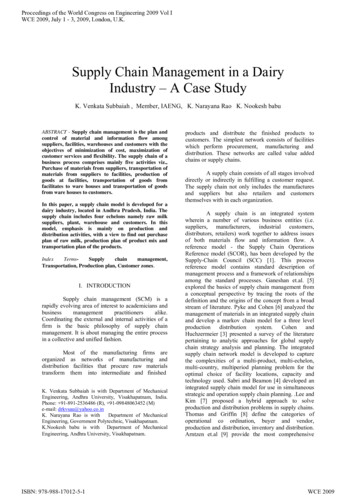
Transcription
Proceedings of the World Congress on Engineering 2009 Vol IWCE 2009, July 1 - 3, 2009, London, U.K.Supply Chain Management in a DairyIndustry – A Case StudyK. Venkata Subbaiah , Member, IAENG, K. Narayana Rao K. Nookesh babuABSTRACT - Supply chain management is the plan andcontrol of material and information flow amongsuppliers, facilities, warehouses and customers with theobjectives of minimization of cost, maximization ofcustomer services and flexibility. The supply chain of abusiness process comprises mainly five activities viz.,Purchase of materials from suppliers, transportation ofmaterials from suppliers to facilities, production ofgoods at facilities, transportation of goods fromfacilitates to ware houses and transportation of goodsfrom ware houses to customers.In this paper, a supply chain model is developed for adairy industry, located in Andhra Pradesh, India. Thesupply chain includes four echelons namely raw milksuppliers, plant, warehouse and customers. In thismodel, emphasis is mainly on production anddistribution activities, with a view to find out purchaseplan of raw milk, production plan of product mix andtransportation plan of the ation, Production plan, Customer zones.I. INTRODUCTIONSupply chain management (SCM) is arapidly evolving area of interest to academicians ng the external and internal activities of afirm is the basic philosophy of supply chainmanagement. It is about managing the entire processin a collective and unified fashion.Most of the manufacturing firms areorganized as networks of manufacturing anddistribution facilities that procure raw materialstransform them into intermediate and finishedK. Venkata Subbaiah is with Department of MechanicalEngineering, Andhra University, Visakhapatnam, India.Phone: 91-891-2536486 (R), 91-09848063452 (M)e-mail: drkvsau@yahoo.co.inDepartment of MechanicalK. Narayana Rao is withEngineering, Government Polytechnic, Visakhapatnam.K.Nookesh babu is with Department of MechanicalEngineering, Andhra University, Visakhapatnam.ISBN: 978-988-17012-5-1products and distribute the finished products tocustomers. The simplest network consists of facilitieswhich perform procurement, manufacturing anddistribution. These networks are called value addedchains or supply chains.A supply chain consists of all stages involveddirectly or indirectly in fulfilling a customer request.The supply chain not only includes the manufacturesand suppliers but also retailers and customersthemselves with in each organization.A supply chain is an integrated systemwherein a number of various business entities (i.e.suppliers, manufacturers, industrial customers,distributors, retailers) work together to address issuesof both materials flow and information flow. Areference model - the Supply Chain OperationsReference model (SCOR), has been developed by theSupply-Chain Council (SCC) [1]. This processreference model contains standard description ofmanagement process and a framework of relationshipsamong the standard processes. Ganeshan et.al. [5]explored the basics of supply chain management froma conceptual perspective by tracing the roots of thedefinition and the origins of the concept from a broadstream of literature. Pyke and Cohen [6] analyzed themanagement of materials in an integrated supply chainand develop a markov chain model for a three eier [3] presented a survey of the literaturepertaining to analytic approaches for global supplychain strategy analysis and planning. The integratedsupply chain network model is developed to capturethe complexities of a multi-product, multi-echelon,multi-country, multiperiod planning problem for theoptimal choice of facility locations, capacity andtechnology used. Sabri and Beamon [4] developed anintegrated supply chain model for use in simultaneousstrategic and operation supply chain planning. .Lee andKim [7] proposed a hybrid approach to solveproduction and distribution problems in supply chains.Thomas and Griffin [8] define the categories ofoperational co ordination, buyer and vendor,production and distribution, inventory and distribution.Arntzen et.al [9] provide the most comprehensiveWCE 2009
Proceedings of the World Congress on Engineering 2009 Vol IWCE 2009, July 1 - 3, 2009, London, U.K.deterministic model for supply chain managementwith an objective function containing the cost andtime elements. Even though supply chainmanagement is relatively new, the idea of co-ordinateplanning is not new. The study of multi-echeloninventory/distribution systems began as early as 1960by Clark and Scarf [2]. Since then many researchershave investigated multi echelon inventory anddistribution systems. Less research has been aimed atco-ordination of procurements, production anddistribution systems. In this paper an attempt hasbeen made to develop a coordinated supply chainplanning model with procurement, production anddistribution systems.AWtwgThe inventory of good g in theware house w at time t.The amount of good g which warehouse w transported tocustomer c at time t.The demand of goods g bycustomer c at time t.RtwcgACtcgAssumptions1.2.3.Capacities of vendors are fixed.Demand is deterministic.Variable cost per unit production is constantMathematical modelII. MODEL FORMULATIONThe proposal of the model is to find an optimalstrategic plan for an integrated supply chain wgCost of material p purchased byvendor v at time tProduction cost of goods g producedby facility f at time tTransportation cost of material pTransported from vendor v tofacility f at time tTransportation cost of goods gtransported from facility f to warehouse w at time tTransportation cost of goods gtransported from ware house w tocustomer location c at time tInventory cost of mterial pof facility f at time tInventory cost of goods gof facility f at time tInventory cost of goods g ofwarehouse w at time tAmount of material p needed forproducing goods gThe amount of material ppurchased by vendor v at time tThe amount of material p whichvendor v Transported of facility f attime t.The inventory of material p in thefacility f at time tAmount of good g which facility fproduced at time tThe inventory of goods g at facilityf at time t.The amount of goods g whichfacility f transported to ware housew at time t.ISBN: 978-988-17012-5-1This model consists of four echelons namelySuppliers, Plants, Distribution Centers (DCs), andCustomer zones (CZs).A multi-objective function is formulated tominimize cost subject to supplies, plant anddistribution capacities, production and distributionthrough put limits and customs demand requirements.Total cost includes fixed costs of production anddistribution, variable costs of production, distributionand transportation.Various costs involved in the supply chain are1.Material Cost 2.Production cost 3.Transportation cost MC tvp * AVtvpvp PC tfg *Rtfgfg VFTC tvfp * Rtvfp FWTC tfwg * Rtfwg WCTC twcg * Rtwcgvfpfwgwcg4.Inventorycost FMIC tfp * AFtfp FGIC tfg * AFtfg WIC twg * AWtwgftfgwgThe objective function of the model is to minimize thetotal cost associated with the supply chain whichincludes material, production, transportation andinventory costs.Minimize Z MC tvp * AVtvp PC tfg * Rtfg VFTC tvfp * Rtvfpvspfgvfp FWTC tfwg * Rtfwg WCTC twcg * Rtwcg FMIC tfp * AFtfpfwgwcgft FGIC tfg * AFtfg WIC twg * AWtwgfgwgWCE 2009
Proceedings of the World Congress on Engineering 2009 Vol IWCE 2009, July 1 - 3, 2009, London, U.K.The above stated problem is solved subjected to thefollowing constraint set.vf121. Upper – Lower bound restrictions0 Rtvfp Rtvfp UPbound0 Rtfwg Rtfwg UPbound0 Rtwcg Rtwcg UPboundRtfg LPbound Rtfg Rtfg UPboundetvf 1; ettw 1; etvc 1;tAF tfp R( t etvf ) vfp BOM gp * Rtfgg AF(t 1) fp t , f , pAW twg R(t et fw ) fwg Rf AW ( t 1) wgtwcgc t , w, g R( t etwc ) 103.833.353.26For facility1g1w13.26211.9313.648.957.56tvfp LVtvp t , v, pv1Facility to ware house transportation cost2. Flow Conservative restrictions RVendor to facility transportation cost ACtcg t , c, gwFor facility 523.2619.818.410.94.523.2619.818.4Ware House to customer transportation costIII. CASE STUDYThe above developed model is applied to VisakhaDairy situated in Andhra Pradesh, India. The abovedairy has six vendors located at Vsiahapatnam,Vizianagaram, Tuni, Ramabadrapuram, Narsipatnamand Srikakulam. It has two facilities located atVisakhapatnam and kakinada to meet the customerdemands. Five warehouses are situated atVisakapatnam, Vizianagaram, Srikakulam Kakinadaand Rajahmundry. Its customer locations are situatedat Visakhapatnam, Vizianagaram, Srikakulam,Kakinada and Rajamundry.The input data required for the design of supply chainfor the above stated industry is given below.Input DataMaterial Costvp11234561140116099111358721056ISBN: 61.240In the above table the transportation cost for good 1 isshown and the same table repeats for the remaininggoods.Inventory carrying cost at the facility for the rawmaterial and goods are considered as Zeros.Inventory const at 050.070.070.070.070.070.050.050.050.050.05WCE 2009
Proceedings of the World Congress on Engineering 2009 Vol IWCE 2009, July 1 - 3, 2009, London, U.K.Table II: Quantities of goods transported from vendorsto facilitiesCapacities of Vendors (in thousands)v123456p117843325452220Capacities of facilities for producing different 40003200030000Capacities of ware house to hold different 02500020000800060005000Demands for different goods at different 61932372616684735262104659The Problem is solved using LINGO student versionpackage.The optimal solution for the model isTable I: Quantities of material to be procured versiondifferent vendors.123456106565430003250002200029000ISBN: 000029000Table III: Amounts of goods produced at both 315020034000286313000Table IV: Amounts of goods transported from facilitiesto warehouseFrom Facility F1g12w1 23048 105920200300400500From Facility 4972882000166841331600Table V: Amounts of goods to be transported fromware houses to customer Zones.IV. RESULTS AND DISCUSSIONSvp1vf12From ware house 1g12c1 23760 60000WCE 2009
Proceedings of the World Congress on Engineering 2009 Vol IWCE 2009, July 1 - 3, 2009, London, U.K.From Ware House 2g12c10021072462430040050195From ware house 3g12c10020031254356449623234500From ware house 5g12c1002003004005003456V. CONCLUSIONS000000000440304001930166840003456In this paper supply chain network isdesigned for a dairy industry. This network includesmaterial purchase plan, production plan, inventoryplan and transportation plan. From the results it isobserved that the total cost of the supply chain is 9.8percent lesser than the existing cost. This model can beextended to varying demand and costs. This can alsobe applied to fast moving consumer 00114000000002464659Table I represents the procurement plan whichindicates quantities of raw materials to be procuredfrom different vendors. As both the material cost andtransportation costs to both the facilities is high fromvendor 4 (i.e., Ramabadrapuram) and the demand forthe raw material can be fulfilled by the remainingvendors, raw material should not be procured fromthe vendor 4. Table III represents the production planfor the optimal product mix. It gives us the quantitiesof material to be produced by both the facilitiesconsidering the demands of the customers and theirtransportation cost.Table II, IV and V represent the transportation plansfor the plant. Table II shows the quantities of materialto be transported from different vendors to both thefacilities. Table IV shows the quantities of differentgoods to the shipped to the warehouses from both thefacilities. Table V shows the quantities of differentgoods to be transported from different warehouse toall the customer locations. The Transportation cost toware house 4 is very high from both the facilities andit is also very far away from all the customer zones,so the warehouse 4 is discarded from the plan. Fromthe above obtained plans the total cost of the supplychain is calculated as Rs.27, 41,039/- per one timeperiod (i.e.12 hours). The obtained value isRs.2,02,539/- less than the existing cost.ISBN: 978-988-17012-5-1REFERENCES[1.] Supply-Chain Council, Inc., 1998, Overviewof the SCOR Model V2.0, www.supplychain.org.[2.] Clark, A. J., and Scarf, H., 1960, OptimalPolicies for a MultiiEchelon InventoryProblem, Management Science, Vol. 6,475490.[3.] Cohen, M. A., and Huchzermeier, A., 1998,Global Supply Chain Management: A surveyof Research and Applications, QuantitativeModels for Supply Chain Management,Kulwer academic publishers .[4.] Ehap H. Sabri and Benita M. Beamon 2000,A Multi-Objective Approach to SimultaneousStrategic and Operational Planning in SupplyChain Design, Omega Vol. 28, NO.5, 581598.[5.] Ganeshan, R , Stephens, P., Jack, E . , andMagazine, M., 1999, A taxonomic review ofsupplychainmanagementresearch,Quantitative models for supply chainmanagement. The Netherlands: Kluweracademic publishers, 839 - 879.[6.] Pyke , D.F . , and Cohen, M . A . , 1994,Multiproductintegratedproductiondistribution system , European journal ofoperations research. Vol 74 , No I , 18 - 49.[7.] T. H. Lee and S.H . Kim. , 2000,optimalproduction distribution planning in supplychain management using a hybrid simulationAnalytic approach.[8.] Thomas D. 1. and P. M. Griffin. , 1996, Cocoordinated supply chain management.European journal of operation research, 94: 115.[9.] Arntzen, B. C., G. C. Brown, T. P. Harrisonand L. Troflan, 1995, Global supply chainmanagement at digital equipment corporation.Interfaces: 25, 69-93.WCE 2009
reference model - the Supply Chain Operations Supply-Chain Council (SCC) [1]. This process reference model contains standard description of management process and a framework of relationships among the standard processes. Ganeshan et.al. [5] explored the basics of supply chain management from a conceptual perspective by tracing the roots of the