesim lets engineers consistently analyze all energy flows in thevarious subsystems of a weaving machine,from the insertion system to the motorover the gearbox and main shaft.LMS Imagine.Lab Amesim model of the weaving machine in co-simulation withLMS Virtual.Lab Motion.To support the scalable optimization ofenergy flows, the graphical user interface(GUI) of LMS Amesim and the machineryThe correlation between on-site system measurements and the LMS Imagine.LabAmesim/LMS Virtual.Lab co-simulation model at 500 RPM.“ We highly appreciate the products andsupport from Siemens PLM Software.They help us design the most energy-efficientweaving looms on the market.”Kristof RoelstraeteManagerResearch and DevelopmentPicanol
Flow chart of the instantaneous energy losses with respect to the dissipating components.components libraries have been speciallyupdated to help engineers design environmentally friendly machines. Picanol engineers optimize machine design from theearliest stage, taking energy-efficiency as acritical performance requirement.One step further in the development process, LMS Amesim is coupled with LMSVirtual.Lab software from Siemens PLMSoftware in a co-simulation arrangement.Consequently, even the complex 3D mechanisms of the weaving machine (whichrequire a detailed dynamic and kinematicmodeling) are simulated and optimized,leveraging the new functionalities of LMSAmesim to deliver a more ecologicaldesign.The LMS Amesim submodel editing tool,the platform’s customization tool, can beused to natively integrate all the requiredpower and energy variables, meaning thatspecific components can be created easilyand quickly and assessed with regard toenergy consumption objectives. In theframework of the ESTOMAD study andwith the particular involvement of theCatholic University of Leuven, Picanolengineers could seamlessly interface LMSAmesim with the MATLAB environmentto perform parameter identification. ThePicanol-ESTOMAD project reveals a precisecorrelation between LMS models andmeasurements performed on weavingmachines, a major study outcome that willhelp improve future machine developmentprocesses.Leveraging model-based systemengineeringThe extensive Siemens PLM Software portfolio supports Picanol in the early-stageoptimization of weaving machines, balancing all critical performance, durability,noise and vibration parameters whileminimizing energy consumption.“We highly appreciate the products andsupport from Siemens PLM Software,” saysRoelstraete. “They help us design the mostenergy-efficient weaving looms on themarket. A platform like LMS Amesim offersextensive libraries of components that alsoconnect to describe complete multiphysicssystems, a prerequisite for advancedmodel-based system engineering.
Solutions/ServicesLMS Imagine.Lab Amesimwww.siemens.com/plm/lms-amesimLMS eving this with scripting programssuch as MATLAB or Python is unrealistic.”More projects focused on energy savingand energy management will probably bestarted in the near future, not onlybecause of the expected profit, but also inresponse to upcoming environmental challenges. Picanol is well-positioned to takethe lead by designing the most ecologicalweaving machines on the market.Roelstraete also predicts that model-basedsystem engineering will become a standard design procedure in the productionmachinery industry in the coming years.Customer’s primary businessPicanol develops, producesand markets high-techweaving machines. Picanolweaving machines are asynthesis of technologicalknow-how and experiencebuilt up over more thanhalf a century. Today, about2,600 weaving mills aroundthe world use Picanol machinery, totaling approximately110,000 weaving machines.www.picanol.beCustomer locationYpresBelgium“ A platform like LMS Amesimoffers extensive libraries ofcomponents that also connect todescribe complete multiphysicssystems, a prerequisite foradvanced model-based systemengineering.”Kristof RoelstraeteDirectorWeaving Machine DevelopmentPicanolSiemens PLM SoftwareAmericasEuropeAsia-Pacific 1 248 952 5664 32 16 384 200 852 2230 3308www.siemens.com/plm 2014 Siemens Product Lifecycle Management Software Inc. Siemens and the Siemens logo are registered trademarks ofSiemens AG. LMS, LMS Imagine.Lab, LMS Imagine.Lab Amesim, LMS Virtual.Lab, LMS Samtech, LMS Samtech Caesam, LMSSamtech Samcef, LMS Test.Lab, LMS Soundbrush, LMS Smart and LMS SCADAS are trademarks or registered trademarks of LMSInternational N.V. or any of its affiliates. MATLAB is a trademark or registered trademark of The MathWorks, Inc. All othertrademarks, registered trademarks or service marks belong to their respective holders.35354-Z7 6/14 A
(GUI) of LMS Amesim and the machinery " We highly appreciate the products and support from Siemens PLM Software. They help us design the most energy-efficient weaving looms on the market." Kristof Roelstraete Manager Research and Development Picanol LMS Imagine.Lab Amesim model of the weaving machine in co-simulation with LMS Virtual.Lab .