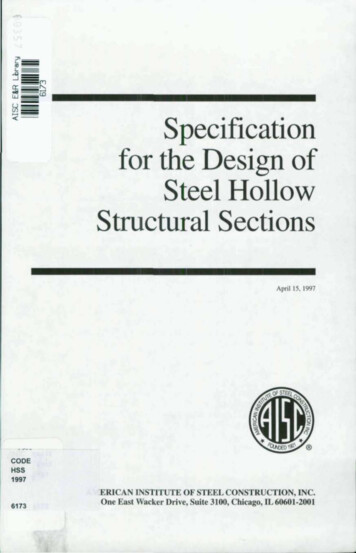
Transcription
Specificationfor the Design ofSteel HollowStructural SectionsApril 15. 1997CODEHSS19976173ERJ CAN INSTITUTE OF STEEL CONSTRUCTION, INC.One East Wacker Drive, Suite 3100, Chicago, IL6060 1·2001
"SPECIFICATION FOR THE DES IGN OF STEEL HOLLOW STRUCTURAL SECTIONSCopyright :I 1997byAmerican lnstitule of Sleel Construction, Inc.All righls resen'ed. This book or allY pari Ihereofmust not be reproduced in any form without thewritten pennission of the publisher.The information presented in tbis publication bas beenprepared in accordance with recognized engineeringprinciples and is for general information only. While itis believed to be accurate, this information should notbe used or relied upon for any specific applicationwitbout competent professional examination and verification of its accuracy, suitability, and applicability bya licensed professional engineer, designer, or architect.The publication of the material contained herein is notintended as a representation or warranty on the partof the American Institute of Steel Construction or ofany other person named herein, that this informationis suitable for any general or particular use or offreedom from infringement of any patent or patents. Anyone making use of this information assumes all liabilityarising from such usc.Caution must be exercised when relying upon otherspecifications and codes developed by other bodies andincorporated by reference herein since such materialmay be modified or amended from time to time subsequent to the printing of this edition. Tbe Institutebears no responsibility for such material other than torefer to it and incorporate it by reference at the time ofthe initial publication of this edition.Printed in the United States of AmericaAMEJUCAN 1'IS11Tt1TE Of STEELCONSTRL:C"nON
SPECIFlCAnON FOR THE DESIGN OF STEEL HOLLOW STRUCTURAL SECTIONSIII\.V10 Table of ContentsSymbolsPreface. vviiSpecification for the Design ofSteel Hollow Stru ctural SectionsI. I. Scope . . . . . . . .1.2. Malerial . . . . . . . . . . .I.Struclural Steel . . . .2.DesIgn Wall Thickness1.3. Loads and Load CombinalionsI1I222.1. Effective et Area for Tension Members.2.2. Local Buck.hng . . . . . . . . .I.ClassIfication. . . . . . .DesIgn by Plastic Analysis . . .2.3.DeSIgn in Seismic Applications2.3. Limiting Slenderness Ratios2444553. 1.Design for Tension . . . . . . . . . .54. 1.Effective Length and Slenderness LimitationsI.Effective Length . . . . .2.Design by PlastIc Analysis4.2. Design for Compression55665. 1. Design for Flexure5.2. Design for Shear .786.9DesIgn for Torsion7. 1. DeSIgn for Combined Flexure and Axial Force7.2. Design for Combined Tomon, Shear, Flexure, andlor Axial Force9108.Concentrated Forces on HSS . . . . . . . . . . . . .8. 1. Concentrated Force DIstributed Transversely . . . .8.2. Concentrated Force Distnbuted Longitudmally at theCenter of the HSS Face . . . . . . . . . . . . . . . .8.3. Concentrated Axial Force on Ihe End of a Rectangular HSSWIth a Cap Plate . . . . . . . . . . . .IIII9.1 . General Provisions for Connections and Fasteners .I.Through Bolts . .2.Special Connectors .3.TenSIOn Connectors .121213131313
SPECIFICATION FOR THE DESIGN OF STEEL HOu.oW STRUCTURAL SECTIONSIY9.2. Welds . . . . . . . . . . . . . .9.3. Other Connection RequirementsI.Shear Rupture Strength .2.TenSIOn Rupture Strength3.PunchJng Shear Rupture Strength9.4.HSS- to-HSS Truss ConnectionsDefinItions of ParametersI.2.Criteria for Round HSS . .2a. Limits of Applicability .2b. Branches with Axial Loads2c. Branches with Flexure . . .2d. Branches with Combined Axial Loads and Flexure .3.Criteria for Rectangular HSS . . . . . . . . . . . . . . . .3a. Limits of Applicability . . . . . . . . . . . . . . .3b. Branches with Axial Loads in T-, Y- and Cross-connections3c. Branches with Axial Loads in Gapped K-connections3d. Branches with Bendmg . . . .13141415151515161617171818181919202110.General Requirements for HSS Fabncauon224.Eccentric Connections . .Commentary1.1. Scope .1.2. Material1.3. Loads and Load Combinations2325272.1. Effective Net Area for Tension Members .2.2 Local Buckling . .29293. 1.Design for Tension304.1.4.2.Effecllve Length and Slenderness LimitationsDesign for Compression30315.1. DeSign for Aexure5.2. Design for Shear .366.3735DeSign for TorsIOn7.1 . Design for Combined Aexure and Axial Force7.2. DeSign for Combined Torsion, Shear, Aexure, andlor Axial Force39408.Concentrated Forces on HSS . . . . . . . . . . .419.1.9.2.9.3.9.4.General Provisions for Connections and Fasteners.Welds . . . . . . . . . . . . . .Other Connection Requirements . . . .HSS-to-HSS Truss Connections . . . .4343444510.General Requirements for HSS Fabrication48References50AMFJUCAN lNSlTTUTEOf STEELCONSTRUCTlON
7 SPECIFICATION FOR THE DESIGN OF STEEL HOLLOW STRUCfURAL SECTIONSv,'V11.0SymbolsAA,area used to calculate A,gross area of cross-sectionA, effecllve net area for tension memberAll net areaA. web areaoverall width of rectangular HSS88 . overall width of rectangular HSS branch member in a truss connectionC HSS torsional constanlDoutside diameter of round HSSD. outside diameter of round HSS branch member in a truss connectionEmodulus of elasticityF;r critical stress for column bu klingcrilical stress for local buckhngen rica) stress for torsionF:tnominal SlfC S for rectangular HSS shear resistanceF. mintmum specified tensile mength of the HSSF'Kr critical !.hear stressF. nummum specified yield stress of the HSSF', \ minimum specified yield strength of plate or connecting clement that is weldedto an HSSF. nunimum specified yield strength of HSS branch member in a truss connectionsH overall height of rectangular HSSH. overall height of rectangular HSS branch member in a truss connectionKcompression member effective length factorLconneClion lengthlength of weld4 unbraced length4 effeClive weld lengthL,. maxmlUm unbraced length for plastic moment M, in plastiC analysisL, maximum unbraced length for yield moment M,M. nom mal /lexural strengthM" pla lic moment of sectlonM , yield mOment of sectionM, required /lexural strenglhM" resultant required /lex ural strength for round HSSM, smaller moment at end of an unbraced length in plastic analysisM , larger moment at end of an un braced length in plastic analysisNbeanng length of concentrated load along length of HSSP,.nominal axial strengthPo reqUired aXial strengthp. addillonal axial load for the moment in a rectangular HSS branchP, axial Yield loadQ effecllve area factorQ, conneclton resistance reduction factor for compresSion in HSS (Section 8.1).parameter u",d for tru" connections as defined 10 Secllon 9.4
v,SPECIFICATION FOR THE DESIGN OF STEEL HOLLOW STRUCTURAL SECTIONSQ.parameler used for truss connecUons as defined in Section 9.4parameler used for truss connecUons as defined in Secllon 9.4reduclion faclor for wind forces on exposed HSSnominal strength of HSS and conneclions 10 HSSelastic seclion modulusSS !! effecllve elaslic section modulus for thin -walled rectangular HSST. nominal torsional strengthT. reqUIred torsional strengthU shear lag faclOr, parameter used for truss connections as defined in SectIOn 9.4V, nominal shear strengthV. required shear strengthZplastic section modulusalength of essentially constant shear In a beambnat WIdth of rectangular HSS nange or SIde, whICh is permitted to be taken as8 - 31b,widlh of plate or connecting elemenl that IS welded to an HSSQpRfR,b,. parameter used for truss conneclions as defined in Secuon 9.4b,. parameter used for truss conneCUons as defined in SectIon 9.4cconstant for bending in rectangular HSS branches of tru conneCllonsdebolt dl3metereccentricity in K-connectionsfstressg gap between branch members In a gapped K-connecuon"nat WIdth of rectangular HSS web or SIde, which is penllltted to be taken asH - 31kdistance from point of application of concentrated force 10 crilical section of HSSImember lengthrradIUS of gyrauonr, radIUS of gyralion aboul the y-axisdesign HSS wall thickness as given in Section 1.2I,thickness of plate or connecling element thai is welded 10 an HSSI.thickness of branch member in an HSS truss connection!! plale thlckne;s (Secuon 8.3.3)xeccentricity for shear lagbranch angle with respect to chord as illustrated in FIgure C9.4- 1aparameter used for truss connections as defined in Sectton 9.4 parameter used for truss connecUons as defined in Secllon 9.4 ". parameler used for truss connecUons as defined In Secllon 9.4 . para meIer used for truss connectIOns as defined In SectIon 9.4 . parameter used for truss connecllons", defined in Secllon 9.4yparameter used for truss conneClJons a defined in SeellO" 9.4cprCMstance factorl]parameter used for truss connections as defined in Secllon 9.4Awall slendernessconstant for type of load in round HSS truss connectionsA. column slendernessA, maXImum wall slenderness for compact sectionA,. maximum wall slenderness for non-compact seclionangle bel ween branch and chord parameter used for truss conneCUons as defined III Secuon 9 .4aaA"'If.RICAN INSTTTt'TE. Of STUl. CO STRl'cnos
SPECIFICATION FOR THE DESIGN OF STEEL HOLLOW STRUCTURAL SECTIONSviiPREFACEThe AISC Load and Resistance Factor Design (LRFD) Specification/or StructuralSteel Buildings is intended to cover the common design criteria in routine officepractice. Accordingly, it is not feasible to also cover the many special and uniqueproblems encountered within the full range of structural design practice. This AISCSpecification/or the Design o/Steel Hollow Structural Sections is a separate documentthat addresses one such topic: the design and construction of building systems thatutilize steel hollow structural sections (HSS). A list of Symbols and a non-mandatoryCommentary with background information are provided.The AlSC Committee on Specifications, Task Committee ll8-Structural Tubing isresponsible for its ongoing development. Additionally, the AlSC Committee onSpecificatjon has enhanced these provisions through careful scrutiny. discussion,suggestion for improvements, and endorsement.By the AISC Committee on Specifications, Task Committee II S-Structural Tubing,D. R. Sherman, ChairmanR. e. KaehlerL. A. Kloiber1. A. PackerF. 1. Palmer1. M. Rieles1. A. Yurae. 1. Carter, Secretary
'HISPECIACATION FOR THE DESIGN OF STEEL HOLLOW STRUCTURAL SECfIONSAMERICAN 1NS1TIVfE OF Sna. CONSTRUCT1ON
oSPECIFICATION FOR THE DESIGN OF STEEL HOLWW STRUCTURAL SECTIONSovJcr,.Specificationfor the Design ofSteel HollowStructural SectionsApnl 15. 19971.1. SCOPEThis Specification is intended for the design of round and rectangular hollowstructural sections (HSS) that are used as s!ructural members in buildings andthe design of connections to HSS. HSS include: (I) prismatic structural shapesand (2) products of a pipe or tubing mill that meet the geometric tolerances,tensile requirements and chemical requirements of a standard specification.Rectangular HSS include square and rectangular cross-sections Ihat haverounded corners within the tolerances of an appropriate product specification.Only unstiffened non-composite HSS in non -fatigue applications are consideredin this Specification.This Specification is a supplement to the AISC Load and Resistance FactorDesign Specification for Structural Steel Bui/dings (AISC, 1993), hereinafterreferred to as the LRFD Specification. In some cases, criteria taken from theLRFD Specification have been modified to appear in non-dimensional form andto apply directly to rectangular HSS, which have two webs. For situations thatare not covered in thi s Specification, the criteria in the LRFD Specification shallapply. [n seismic applications, HSS shall also be designed to meet the requirements of the AISC Seismic Provisions for Structural Steel Buildings (AISC,1997).1.2.MATERIAL1.Structural SteelHSS malerial that meets the requirements in one of the following ASTMspeCIfications is approved for use under this Specification:ASTM A53-96 Grade B, "Standard Specification for Pipe, Steel,Black and Hot-Dipped, Zinc-Coated, Welded and Seamless"ASTM A500-93, "Standard Specification for Cold-Formed WeldedAMERICAN INSTTTVrEOf' SllXL. CONSTRucnON
2SPECIFICATION FOR THE DESIGN OF STEEL HOLLOW STRUCTURAL SECTIONSand Seamless Carbon Steel Struclural Tubing in Rounds andShapes"ASTM A501 -93, "Standard Specification for HOI-Formed Weldedand Seamless Carbon Sleel Structural Tubing"ASTM A618-95, "Standard Specificalion for HOI-Formed Weldedand Seamless High-Strength Low-Alloy Structural Tubing"ASTM A847-93, "Slandard Specification for Cold-Formed Weldedand Seamless High Strenglh, Low Alloy Structural Tubing withImproved Almospheric Corrosion Resistance"Cenified mill lesl reports or certified reports of tesls made by thefabricalor or a qualified lesting laboralory thai meet the requirements inASTM A370 and the governing specification shall constilute sufficienlevidence of conformily with one of the above ASTM standards. Ifreque led, the fabricalor shall provide an affidavit stating that thestructural steel furnished meets the requirements of the grade specified.2.Design Wall ThicknessThe design wall thickness I shall be used in calcu lalions involving theHSS wall thickness. When the design wall thickness is not known, it ispermilled 10 be taken as 0.93 times the nominal wall thickness.1.3. LOADS AND LOAD COMBlNATIO SIn the absence of other applicable building code provisions, the load combinations of LRFD Specification Section A4 shall apply.If permilled by the applicable building code, wind forces on the projected areasof exposed HSS are permitted to be reduced by the factor R, from the forces onframeworks with similar configurations but using sections or shapes with natelements. R,shall be taken as follows:(a) For round HSS , R, 2/3.(b) For rectangular HSS with outside comer radii that are greater than or equalto 0.05 times the widlh 8 and wind force acting on the short side (8 ),R, 0.4 0.68 IH!. 213, where H is the depth of the HSS.(c) For rectangular HSS under other conditions, R, 1.0.2.1. EFFECTIVE NET AREA FOR TENSION MEMBERSThe effective nel area A. for lension members shall be delermined as follows:A. AU(2.1-1)(a) For a welded conneclion that is continuous around the perimeter, A A"where A, is the gross area and U I .(b) For connections WIth concentric gusset plates and slolled HSS, A A.where the net area A. al the end of the gussel plate is the gross area minusthe product of the thickness and 100al width of material that is removed toform the slots, andU l -rxIL)!.0.9AMERICAN INsmvrE OF STEEL CONSTRUCTION(2.1-2)
,, 'SPECIFICATION FOR THE DESIGN OF STEEL HOLLOW STRUCTURAL SECTIONS3Table 2.2-1Limiting Wall Slenderness forCompression Elements IElementround HSSfor axial compressionfor flexurefor plastic analysisA lml a" Slende: essAfa11n.a.0. 114 1 Fy0.309 1 Fy0.0714 1 Fy0.0448 1 Fy0 .3 .-I-Mrectangular HSS wallfor uniform compressionor1.12" 1 Fyhit1.40" 1 Fyfor plastic analysis0.939V 1 Fyrectangular HSS wall as a webin flexural compressionhit3.76" 1 Fyrectangular HSS wall as a webin combined flexure and axialcompressionhit[b]5.7oV 1 Fy5.7 1 Fy I 0.75Pu'bPy(8j DJ! mustbe tess than or equal to O.448E / F"Pu /toP,S 0.t25(b For.2.75Pu)3.76 ,fE / F, ( t ---".-,lor Pu /toP, 0.1251.12 E / F,(2.33 -Pu) 1.49,fE / F,toP,.:.---In the above equatIon, i is the perpendicular distance from the weld to thecentroid of the cross-sectional area that is tributary to the weld.For round HSS with a single concentric gusset plate-x D(2.1-3)J[For reclangular HSS with a single concentric gusset platexB' 2BH4(B H)(2. 1-4)(c) For connections with rectangular HSS and a pair of side gusset plates,A A" where A, is the gross area and U shall be calculated using Equation2.1-2 withAMERICAN INSTTTUJ'EOP STm. CON5nllCTlON
4SPECIRCAnON FOR THE OESIGN OF STEEL HOu.oW STRUCTURAL SECTIONSx4(B H)(2.1-5)whereL length of the connection 10 the directoon of loadmgD outside diameter of round HSSB overall width of rectangular HSSH overall heighl of reclangular HSSLarger values of U are permilled to be used when justified by lesls or ralionalcriteria. For other end-connecllon configurations. U shall be delermined by testsor rational criteria.2.2LOCAL BUCKLINGI.Classification of Steel SectionsHSS are classified for local buckling of the wall in compression as compact,non-compact. or slender-element croSS-sectiOns accordmg to the limiting waJlslenderness rallOS A,. and A., 10 Table 2.2-1. For an HSS to quahfy as compacl,the wall slenderness raUo A must be less than or equal to A,. If A exceeds A,. butis less than or equal to Ao Ihe HSS is non-compact. If A exceeds Ao the HSS isa slender-clement cross-section. The wall slenderness ratio shall be calculatedas follows:(a) For round HSS. A DII. where D IS the outside diameter and I is the wallthlckne . This Specificauon IS apphcable only to round HSS with A lessthan or equal to 0.448 11;. where is the modulus of elastiCity and F, is theminimum specified yield Mress. (b) For nanges of reclangular HSS. A bll, where b is Ihe clear dislancebetween webs less the inside comer radius at each web and I is the wallthickness. If the comer radiUS IS not known. b IS pemlllled 10 be taken asthe overall nange width B mlOus three Urnes the wall thickness I.(c) For webs of rectangular HSS, A "II. where" IS the clear distance betweenflanges less the inside comer radius at each flange and I is Ihe walllhickness.If the comer radius is nol known, h is permllled 10 be laken as Ihe overallweb depth H minus three limes the wallihickness I.2.Design by Plastic AnalysisDesign by plastic analysis IS permitted when A IS less than or equalplaslic analysis as defined in Table 2.2- 1.3.10A,.forDesign in eismic ApplicationsIn seismic apphcations, A shall also meetlhe requiremenls in Ihe AISC SeismicProvisions/or Slruclural Sleel Buildings (AISC. 1997).23. LIMITING SLENDERNESS RATIOSFor compression members, the slenderness ralio Kllr preferably should nolexceed 200.For tension members, the slenderness ralio Ilr preferably should not exceed 300.
SPECIFICATION FOR THE OESIGN OF STEEL HOLLOW STRUCTURAL SECTIONS5Members that are primanly tension members but that are subject to somecompression under other load conditions need not satisfy the compressionslenderness IIm1l.For bracing members In seIsmic applications. IIr shall meet the requirements inAISC SeismIC Prol'isions!or Structural Steel Buildmgs.3.1. DESIGFOR TENSIONThe deSIgn strength of tension members ,P" shall be the lower value obtainedaccording to the limit states of yielding in the gross section and fracture in thenet section.(a) For yielding on the gross area: , 0.9I! f;A,(3.1-1)(b) For rupture on the net effective area: , 0.75P,. ;;;: F.A .(3.1-2)whereAr effective net areaA, gross area of HSSF, specified minimum yield strengthF,. specified mjnimum tensile strengthP" nominal axial strength4.1.EFFECTIVE LE GTH AND SLENDERNESS LIMITATIONSI.Effective LengthThe effective length factor K for compression members shall be taken as followsor as determined by rational analysis:(a) In trusses that are made with HSS branch (web) members that are weldedaround their full penmeter to continuous HSS chord members, the effectivelength factor K used to modify the length between panel points for in-planebuck.IIng, or between locations of lateral bracing for out-of-plane budding,shall be not less than :K 0.75 for branch membersK 0.9 for chord members(b) In trusses that are made with HSS branch members that do not meet therequirements in Section 4.1.1 (a) or with non-HSS branch members connected to continuous HSS chord members. the effective length factor K usedto modIfy the length between panel points for in-plane buck.ling shall be notless than:K 1.0 for branch membersK 0.9 for chord membersAMERICAN lNSlTTUTE OF STEEl. CONSTRUC1l0N
6SPECIFICATION FOR THE DESIGN OF STEEL HOLLOW STRUCTURAL SECTIONS(c) In frames for which lateral stabilily is provided by diagonal bracing, shearwalls or equivalent means, K shall be taken as unily, unless a lesser valuecan be justified by rational analysis.(d) In frames for which lateral stabilily is dependanl upon the flexural sliffnessof ngidly connecled beams and columns, K shall be detennined by rationalanalysis.2.Design by Plastic AnalysisDesign by plastic analysis is permitted if the column slenderness parameter A,.is less than or equallo I .SK and the axial force in columns of unbraced framesdue 10 factored gravity loads plus faclored laleral loads does nOI exceed 1 , times0.75F,A, .4.2.DESIGN FOR COMPRESSIONThe design strength for flexural buckling of compresSIon members l J': shall bedelennined as follows : 1 , 0.85P,. :;:: Fer A,(4.2-1)F" shall be detennined as follows:(a) For].,.JQ S 1.5F" -- Q(0.658 Q )F,(4.2-2)(b) For A,.JQ 1.5F.t', [0.877]A; F.,(4.2-3)where(4.2-4)Q shall be determined as follows :(a) For A S A, in Section 2.2, Q I(b) For A A,. in Section 2.2, for round HSS with A 0.448E/ Q 0.0379E lF,(D/I)3(4.2-5)For rectangular HSS.Qeffecti ve areaA,(4.2-6)where the effective area is equal to the summation of the effective areas ofthe sides usingAMElucAf'i INS1TTUTE OF STEFl. CONSTRUC11ON
SPECIFI ATION FOR THE DESIGN OF STEEL HOLLOW STRUCTURAL SECTIONSb 191,.- [1 0.381 ] S.b''V7(bll) '1 7I7(4.2·7)with f P. IA,.5.1.DESIGN FOR FLEXUREThe design flexural strength I"M, shall be delermined as follows: I. 0.9 a) For round HSS, for A A" in Seclion 2.2,M. Mp F,Z(5.1-1 )M, (0.0207K. I)F.SDII F. ,(5.1-2)for A,. d. s. A,for A,. A S. 0.448 IF,M 0.330 S,DII(b) For rectangular HSS, for A (5.1-3)A,. in Section 2.2,M. Mp F.Z(5.14)for A,. A s. A,(5.1-5)whereM, F,Sfor A A,.M, F,S f{(5.1-6)where S., IS the effective section modulus with the effeclive width of thecompression flange taken asO. 'I- fE]'IfE[IF. (bll)F; S.bb, 1.911-38 1(5.1-7)L, is not limited for HSS strUctures designed by elastic analysis. Design byplastic analysis is pcnniued for compact round HSS wilh Aless than or equal 100.0448 11; and for reclangular HSS with A less than or equal 10 A" in Section2.2. For reclangular HSS bent aboul the major axis,lhe lalerally unbraced length4 of Ihe compression flange adjacenl lo plastic hinge local ions thai are associaled wilh the failure mechanism shall nOI exceed L,. whereAMERICAN lNSTTTUTE OF STEa. CO/'olSTllUCTlON
SPECIRCATION FOR THE DESIGN OF STEEL HOLLOW STRUCTURAL SECTIONS85,000 3,OOO(M, 1M, )F,r, 3,OOOr.Jr"(5.1-8)andF., specified mjOlmum yield stressM, smaller momenl at the end of the un braced lengthM, larger moment at the end of the un braced lengthr, radius of gyration about the minor axisM\IM2 is positive when moments cause reverse curvature and negative for single curvatureFor seismic applications, refer to A15C Seismic Provisions for Strllctural SteelBlli/dings (AI5C, 1997).5.2.DESIGN FOR SHEARThe design shear strength of unstiffened H55follows:41. V,shall be detemuned as41. 0.9(a) For round H55 witha3.2( 1 F,)'D(Dltt'- (5 .2- 1)and A. A.,. in Table 2.2- 1,V, 0.3F,A,(5.2-2)V" F"A .(5.2-3)A. 2Ht(5.2-4)(b) For rectangular H55,whereF. shall be detemUned as follows :(i) For hitS 2.45-4 I F,F. 0.6F,(5.2-5)(ii) For 2.45-4 I F, hit 3.07-4 IF,F. 0.6F, (2.45-4 IF,) I (h I t)(5.2-6)(iii) For 3.07-4 I F; hit 260F. 0.458lt' I (h It)'6.DESIGN FOR TORSIOThe des'gn torsional strength q,TT, shall be detemUned as follows :AMllUCAN lNSTmII'E OF STEfl. CONSTRUCTION(5.2-7)
SPEC IFICAT ION FOR THE DESIGN OF STEEL HOLLOW STRUCTURAL SECTIONS9 T 0.9T. F;,C(6- 1)where C IS the HSS tOrsIonal constantF;, shall be dctennined as follows:(a) For round HSS. F;, shall be the larger of1.23 LI Dd 0.6 an (DII)JIl(DII)'"(6-2)bUI shall nOI exceed 0.61';.(b) For rectangular HSS. for II I I 5 2.45 I I';Fa 0.61';(6-3)for 2.45 I I'; h I I 5 3.07 IF,F" 0.6F,(2 .45 1F, )/(1111)(6-4)for3.07 IF, h11526OF"7.1. 0.4581 ' I (h I I)'(6-5)DESIGN FOR COMBINED FLEXURE AND AXJAL FORCEThe inlcmclion of flexure and axial force shall be limiled by Equalions 7.1-1and 7.1-2.(a) For P. I P. 0.2 ( M.x M" )5 1.0(7.1-1)P. (-M.xM")-- - - 5 I .0(7.1-2) P.9 oM oM"(b) For P. I P' 0.22 P. oMu oM.wherep"P,. required axial tensile or compressive strength nominal tensile or compressive strength determined in accordance withSeclions 3.1 or 4.2M. required flexural strength detennined in accordance with LRFD Specificallon Section C 1M,. nominal flexural strength detennined in accordance with Section 5.1x subscript relating symbol to strong axis bendingy subscript relating symbol to weak axis bending , from Section 3.1 for lens ion 0.85 for compression . 0.90AMF.RICAN LNsrrn.rre OF STEEL CONSTROCllON
10SPECIFICATION FOR TIlE DESIGN OF STEEL HOLLOW STRUCfURAL SECTIONSFor biaxial nexure of round HSS that are laterally unbraced along their lengthand with end conditions such that the effective length factor K is the same forany direction of bending, the design is permitted to be based upon a singleresultant moment M.,. where:(7.1-3)Alternatively, use of the provisions in LRFD Specification Appendix H.3b ispermitted.7.2.DESIGN FOR COMBINED TORSION, SHEAR, FLEXURE,AND/OR AXIAL FORCEWhen the required torsional strength IS significant, the interaction of torsion,shear, nexure, andlor axial force shall be limited by Equation 7.2-1 .(7.2-1)In the above equation,p. required axial tensile or compressive strengthp. nominal tensile or compressive strength detemuned tn accordance withSections 3. I or 4.2M. required nexural strength determined in accordance with LRFD Speci-fication Section C IM, lesser of F, Sand M, determined in accordance with Section 5. IS elastic section modulusV. required shear strength at the section corresponding to M.V"7;.7;, nominal shear slrength dClcnnined in accordance with Section 5.2 required torsional strength nominal torsional strength determined in accordance with Section 6 " from Section 3. I for tension0.85 for compression " " ,, 8.0.90CONCENTRATED FORCES 0HSSThe design strength ,R, at locations of concentrated forces on unstiffened HSSshall be determined from the applicable criteria in Sections 8. I through 8.3.8.1.Concentrated Force Distributed TransverselyWhen a concentrated force is distributed transversely to the axis of the HSS, thedesign strength ,R, shall be determined as follows:(a) For round H5S,, R1.05F,r, - I - 0.8Ib I ID QfAMfR.lCAN IJIIS'TTT1J1"E Of Sna C ONSllUX"nON(8.1- 1)
'",SPEClFICATION FOR THE DESIGN OF STEEL HOLLOW STRUCfURAL SECfIONSII) ,0"0',whereb, Ihe widlh of the loadQ, I for lension in the HSS I - 0.3J1I; - 0.3iflF,)'" I for compression in Ihe HSSf the magnitude of the maximum compression stress in the HSS due toaxial force and bending at the location of the concentrated force(b) For rectangular HSS,4j 1.0101';/R. (811) b l " 1';1 Ilb l(8.1-2)whereb l the width of the loaded platethe thickness of the loaded plate1';1 minimum specified yield strength of the loaded plateII When the force is distributed across the full width of the rectangular HSS, thelimit state of local web yielding shall be checked for both tensile and compressive forces and the limit state of web crippling shall be checked for compressiveforces. For local web yielding,4j 1.0R. 21';1(5k N)(8. I -3)For web crippling,4j 0.75R. 1.6t'[1 3NIh]VEF,(8.1-4)wherek outside comer radius of the HSS, which if not known is pemlitted to betaken as 1.51N bearing length of the load along the length of the HSSII nat width of side wall of the HSS as defined in Section 2.2. IWhen the force is di stributed across a width of the rectangular HSS that is greaterthan 0.858 but less than 8 - 21, the design strength shall not exceed 4j R., where4j 1.0R. 0.61'; 1(211 2b,,)(8. I-5)where b" I Ob, 1(81 t) " b ,When compressive forces coincide on opposite faces of the reclangular HSS,the limit state of compression buckling of the webs shall be checked and thedesign st rength shall not exceed 4j R., whereAMERICAN I NSTIT\ITE OF STEEL CONSTRUC110N
12SPECIRCATION FOR THE DESIGN OF STEEL HOLLOW STRUCTURAL SECTIONS 0.90R.8.2.48rlEif(8.1-6)hConcentrated Force Distributed Longitudinally at the Centerof the HSS FaceWhen a concentrated force is distributed longitudinally along the axis of theHSS at the center of the HSS face, the design strength R. shall be detemlinedas follows :(a) For round HSS , 1.0R. 5F, 1'( I 0.25N 1 D)Q,(8.2-1 )whereN bearing length of the load along the length of the HSSQj I for tension in the HSS I - 0.3f1F, - 0.3([1F,)'" I for compression in the HSSf the magnitude of the maximum compression stress in the HSS dueto axial force and bending at the location of the concentrated force(b) For rectangular HSS, 1.0R.F,rI - I, 1 B[2N 4,f 1 -1\I BlQ,BJ(8.2-2)where 1\ is the thickness of the loaded plate.8.3.Concentrated Axial Force on the End of a Rectangular HSSwith a Ca p PlateWhen a concentrated force acts on the end of an HSS with a cap plate and alongthe axis of the HSS, the design strength R. ; hall be determlDed for each loadedwall a follows. The limit state of local wall yielding shall be checked for bothtensile and compressive forces and the limit state of wa ll crippling shall bechecked for compressive forces. For local wa ll yieldi ng, 1.0R. (51\ NlF,I" BF,I(8.3-1)For wa ll crippling, 0.75(8.3-2)whereAMERICAN INS11T\1TEOf SlnL CO STRurnON
SPECIFICATION FOR TIl E DESIGN OF STEEL HOLLOW STRUcruRAL SECTIONS13I, thicleness of cap plateN beanng length of the load across the width of the HSS9.1.GE ERAL PROVISIO S FOR CONNECfIONS A 0 FASTENERSThe provisIons of LRFD SpecIfication Section J 1.1 through J 1.11 and theprovIsions for bolls and threaded pans in LRFD SpecificatIon Section J3.1through J3 .11 shall apply with the following additions and modifications.1.Through BoltsWhen connections are made usin
SPECIFICATION FOR THE DESIGN OF STEEL HOLWW STRUCTURAL SECTIONS 1.1. SCOPE Specification for the Design of Steel Hollow Structural Sections Apnl 15. 1997 This Specification is intended for the design of round and rectangular hollow structural sections (HSS) that are used as s!ructural members in buildin