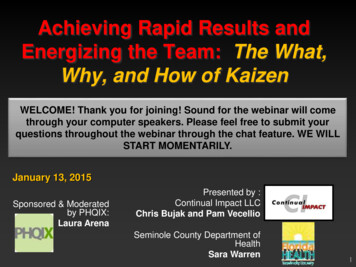
Transcription
Achieving Rapid Results andEnergizing the Team: The What,Why, and How of KaizenWELCOME! Thank you for joining! Sound for the webinar will comethrough your computer speakers. Please feel free to submit yourquestions throughout the webinar through the chat feature. WE WILLSTART MOMENTARILY.January 13, 2015Sponsored & Moderatedby PHQIX:Laura ArenaPresented by :Continual Impact LLCChris Bujak and Pam VecellioSeminole County Department ofHealthSara Warren1
TO:Share information on the Kaizen process and the results itcan produceFOR:Quality Improvement practitioners who are a) new to Kaizenand what to try it and b) have tried Kaizen and want tips forimproving their resultsWhat is the goal,purpose or outcomedesired?Who benefits from theresults? What is thescope?SO THAT:What are the benefitsfrom achieving thegoal? STANDARDS:How will you measuresuccess; Measure andTargetYou increase their knowledge of Kaizen and its processYou know how Kaizen fits in Quality ImprovementYou are able to describe Kaizen to othersYou are energized to learn more about its potentialWhatHow MeasuredTargetAttendance# of attendees 100Participation# of questions asked by attendees 10Value# attendees expressing positivefeedback – post survey 2014 Continual Impact LLC 90%2
CONDITIONS:What requirements orlimitations exist? Session is conducted in 1 ½ hours You understand the webinar does not able you to conduct anevent without additional trainingBY:How will youachieve the result?Basic approach?WhatWhoTimePreliminaries; Session goal; Learning Laura Arena &objectivesChris Bujak10 min.Definition of Kaizen10 min.Chris BujakOverview of Kaizen ProcessPam Vecellio(relationship to the improvement cycle,day by day activities, techniques usedduring the process)20 min.Benefits of KaizenChris Bujak,Pam Vecellio15 min.Share lessons learned and casehistoriesChris Bujak,Sara Warren20 min.Summary take aways; Questions &AnswersAll 2014 Continual Impact LLC15 min.3
2014 Continual Impact LLC4
2014 Continual Impact LLC5
Principle of Conduct: Striving forPerfectionThe pursuit ofperfection in all one Management Principle: Creates does. In this use, theBusiness Successterm is applicableacross the areas of Method: Work Processone’s life andImprovementrepresents a guidingethic for conducting– Individual Work Processa life.Improvement– Day to Day Team Work Process Improvement– Special Event Work Process Improvement 2014 Continual Impact LLC6
The pursuit of perfection in all one does. In thisuse, the term is applicable across the areas ofone’s life and represents a guiding ethic forconducting a life. 2014 Continual Impact LLC7
It is expressed in all activities, personal and teamed, thatdevelop and use learning to make processes better atsatisfying customer requirementsIts origins are in the fifth of W. Edwards Deming’s 14management points: “Improve constantly and forever thesystem of production and service” (Deming, 1982, p. 49)Outside the United States, the term kaizen, on its own,more frequently refers to a comprehensive companywidemanagement program best represented by the work ofMasaaki Imai (1986). 2014 Continual Impact LLC8
A group of methods for making work process improvements. Themethods that have been placed under the label Kaizen arevaried and range from use by the individual (Teian Kaizen) toplanned teamed events conducted in the workplace thatsystematically uncover waste in a work process and eliminateit (Gemba Kaizen).In this definition the Kaizen methods are organized in to 3categories: Individual Day-to-day Special event 2014 Continual Impact LLC9
Also known as Kaizen Blitz or Kaizen Event Most common Kaizen method. Prior planning followed by fully executing the processimprovement cycle over a period of days. Performed at the sub process level or where the work isdone (“Gemba”). Focus on making improvements by detecting andeliminating waste. 2014 Continual Impact LLC12
Kaizen event A team-based approach to problem solving that flows through allphases of the improvement cycle effectively and rapidly. Before the event, a kaizen-appropriate problem is identified alongwith goals in areas such as customer satisfaction, cycle time andlabor reduction, and error elimination. A typical event uses a systematic process to identify waste in thetargeted work process, enable the team to understand and analyzethe root causes, identify and test solutions, learn, installimprovements, and create a system for ongoing improvement. Asthe event progresses, numerous QI and change managementmethods and techniques are applied. All of this work is accomplished in a brief period of time, typically 5days, with full benefits achieved within 1-3 months! 2014 Continual Impact LLC11
Kaizeneventsengage staff& achieveearlysuccesses,benefits Powered by People Special type of Leadership Superbly Focused on their purpose Use Learning to create results Implement well, installing the new way andcontinually improving Improvement Methods used to empower theindividual and effectively solve problems 2014 Continual Impact LLC12
Confirm 2014 Continual Impact LLCPreparePerformInstitutionalize13
Improvement Cycle: (6-8 months)Do /TryPlan/SolveCheck /LearnAct/InstallKaizen Event Steps: (6 weeks)ConfirmPreparePre-EventWork Time:30 minElapsed Time:1 dayWork Time:12 hrsElapsed Time:3 wks 2014 Continual Impact LLCPerformInstitutionalizeEventPost-EventWork Time: 40 hoursElapsed Time: 5 daysWork Time:20 hrsElapsed time:2 wks14
The Improvement Cycle &A Kaizen EventSimilaritiesCompleting all the improvement cycle stepsTeam members are criticalInformation & data based problem solvingDifferences for a Kaizen EventShorter cycle time to achieve resultsLess work content time for projectTarget running the new process the day after the eventMore critical: Preparation work Speed of Observing/Evaluating Data, Testing, Making Decisions, &Implementing ActionsEvent leader’s competency in multiple improvement methods 2014 Continual Impact LLC15
What Draft the project gap (starting point & vision) Draft the project goal statement Confirm kaizen as the best improvement method Obtain leadership supportWhy Ensure the best improvement method to addressthe gap The improvement project is off to a successfulstart 2014 Continual Impact LLC16
Kaizen Event Selection Criteria The problem is definable The problem is measureable (currently or can be defined in the event) The leadership team is committed to provide event resources, logistics The team has the authority, knowledge, and skills to make theneeded decisions The benefits case is clear The process can be observed within the event timeframe The resources can commit to 5 consecutive days or 40 hourswithin 3 weeks (this is less ideal) It is feasible to test and install solutions within the week Solving this problem supports our strategic plans & our annualimprovement plans No significant change management issues 2014 Continual Impact LLC17
What Finalize event goal Confirm team members & subject matter experts Confirm improvement owner Gather & review relevant work process data, documents,issues Prepare & share event communications Coordinate event logistics & room set upWhy Confirm that team members, leaders, and QI Leader areprepared to fully participate 2014 Continual Impact LLC18
Day 1: Focus the team; Gather process data &information; Understand the current stateDay 2: Prioritize issues; Evaluate/Root cause the wastesand Solve the ProblemDay 3: Develop future state process & solutions (job aids);Start to Test & LearnDay 4: Test & Learn; Continue to develop solutions;Develop training material; Prepare process ownerDay 5: Pilot the new process & Learn; Measure results;Communicate results; Hand off to Process Owner & team 2014 Continual Impact LLC19
What: Post the Event Complete Follow-up action items(communications, training, go-live) Transition responsibilities from project team toprocess owner and process team members Share success; Replicate improvements at othersites, locationsWhy: Ensure Work process improvements are fullyinstitutionalized 2014 Continual Impact LLC20
1. Create a process that is reliable,Part ofstandardized and with clearperformingaccountabilitiesthe kaizenevent2. Teach the new process effectively(Tell,Show, Do, Recycle)3. Define and operationalize measures and targets; trackperformance4. Create a feedback mechanism for questions and ideas;resolve problems and incrementally improve5. Coach Performance; feedback and consequences 2014 Continual Impact LLCSee NACCHO Self Assessment Tool; Sub Element 6.7,Process Management, Results and Continual Improvement21
Create a feedback mechanism for questions and ideas;resolve problems and incrementally improveProcess Owner holds a CISmeeting to find out howimplementation has gone thus far.She later states, “I couldn’t havedone standardization of thisprocess without kaizen.”2 weeks following processimplementation Identify issues and ideas on an ongoing basis Create a local problem solving system including escalation if necessary Routinely review process performance 2014 Continual Impact LLC22
40 Techniques to HelpUnderstand & Make theChangeIn a Kaizen Event 2014 Continual Impact LLC23
TECHNIQUEStarting Point and GapPURPOSEFocus the IssueGoal Statement including measures of success Focus the IssueMeasure Definition SheetFocus the IssueProject PrISM (project summary, storyboard)Focus the IssueStakeholder AnalysisAlign stakeholdersCommunications StrategyMotivate Interest,Align stakeholdersSingle Communication ROAMMMMotivate Interest,Align stakeholdersGathering Practical KnowledgeFocus the issue 2014 Continual Impact LLC24
TECHNIQUETECHNIQUEStarting Point and GapSub process mappingGoal StatementWaste / Value AnalysisWorking with OthersInformation Based Problem Solving;Cause and EffectDaily NewspapersDaily Leadership report outs2 X 2 Prioritization MatrixPerforming tests with stakeholdersTest Lessons Learned (SRLD)Daily StakeholdercommunicationsEvent report out5S, Mistake Proofing,Kanban, Flow, QuickChange 2014 Continual Impact LLCStandardized Work Templates(Single Topic Guideline, GatheringPractical Knowledge)5 Step Install Process ( Training)25
TECHNIQUEPURPOSEProject PrISM (project summary,storyboard)Align stakeholdersSingle Communication ROAMMMAlign stakeholders5 Step Install Process (incl Training)Create support, Implement,Monitor and LearnProcess OwnerCreate support, Implement,Monitor and LearnContinual Improvement System (ongoing measurement, teaminvolvement, and improvement)Create support, Monitorand LearnEvent Lessons Learned (SRLD)Monitor and Learn 2014 Continual Impact LLC26
Why Kaizen?Who Benefits?The QI LeaderThe kaizen teamThe organizationThe impacted stakeholders 2014 Continual Impact LLC27
“People are the heart, head and muscle of the highperforming organization—who they are determineswhether it exists or fails to exist”Vital Enterprises, The High Performing LearningOrganization, Aug 1997Giving them the opportunity,setting, process and skills arefoundations to success 2014 Continual Impact LLC32
The types of activities which peopleconsistently report mostrewarding—involve a clearobjective, a need forconcentration so intense that no Survival Belonging Powerattention is left over, lack ofinterruptions and distractions,FreedomFunclear and immediate feedback on(Creativity)progress toward the objective,and a sense of challengePowers and GlasserPsychologist Mihaly Csikszentmihalyi,Univ of Chicago 2014 Continual Impact LLC33
SPEED to Benefit realizationIncreases capacity to conduct additionalimprovement projects Measurement installation and performance tracking Demonstrate a CAN-DO change culture Show the organization that you can make change ina short period of time Timely decision making Team member involvement & excitement for additionalimprovement 2014 Continual Impact LLC30
Food inspection process: Decreased inspection admin.time from 7 hour to 30 minutes per inspection ROI: 1 Year return on every dollar spent 8 Issuing death certificates: Decreased labor time from 22to 9 minutes per certificate # of Citizens and Funerals seeking and providinginformation: 6,500 / year Supply ordering process: Decreased labor time from 93 to16.5 minutes per order ROI: 1 Year return on every dollar spent 3With 1 day - 1 month following the Kaizen event 2014 Continual Impact LLC31
Share drive usage: Decreased search time, e.g. keydocument, from 20 to 7 seconds Request for assistance (Phone Mgmt.): Increased callscompleted within one transfer from 11% to 80% # Citizens seeking information to make informeddecisions: 26,000 / yearWith 1 day - 1 month following the Kaizen event 2014 Continual Impact LLC32
“Kaizen shocked us, we thought that we were going to spend a week toremove 10 minutes instead we identified how to remove 190 minutes.” “Nothing has ever happened this quickly in the department before. Wesolved a 16 year old problem in 5 days.” “We’ve never been asked our opinion before, we’re just told what to do. Ihave much more capability than people realize but feel looked down onbecause I’m just an operator. Kaizen changed that!” “It is nice to see how proud people are and how they own theseimprovements and the new process.” “This kaizen event was a roller coaster, after I got off I’m ready to do itagain!” “ the change that we are making to our organization to empower people,get them more involved in the day-to-day decision making, is going to get usbetter results” 2014 Continual Impact LLC33
Lessons LearnedAnd a Success Story 2014 Continual Impact LLC34
Our Team2013-2014 Strategic Plan Streamline 2014 Continual Impact LLC35
2014 Continual Impact LLC36
Purchasing Process Post-Kaizen 2014 Continual Impact LLC37
PLANData, Stakeholders, EnvironmentPERFORMPhysically, Mentally
Why, and How of Kaizen January 13, 2015 1 Sponsored & Moderated by PHQIX: Laura Arena WELCOME! Thank you for joining! Sound for the webinar will come through your computer speakers. Please feel free to submit your questions throughout the webinar through the chat feature. WE WILL START MOMENTARILY. Presented by : Continual Impact LLC Chris Bujak and Pam Vecellio