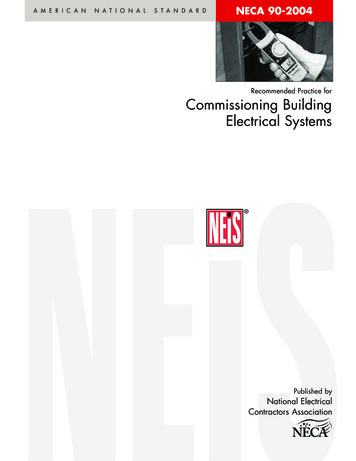
Transcription
A M E R I C A NN A T I O N A LS T A N D A R DNECA 90-2004Recommended Practice forCommissioning BuildingElectrical Systems Published byNational ElectricalContractors Association
NECA 90-2004Recommended Practice forCommissioning BuildingElectrical SystemsAn AmericanNational StandardT Published byNational ElectricalContractors AssociationJointly developed withEnviro-Management& Research, Inc.
NOTICE OF COPYRIGHTThis document is copyrighted by NECAReproduction of these documents either in hard copy or soft (including posting on the web) is prohibitedwithout copyright permission. For copyright permission to reproduce portions of this document, pleasecontact NECA Standards & Safety at (301) 657-3110 ext. 546, or send a fax to (301) 215-4500.ORNational Electrical Contractors Association3 Bethesda Metro Center, Suite 1100Bethesda, Maryland 20814(301) 657-3110Organizations may obtain permission to reproduce a limited number of copies by entering into a licenseagreement. For information, contact:Global Engineering Documents15 Iverness Way EastEnglewood, CO 80112-5704 or call1-800-854-7179 (USA and Canada)(303) 397-7956 (International)
Table of ContentsForeword . . . . . . . . . . . . . . . . . . . . . . . . . . . . . . . . . . . . . . . . . . . . . . . . . . . . . . . . . . . . . .v1.1.11.2Scope . . . . . . . . . . . . . . . . . . . . . . . . . . . . . . . . . . . . . . . . . . . . . . . . . . . . . . . . . . . . . . . . .1Applications Included . . . . . . . . . . . . . . . . . . . . . . . . . . . . . . . . . . . . . . . . . . . . . . . . . . . . . . . . . . . . . . . .1Regulatory and Other Requirements . . . . . . . . . . . . . . . . . . . . . . . . . . . . . . . . . . . . . . . . . . . . . . . . . . . .12.Definitions . . . . . . . . . . . . . . . . . . . . . . . . . . . . . . . . . . . . . . . . . . . . . . . . . . . . . . . . . . . . .23.3.13.23.33.4Commissioning Process . . . . . . . . . . . . . . . . . . . . . . . . . . . . . . . . . . . . . . . . . . . . . . . . . . . 3Commissioning Intent . . . . . . . . . . . . . . . . . . . . . . . . . . . . . . . . . . . . . . . . . . . . . . . . . . . . . . . . . . . . . . . .3Roles and Responsibilities of the Commissioning Authority . . . . . . . . . . . . . . . . . . . . . . . . . . . . . . . . . .3Commissioning Authority Qualifications . . . . . . . . . . . . . . . . . . . . . . . . . . . . . . . . . . . . . . . . . . . . . . . . .4Roles and Responsibilities of Other Parties . . . . . . . . . . . . . . . . . . . . . . . . . . . . . . . . . . . . . . . . . . . . . . . .44.4.14.24.3Testing Requirements . . . . . . . . . . . . . . . . . . . . . . . . . . . . . . . . . . . . . . . . . . . . . . . . . . . . .6Test Equipment . . . . . . . . . . . . . . . . . . . . . . . . . . . . . . . . . . . . . . . . . . . . . . . . . . . . . . . . . . . . . . . . . . . . . 6Verification and Pre-functional Performance Testing . . . . . . . . . . . . . . . . . . . . . . . . . . . . . . . . . . . . . . . 6Functional Performance and Condition Monitoring Tests . . . . . . . . . . . . . . . . . . . . . . . . . . . . . . . . . . . 74.3.1Medium and High Voltage Power Cables (above 600V) . . . . . . . . . . . . . . . . . . . . . . . . . . . . . . . .74.3.2Low Voltage Power Cable (below 600V) . . . . . . . . . . . . . . . . . . . . . . . . . . . . . . . . . . . . . . . . . . . .74.3.3Electrical Feeders and Branch Circuits (600V or below) . . . . . . . . . . . . . . . . . . . . . . . . . . . . . . . .74.3.4Liquid-Filled Transformers . . . . . . . . . . . . . . . . . . . . . . . . . . . . . . . . . . . . . . . . . . . . . . . . . . . . . .74.3.5Dry-Type Transformers . . . . . . . . . . . . . . . . . . . . . . . . . . . . . . . . . . . . . . . . . . . . . . . . . . . . . . . . .84.3.6Instrument Transformers . . . . . . . . . . . . . . . . . . . . . . . . . . . . . . . . . . . . . . . . . . . . . . . . . . . . . . .84.3.7Switchgear and Switchboard Assemblies Rated 1200A or Greater . . . . . . . . . . . . . . . . . . . . . . . . .84.3.8Metal-Enclosed Bus Duct . . . . . . . . . . . . . . . . . . . . . . . . . . . . . . . . . . . . . . . . . . . . . . . . . . . . . . .94.3.9Motor Control Centers . . . . . . . . . . . . . . . . . . . . . . . . . . . . . . . . . . . . . . . . . . . . . . . . . . . . . . . . .94.3.10 Medium-Voltage Circuit Breakers . . . . . . . . . . . . . . . . . . . . . . . . . . . . . . . . . . . . . . . . . . . . . . . . .94.3.11 Low-Voltage Air Circuit Breakers . . . . . . . . . . . . . . . . . . . . . . . . . . . . . . . . . . . . . . . . . . . . . . . . .94.3.12 High and Medium-Voltage Air Switches . . . . . . . . . . . . . . . . . . . . . . . . . . . . . . . . . . . . . . . . . . .104.3.13 Protective Relays . . . . . . . . . . . . . . . . . . . . . . . . . . . . . . . . . . . . . . . . . . . . . . . . . . . . . . . . . . . . .104.3.14 Molded-Case Circuit Breakers . . . . . . . . . . . . . . . . . . . . . . . . . . . . . . . . . . . . . . . . . . . . . . . . . . .104.3.15 Service Ground . . . . . . . . . . . . . . . . . . . . . . . . . . . . . . . . . . . . . . . . . . . . . . . . . . . . . . . . . . . . . .104.3.16 Ground-Fault Protection Systems . . . . . . . . . . . . . . . . . . . . . . . . . . . . . . . . . . . . . . . . . . . . . . . .114.3.17 Panelboards . . . . . . . . . . . . . . . . . . . . . . . . . . . . . . . . . . . . . . . . . . . . . . . . . . . . . . . . . . . . . . . . .114.3.18 Recepticles and Devices . . . . . . . . . . . . . . . . . . . . . . . . . . . . . . . . . . . . . . . . . . . . . . . . . . . . . . . .114.3.19 Engine Generators . . . . . . . . . . . . . . . . . . . . . . . . . . . . . . . . . . . . . . . . . . . . . . . . . . . . . . . . . . . .114.3.20 Automatic Transfer Switches . . . . . . . . . . . . . . . . . . . . . . . . . . . . . . . . . . . . . . . . . . . . . . . . . . . .124.3.21 Variable Frequency Drives . . . . . . . . . . . . . . . . . . . . . . . . . . . . . . . . . . . . . . . . . . . . . . . . . . . . .124.3.22 Rotating Machinery . . . . . . . . . . . . . . . . . . . . . . . . . . . . . . . . . . . . . . . . . . . . . . . . . . . . . . . . . .124.3.23 Battery Systems . . . . . . . . . . . . . . . . . . . . . . . . . . . . . . . . . . . . . . . . . . . . . . . . . . . . . . . . . . . . .134.3.24 Uninterruptible Power Supply (UPS) System . . . . . . . . . . . . . . . . . . . . . . . . . . . . . . . . . . . . . . .134.3.25 Lighting . . . . . . . . . . . . . . . . . . . . . . . . . . . . . . . . . . . . . . . . . . . . . . . . . . . . . . . . . . . . . . . . . . . .144.3.26 System Testing . . . . . . . . . . . . . . . . . . . . . . . . . . . . . . . . . . . . . . . . . . . . . . . . . . . . . . . . . . . . . . .15iii
NECA 90Recommended Practice for Commissioning Building Electrical Systems4.44.5Deferred Testing . . . . . . . . . . . . . . . . . . . . . . . . . . . . . . . . . . . . . . . . . . . . . . . . . . . . . . . . . . . . . . . . . . . .15Seasonal Testing . . . . . . . . . . . . . . . . . . . . . . . . . . . . . . . . . . . . . . . . . . . . . . . . . . . . . . . . . . . . . . . . . . . .155.5.15.2Recording and Documenting Performance . . . . . . . . . . . . . . . . . . . . . . . . . . . . . . . . . . . . .16Documentation . . . . . . . . . . . . . . . . . . . . . . . . . . . . . . . . . . . . . . . . . . . . . . . . . . . . . . . . . . . . . . . . . . . . .16Non-conformance Forms . . . . . . . . . . . . . . . . . . . . . . . . . . . . . . . . . . . . . . . . . . . . . . . . . . . . . . . . . . . . .166.O&M Manuals . . . . . . . . . . . . . . . . . . . . . . . . . . . . . . . . . . . . . . . . . . . . . . . . . . . . . . . . .177.Training . . . . . . . . . . . . . . . . . . . . . . . . . . . . . . . . . . . . . . . . . . . . . . . . . . . . . . . . . . . . . .18Annex A: Test and Measurement Equipment . . . . . . . . . . . . . . . . . . . . . . . . . . . . . . . . . . . . . . . . 19A.1 Vibration Monitoring . . . . . . . . . . . . . . . . . . . . . . . . . . . . . . . . . . . . . . . . . . . . . . . . . . . . . . . . . . . . . . . .19A.2 Infrarad Thermography (IRT) . . . . . . . . . . . . . . . . . . . . . . . . . . . . . . . . . . . . . . . . . . . . . . . . . . . . . . . . .19A.3 Insulation Power Factor . . . . . . . . . . . . . . . . . . . . . . . . . . . . . . . . . . . . . . . . . . . . . . . . . . . . . . . . . . . . . .19A.4 Battery Impedance . . . . . . . . . . . . . . . . . . . . . . . . . . . . . . . . . . . . . . . . . . . . . . . . . . . . . . . . . . . . . . . . . .20A.5 Breaker Timing . . . . . . . . . . . . . . . . . . . . . . . . . . . . . . . . . . . . . . . . . . . . . . . . . . . . . . . . . . . . . . . . . . . . .20A.6 Insulation Resistance . . . . . . . . . . . . . . . . . . . . . . . . . . . . . . . . . . . . . . . . . . . . . . . . . . . . . . . . . . . . . . . .20Annex B: Reference Standards . . . . . . . . . . . . . . . . . . . . . . . . . . . . . . . . . . . . . . . . . . . . . . . . . . .21 iv
(This foreword is not a part of the standard)ForewordNational Electrical Installation Standards (NEIS ) are designed to improvecommunication among specifiers, purchasers,and suppliers of electrical construction services.They define a minimum baseline of quality andworkmanship for installing electrical productsand systems. NEIS are intended to be referencedin contract documents for electrical constructionprojects. The following language isrecommended:All electrical systems shall be commissionedin accordance with NECA 90-2004, Standardfor Commissioning Building ElectricalSystems (ANSI).Use of NEIS is voluntary, and the NationalElectrical Contractors Association (NECA)assumes no obligation or liability to users of thispublication. Existence of a standard shall notpreclude any member or non-member of NECAfrom specifying or using alternate constructionmethods permitted by applicable regulations.This publication is intended to comply with theedition of the National Electrical Code (NEC) ineffect at the time of publication. Because theyare quality standards, NEIS may in someinstances go beyond the minimum safetyrequirements of the NEC. It is the responsibilityof users of this publication to comply with stateand local electrical codes when installingelectrical products and systems.Suggestions for revisions and improvements tothis standard are welcome. They should beaddressed to:NECA Standards & Safety3 Bethesda Metro Center, Suite 1100Bethesda, MD 20814(301) 657-3110(301) 215-4500 faxwww.neca-neis.orgneis@necanet.orgTo purchase NEIS, contact the NECA OrderDesk at (301) 215-4504 tel, (301) 215-4500 fax,or orderdesk@necanet.org. NEIS can also bepurchased in .pdf download format atwww.neca-neis.org/standards.Copyright 2004, National ElectricalContractors Association. All rights reserved.Unauthorized reproduction prohibited.National Electrical Installation Standards,NEIS, and the NEIS logo are trademarks of theNational Electrical Contractors Association.National Electrical Code and NEC are registeredtrademarks of the National Fire ProtectionAssociation.Cover photo courtesy of Fluke Networks.v
This page intentionally left blank
1. ScopeThis standard describes installation proceduresfor commissioning newly installed or retrofittedbuilding electrical systems. It defines theprocess of commissioning building electricalsystems and provides sample guidelines forattaining optimum system performances thatconform to design, specification, and industryaccepted codes and standards.1.1 Regulatory and Other Requirementsa) All information in this publication isintended to conform to the National ElectricalCode (ANSI/NFPA 70). Installers shouldalways follow the NEC, applicable state andlocal codes, manufacturer’s instructions, andcontract documents when commissioning newlyinstalled or retrofitted building electricalsystems.b) Only qualified persons familiar with thecommissioning of building electrical systemsshould perform the work described in thispublication.c) General requirements for installing electricalproducts and systems are described in NECA 1,Standard Practices for Good Workmanship inElectrical Contracting (ANSI). Other NationalElectrical Installation Standards provideadditional guidance for installing particulartypes of electrical products and systems. Acomplete list of NEIS is provided in Annex B.1
2. DefinitionsAcceptablePerformancePerformance of systems,subsystems and componentsthat meets specified design performance perimeters underactual load, and responds tochanging conditions andperimeters appropriately asexpected and specified.Basis of DesignA document that records thedesign criteria and assumptionsupon which the design is based.Design IntentA narrative description of systems equipment and theirintended modes and sequencesof operation, as documented inthe project drawings and specifications.CommissioningA systematic process for ensuring that in a building the electrical system performs in accordance with the design intentand the owner’s vidual or company responsible for developing and coordinating the execution of a commissioning plan, observing anddocumenting performance, andensuring that building systemsand equipment function inaccordance with the designintent and the owner’s operational requirements. 2CommissioningPlanA document that outlines theorganization, scheduling, andallocation of resources and documentation for the overall commissioning process.FunctionalPerformanceTestsA full range of checks and testscarried out to determine if allsystems, subsystems, and components function in accordancewith the design intent.VerificationThe full range of checks andtests carried out to determine ifall components, subsystems, systems, and interfaces betweensystems operate in accordancewith the contract documents. Inthis context, “operate” includesall modes and sequences of control operation, interlocks andconditional control responses,and specified responses toabnormal or emergency conditions.
3. Commissioning ProcessCommissioning of building electrical systems is asystematic process of ensuring that all systems perform in accordance with the design intent and theowner’s operational needs. This is achieved by verifying that the performance meets or exceeds thedesigner’s intent as documented in the project drawings and specifications. The electrical commissioningprocess includes the traditionally separate functionsof equipment startup, control system calibration,testing and balancing, functional performance testing, system documentation, and training.3.1Commissioning IntentElectrical system commissioning should achieve thefollowing objectives:a) Ensure that all electrical equipment, subsystems,and systems are installed according to the final plans,specifications, and requirements; the contract documents; the manufacturer’s recommendations; and toindustry accepted minimum standards. Ensure thatall electrical equipment, subsystems, and systems,and that they receive adequate operational checkout,as well as detailed testing, calibration, and adjustment by the installing contractor.b) Verify and document proper performance of allelectrical equipment and systems.c) Ensure that electrical system operations andmaintenance (O&M) documentation, as required bythe contract documents, is complete and left on site.d) Ensure that the Owner’s operating personnel areadequately trained on all electrical equipment, asrequired by the contract documents.3.2Roles and Responsibilities of theCommissioning AuthorityThe Commissioning Authority (CA) is responsiblefor developing and coordinating the execution of acommissioning plan, observing and documentingperformance, and ensuring that electrical systems arefunctioning in accordance with the documenteddesign intent and contract documents. The CA doesnot have authority to approve materials, methods,and systems, but can recommend their approval tothe owner, project manager, or contracting officer.The CA should be the installing electrical contractor, the electrical design engineer, or a third partycontracted to perform the commissioning process.In general, the CA is responsible for the followingtasks:a) Obtaining and reviewing design documents foroverall design intent and the overall required systemconfigurations.b) Reviewing shop drawings and submittals forinstallation criteria and construction details as theysupport and define system features.c) Coordinating and directing commissioning activities in a logical, sequential, and efficient manner,using standard forms and centralized documentation.d) Providing all field technical services, tooling,equipment, instrumentation, and technical supervision to perform all tests and inspections.e) Providing specific power requirements for testequipment.3
NECA 90Recommended Practice for Commissioning Building Electrical Systemsf) Reviewing and approving O&M materials, controlsequences and interlocks, contractor start-up procedures, and checkout procedures for completeness andaccuracy.g) Developing and distributing the required electrical pre-functional test forms.e) Design specification and installation of buildingsystems and equipment.f) Writing functional performance test plans anddirecting building system tests, including workingwith testing instrumentation.g) Developing and managing project documentation.h) Performing site visits, as necessary, to observecomponent and system installations.i) Coordinating, witnessing, and approving functional performance tests performed by the installingcontractor(s). Coordinating re-testing as necessaryuntil satisfactory performance is achieved.j) Notifying the owner’s representative and otherconcerned parties of the commissioning schedule,and of deficiencies and follow-up services undertaken to correct and re-test deficient items.k) Providing a detailed, data-based report of all testrecords, testing, results, and recommendations.3.3Commissioning Authority QualificationsThe CA should have several years of experience incommissioning techniques and practices as they pertain to systems and equipment testing, adjusting, andbalancing; sound and vibration measurement; performance documentation; performance versus designcriteria; operation verification; and functional performance testing. The CA should have expertise in thefollowing (for further guidance, refer to NETA standard ETT-2000):h) Planning and delivering O&M training.i) Total quality for successful project performance.3.4Roles and Responsibilities of OtherPartiesProper commissioning of building electrical systemsrequires cooperation and coordination between alltrades. In particular, the electrical contractor,mechanical contractor, and the electrical design engineers have key roles and responsibilities. The rolesand responsibilities of the CA and all contractorsshould be included in the contract documents andCommissioning Plan. Failure to perform these dutiesin a timely manner should be considered a breach ofcontract.3.4.1 Electrical ContractorThe electrical contractor provides and installs theelectrical equipment and furnishes all tools needed tostart up, check out, and conduct functional performance tests on the electrical systems and equipmentinstalled.3.4.2 Mechanical Contractora) All commissioning functions and the work eachcontractor is providing.b) Operation and maintenance requirements of allbuilding systems.c) Construction management.d) Building codes and standards, including those foreach applicable construction industry (e.g., electrical,lighting, HVAC, plumbing, etc.). 4The mechanical contractor installs all mechanicalequipment in accordance with the contract documents, performs pre-functional and functional testsas defined in the Commissioning Plan, and coordinates work with other trades. Motors are generallyinstalled on equipment by the mechanical contractor.For this reason, the mechanical contractor is responsible for functional tests involving vibration monitoring, balance, and adjustment. The controls contractoris responsible for functional testing of the mechanicalcontrol system.
Commissioning Process3.4.3 Electrical Design EngineerThe electrical design engineer is responsible fordeveloping the design concepts, establishing thedesign criteria, and ensuring compliance with codes.The electrical design engineer is also responsible fordeveloping the design intent and the basis of design,construction scheduling, estimating cost, and fordeveloping the technical project specifications.5
4. Testing RequirementsConduct tests of electrical equipment, subsystems,and systems using normal procedures and requirements to ensure safety. Disconnect sensitive electronic equipment, such as TVSS devices, before dielectricor megger tests. Also, items such as transformers andcoils should have one side disconnected before suchtests.4.1Test EquipmentCommissioning electrical equipment requires theuse of proper test equipment. Many electrical systems require special tools and instruments for measurement of the equipment performance. All electrical testing equipment should be of sufficientquality and accuracy to test and/or measure thesystem performance with tolerance levels specifiedin the manufacturer’s specifications and designdocuments.a) Calibration. It is essential that all test equipmentused for performance verifications during the commissioning process has been calibrated within oneyear of its use for testing.b) Data Logging. Use data logging instruments andsoftware to measure the performance of electricalequipment and systems performance over a specifiedtime, to ensure that they are functioning in accordance with the design intent and specifications. Thismay require energy management control systemtrending, stand-alone data log monitoring, or manual functional testing.4.2Verification and Pre-functionalPerformance TestingThe objective of verification and pre-functional performance tests is to ensure that the specified equipment, subsystem, or system is installed correctly, 6starts up, and is ready for functional performancetests. This includes all operating modes, interlocks,control responses, and specific responses to abnormalor emergency conditions.These tests are often in checklist format. They arebased on design intent documentation and equipment submittals. The verification checklists should ata minimum ensure:a) All related equipment has been started up, withstart-up reports and pre-functional checklists submitted and approved as ready for functional testing.b) Testing, balancing, and calibration is completeand accepted by commissioning authority.c) All control system functions and all interlockingsystems are programmed and operable per contractdocuments, including final set points and schedules,with debugging, loop tuning and sensor calibrationscompleted.d) All architectural/engineering (A/E) punchlistitems for this equipment have been corrected.e) Functional test procedures have been reviewedand approved by the installing contractor.f) Safety, operating ranges, and functions have beenreviewed by the commissioning authority.g) Sufficient clearance around equipment is provided for servicing and maintenance.h) A record has been made of all values for pre-testset points that were changed to accommodate testing.Check boxes can be used to verify that All pre-test setpoints (control parameters, limits, delays, lockouts,
Testing Requirementsschedules, etc.) have been returned to original values,as verified by a check box.b) Perform an insulation resistance test using a testvoltage of 1000V DC.i) Other operational, safety, alarm checks, and startup reports have been completed successfully.c) Perform a continuity test to insure correct cableconnection.4.3Functional Performance andCondition Monitoring Tests4.3.3 Electrical Feeders and Branch Circuits(600V or below)Pre-functional and functional performance testsdetermine if the electrical system is providing therequired services in accordance with the finalizeddesign intent. Each functional performance testshould be performed under conditions that simulateactual operating conditions as closely as possible.a) Test each circuit for continuity to insure correctcable connection.Upon satisfactory completion of all verified tests, thebuilding electrical equipment and systems should bereturned to the condition required by the contractdocuments as a complete and operational system.Deficiencies should be corrected by the installingcontractor and the equipment, subsystems, or systems re-tested.When performing any test, be sure to follow propersafety procedures and use personal protective equipment (PPE).4.3.1 Medium and High Voltage Power Cables(above 600V)a) Perform a visual and mechanical inspection ofcable and connections.b) Perform an insulation resistance test using a testvoltage of 2500V DC or higher.b) Physically examine the grounding installation toensure that the equipment grounding conductor,grounding electrode conductor, and bonding groundjumpers are properly installed and firmly connected.c) Perform a 500-volt megohm meter test on eachcircuit cable rated 300 volts and below, and a 1000volt megohm meter test on each circuit cable rated600 volts, between the conductor and ground. Theinsulation resistance shall not be less than 2 megohmsfor circuits under 115V, 6 megohms between conductor and ground on those 115-600V circuits (115V –600V) with total single conductor length of 2500 feetand over, and not less than 8 megohms for 115-600Vcircuits with single conductor length of less than 2500feet. If the conductor fails the test, have the installingcontractor replace the conductor and replace wiringto correct the defect and retest.d) Using a calibrated torque wrench, perform torquetest for every conductor that is part of the tested circuit and terminated in an overcurrent device or bolted type connections. Torque all connections in accordance with the per manufacturer’s recommendationsand record the results on a tabular form.c) Perform a DC hi-pot test and a shield continuitytest in accordance with NECA 600, NEMA/ICEA,NETA, and IEEE standards.f) Verify conductor color coding with applicablespecifications and the National Electrical Code.d) For additional information, see NECA 600.4.3.4 Liquid-Filled Transformers4.3.2 Low Voltage Power Cable (below 600V)a) Perform visual and mechanical inspection oftransformer and connections.a) Perform a visual and mechanical inspection ofcable and connections.7
NECA 90Recommended Practice for Commissioning Building Electrical Systemsb) Perform an insulation resistance test on windingto-winding and on each winding-to-ground as follows: For transformers rated 600V and below, use aminimum voltage of 1000V DC For transformers rated 601-5000V, use a minimum voltage of 2500V DC For transformers rated above 5000V, use a minimum voltage of 5000V DCe) Perform an insulation power factor/dissipationfactor tests on each winding in accordance withtransformer manufacturer’s published data or testequipment manufacturer’s published data.f) For additional information, see NECA 409.4.3.6 Instrument Transformersa) Perform an insulation resistance test.b) Perform a ration and polarity test.c) Perform a turns ratio test at all tap positions.d) Perform liquid insulation tests for dielectricstrength, acidity, interfacial tension, specific gravity,water content, power factor/dissipation factor, andcolor.e) Perform an insulation power factor/dissipationfactor test on each winding in accordance with transformer manufacturer’s published data or test equipment manufacturer’s published data.f) Perform a power factor test on transformer bushings that are equipped with power factor taps, andperform hot color test on filled bushings that are notequipped with power factor taps.4.3.5 Dry-Type Transformersa) Perform an insulation resistance tests on windingto-winding and winding-to-ground as follows:4.3.7 Switchgear and Switchboard AssembliesRated 1200A or Greatera) Perform a visual inspection. Torque all boltedconnections to manufacturer’s specified values usinga calibrated torque wrench.b) Perform an insulation resistance test on each bussection, phase-to-phase, and phase-to-ground, andon control wiring. Minimum test voltage and insulation resistance shall be as shown in Table 1.c) Perform a power factor test. For switchgear rated5 kV and above, power factor should not exceed thevalues shown in Table 2.d) Perform a thermographic infrared scan under fullload. Identify all hot spots and promptly mark andcorrect sources of heating problems.e) For additional information, see NECA 400. For transformers rated 600V and below, use aminimum voltage of 1000V DCTable 1 For transformers rated 601-5000V, use a minimum voltage of 2500V DC For transformers rated above 5000V, use a minimum voltage of 5000V DCMinimum Test Voltage andInsulation ResistanceVoltageRatingMinimum TestVoltageMinimumInsulationResistance500V DC25 ohmsb) Perform polarization index test.0-250Vc) Perform a turns ratio test at all tap positions.250-600V1000V DC100 ohms601-5000V2500V DC1000 ohms5001-15,000V2500V DC5000 ohmsd) Perform an overpotential test on all high and lowvoltage windings-to-ground. 8
Testing Requirementsc) Measure insulation resistance of the line busphase-to-phase and phase-to-ground.4.3.8 Metal-Enclosed Bus Ducta) Measure insulation resistance of each bus phaseto-phase and phase-to-ground for one (1) minute.b) Inspect all accessible bus joints and cable connections by infrared scanner while maintaining maximum load on the bus for at least one hour, or untiltemperature has stabilized, to detect loose or highresistance connections and other circuit anomalies.c) Perform an overpotential test on each buswayphase-to-ground, with the phases not under testgrounded, in accordance with manufacturer’s published data.d) Perform thermographic infrared scan under load.Identify all hot spots and correct sources of heatingproblems promptly.e) For addit
all electrical equipment, subsystems, and systems, and that they receive adequate operational checkout, as well as detailed testing, calibration, and adjust-ment by the installing contractor. b) Verify and document proper performance of all electrical equipment and systems. c) Ensu