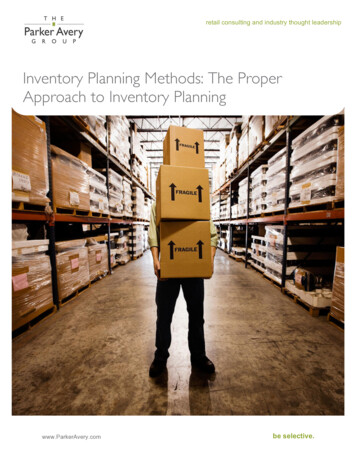
Transcription
Inventory Planning Methods: The ProperApproach to Inventory Planningwww.ParkerAvery.combe selective.!!!retail consultingindustrythoughtInventory andPlanningMethods !1leadership
Inventory Planning Methods !2Merchandise planning is a systematic approach taken tomaximize inventory investment and increase profitability.Proper inventory planning strives to ensure markdowns due to overstock and lost salesdue to stock outs are minimized.The leading practice for inventory planning is to enter key performance indicator (KPI)values, based on historical performance, and derive the inventory values. There are sixmethods for planning inventory values:1. Forward Weeks of Supply2. Weeks of Supply3. Stock to Sales Ratio4. Sell Through Percent5. Turn6. Basic StockThese methods are outlined next along with our strategic recommendation forimplementing inventory planning in your retail business.Copyright The Parker Avery Group. All rights reserved.be selective.!
Inventory Planning Methods! !31. Forward Weeks of SupplyForward Weeks of Supply (FWOS) is superior for planning appropriate inventory levelsin plans to the week level. Using FWOS allows a planner to think about their inventoryacross time and is essential to effectively managing inventory levels. The goal ofeffective inventory management is to have enough inventory on hand at any given timeto support planned sales until the next delivery arrives.FWOS is calculated as the number of weeks of planned sales from the next weekforward that the current inventory value represents. When FWOS is entered in a plan, itwill calculate the ending period inventory (EOP) by counting the forward number ofweeks of sales and summing the value to calculate the required ending inventory. Toillustrate (using the method of wrapping sales to the beginning of the plan when forwardsales are exhausted):Figure 1: FWOS Sample CalculationWeek 1Week 2Week 3Week 4Week 5Week 6Sales102025607515FWOS (entered)4.04.03.53.03.04.0EOP (calculated)18017515510045115FWOS requires a complex calculation when planning the end of the plan time horizonand the sales of the plan have been exhausted. There are advantages anddisadvantages to Forward Weeks of Supply, but we believe its complexity is worth theeffort.www.ParkerAvery.combe selective.!
Inventory Planning Methods !4Advantages of using Forward Weeks of Supply as a planned valueInventory is linked to the sales trendacross timeBetter information to make merchandisechoicesPlanned sales trends are the driving factorwhen using FWOS. Inventory levels areplanned to meet future sales and thepotential for overstock situations isdiminished. FWOS puts the focus onmaximizing the return on the inventoryinvestment by linking inventory levelsdirectly to planned sales.With explicit visibility to the amount ofinventory required to meet sales objectives,Forward Weeks of Supply provides greaterinsight into how each product and/orcategory will contribute to the overallinventory objectives.Disadvantages of using Forward Weeks of Supply as a planned valueAs part of defining the FWOScalculation, planners need to define thebehavior when sales in a plan areexhaustedForward Weeks of Supply calculates bycounting the number of weeks of plannedsales from the next week forward that thecurrent inventory represents. A statementneeds to be added to the calculation toaddress behavior when there are notenough forward weeks of sales available ina plan. Three methods are: Enable the calculation to wrap aroundthe beginning of the current plan’s timehorizon. This solution means planningfor the end of the current plan is basedon the beginning of the current plan,which is less than ideal for businessesexperiencing growth or retraction insales, or for plan horizons that are not afull year. Use the average weekly sales for theentire plan horizon. This solutionprovides a less than ideal FWOS valuefor the ending of the planning timehorizon, yet it is the easiest to achieve inmost planning solutions. Enable the calculation to look into afuture plan. This is complex behaviornot available in all planning solutions. Itis important to note that there will be nofuture plan available during the earliestpreseason planning.Requires planning to the week levelIn order to calculate FWOS, plans must becreated to the week level. Weekly planningis not always practical when creating highlevel top down plans.Lorem ipsum dolor sit amet, consecteturadipiscing elit. Sed ullamcorper tellusmagna, et congue orci. Suspendissepotenti. Vestibulum rutrum, enim achendrerit aliquam, nisi ipsum malesuadaerat, vel malesuada mauris diam quis erat.Sed consequat enim et lorem lacinia ingravida erat faucibus. Suspendisse potenti.In mattis sem non augue congue sed iaculisaugue adipiscing. Morbi posuere accumsanvestibulum. Sed sit amet erat tellus.Phasellus eget mi orci, sed convallis metus.Mauris id tortor tellus. Donec pharetraadipiscing purus, non ultrices ante feugiatid. Donec sit amet mattis nisl. Donec laciniaenim quis ante adipiscing elementumsagittis lorem posuere. Maecenas feugiatlibero a ipsum ullamcorper faucibus.Aliquam blandit elementum eros vitaepharetra. In hac habitasse platea dictumst.Nulla facilisi. Ut gravida elit sit amet erosvestibulum tempus. Mauris pharetra massavitae justo placerat vitae porttitor estimperdiet. Class aptent taciti sociosqu adCopyright The Parker Avery Group. All rights reserved.be selective.!
Inventory Planning Methods! !52. Weeks of SupplyWeeks of Supply (WOS) is an inventory measure calculated by dividing currentinventory by average sales. WOS helps to educate a planner to think of inventory interms of time. To illustrate:Figure 2: Weeks of Supply Sample CalculationWeek 1Week 2Week 3Week 4Week 5Month ASales1020256075190WOS Advantages of Weeks of Supply as a planned valueSimple calculationWeeks of Supply is an uncomplicated calculation, taking the inventory position for a period (i.e.,month) and dividing it by the average sales for the period. WOS requires no complex behaviorfor exhausted sales, since the measure looks at past trend versus future sales projection.Disadvantages of Weeks of Supply as a planned valueNot appropriate for detailed inventoryplanningLooks at past trend, not future forecastSince WOS uses average sales values tocalculate, it cannot be used for planningweekly inventory requirements. WOS canonly display values at an aggregated timelevel (i.e., month) and performs as ananalytics measure rather than a planningmeasure.WOS is not an appropriate measure tocalculate inventory needs. By using pastsales, WOS illustrates an inventoryposition based on where the business hasbeen, not where the future sales trend isgoing.www.ParkerAvery.combe selective.!
Inventory Planning Methods !63. Stock to Sales RatioStock to Sales Ratio (SSR) is ideal for planning appropriate inventory levels in plans tothe month level. Stock to Sales Ratio forecasts how much inventory is required toachieve the projected sales. SSR represents proportion of merchandise on hand at thebeginning of a period to the expected sales for that period. SSR is calculated by dividingstock at the beginning of the period by sales for the period.Advantages of Stock to Sales Ratio as a planned valueInventory is linked to sales valuesProvides an estimate of annual TurnStock to Sales Ratio is the most logical keyperformance measure to plan inventoryvalues in a month level plan. SSRcalculates inventory levels to meet plannedsales, resulting in the potential for overstocksituations to be diminished. VStock to Sales Ratio provides a planner witha guideline of expected annual inventoryturnover. vitae justo placerat vitae porttitorest imperdiet. Class aptent taciti sociosquad vitae justo placerat vitae porttitor estimperdiet. Class aptent taciti sociosqu adFigure 3: Stock to Sales Sample Estimate of TurnAverage Monthly SSREstimated Annual Turn433.53.5342.55Disadvantages of Stock to Sales Ratio as a planned valueOnly looks to one period of timeStock to Sales Ratio uses a single time value to calculate planned inventory and does notconsider the movement of a sales trend over time. The higher the level of time dimension beingplanned (i.e., quarter versus month) the more the sales and inventory fluctuations over time areflattened.Copyright The Parker Avery Group. All rights reserved.be selective.!
!Inventory Planning Methods !74. Sell Through PercentSell Through Percent (ST) allows a planner to understand the rate at which inventory isconsumed as compared to sales. While ST is a Key Performance Indicator, it is bestsuited for analysis rather planning. Sell Through Percent represents the ratio of salesto beginning period inventory. ST is calculated by dividing sales for a time period bystock at the beginning of the period.Advantages of Sell Through Percent as a planned valueLinks inventory consumption to salesSell Through Percent illustrates the relationship between sales and inventory, providingguidance to historical results and industry standards.Disadvantages of Sell Through Percent as a planned valueOnly looks to one period of timeSell Through Percent uses a single time value to calculate planned inventory and does notconsider the movement of a sales trend over time. The higher the level of time dimension beingplanned (i.e., quarter versus month) the sales and inventory fluctuations across time areflattened.www.ParkerAvery.combe selective.!
Inventory Planning Methods !85. TurnTurn, also known as turnover, refers to the number of times during a period that theaverage inventory is sold and replaced. Turn is a ratio of sales to inventory for along period of time, usually season or year. While Turn is the most commonly usedKey Performance Indicator, it is best suited for analysis rather planning, since inventoryfluctuations across time are flattened. Turn is typically calculated by dividing salesby the average inventory value.Advantages of Turn as a planned valueProvides a starting point to planned inventoryIn the absence of all other inventory key performance indicators, Turn can provide direction instarting the inventory planning process. Typically Turn Targets are developed early in theplanning process and can be used to roughly estimate inventory levels by month.Disadvantages of Turn as a planned valueUses average values, thus flattening trendsTurn is not an ideal measure from which to calculate planned inventory since Turn is calculatedfrom average inventory. Average inventory is a blend of beginning and ending inventory valuesacross time; using average inventory to calculate a specific time period’s beginning and endinginventory will result in seasonal fluctuations being flattened.Copyright The Parker Avery Group. All rights reserved.be selective.!
Inventory Planning Methods! !96. Basic StockThe Basic Stock method of inventory planning calculates a baseline level of inventorythat is the same for all months; inventory should not drop below the base level. Plannedsales for each month are added to the basic stock to derive the beginning of periodinventory value. Basic stock value is calculated as average inventory divided byaverage sales.Advantages of using Basic Stock method to plan inventorySupplies a very conservative method of inventory planningThe Basic Stock method of inventory planning is an option to consider for businesses with veryconsistent sales and inventory levels, meaning there is little seasonality or fluctuation in sales,as the baseline stock is the same for all months.Disadvantages of using Basic Stock method to plan inventoryUses average values, thus flatteningtrendsBetter suited for planning at the lowestlevel of detail (SKU)Basic Stock is not an appropriate methodfrom which to calculate planned inventoryfor seasonal business, emerging categories,or products with less predictable sellingpatterns. Basic Stock is calculated fromaverage inventory and average; usingaverage values to calculate a specific timeperiod’s inventory will result in seasonalfluctuations being flattened.Basic Stock method is suitable for planningindividual SKU’s and is similar to theprocess used by replenishmentapplications.www.ParkerAvery.comvitae justo placerat vitae porttitor estimperdiet. Class aptent taciti sociosqu advitae justo placerat vitae porttitor estimperdiet. Class aptent taciti sociosqu adbe selective.!
Inventory Planning Methods 10!Final WordBased on the advantages and disadvantages of the different methods of planninginventory as described, The Parker Avery Group recommends:Forward Weeks of Supply (FWOS) is the ideal method for calculating planned inventorylevels and should be used in all plans containing the week level of time. FWOS is thebest method of planning inventory to support the projected sales trend across time.FWOS is a retail industry best practice inventory planning measure. The Parker AveryGroup recommends enabling the FWOS calculation to wrap around the beginning of thecurrent plan’s time horizon when future sales are exhausted.Stock to Sales Ratio (SSR) is the most appropriate method for high level, top downinventory plans and other inventory plans that do not contain the week level of time.SSR forecasts the appropriate inventory level required to support projected sales. SSRis a leading retail industry planning measure.Copyright The Parker Avery Group. All rights reserved.be selective.!
Inventory Planning Methods! 11!The Parker Avery GroupThe Parker Avery Group is a boutique strategy and management consulting firm that is a trusted advisor toleading retail brands. We combine practical industry experience with proven consulting methodology to delivermeasurable results. We specialize in merchandising, supply chain and the omnichannel business model,integrating customer insights and the digital retail experience with strategy and operational improvements.Parker Avery helps clients develop enhanced business strategies, design improved
The Basic Stock method of inventory planning calculates a baseline level of inventory that is the same for all months; inventory should not drop below the base level. Planned sales for each month are added to the basic stock to derive the beginning of period inventory value. Basic stock value is calculated as average inventory divided by