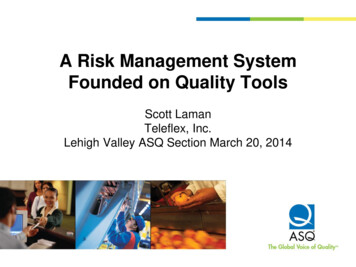
Transcription
A Risk Management SystemFounded on Quality ToolsScott LamanTeleflex, Inc.Lehigh Valley ASQ Section March 20, 2014
Teleflex Corporate HQ – Limerick, PA 12,000 global employees In 130 countries Class I, II and III devices Businesses: Vascular, Respiratory,Anesthesia, Urology, Dialysis, Surgical,Cardiac
Typical Medical Kit
Presentation Objectives Summarize quality tools used in riskmanagement system development– Provide ideas for how to approach developingquality system processes Describe and link types of product riskanalyses– Provide knowledge of typical risk analyses Demonstrate the relationship between riskmanagement and statistics
Example of Risk Management What is the highest-riskanimal in Pennsylvania? How do you evaluaterisk?
Example of Risk ManagementAnimalSeverity RatingProbability Rating
Medical Risk Management Objectives Safe and effective products–Minimize the patient/user risks Compliance with internal and externalstandards–Minimize the Regulatory risk Stay in business so products remainavailable–Minimize the business risk
ISO 14971 Risk ManagementRisk Management is the systematic applicationof management policies, procedures andpracticesto the tasks ofanalyzing, evaluating and controlling(mitigating and monitoring) risk
ISO 14971 Risk Management ProcessRisk analysis Risk Analysis Risk Assessment· Intended use andidentification ofcharacteristics related tothe safety of the medicaldevice· Hazard identification· Risk estimationRiskAssessmentRisk evaluation· Risk acceptability decisions Risk Evaluation Risk ControlRisk control······Option analysisImplementationResidual risk evaluationRisk/benefit analysisNew risks from controlsRisk control completenessEvaluation of overall riskacceptabilityRisk management reportProduction and Postproduction informationRiskManagement
Risk Management System Development Process characterization Prioritization Procedures Improvement Quality system connections
Process Characterization - SIPOCSuppliersInputsRegulatoryAgenciesGuidances andRegulationsProduct UsersManagement withExecutiveResponsibilityStep 1:Plan RiskManagementActivitiesProcessOutputsRisk ManagementFileFeedback, complaints,data for reliabilityanalysisProductsResources, toplevel vision, keydecisionsStep 2:Publish the RiskManagement PlanStep 3:Conduct sCompliancePatients, physicians,nursesHigh quality, safety,ease of use, clearinstructionsManagement siness successStep 4:Publish the RiskManagementReportStep 5:Maintain theRiskManagement File
Prioritization: Importance/UrgencyHighUrgencyLowLowHighImportance
Procedures – Seeing the Same Way
Procedures: Consensus ChartYesDo We Want toStandardize?NoNoYesIs There Consensus?
Consensus Chart StrategiesYesHold Meetings toWork dize?ConsensusDo We Want toStandardize?NoLet There BeVariationEveryone AgreesAnywayNoYesIs There Consensus?
ImprovementPLANACTDOSTUDY
Improvement ExamplesImprovement OpportunityCorrective ActionToo many procedures, overlapReduce # of procedures – eliminateredundancyProcedures not usedMake documents obsoleteInconsistent usageProceduralize important issuesPlan/Report not alignedCreate templatesPoor documentation practicesReinforce and trainInadequate training recordsUpdate records
Connections – Within RM SystemQuality azardsAnalysisDesign FailureMode andEffectsAnalysis(DFMEA )Process FailureMode andEffectsAnalysis(PFMEA)UseabilityFailure Modeand EffectsAnalysis(UFMEA )HazardsAnalysisTemplateDesign FailureMode andEffectsAnalysisTemplateProcess FailureMode andEffectsAnalysisTemplateUsabilityFailure Modeand EffectsAnalysisTemplateFault TreeAnalysisRiskManagementPlan veillanceRisk tionHealth HazardEvaluationWorkInstructionComplaint RiskEvaluationTemplateRiskAssessmentFormHealth HazardEvaluationTemplate
Risk Management Process FlowRiskManagementPlanningNew ProductDevelopmentor skManagementReportPost-marketSurveillance
Design Control Process FlowDesignConceptDesign onProductReleaseDesignChange
Add Risk Management Risk ManagementPlanDesignConceptDesign EARisk HazardsAnalysisDesignChangePost MarketSurveillance
Risk Analysis Linkages FTA/Hazards Analysis: Useresults from clinician interviews,field data, engineering UFMEA/DFMEA: Use resultsfrom hazards analysis PFMEA: Use results fromhazards analysis and DFMEA
The Tree of Potential HarmPatient HarmHazardousSituationReasonable ,ForeseeableMisuseProduct FailureDesignFailureProcessFailure
Hazards Analysis Top-down, most general safety driven, focused on patient and user risk Considers potential product failure and productmisuse Identify potential hazards, estimate severity ofharm and probability of occurrence, evaluaterisks, identify controls, recommend risk reductionactions
Hazards Analysis Severity ScaleEffectCriteriaPerson / Operator / BystanderRankCriticalDeath caused directly by the hazardous situation where the device was acontributing factor5SeriousSerious injury, defined as an injury that is life-threatening or resulting inpermanent impairment of a body function or permanent damage to bodystructure4Serious injury that is not classified as 4, but is defined as requiringmedical intervention to preclude permanent impairment of a body functionor permanent damage to a body structure (temporary)3Non-serious injury not involving medical or other third-party intervention,or moderate discomfort/stress requiring medical intervention2ModerateLimitedNegligible No injury; cosmetic or nuisance only1
Hazards Analysis Probability ScaleCategoryProbability ofOccurrenceRankFrequent 1 in 105Probable 1 in 100 1 in 104Occasional 1 in 1000 1 in 1003Remote 1 in 10,000 1 in 10002Improbable 1 in 10,0001
Fault Tree Analysis Supplemental tool to HA or FMEAs Top-down approach, single failure mode focus Analysis diagram utilizing AND and OR gates(similar to a reliability diagram) Often used on highest risk failure modes from anFMEA
Example Fault Tree AnalysisCatheter breaksduring removalOR2.5%0.7%1.5%Excessive forceapplied tocatheterWeak spot incatheter0.1%Catheterdamaged by user0.2%Catheterdamaged inpackageORProduction qualityproblemImproperhandling nsfor use notclearQA sampletoo smallIncorrectcomponentplacementCatheter stuckin patientImproperinsertionInstructionsfor use notclearANDAND15%Doctor nottrainedExtrusiontemperatureinconsistentLack ofprocesscontrolPackingpersonnelnot trainedQA notcheckingplacement
FMEATypePurposeUsabilitySystematically looks at theprocedural steps orinstructions for useDesignConsiders risk with productfunctionalityProcessConsiders risk with productmanufacturabilityProcessIdentify use failure modes,estimate and evaluate risks,identify controls, recommendrisk reduction actionsIdentify failure modes,estimate and evaluate risks,identify controls, recommendrisk reduction actions
Risk EvaluationRisks can be prioritized using: RI (Risk Index) RI a combination of S and O View in table format Ultimately 2 options: AR, UR RPN (Risk Priority Number) RPN product of S x O x D The lower the betterHazardsAnalysisDFMEAPFMEAUFMEA
Risk AcceptabilityHazards Analysis Risk Index TableProbability of wMedium1LowLowLowLowMediumSeverityKey:LowLow Risk – AcceptableMediumMedium Risk – AcceptableHighHigh Risk – Unacceptable
Example of Combined Risk AnalysisPatient HarmHazardous SituationTissue/Vessel Damage,Delayed TreatmentStandard SyringeLoss of Syringe DeviceFunctionalityExcessive force during useleading to separationSyringe plunger does not fullydepressProduct FailureUsabilityProcessDesign: InsufficientDesign tolerance of piston diameterdimensionPiston Molding:Excessive moldpressure
Syringe Hazards AnalysisHazard orHazardousSituationHarmSeverityRatingCause of FailureImproper useSyringe doesnot fullydepressTissue/ VesselDamage,DelayedTreatment5Improper ting3Controls to Preventor Detect a CauseInstructions for use,product labeling2Adequaterequirements, propermaterial selection4Manufacturingprocess controls,operator training, finalinspection
Syringe UFMEAProcessStepFailureModeSyringedoes notfullydepressClinicianUsesExcessiveForceEffect onProcedure/PatientProcedural stepneeds to berepeatedTissue/vesseldamage/delayof ng orinstructionsProb.Rating2ControlsInstructions warnto not useexcessive forcePrev.Rating6
Syringe DFMEAItem NameandFunctionStandardSyringe onmoves withexcessiveresistancePiston isseverelywedged insyringebarrelEffect ay oftreatmentLoss useProb.Rating7Inadequatepiston erence fit ofpiston to syringebarrelMaterial design:piston and barrelmaterialcompatibilityDet.Rating1
Syringe PFMEAProcess StepPistonmoldingFailureModeMoldpressuretoo highEffect onProcedure/PatientProcedural stepneeds to berepeatedTissue/vesseldamage/delay ing ucer2ControlsStandardoperatingprocedures,operator training,in-process andfinal inspectionSupplier et.Rating43
Statistical Techniques Opportunities Design verification and validation Process validation Post-market clinical follow-up/surveys Specific tasks– Sample size determination– Acceptance criteria– Analysis of data
Design V&V Sample Sizes Consider the type of data– Attribute– Variable Use the risk analysis Perform statistical analysis
Attribute Data Analysis Minimum sample size– No failures allowed Larger sample sizes– May allow failures
Formula for 0 Failure Sample Sizes
Attribute Testing Sample SizesEffect and CriteriaRankCritical Death caused directly by the hazardous situationwhere the device was a contributing factor5Serious Serious injury, defined as an injury that is lifethreatening or resulting in permanent impairment of a bodyfunction or permanent damage to body structure4Moderate Serious injury that is not classified as 4, but isdefined as requiring medical intervention to preclude permanentimpairment of a body function or permanent damage to a bodystructure (temporary)3Limited Non-serious injury not involving medical or other thirdparty intervention, or moderate discomfort/stress requiringmedical interventionNegligible No injury; cosmetic or nuisance onlyTest StrategyConfidence 95%Reliability 95%N 592Confidence 95%Reliability 93%N 421Confidence 90%Reliability 90%N 22
Variable Testing Confidence/ReliabilityEffect and CriteriaRankConfidence/ReliabilityCritical Death caused directly by the hazardous situationwhere the device was a contributing factor5Serious Serious injury, defined as an injury that is lifethreatening or resulting in permanent impairment of a bodyfunction or permanent damage to body structure4Moderate Serious injury that is not classified as 4, but isdefined as requiring medical intervention to precludepermanent impairment of a body function or permanentdamage to a body structure (temporary)3Limited Non-serious injury not involving medical or otherthird-party intervention, or moderate discomfort/stressrequiring medical intervention2Confidence 95%Reliability 93%Negligible No injury; cosmetic or nuisance only1Confidence 90%Reliability 10%Confidence 95%Reliability 95%
Variable Testing Confidence and PowerEffect and CriteriaRankCritical Death caused directly by the hazardous situationwhere the device was a contributing factor5Serious Serious injury, defined as an injury that is lifethreatening or resulting in permanent impairment of a bodyfunction or permanent damage to body structure4Moderate Serious injury that is not classified as 4, but isdefined as requiring medical intervention to precludepermanent impairment of a body function or permanentdamage to a body structure (temporary)3Limited Non-serious injury not involving medical or otherthird-party intervention, or moderate discomfort/stressrequiring medical intervention2Negligible No injury; cosmetic or nuisance only1Confidence/PowerConfidence 95%Power 95%Confidence 95%Power 90%Confidence 90%Power 90%
Variable Testing Difference to DetectConfidence Level 95%Power ofTest (%)9590Confidence Level 90%Difference to Detect, δ (interms of std. dev.)SampleSizeDifference to Detect, δ (interms of std. .71.01.58583619116
Conclusions Quality tools and techniques significantly help inrisk management system development. The risk management system is connected tomany other quality system processes. Product risk analyses are also interconnected.Different techniques applied together are neededto comprehensively assess risk.
THANK YOU FOR ATTENDING!
FMEA Type Purpose Process Usability Systematically looks at the procedural steps or instructions for use Identify use failure modes, estimate and evaluate risks, identify controls, recommend risk reduction actions Design Considers risk with product functionality Identify failure modes,