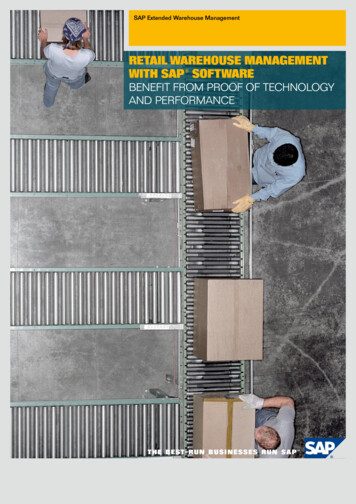
Transcription
SAP Extended Warehouse ManagementRetail Warehouse Managementwith SAP SoftwareBenefit from Proof of Technologyand Performance
CONTENT3 Overview4Executive Management Summary5High-Level Scenario Descriptions5 Inbound Goods Receipt5 Outbound Goods Issue5 Flow-Through6 Cross-Docking6 Simultaneous Scenarios7Scenario Description7 Test Methodology7 Master Data Setup andWarehouse Layout9The Inbound Scenario10 Values of PerformanceCharacteristics (Inbound)11 The Outbound Scenario12 Values of PerformanceCharacteristics (Outbound)13 Flow-Through Process14 Values of PerformanceCharacteristics (Flow-Through)15 Cross-Docking15 Values of PerformanceCharacteristics (Cross-Docking)16 Test Results16 Overall Results17 System Throughput18 CPU Utilization in SimultaneousScenario18 Find Out More19 Appendix19 Test Setup19 Test Approach20 Technical Setup: SystemLandscape and Test EnvironmentOverviewMany leading retail companies create value by leveraging a highly efficient,high-performing retail warehouse as the backbone of their commercial success.Thus, to help you make good business decisions about your retail warehousing,SAP provides a comprehensive proof of technology and performance for the latestversion of the SAP Extended Warehouse Management (SAP EWM) application.To manage today’s challenges, your retail organization requires extremeperformance, stability, and scalability of your warehouse management solutionsas well as your IT infrastructure. This document provides comprehensive,up-to-date performance information to help you optimize your IT investments.The information is designed for: Decision makers responsible for IT investments Customers implementing SAP EWM Partners providing implementation servicesSAP built a dedicated test environment to: Optimize SAP EWM application support for processes for food and hardgoods retailers, combined with guidance for detailed sizing and configuration Prove the high performance and scalability of SAP EWM Support and accelerate implementation projects for SAP EWM
Executive Management SummaryPerformance Test ResultsCompleted in early 2010, the performance test project for the SAP Extended Warehouse Management(SAP EWM) application offered comprehensive proof of performance andscalability in a real-world environmentsimulating a typical retail distributioncenter. The test focused on: Support for actual warehouse businessprocesses and achievement of keyperformance indicators (KPIs) Retail-typical logistical volumes inhard goods and food assortments An increasing number of parallelusers in warehouse processes forlarge retailersIn the performance test results, SAPEWM demonstrated the ability tohandle: Live warehouse business processes,with the test covering 39 processesin 4 scenarios for:– Inbound goods receipt, includingthe material flow system with aprogrammable logic controller(PLC) emulation– Outbound goods issue, with 10large picking waves for 42,000delivery items each– Flow-through– Cross-docking Daily mass volumes of transactionsand a secured flow of informationbetween SAP EWM, automated PLC,and mobile devices and user interfaces(UIs), as proved within the requiredKPIs:– Receipt of and wave creation for420,000 delivery items per day inabout 1 hour– Release of picking waves within15 to 20 minutes– Response time below 1 second forevery process step performed inthe mobile UI4We tested SAP EWM with industry-typical hardwareresources and normal, measured resource utilization.The test evidenced a high scalability and efficiencyof SAP EWM. In one of the most critical processsteps, picking by a warehouse worker, SAP EWMenabled 180,000 delivery items to be picked within60 minutes.Note that the results surpassed therequirements of the KPIs.One of the most important resultspertains to time-critical daily processingof information on the SKU level and ina parallel-user environment. The testresults showed that activities for complex and simultaneous warehouse processes were processed without issues,in the necessary time frames.We tested SAP EWM with industrytypical hardware resources and normal,measured resource utilization. The testevidenced a high scalability and efficiencyof SAP EWM. In one of the mostcritical process steps, picking by awarehouse worker, SAP EWM enabled180,000 delivery items to be pickedwithin 60 minutes in the outboundscenario.All of the performance test results areapplicable to every customer and partnerbecause of detailed process descriptions that enable fast implementationand support for high-performing warehouse business processes.
High-Level Scenario DescriptionsPerformance-Critical Activities of aDistribution CenterThe overall focus was on a very biggrocery distribution center with morethan 400,000 items per day of goodsissue. In addition, we tested goodsreceipt and merchandise distribution.The warehouse included automatedhigh-rack storage as well as mobiledevice integration. Thus, we examinedall main performance-critical activitiesof a distribution center, both as singleunits and as simultaneous events.The most important KPIs were asfollows: Relevant mobile device transactionshave a response time below 1second. The time for distributing store ordersfrom a central merchandise systemis sufficiently short so that the data isavailable early enough in SAP EWMfor planning purposes.Inbound Goods ReceiptWe tested the following scenario:obtaining goods from reliable vendors,with the warehouse already having beennotified of all arriving physical deliveriesvia electronic data interchange or a similarnotification method, such as fax.The performance-measurement schemesdifferentiated between a big number ofdeliveries with only a few items eachand a small number of deliveries with alot of items. The scenario involved thefollowing steps:1. The full freight vehicle arrived withpalletized goods.2. The driver contacted the goodsreceipt office.3. The office clerk posted the goodsreceipt.4. Workers unloaded pallets from thefreight vehicle.5. Workers put away pallets, accordingto system-guided strategies, usinga material flow system.Outbound Goods IssueThe outbound goods issue scenariotested goods issue for stores, plannedas distributed workload over the workinghours by grouping deliveries accordingto their planned time of leaving thedistribution center.The measurement schemes tested aworking period of either one shift orone of two shifts. We grouped the outgoing deliveries of one day in pickingwaves. For every wave, the followingwork was done:1. After the internal replenishment fromthe high rack to the picking zone,warehouse workers picked productsfor each store per store order usingmaterial-handling trucks. The pickingstrategy was man-to-goods, andworkers confirmed every pick.2. At the same time, the empty freightvehicles arrived and docked at thedoors.3. After picking, the workers transported the material-handling trucks to thegoods-issue staging area.4. Workers loaded every materialhandling truck into a freight vehicleand printed the delivery note.5. Workers closed the freight vehicle,and the vehicle left the distributioncenter.Flow-ThroughThe flow-through focused on the followingtask: a planned distribution of productsfrom vendor pallets to store materialhandling trucks in the distribution center;this is called “product-driven flowthrough.” This activity took place aftera goods receipt, more or less withoutany storage time. As in the first scenarios,the assumption was that planning datawas already in SAP EWM. The detailedsteps were as follows:1. The full freight vehicle arrivedwith palletized goods. (Every palletcontained only one product.)2. Warehouse workers unloaded thepallets from the freight vehicle andtransported them to the distributionarea.3. There, workers distributed the products as planned from the pallets tomaterial-handling trucks for differentstores. At the same time, emptyfreight vehicles arrived and dockedat the doors.4. After picking, workers transportedthe material-handling trucks to thegoods issue staging area and thenloaded every material-handling truckin a freight vehicle and printed thedelivery note.5. Workers closed the freight vehicle,and the vehicle left the distributioncenter.5
InboundUnloading and ure 1: Simultaneous Scenarios in Two ShiftsCross-DockingIn this scenario, we tested a distribution of complete pallets – such as thedistribution of prepacked pallets – fromvendor to stores in the distribution center. The planning data was already inSAP EWM. The steps were as follows:1. The full freight vehicle arrived withpalletized goods.2. After unloading the pallets from thefreight vehicle, workers transportedthe pallets to the goods issue staging area, according to the plan.3. At the same time, the empty freightvehicles arrived and docked at thedoors.64. After picking and staging, the workers loaded every material-handlingtruck into a freight vehicle and printed the delivery note.5. Workers closed the freight vehicle,and the vehicle left the distributioncenter.Simultaneous ScenariosIn addition to testing the scenarios individually, we tested them simultaneously, because this simultaneous processing occurs in real-life warehouses (seeFigure 1). For example, outbound processes of subsequent picking wavescould overlap in time. Outbound processes took place throughout thewhole day, while most of the inboundprocesses took place in the morning.The test scenarios covereda realistic set of businessactivities that are relevant fora large grocery distributioncenter. For efficiency, theimplementation optimizedsupport for processes andminimized the interaction ofoffice workers with the software system. Mobile devicesenabled system-guided, validated execution of the warehouse labor. To test potentialperformance-relevant characteristics of the scenarios, weexamined extreme occurrences of the characteristics.
Scenario DescriptionThe Technical Aspects of the TestingThe test scenarios covered a realisticset of business activities that are relevant for a large grocery distributioncenter. For efficiency, the implementationoptimized support for processes andminimized interaction of office workerswith the software system. Mobile devicesenabled system-guided, validated execution of the warehouse labor. To testpotential performance-relevant characteristics of the scenarios, we examinedextreme occurrences of the characteristics. However, the scenarios were stillwithin the borders of expected businessprocesses in retail.Test MethodologyWe conducted the test on a softwaresystem that we created by merelycustomizing a standard SAP EWM 7.0application. The technical details of thetest setup – such as the server hardware and the approach of consecutivetest phases – are described in theappendix section of this document.Master Data Setup and WarehouseLayoutThe master data setup described here,together with the material flow depictedin Figure 2, gives a brief but informativeoverview of the implementation of SAPEWM. The layout in Figure 2 shows thematerial flow of all four scenarios inscope, abstracting from the real implemented warehouse layout. The left sidewas reserved for goods receipt, theright side for goods issue. The materialflow started with unloading (inbound,flow-through, and cross-docking). In theinbound scenario, handling units werestored in high-rack storage that wasfully automated by the material flowsystem. That means that the movementfrom the staging area to high-rack storage– that is, put-away – ended at the identification point of the high-rack storagearea. SAP EWM controlled the materialflow within the high-rack storage areaby sending telegrams to the PLC.The same situation existed for thereplenishment step, which was thestarting point of the outbound scenario.Here, workers moved pallets from highrack storage picking points to the picking area. The pickers collected itemsfrom the replenished pallets and putthem into material-handling trucks,Stagingarea1High-rack storage2InboundIdentification Pickingpointpointwhich were then moved to the stagingarea (picking and staging). In the flowthrough scenario, workers removed thereceived pallets (put-away) to the distribution area, and there the workersdistributed items to material-handlingtrucks (picking), which were then transported to the outbound staging area. Inthe cross-docking scenario, workersdirectly moved pallets from the inboundstaging area to the outbound stagingarea, a process that is also called“picking.” Finally, in outbound, flowthrough, and cross-docking, workersloaded the staged handling units ontofreight vehicles.Picking area3Stagingarea4Identification n area124.56Cross-docking11 Unloading 2 Put-away43 Replenishment64 Picking5 Staging6 LoadingFigure 2: Warehouse Layout for Performance-Testing Scenarios7
The master-data setup supported theintended throughput (see the table).The number of vendors, products, andstores reflected the quantity structureof inbound deliveries and outbounddeliveries. In the first testing of the inbound scenario, for example, detailedin the section titled “The InboundScenario,” 1,000 items of 1 producteach were delivered in 40 deliveries.The number of doors, in contrast,depended on the intended parallelizationof the unloading and loading processes.In this test, for instance, 20 mobileusers unloaded the 40 deliveries. Inaddition, because mobile users had tolog in to unique resources of SAP EWM,these resources exactly mirrored theparallelization of the related mobilebased processes.Master sStoresProductsDoors – InDoors – OutHigh-rack storage(material flow system)Resources (RF) g40–1,00020–4 identification points–4201,000–424 picking ��420420421–12440401––3–238
The Inboun
SAP Extended Warehouse Management Retail WaRehouse ManageMent With saP softWaRe Benefit from Proof of technology and Performance. 3 overview 4 Executive Management Summary 5 High-Level Scenario Descriptions 5 inbound goods receipt 5 outbound goods issue 5 flow-through 6 cross-docking 6 Simultaneous Scenarios 7 Scenario Description 7 test methodology 7 master data Setup and