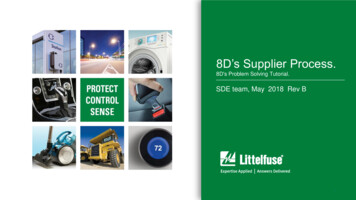
Transcription
8D’s Supplier Process.8D's Problem Solving Tutorial.SDE team, May 2018 Rev B1
Purpose of 8D’s tutorial. To have a standard and objective 8D’s tutorial for suppliers. SQE & SDE can share and use this file when training asupplier. To improve the quality of supplier’s 8D report. The supplier canunderstand clearly how to submit an 8D report. To help the supplier find out the systemic root cause(Management Root Cause) and implement the correctiveaction. Not only focus on shallow cause.Confidential and Proprietary Littelfuse, Inc. 20182
What is an 8D’s report?. The eight disciplines (8D) model is a quality problem solvingtool. Its purpose is to identify, correct, and eliminate recurringproblems, and it is useful in product and process improvement. The approach establishes a permanent corrective actionbased on statistical analysis of the problem and focuses on theorigin of the problem by determining its root causes.Confidential and Proprietary Littelfuse, Inc. 20183
Phases of 8D’s process.D8 .PreventiveactionsDefine teammembersDefineproblemdescriptionRoot essonsLearnInterim containments actionsConfidential and Proprietary Littelfuse, Inc. 20184
D1.- Define team members.The approach is based on a cross-functional team working together to solve a problem. Teamwork must be coordinated and guided. The teamshould include only competent persons actively involved in the process and who have been assigned a task or responsibility in subsequent steps.Efficient teams are usually not big.Task Select team membersAction Select members withappropriate skills based on theproblem description. Appointed team leader, asponsor. Are all team membersreasonability's clear?Output Establish a team & defineresponsibilities among the teammembers.Confidential and Proprietary Littelfuse, Inc. 20185
D1.- Define team members. The Champion of the team has been identified? The people affected by the problem are represented on the team? Does the team have the right people (technical and specialist skills)? The team's goals and membership roles have been clarified? Should customer / suppliers be involved in 8D’s meetings?Confidential and Proprietary Littelfuse, Inc. 20186
D1.- Good / Not Good Sample.Good Sample1. Multidisciplinary team.2. Department , name and title are clear.3. Champion is identified.Not Good Sample1.2.3.Team members were not identified.Roles are not clear.Champion is unknown.Confidential and Proprietary Littelfuse, Inc. 20187
D2.- Problem Description.Problem solving must be based on facts, not opinions. It is important to clarify the issue type, what is wrong, when did it happen, how big thefailure extent is and how many times it has happened. The description must be specific and easy to understand.TaskAction Describe the internal/externalcustomer problem by identifying"what is wrong with what" anddetail the problem inquantifiable terms. Gather and evaluate objectivedata. Answer the questions 5 Why’sand 2H’s. (Who / What / Why /Where / When / How / HowoftenOutput Description of thefundamental problem based onfacts only.Confidential and Proprietary Littelfuse, Inc. 20188
D2.- Problem Description. Has the problem been sufficiently defined? Analysis has been performed (who, what, where, when, why, how, and how often)? All required data has been collected and analyzed? The problem description has been confirmed as to what the customer(s) and/or affectedparty(s) are experiencing?Confidential and Proprietary Littelfuse, Inc. 20189
D2.- Good / Not Good Sample.Good SampleProvided information includes:1.Problem description reported by Littelfuse andproblem description reported by Supplier.2. Failure Rate.3. Sketch of the problem4. Quality data for affected lot or date codeNot Good Sample1. Copy only what Littelfuse team states.2. Neither Lot# nor failure rate information available.3. No information of affected parts numbers.Confidential and Proprietary Littelfuse, Inc. 201810
D3.- Develop Interim Containment Actions.The primary purpose of this discipline is to isolate the issue and protect the customer from receiving more parts with same quality defect.TaskActionOutput Determine the most suitablecontainment actions. Containment Actions start inthe D2(Define problemdescription) until D6(validatepermanent corrective actions) Define, verify, and implementthe Interim Containment Action(ICA) to isolate effects of theproblem from anyinternal/external customer untilPermanent Corrective Actions(PCAs) are implemented. Safeguard the situation bycontainments actions, toprevent a reoccurrence of theproblem at the customer Containment actions thereforeserve only as a safeguard andoften bear no relation to thecause of the problem. Cost considerations shouldplay little or no part in the initialresponse Develop a schedule forimplementing the containmentsactions Blocking of all parts, stock (inhouse, transit, customer) Sorting of parts. Identify thegood ones from the bad ones. Customer receives onlycertified material (While theinvestigation and resolution ofthe problem continues). There is a clear breakpointwith identified good material All suspect inventory, at alllocations, is properlyquarantined Instant information andsupport to the customer as wellas implementation ofcontainment actions is done asquickly as possible.Confidential and Proprietary Littelfuse, Inc. 201811
D3.- Develop Interim Containment Actions.Containing the problem and protecting the customer must occur immediately, 24 hrs is theLittelfuse norm for containment actions to take place. Have effective containment actions been implemented? How was the effectiveness of these actions verified? Is the work force responsible for executing the containment actions sufficientlyinstructed? Do the containment actions give the customer adequate protection against furtherdefects? Are defective products being identified and rejected as early as possible in currentprocess sequence?Confidential and Proprietary Littelfuse, Inc. 201812
D3.- Good / Not Good Sample.Good Sample1. Effective containment actions including productionand inventory in pipe line.2. Littelfuse is notified of affected material that may beintheir pipeline.3. Clean point is clearly identified and marking method.4. Quality Alert in place.Not Good Sample1. No information of material in pipeline.2. No clean point identified.3. No marking method for parts inspected until rootcauses and corrective actions are in place.Confidential and Proprietary Littelfuse, Inc. 201813
D4.- Define and Verify Root Cause and Escape Point.To effectively prevent a problem from occurring again, the root cause must be indentified and removed. In rare situations there could be more thanone root cause.TaskActionOutput Determine technical andsystemic root cause using, butnot limited to, the followingquality tools:- 5Whys- Fishbone- Brainstorming Description of the rootcauses (TRC and SRC)documented with evidence Isolate and verify the rootcausebytestingeachpossible cause against theproblem description and testdata. Isolate and verify the placein the process where theeffect of the root cause shouldhave been detected andcontained (Escape Point). The Acid Test: How do youknowwhenyouhaveidentified the actual rootcause? The Failure Modecan be turned on and off . The technical and systemicroot causes and escape pointare confirmed. Send 4D’s report to Littelfuserepresentative within 4 businessdays since claim was reported.TRC Technical Root CauseSRC Systemic Root CauseNOTE: If the root cause of aproblem is “ operator error”that’s not the real root cause.The root cause is more likelythat the process is not “errorproofed”Confidential and Proprietary Littelfuse, Inc. 201814
D4.- Root Cause Analysis.When identifying root cause the team should focus on why the issue occurredfirst, then how the defect was missed and finally what failed on the quality system.1) Technical root cause Root cause onoperative/technical level thatresults from description of logicaland functional relationships (cause effect relationship)Examples: Physical / Chemical functionproperties of materials. ( e.g.Colour , strength , strain) In technical process. Tooling worn.2) Escape point The escape point is the place inthe process where the root causecould have been detected andcontained , but was allowed topass. This root cause refers todetection system.Examples: Dimension not included onSPC chart. Tester not capable to detectthe issue. Characteristic is not part ofthe inspection plan.3) Systemic root cause This root cause refers to theQuality and ManufacturingSystems that surround theproduct and process (Refer toPFMEA for Product and Processcontrols).Examples: Instructions for the process /product not created, incomplete,unclear or faulty description. Core tools with faultyimplementation, faultyapplication or unclear.Confidential and Proprietary Littelfuse, Inc. 201815
D4.- Root Cause Analysis ( Example).Problem Description: Customer reported the cover HNXE13 was loose in several sensors, andsticking to the grip in others.Real Root Cause.1) Technical root cause2) EscapeCoverpointsnap fit leg getsOne side of cover isloose in the sensor.The tip end of one ofthe snap fit legs issheared off.High interference oncover leg at rotor flatsurface before leadingangle begins.The snap feature designon rotor (leading angleand cavity opening) notoptimized for insertion.Process instructionscalled for presenceonly but retentionforce was notmonitored.Product print calledonly for cover to belocked and present onsensor.The retention force specwas not documentedinto any customer officialdocument.Efforts were focusedon the covermodifications toaccommodatefunction addedCustomer made a lateengineering change inthe cover design toaid the assembly ofthe grip into thesensor (Close toSOP)Assembly requirementsfor the sensor in thevehicle application werenot fully developed bycustomer prior to SOP.damaged duringassembly into rotorsnap feature.2) Escape PointThe qualityacceptance criteriadid not detect coversthat were loose.After cover assembly ,there was noevidence of loosecovers.3)Systemic root causeThe snap feature onthe sensor failed dueto the design allowingfor interference andinsufficient lead in forcover legs to engageinto the rotor snap fitopening.Snap fit feature inrotor design was notthoroughly analyzed /optimized.Confidential and Proprietary Littelfuse, Inc. 201816
D4.- Root Cause Analysis. Less Structured Approaches:- Intuition, networking, and experience. Structured Approaches:- 5 Whys.- Cause and effect diagram.- Trend analysis.- Pareto Diagrams.- Brainstorming.- Flow and Process chart.- other techniques : DOE ( design of experiments) , ANOVA ( analysis of variance)NOTE 1: These structured approaches can be used to find out the root cause for occurrence(technical), systemic and escape point.NOTE 2 : When identifying root cause, the team should focus on why the issue occurred first, thenhow the defect was missed and finally what failed on the quality/manufacturing system.Confidential and Proprietary Littelfuse, Inc. 201817
D4.- Root Cause Analysis. Operator not trained.Failure to follow procedures / Work instructionsOperator errorInspection not recorded by the operatorThese are not root causes, they are just symptoms of the true rootcause.Confidential and Proprietary Littelfuse, Inc. 201818
D4.- Root Cause Analysis. Problem description was not well defined. Possibly some of the “facts” are not true. Incorrect data. The right people was not included to fully understand the problem. The team is working on symptoms instead of the real problem.Confidential and Proprietary Littelfuse, Inc. 201819
D4.- Define and Verify Root Cause and Escape Point. Have all sources of information been considered in determining the root causes? Why has the problem not occurred before? Is there a provable connection between the problem and particular processes? The causes were reviewed to determine if, collectively, they account for all of theProblem Description (i.e., the desired performance level is achievable)? has been Isolated and verified the root cause by testing each possible cause against theproblem description and test data? Have been confirmed the technical and systemic root causes? Escapepoint?Confidential and Proprietary Littelfuse, Inc. 201820
5Whys.By repeatedly asking the question “Why” (five is a good rule of thumb), you can peel awaythe layers of symptoms which can lead to the root cause of a problem.NOTE: You may find that you will need to ask the question fewer or more times than fivebefore you find the issue related to a problem.How to Complete the 5 Whys1.- Write down the specific problem. Writing the issue helps you formalize theproblem and describe it completely. It also helps a team focus on the sameproblem.2.- Ask Why the problem happens and write the answer down below the problem.3.- If the answer you just provided doesn’t identify the root cause of the problemthat you wrote down in Step 1, ask Why again and write that answer down.4.- Loop back to step 3 until the team is in agreement that the problem’s root causeis identified. Again, this may take fewer or more times than five WhysConfidential and Proprietary Littelfuse, Inc. 201821
5Whys ( Example).Problem Statement:Wrong item shipped to customerWhy?The wrong item was pulled from inventoryWhy?The item we pulled from inventory was mislabeledWhy?Our supplier mislabeled the item prior to shipping it to our warehouseWhy?The individual applying labels to our product at the supplier placed thewrong label on the product.Why?Labels for different orders are pre-printed and it is easy to apply thewrong labelConfidential and Proprietary Littelfuse, Inc. 201822
Cause and Effect Diagram.A cause and effect diagram can help in brainstorming to identify possible causes of aproblem and in sorting ideas into useful categories.In a cause and effect diagram you will find the following categories : Method / Machine /People / Environment / Measurement Method / MaterialHow to Complete a Cause and Effect Diagram1.- Agree on the problem statement.2.- Brainstorm all the possible causes of the problem. Ask “Why does it happens?” as eachidea is given, the facilitator writes the causal factor as a branch from the appropriatecategory.3.- Again ask “Why does it happen ?” about each cause . If applicable write sub-causesbranching off the cause branches.Tips:- Consider drawing your cause and effect diagram on a flip chart or large dry erase board.- Use this tool to keep the team focused on the causes of the problem, rather than symptomsConfidential and Proprietary Littelfuse, Inc. 201823
Cause and Effect Diagram ( Example).MethodMaterialNot standard process Material shrinks in Screens are nottensioned properly Wrong squeegee used-Procedure not detailedenough Over processing oninspection -Lack of Ownership -Ambient heat causeddrier temp to go out ofcontrol-ResourcesLack of formal training -Not organized areasHard to spot issueswith product --Pressure to get work outat all-EnvironmentPeopleMachineToo much pressurefrom squeegee Machining running toofast -- Drier temperature toohigh- Drier temperature notcontrolled- Thermometer is notcalibrated20% Scrap on W200print , due to poorregistration- InadequateThermometer for thisapplicationMeasurementmethodConfidential and Proprietary Littelfuse, Inc. 201824
D4.- Good / Not Good Sample.Good Sample1. True root cause identified through 5whys / Ishikawadiagram. Analysis addresses occurrence, escape pointand system root causes.2. Quality issue can be turn off and on. (root causes areverified and linkage is established to original failuremode)Not Good Sample1.No quality tools were used to find out the rootcause.2. Root cause was not verified.3.- Addressing the symptom but no the real rootcause.Confidential and Proprietary Littelfuse, Inc. 201825
D5.- Choose and Verify Permanent Corrective Actions for Root Cause andEscape Point.The goal of corrective actions is to remove the root cause and prevent the problem from ever happening again. If good corrective actions are taken , theissue must not occur again.TaskActionOutput Develop and evaluatecorrective actions for technicaland systemic root causes andescape point. Define corrective actions toeliminate the root causes(occurrence & non-detection;TRC & SRC)with evidence ofeffectiveness Consider all the correctiveactions that can eliminate theproblem. For each determined rootcause(TRC and SRC)appropriate corrective actionplan defined. Verification: no induction ofnew problems throughimplementation of correctiveactions. There is a set of well definedCorrective Actions for theOccurrence, Detection/Escapeand System.TRC Technical Root Cause(Occurrence).SRC Systemic Root Cause. There is data to show a directlink between the action and theroot cause that was identified.Confidential and Proprietary Littelfuse, Inc. 201826
D5.- Choose and Verify Permanent Corrective Actions forRoot Cause and Escape Point. Haveall possibilities for determining permanent corrective actions beenthoroughly exhausted? Have the “correct “ indicators been used to prove the effectiveness of thecorrective actions? An action plan has been defined (responsibilities assigned; timingestablished; required support determined)? Is there any emergency plan in case corrective actions do not result in thedesired success or if the actions cause other/new defect?Confidential and Proprietary Littelfuse, Inc. 201827
D5.- Good / Not Good Sample.Good Sample1.Corrective actions addresses all root causesidentified.2. Responsible for each action is identified as well asdue date and status.Not Good Sample1. Specific corrective actions are not clear.2. Status of implementation of corrective action ismissed.3.- Training is not an acceptable corrective action.Confidential and Proprietary Littelfuse, Inc. 201828
D6.- Implement and Validate Permanent Corrective Actions.The purpose of this step is to verify if the corrective actions implemented on 5D section, removed the root cause.TaskActionOutput Plan and implement selectedpermanent corrective actions. Validate effectiveness afterimplementing and ensure thatthere are no negativeconsequences. There is data to show that theeffectiveness of each CorrectiveActions was properly evaluated. Determine a plan to removethe interim containment action. Monitor the long-term results. Monitoring of correctiveactions Monitoring of defectoccurrence Document results After the actions wereimplemented, there is evidencethat the failure mode/defect hasnot reoccurred, it is detectedwith 100% confidence and theQuality and Manufacturingsystems were updated as aresult. Containment actions from D3may be removed (prioragreement with the customer),based on evidence.Confidential and Proprietary Littelfuse, Inc. 201829
D6.- Implement and Validate Permanent Corrective Actions. Do the selected corrective actions represent the best possible long term solution? The plan has been communicated to those that have a need to know? Has a schedule been drawn up for the implementation of the corrective actions? What monitoring methods have been defined? (evidence of effectiveness) All changes are documented (e. g., FMEA, Control Plan, Process Flow)?Confidential and Proprietary Littelfuse, Inc. 201830
D6.- Good / Not Good Sample.Good Sample1. Clear plan to validate the effectiveness of correctiveactions implemented.2. Effective date is clearly identified.3.- Responsible for each action is identified as well asdue date and statusNot Good Sample1. Actions to validate the effectiveness of correctiveactions are not clear.2. Responsible to complete each verification actionwas is not clear.Confidential and Proprietary Littelfuse, Inc. 201831
D7.-Preventing Recurrence.Preventive actions remove causes for a potential problem and prevent it from ever happening. 7D actions are proactive and oriented towards apotential event in the future.TaskActionOutput Establish preventive actionsto avoid occurrencecomparable problems in otherbusiness or productionprocesses and products. Transfer acquired experiencesvia Lessons Learned toother/comparable products,processes, production sites anddivisions. Updated standards (QMsystem, design rules, workinstructions etc.) are released;experiences are exchanged(Lessons Learned). Look Across and Fan Outmethodologies Modify / update the necessarysystems including policies,practices, and procedures toprevent recurrence of thisproblem and similar ones. (e.g.PFMEA, Control plan, flowchart, inspections sheets, workinstructions). There is evidence thatLessons Learned were appliedto similar products andprocesses that are sensitive tothe same defect or failure modeConfidential and Proprietary Littelfuse, Inc. 201832
D7.- Preventing Recurrence. Are there similar situations/processes elsewhere in yourplant/division/company which can benefit from what your team has learned? How can the solutions implemented in step D6 be systematized, written intopolicies, and/or added to “lessons learned?” What else can be done to insure this situation doesn’t reappear elsewhere?Confidential and Proprietary Littelfuse, Inc. 201833
D7.- Good / Not Good Sample.Good Sample1. Related documents were updated.2. PFMEA and control plan were updated.3. Responsible were assigned for each activity.4. Corrective actions were implemented across the organizationwhere applicable ( report shows evidence of implementation)Not Good Sample1. Responsible were non identified.2. Neither due date nor status of actions are clear.3. PFMEA and Control plan were not updated.Confidential and Proprietary Littelfuse, Inc. 201834
D8.- Recognize Team and Individual Contributions.This step is to recognize the team efforts and special team member contributions. This is also a good point to document lessons learned.TaskActionOutput Conduct final meeting with the8D team. Review and evaluation ofsteps D1 thru D7 Prerequisite: Completion of allsteps D1 to D7. Conclusion of the problemsolving with agreement of theinvolved persons, if necessarycustomer 8D activities related to thisproblem finally concluded. Noopen or “in-progress” actionitems. The way the team and itsmembers are acknowledged isonly limited by the creativity ofthe organization. Recognize each team memberand their contributions. Obtain customer approval toformally close the 8D’sConfidential and Proprietary Littelfuse, Inc. 201835
D8.- Recognize Team and Individual ContributionsKey questions Have the root causes been eliminated? All the corrective actions been implemented? Have monitoring processes been put in place? Has the customer been notified of the final conclusion? Team process has been evaluated and lessons learned identified? All current and past team members are being recognized? Did the Quality Manager and Plant Manager review and approve the 8D’s report(sign off)?Confidential and Proprietary Littelfuse, Inc. 201836
D8.- Good / Not Good Sample.Good Sample1. Quality and Plant Manager sign off.2. Identification of lessons learned.Not Good Sample1. Report was not approved by the quality manager norplant manager.Confidential and Proprietary Littelfuse, Inc. 201837
Example of8D’s reportConfidential and Proprietary Littelfuse, Inc. 201838
D1.- Define Team Members.The approach is based on a team working together to solve a problem. Teamwork must be coordinated and guided. The team should include onlycompetent persons actively involved in the process and who have been assigned a task or responsibility in subsequent steps.Confidential and Proprietary Littelfuse, Inc. 201839
D2.- Problem Description.Problem solving must be based on facts, not opinions. It is important to clarify the issue type, what is wrong, when did it happen, how big the failureextent is and how many times has it happened. The description must be specific and easy to understand. - See more.Confidential and Proprietary Littelfuse, Inc. 201840
D3.- Develop Interim Containment Actions.The primary purpose of this discipline is to isolate the issue and protect the customer from receiving more parts with same quality issue.Confidential and Proprietary Littelfuse, Inc. 201841
D3.- Develop Interim Containment Actions.The primary purpose of this discipline is to isolate the issue and protect the customer from receiving more parts with same quality issue.Confidential and Proprietary Littelfuse, Inc. 201842
D4.- Define and Verify Root Cause and Escape Point.To effectively prevent a problem from occurring again we have, the root cause must be indentified and removed. In rare situations there could bemore than one root cause.1) Technicalroot cause.Confidential and Proprietary Littelfuse, Inc. 201843
D4.- Define and Verify Root Cause and Escape Point.To effectively prevent a problem from occurring again we have, the root cause must be indentified and removed. In rare situations there could be morethan one root cause.1) Technicalroot cause.Confidential and Proprietary Littelfuse, Inc. 201844
D4.- Define and Verify Root Cause and Escape Point.To effectively prevent a problem from occurring again we have, the root cause must be indentified and removed. In rare situations there could bemore than one root cause.1) Technicalroot cause.Confidential and Proprietary Littelfuse, Inc. 201845
D4.- Define and Verify Root Cause and Escape Point.To effectively prevent a problem from occurring again we have, the root cause must be indentified and removed. In rare situations there could bemore than one root cause.1) Technicalroot cause.Confidential and Proprietary Littelfuse, Inc. 201846
D4.- Define and Verify Root Cause and Escape Point.To effectively prevent a problem from occurring again we have, the root cause must be indentified and removed. In rare situations there could bemore than one root cause.1) Technicalroot cause.Confidential and Proprietary Littelfuse, Inc. 201847
D4.- Define and Verify Root Cause and Escape Point.To effectively prevent a problem from occurring again we have, the root cause must be indentified and removed. In rare situations there could bemore than one root cause.2) EscapePoint.Confidential and Proprietary Littelfuse, Inc. 201848
D4.- Define and Verify Root Cause and Escape Point.To effectively prevent a problem from occurring again we have, the root cause must be indentified and removed. In rare situations there could bemore than one root cause.3) Systemicroot cause.Confidential and Proprietary Littelfuse, Inc. 201849
D5.- Choose and Verify Permanent Corrective Actions for Root Cause andEscape Point.The goal of corrective actions is to remove the root cause and prevent the problem from ever happening again. If good corrective actions have beentaken , the issue must not occur again.Confidential and Proprietary Littelfuse, Inc. 201850
D6.- Implement and Validate Permanent Corrective Actions.The purpose of this step is to verify if the corrective actions implemented on 5D section, removed the root cause.Confidential and Proprietary Littelfuse, Inc. 201851
D7.-Preventing Recurrence.Preventive actions remove causes for a potential problem and prevent it from ever happening. 7D actions are proactive and oriented towards a potentialevent in the future.Confidential and Proprietary Littelfuse, Inc. 201852
D8.- Recognize Team and Individual Contributions.This step is to recognize the team efforts and special team member contributions. This is also a good point to document lessons learned.Confidential and Proprietary Littelfuse, Inc. 201853
8D’s Problem Solving Flow Chart.D4 Root Cause Analysis.D1 Define teammembers.Indentify Potential Causes.Select Likely Causes.D5 PermanentCorrective Actions.D6 Validate PermanentCorrective Actions.D2 Define problemdescription.NOD3 Interim containmentactions.D7 EstablishPreventive Actions.RootCause?YESD8 Lessons Learn.Identify Possible Solutions.Confidential and Proprietary Littelfuse, Inc. 201854
ENDConfidential and Proprietary Littelfuse, Inc. 201855
D4.- Root Cause Analysis ( Example). 1) Technical root cause 2) Escape Point 2) Escape point 3)Systemic root cause Problem Description: Customer reported the cover HNXE13 was loose in several sensors, and sticking to the grip in others. One side of cover is loose in the sensor