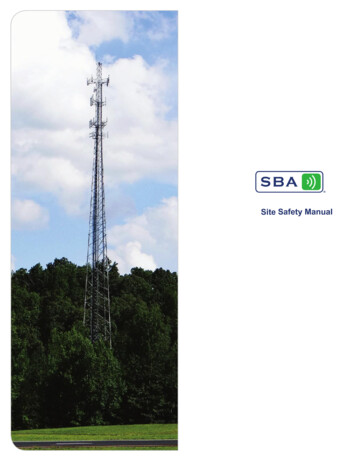
Transcription
SBA Site Safety ManualRevised December 20161 P a g e
1.0SBA’S POLICY AND COMMITMENT TO SAFETYAs a leader in the wireless industry, it is the ultimate goal of SBA CommunicationsCorporation (“SBA”) to provide a healthy and safe work environment for the protection ofour most vital resources – our employees and contractors. SBA’s core belief is that allinjuries and incidents are preventable. Accordingly, each SBA employee and contractorequally shares the responsibility and accountability for safety.The fundamental premise of SBA’s health and safety philosophy is that no task is soimportant that it should be performed in an unsafe manner. SBA’s commitment to itsemployees and contractors allows for Stop Work Authority without fear of disciplinaryaction.2.0APPLICATION OF SITE SAFETY HANDBOOKThe Site Safety Handbook shall be used in conjunction with applicable federal and statesafety regulations and is intended to be used as a field reference. The Site SafetyHandbook provides SBA’s expectations and minimum requirements for health and safetyperformance. It should be understood that additional requirements may apply dependingupon the scope of work and task performed.SBA’s Site Safety Handbook includes five focus topics closely associated with our mostcommon and severe risks. SBA’s Focus Five closely align with OSHA’s Focus Four safetytopics with one additional topic. The topics include: Fall Protection Electrical Safety (Lockout Tagout) Manual Material Handling and Lifting Cranes, Hoists, and Rigging Safety Electromagnetic Energy (EME) SafetySBA employees will be granted access to an electronic copy of the Site Safety Handbookat the time of initial employment. Electronic versions of the Site Safety Handbook and allreferenced forms are available on SIGNALS including the company provided externalwebsite. Contact the SBA Safety Department for any safety-related questions regardingthe Site Safety Handbook and referenced forms.Contractors will be have access to SBA’s Injury and Illness Prevention Program (I2P2) attime of via external website. Contractor(s) shall have and must abide by their own healthand safety program along with the SBA Site Safety Handbook and client’s health andsafety policies, as applicable. Contractor shall at all times conduct operations in such amanner to avoid the risk and endangerment to health, bodily harm to persons, damage toproperty, and damage to the natural environment. Contractor shall comply with allapplicable safety and health laws and regulations. Contract employees must have in theirpossession and use all personal protective equipment required for the work activities tobe performed. Contractor shall furnish all environmental, health and safetydocumentation, procedures and plans, as well as safety equipment and instructionsrequired to complete the work.3.0TRAINING AND COMMUNICATIONThis section details the health and safety training requirements for SBA employees andcontractor personnel. All training administered to employees shall be taught inaccordance with the latest revision of ANSI Z490. Contractor’s personnel are required tohave completed Occupational Safety and Health Administration (OSHA) health and safetySBA Site Safety ManualRevised December 20162 P a g e
training in accordance with 29 Code of Federal Regulations (CFR) 1910, 29 CFR 1926,ANSI Z359, TIA 1019A, TIA 222 and all other applicable industry standards, includingannual refresher training. SBA’s safety training program and practices entail formal andinformal health and safety training provided by SBA’s Safety Department and approvedoutside sources. Per the scope of work being performed, all SBA employees andcontractors shall adhere to federal, state and local regulatory requirements with regards totraining. This training may include but not limited to the following: Introduction to OSHATrenching and ExcavationsManual LiftingRF Site Safety AwarenessFall ProtectionEmergency PreparednessHousekeepingElectrical Safety/Lockout TagoutForkliftsHot WorkConcrete WorkPersonal Protective EquipmentFirst Aid/CPR Incident Investigation and ReportingSBA Policies/ProceduresHazard Communication/GHSSite Safety AssessmentRopes/KnotsTower RescueTower Site SecurityAuthorized/Competent ClimberHand and Power Tool SafetyCranes, Hoists, and Rigging SafetyBloodborne PathogensCapstan HoistHazard IdentificationEmployee training is documented through completion of attendance sheets and skillsevaluations. Training records are maintained in accordance with SBA’s record retentionpolicy.4.0WORKSITE ANALYSIS AND INSPECTIONPre-Work AssessmentIt is the responsibility of SBA field supervision, contractors, or designated SBA employeesto perform a Pre-Work Assessment of the jobsite to identify all pre-existing and potentialhazards. All visitors must be escorted by a SBA representative and provided with essentialinformation related to site hazards and emergency response requirements. Necessarysafety measures, as determined by the Pre-Work Assessment, must be taken to eliminateidentified hazards.Information required for completion of the Pre-Work Assessment includes: Job information Project personnel Emergency procedures Job-site exposures Hazard control measures Civil work information Tower work information Review and signature blockSafety hazards and control measures in the Pre-Work Assessment shall be discussedwith field crews prior to the start of work and on a periodic basis (i.e., daily, weekly).SBA Site Safety ManualRevised December 20163 P a g e
The Pre-Work Assessment shall be reviewed each day and revised accordingly to ensurethat hazards have not changed. All employees and contractors onsite should sign theassessment indicating they have reviewed it and understand the hazards and safetyrequirements.The Pre-Work Assessment must be located in an area that is known to all employees andremain onsite for the duration of the job. Employees and contractors should consult with theSBA supervisor or reference project-specific documents to determine requirements forretention of completed Pre-Work Assessment.PPE Hazard AssessmentPersonal protective equipment (PPE) assessments are completed by SBA’s SafetyDepartment for specific site or work tasks to determine if hazards are present that wouldnecessitate the use of PPE. The assessments are completed and documented inaccordance with OSHA 29 CFR 1910.132 (d). The PPE assessments are to be used in theproper selection of PPE based upon scope of work. Training will be provided to employeeson PPE initially and as site hazards and associated PPE requirements change. The PPEHazard Assessment shall be available under Safety Resources on the company’s Signalswebpage.Equipment Safety InspectionEquipment safety inspections include, but may not be limited to: Personal fall arrest systems (PFAS) Ladders and scaffolds Hand and power tools PPE Ropes (load ropes, tag ropes, safety ropes) Rigging equipment Fire extinguishers First-aid kits Vehicles Forklifts Cranes and hoists Personnel lifts (aerial lifts) Hot work equipment (cutting and welding) Electrical (temporary or permanent)Inspections may be required on a pre-use, daily, or monthly basis, and according toregulatory requirements or manufacturer’s recommendations. Equipment safety inspectionsare performed by the equipment operator or user prior to equipment use or as required.Inspections should be documented and records maintained available onsite.Health and Safety AuditsThe Safety Manager, Safety Technician, or Field Supervisor will conduct safety auditscoinciding with each site walkthrough to identify any unsafe conditions, work practices, ornon-compliance issues and review of required safety documentation. The purpose of theseaudits will be to review compliance with federal, state, and provincial regulations, consensusstandards, and SBA health and safety requirements. The audit will be documented on theHealth and Safety Checklist. The audit findings will be reviewed and discussed with fieldSBA Site Safety ManualRevised December 20164 P a g e
supervision. Health and Safety Checklists completed by the Field Supervisor shall beturned in weekly to their respective Health and Safety Representative.Incident ReportingReporting of Work-Related Injuries/Illnesses and Near MissesSBA pays the entire amount of the Workers' Compensation insurance premiumwhich provides benefits to employees who experience injury or illness arising outof their employment. Eligibility for Workers' Compensation benefits is governed bylaw. Thus, it is mandatory that employees immediately report all work-relatedincidents, injuries, and illnesses to their manager/supervisor. The supervisor willcontact a Safety Department Representative.Employees involved in an incident must notify their Supervisor and respectiveSafety Manager once aid is rendered and the scene is safe. SBA’s Worker’sCompensation Reporting Worksheet shall also be completed if an injured employeeseeks medical attention. If a work-related injury does not require medical attention,SBA’s First-Aid Report must be completed and returned to the Safety Department.The Supervisor, in conjunction with the injured employee, must complete the form.All forms shall be completed immediately following the incident and returned to theSafety Department. Investigations of incidents will be conducted as soon as possiblefollowing the incident.A post-incident urinalysis may be required after the incident. Contact your SafetyManager or Insurance Administrator for instructions.Motor Vehicle IncidentA report of all work-related motor vehicle (SBAowned, rental, or employee-owned) incidents must bemade immediately after the incident. After reportingthe incident to your supervisor, you must call GE Fleetto report the incident. NOTE: Your reportingresponsibilities do not end after calling GE Fleet.Reporting forms and incident post incident urinalysisare still required. SBA’s reporting form must becompleted and submitted the day of the incident tothe Safety Department.A post-incident urinalysis may be required after theincident. Contact your Safety Manager or Insurance Administrator for instructions. Contact police/911. If safe, follow first-aid/CPR training.Contact Supervisor who will notify the Safety Manager of the incident.Take photographs and collect information at the incident scene.Call GE Fleet to report Incident.Complete required SBA reporting form then forward to Supervisor and theSafety Manager.Work-Related InjuryIf injury is life threatening, call 911. If safe, follow first-aid/CPR training.SBA Site Safety ManualRevised December 20165 P a g e
5.0Immediately call Supervisor to report injury. Supervisor will contact the SafetyManager and determine the appropriate medical treatment facility.Complete appropriate SBA reporting form then forward to Supervisor and SafetyManager.Property Damage or TheftContact police to report incident.Contact Supervisor who will notify the Safety Manager of the incident.Complete appropriate SBA reporting form then forward to Supervisor and SafetyManager.EMERGENCY RESPONSEThe Pre-Work Assessment form contains all localemergency services numbers, company contactinformation, directions to the worksite, nearestoccupational healthcare facility and hospital. Adesignated evacuation/assembly point that will serve asa gathering point in the event of an emergency shall beidentified and communicated to all site personnel. Allvisitors must be escorted by a SBA representative andprovided with essential information related to sitehazards and emergency response requirements.All SBA worksites shall have a minimum of two personsonsite at all times who hold a current first-aid (FA) and cardio-pulmonary resuscitation (CPR)certification from the American Red Cross (or equivalent).Emergency CommunicationsIf an emergency situation occurs, emergency services should be summoned by dialing 911or designated emergency number. In the event cellular service is not available on theworksite, the nearest location for landline or cell service shall be indicated on the Pre-WorkAssessment form.Emergency PreparednessThe geographical location of the site has the potential to influence the type of emergencythat may be encountered (e.g., hurricane near the coast, tornadoes in the Midwest). Thefollowing are examples of emergencies that may occur on SBA worksites and theprocedures to follow:Medical EmergencyIf a medical emergency (heart attack, fall from a height, etc.) occurs on the work site: Perform medical treatment to the degree that training allows (e.g., CPR,bandaging). If injuries are significant (as determined by the first-aid/CPR-trainedresponder), then: Notify 911 or the local ambulance service immediately and give the operator thefollowing information:o Your name and the name of the company;o Site location using longitude and latitude numbers (can be retrieved from thePre-Work Assessment form);SBA Site Safety ManualRevised December 20166 P a g e
Directions to the site (directions can be retrieved from the Pre-WorkAssessment form);o Nature and severity of the emergency; ando Wait for and follow any instructions from the emergency services operator.DO NOT hang up unless the operator instructs you to do so.Once emergency medical services arrive on site, assist the medical personnel inwhatever manner they request.o FireIf a fire occurs on the worksite, notify 911 or the local fire department and give theoperator the following information: Your name and the name of the company; Site location and directions to the site (directions can be retrieved from the PreWork Assessment form); Nature and severity of the emergency; and Wait for and follow any instructions from the emergency services operator. DONOT hang up unless the operator instructs you to do so.Extinguishing: If the fire is small (incipient stage), attempt to extinguish with fire extinguishers onhand; If the fire cannot be controlled with the extinguishers on hand, evacuate the workarea and proceed to the designated Evacuation/Assembly Point; Perform a count of personnel to ensure that everyone is at the designated point;and Wait for the fire department to arrive.TornadoIf a tornado warning is issued for the area or a tornado has been spotted by amember of the work crew: Take shelter immediately in a pre-designated safe area; and Remain in the safe area until the tornado warning has expired or until the tornadohas passed and it is deemed safe to leave the safe area by the supervisingperson on site.Other Severe Weather Conditions:When severe weather conditions are present in the area of an SBA worksite: If any lightning is visible, immediately discontinue any outdoor work. Climbing onany tower or working on rooftop when lightning is visible is prohibited. Remainoff the tower or rooftop for thirty minutes after the last visible lightning. If high winds are present at the SBA worksite, work on the tower or rooftop mustbe discontinued or be reevaluated by the site competent person. All materialsand equipment must be secured to prevent incidental displacement.Bloodborne PathogensPotential exposure to bloodborne pathogens exists during unprotected contact withpotentially infectious material such as blood and other body fluids. Universal precautionsrequire that all blood and body fluid be considered contaminated with bloodborne pathogens,including HIV/HBV, and treated as such. This contact could occur while providingmedical/first-aid assistance or while cleaning up after a first-aid or medical incident.SBA Site Safety ManualRevised December 20167 P a g e
Guidelines to protect from unprotected exposure to bloodborne pathogens include thefollowing: Attend SBA-provided or other recognized FA/CPR training. All first-aid responders will use gloves when touching blood, body fluids, mucousmembranes, or non-intact skin of any injured personnel or when handling items orsurfaces soiled with blood or body fluids. Change gloves when switching from patient topatient. All contaminated protective equipment and clothing will be removed and placed in adisposal bag prior to removing gloves. Wash hands immediately after gloves areremoved with a micro-biocide antiseptic cleaner. Avoid self-inflicted incidental wounds from sharp objects contaminated with potentiallyinfectious material. Proper hand washing should be performed as soon as possible post injury response.Wash hands with antibacterial soap and water immediately after removing gloves anddisposable clothing, particularly when contaminated with blood or body fluids. First-aid providers who have open wounds must refrain from all employee care and fromhandling first-aid equipment and supplies until the condition is completely healed.Likewise, fluid or dressings from employees with open wounds must be handled as anybody fluid contaminated object.6.0TOWER SITE SECURITYSecurity during Tower ConstructionThe most significant security risks during the tower construction phase are vandalism, theftof tools and equipment, and workplace violence by, or injury to, non-authorized individuals.The following guidelines shall be observed as much as feasible during tower construction: Indicate the perimeter of the tower site with barrier tape, and have the security fenceerected as early in the site work as feasible.Be observant of site conditions and prevent unknown persons from accessing the site.Establish access points for vehicles and park so as to limit access to the site.Clean up the site at the end of each shift, placing tools and equipment in lockedcontainers.Require that site visitors be escorted at all times.Lock out or remove the keys from equipment prior to departure from the site at the endof the day.Excavations left overnight must be protected and appropriately secured fromunauthorized entry.Ensure all equipment and materials are secured and left in a safe and stable condition.Post SBA’s 4-in-1 Safety Sign.Security for Existing TowersThe most significant security risks for existing towers are vandalism and injury totrespassers. The following guidelines shall be observed as much as feasible for existingtowers: A security fence is the minimum security for isolated tower sites (not located onbuildings).A lock will be used to secure the access gate.Regulatory signs will be posted as required.SBA Site Safety ManualRevised December 20168 P a g e
7.0Some sites may have special security requirements, such as card access and remotevideo monitoring. These are typically customer requirements, but may be adopted atSBA’s discretion on a site-specific basis.Security for Controlled Access AreasAccess to rooftops and similar sites is generally controlled by property management.Some sites may have special security requirements, such as card access and remotevideo monitoring. These are typically customer requirements, but may be adopted atSBA’s discretion on a site-specific basis.PERSONAL PROTECTIVE EQUIPMENT PPE is to be selected and used based upon information from the annual HazardAssessment and the Pre-Work Assessment. Supervisors will ensure all employees maintain their PPE and acquire new equipmentwhen needed. Changes in PPE should be evaluated based upon changing site hazardsand/or scope. All PPE must be marked with the appropriate American National Standard Institute(ANSI) standard, where applicable. All PPE must be inspected prior to each use. PPE found to have defects, damage, orexcessive wear, or is otherwise non-compliant, shall be removed from service. If additional clarification is needed on PPE selection, contact SBA Safety DepartmentRepresentative. Head ProtectionAll head protection shall comply with ANSI-Z89.1.Hardhats are required at all times on SBA worksites.ANSI-approved, Class E, climbing helmets arepermitted when working at heights.All head protection must be worn in accordance withmanufacturer’s recommendations.Inspect hardhats for cracks and defects daily.Eye ProtectionAll eye protection must comply with ANSI-Z87.1.ANSI-approved safety glasses with side shields must be worn when exposed to eyehazards such as flying or falling objects, airborne dust, concrete chipping, and grinding.In some instances (chemical handling, excessive dust, grinding operations) additionaleye protection (face shields, goggles) must be worn.Appropriate eye protection must be worn for welding and cutting (minimum density - #3).Hand ProtectionWear suitable work gloves (leather, Kevlar) while handling materials that can causelacerations, abrasions, burns, or other injuries.Wear chemical-resistant gloves when handling or dispensing hazardous substances asreferenced by the chemical safety data sheet (SDS).Utilize electrically insulated gloves when performing work on electrical componentsgreater than 50 volts which are energized and exposed or conducting live electrical(AC/DC) work.SBA Site Safety ManualRevised December 20169 P a g e
Foot ProtectionWhen applicable, safety-toed shoes shall comply with ANSI-Z49.1.Wear substantial leather work shoes or boots with non-slip, non-conductive soles toprotect feet from contact with physical hazards.Rubber boots are required when performing concrete work.Employee shall, at a minimum, use a slip-on metatarsal foot guard when usingcompactors or jackhammers.Hearing ProtectionHearing protection shall be worn in high noise areas (difficult to verbally communicatewithin arm’s reach) or areas with measured levels of 90 decibels(Time Weighted Average) or greater.Hearing protection shall be maintained in a clean and sanitarycondition.Personnel wearing hearing protection shall receive training onnoise hazards and use of hearing protection.Acceptable hearing protection includes ear plugs (foam or molded)or ear muffs.Cotton, tissue, cloth, or other make-shift perceived sounddampening materials are prohibited.Respiratory ProtectionSBA has conducted a hazard assessment and determined that SBA’s normal workoperations do not require the routine use of respiratory protection to maintain employeeexposures below regulatory exposure limits; however, in the interest of employee comfort,SBA will allow the voluntary use of nuisance-dust mask for qualified employees whorequest them. Requests for use of an air-purifying or supplied-air respirator shall be reviewed andapproved by the Safety Department. Only filtering face pieces (commonly known as dust masks) will be used for nuisanceexposures. No cartridge air-purifying or any air-supplying respirators will be used forcontrolling nuisance exposures. The voluntary use of nuisance dust mask is allowed to provide an additional level ofpersonal comfort, even when not required by the Pre-Work Assessment. Prior to the voluntary use of nuisance-dust masks, workers must complete a Dust MaskRequest form and be trained in the proper use of dust masks.Respiratory protection for SBA subcontractors: It is understood that work performed by SBAsubcontractors may require the use of tight-fitting, air-purifying respirators. Accordingly,respiratory protection usage by SBA subcontractors will be determined by thesubcontractor’s respiratory protection program and in accordance with OSHA 1926.103.8.0FOCUS FIVE TOPIC 1 – FALL PROTECTIONIt is a requirement of SBA with regard to the hazards of elevated work that all employees andcontractors maintain 100% fall protection at all times. Elevated work is considered work onelevated surfaces that have an unprotected side or leading edge that is 6 feet or more abovea lower level.The following section identifies the specific field safety requirements for safe-work practicesand fall protection equipment for hazards associated with elevated work while working onSBA Site Safety ManualRevised December 201610 P a g e
communication towers, including antennas, broadcast, stealth, rooftops, and otherstructures that support communication-related equipment.General Requirements100% fall protection, compatible with the tasks assigned, is to be provided, used, andmaintained pursuant with this program when personnel are exposed to falls in excess of 6feet. All Equipment used for Fall Protection and Rescue must meet the requirements of thelatest revision of ANSI Z359.Positioning devices SHALL NOT be used in place of a PFAS, and their use will beconsidered free climbing. Free climbing is strictly prohibited. ReferencesOSHA Standardso OSHA 1926 Subpart Mo OSHA 1910 Subpart Do North Carolina OSHA 13 NCAC 07Fo Michigan OSHA-STD-1329ANSI/TIA Standardso ANSI Z359.1o ANSI A10.32o ANSI A14.3o ANSI A10.14o TIA-1019o TIA-222-GJob PlanningAll projects requiring climbing shall be planned by a Competent Person. Pre-jobplanning shall include identification of primary and alternate climbing routes,evaluation of obstructions, qualifications/training of climbers, PFAS, and any otherfactors associated with climbing activities. To reduce the concern for potentialsuspension trauma in the event of a fall, a rescue plan shall be developed as partof pre-job planning.Fall Protection Systems EvaluationFor the duration of each project, the Competent Person shall evaluate workoperations, climbing facilities, weather conditions, and PFAS to determine if anymodifications to the pre-job plan are required.InspectionPFAS shall be inspected and the inspection documented (using the Personal FallArrest System Checklist) by a trained employee daily (or prior to use) for wear,damage, defect, or other deterioration. Defective equipment shall be identified andtagged as unsafe and immediately removed from service.Training/QualificationsBefore performing work at heights above 6 feet, SBA employees and contractors mustreceive required fall protection training. Authorized / Competent Climber/Rescuertraining shall be provided by SBA Safety Department. Contractors must be certifiedthrough a National Association of Tower Erectors Tower Climber Fall ProtectionSBA Site Safety ManualRevised December 201611 P a g e
Training Standard (NATE CTS) vendor prior to climbing any structure or workingfrom heights greater than 6 feet. Training must be documented per the provider’srequirements, and each Authorized / Competent Climber must be in possession oftraining certification while on an active jobsite. Personal Fall Arrest Systems (PFAS)Employees must pre-plan their climbing activities to insure they have the properPFAS components to perform the job safely.PFAS will require at least a full-body harness with shock absorbing lanyards orretractable lifeline and an anchorage point rated at 5,000 pounds.Positioning devices SHALL NOT be used in place of a fall arrest system and willbe considered “free climbing”. Free climbing is not permitted under anycircumstances!Anchorage PointsAll anchorage points for personal fall arrest systems shall be capable ofsupporting 5,000 pounds per employee attached.Whenever possible, an overhead anchorage point should be selected to reducethe contact hazards and forces associated with a fall.Step bolts may not be used as anchorage points.Anchorage points for vertical and horizontal lifelines shall be independent of anyother system and shall be capable of supporting 5,000 pounds per employeeusing the anchorage.All safety lines and lanyards shall be protected against being cut or abraded.When vertical lifelines are used, no more than one employee shall be attached toany one lifeline. Synthetic ropes used in vertical lifelines shall have a minimumbreaking strength of 5,600 pounds (25kN). Lanyards used with vertical lifelinesshall not exceed 3 feet.When more than one employee is using a horizontal lifeline for fall-arrestpurposes, the lifeline shall be capable of supporting 5,000 pounds per employee(maximum of two people are permitted on a single horizontal lifeline at any onetime unless otherwise specified by the manufacturer).Connecting Device Fall RestraintAnchorage PointBody HarnessFull-Body HarnessA personal fall arrest system shall include a full-body harness that is properlyfitted to the worker and utilized to manufacturer’s specifications.The use of a body belt is prohibited as an approved PFAS.SBA Site Safety ManualRevised December 201612 P a g e
Prior to accessing towers or rooftops, employees must conduct an inspection ofPPE, and complete the Personal Fall Arrest System Checklist form. Thecompleted forms must remain accessible and at the jobsite at all times. Duringinspection, damaged PPE found must be removed from service immediately.Connecting DevicesA twin shock-absorbing lanyard shall be utilized to attach from the full-bodyharness to an approved anchor or connection point.For use with a PFAS the attachment point of the lanyard to the body harnessshall be to the D-ring in the center of thewearer’s back.Snap hooks and carabineers shall have aminimum of two deliberate actions requiredto open. These devices must be self-lockingand shall not be connected to each other.Snap hooks and carabineers shall becapable of sustaining a 5,000 (22.2kN)pound tensile load and gate-strength ratedat 3,600 (16kN) pounds.Connection devices, including carabineers,cross-arm straps, self-retractable lifelines,snap hooks, cable/rope grab, lanyards,etc., shall be utilized to manufacturer’sspecifications.Elevated Tower WorkThe following safety precautions are intended to inform all personnel working in elevatedpositions of the skills and techniques necessary to safely construct, modify, and installtelecommunications equipment on towers.AT NO TIME SHALL THE TOWER CLIMBER RIDE THE LINE TO GAIN ACCESS TO THESTRUCTURE. Minimum of two trained climbers/rescuers must be onsite while performing elevatedtower work.Review tower engineered drawings and the Pre-Work Assessment to identify potentialhazards and control measures associated with elevated work activities.Discuss and select the safest path of travel to access, ascend, and descend the tower.Inspect all tools, equipment, and rigging to e
SBA Site Safety Manual Revised December 2016 3 Page training in accordance with 29 Code of Federal Regulations (CFR) 1910, 29 CFR 1926, ANSI Z359, TIA 1019A, TIA 222 and all other applicable industry standards, including annual refresher training. SBA’s safety