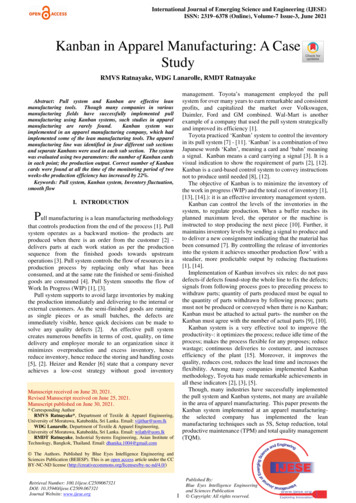
Transcription
International Journal of Emerging Science and Engineering (IJESE)ISSN: 2319–6378 (Online), Volume-7 Issue-3, June 2021Kanban in Apparel Manufacturing: A CaseStudyRMVS Ratnayake, WDG Lanarolle, RMDT Ratnayakemanagement. Toyota’s management employed the pullsystem for over many years to earn remarkable and consistentprofits, and capitalized the market over Volkswagen,Daimler, Ford and GM combined. Wal-Mart is anotherexample of a company that used the pull system strategicallyand improved its efficiency [1].Toyota practiced ‘Kanban’ system to control the inventoryin its pull system [7] - [11]. ‘Kanban’ is a combination of twoJapanese words ‘Kahn’, meaning a card and ‘bahn’ meaninga signal. Kanban means a card carrying a signal [3]. It is avisual indication to show the requirement of parts [2], [12].Kanban is a card-based control system to convey instructionsnot to produce until needed [8], [12].The objective of Kanban is to minimize the inventory ofthe work in progress (WIP) and the total cost of inventory [1],[13], [14].): it is an effective inventory management system.Kanban can control the levels of the inventories in thesystem, to regulate production. When a buffer reaches itsplanned maximum level, the operator or the machine isinstructed to stop producing the next piece [10]. Further, itmaintains inventory levels by sending a signal to produce andto deliver a new consignment indicating that the material hasbeen consumed [7]. By controlling the release of inventoriesinto the system it achieves smoother production flow’ with asteadier, more predictable output by reducing fluctuations[1], [14].Implementation of Kanban involves six rules: do not passdefects-if defects found-stop the whole line to fix the defects;signals from following process goes to preceding process towithdraw parts; quantity of parts produced must be equal tothe quantity of parts withdrawn by following process; partsmust not be produced or conveyed when there is no Kanban;Kanban must be attached to actual parts- the number on theKanban must agree with the number of actual parts [9], [10].Kanban system is a very effective tool to improve theproductivity-: it optimizes the process; reduce idle time of theprocess; makes the process flexible for any proposes; reducewastage; continuous deliveries to costumer, and increasesefficiency of the plant [15]. Moreover, it improves thequality, reduces cost, reduces the lead time and increases theflexibility. Among many companies implemented Kanbanmethodology, Toyota has made remarkable achievements inall these indicators [2], [3], [5].Though, many industries have successfully implementedthe pull system and Kanban systems, not many are availablein the area of apparel manufacturing. This paper presents theKanban system implemented at an apparel manufacturingthe selected company has implemented the leanmanufacturing techniques such as 5S, Setup reduction, totalproductive maintenance (TPM) and total quality management(TQM).Abstract: Pull system and Kanban are effective leanmanufacturing tools. Though many companies in variousmanufacturing fields have successfully implemented pullmanufacturing using Kanban systems, such studies in apparelmanufacturing are rarely found.Kanban system wasimplemented in an apparel manufacturing company, which hadimplemented some of the lean manufacturing tools. The apparelmanufacturing line was identified in four different sub sectionsand separate Kanbans were used in each sub section. The systemwas evaluated using two parameters: the number of Kanban cardsin each point; the production output. Correct number of Kanbancards were found at all the time of the monitoring period of twoweeks-the production efficiency has increased by 22%.Keywords: Pull system, Kanban system, Inventory fluctuation,smooth flowI. INTRODUCTIONPull manufacturing is a lean manufacturing methodologythat controls production from the end of the process [1]. Pullsystem operates as a backward motion- the products areproduced when there is an order from the customer [2] delivers parts at each work station as per the productionsequence from the finished goods towards upstreamoperations [3]. Pull system controls the flow of resources in aproduction process by replacing only what has beenconsumed, and at the same rate the finished or semi-finishedgoods are consumed [4]. Pull System smooths the flow ofWork In Progress (WIP) [1], [3].Pull system supports to avoid large inventories by makingthe production immediately and delivering to the internal orexternal customers. As the semi-finished goods are runningas single pieces or as small batches, the defects areimmediately visible, hence quick decisions can be made tosolve any quality defects [2]. An effective pull systemcreates numerous benefits in terms of cost, quality, on timedelivery and employee morale to an organization since itminimizes overproduction and excess inventory, hencereduce inventory, hence reduce the storing and handling costs[5], [2]. Heizer and Render [6] state that a company neverachieves a low-cost strategy without good inventoryManuscript received on June 20, 2021.Revised Manuscript received on June 25, 2021.Manuscript published on June 30, 2021.* Corresponding AuthorRMVS Ratnayake*, Department of Textile & Apparel Engineering,University of Moratuwa, Katubedda, Sri Lanka. Email: vijithar@uom.lkWDG Lanarolle, Department of Textile & Apparel Engineering,University of Moratuwa, Katubedda, Sri Lanka. Email: wilath@uom.lkRMDT Ratnayake, Industrial Systems Engineering, Asian Institute ofTechnology, Bangkok, Thailand. Email: dhanika.1004@gmail.com The Authors. Published by Blue Eyes Intelligence Engineering andSciences Publication (BEIESP). This is an open access article under the CCBY-NC-ND license )Retrieval Number: 100.1/ijese.C2509067321DOI: 10.35940/ijese.C2509.067321Journal Website: www.ijese.org1Published By:Blue Eyes Intelligence Engineeringand Sciences Publication Copyright: All rights reserved.
Kanban in Apparel Manufacturing: A Case StudyII. METHODOLOGYKanban should be completed by the line in 3.84 minutes.As per Japanese Management Association [19], if aKanban system is implemented with large number ofKanbans it is unexpected to have a higher accuracy- when thenumber of Kanbans are smaller, more accurate results can beobtained. In order to obtain the more effective outcome it wasdecided to split the production line into several well definedsections so that the operators can work in their particularsection. Considering the sequence of operations and the partsof the garment, initially 3 sections were identified as frontoperations, back operations the assembly operations.Standard times of the operations of these sections were 7.04minutes, 10.59 minutes and 15.98 minutes respectively. Thenumber of Kanbans to each section was allocated based onthe standard time of the respective section. The number ofKanbans allocated to front operations, back operations andassembly operations sections were 7, 11 and 17 respectively.Since the assembly section has the higher number of Kanban,this section was divided into 2 sub sections: Assembly 1 andassembly 2 when assigning the Kanbans. Total standard timeof the operations in assembly section 1 was 9.09 minutes andin assembly section 2 was 6.89 minutes. The number ofKanbans allocated to assembly sections 1 and 2 arerespectively 10 and 7.The standard times assigned to each operation was takenfrom the work-study department. The procedure ofimplementing the Kanban system is described below usingthe front operation section. Table I shows the operations ofthe front operations and their input & output operations withthe standard time of operations and the machines used foreach of the operations.Also for the successful implementation of Kanban systemall the employees in the selected production line were awareon the Kanban system and specially the six rules of Kanban.Thereafter trained them how to follow the rules andmonitored their work.A. Introduction of the Production LineThe selected factory produces men’s wear apparels in 20production lines. The management of the factory agreed toimplement pull system through the Kanban tool as they haveobserved high WIP fluctuations in; all production lines. Themanagement of the factory recommended to use a productionline that was producing men’s short-this line hadcomparatively high WIP fluctuation and the output wasbelow the expected production.The operation breakdown of the men’s short contained 69operations-the number of operators assigned to the line was35. Almost all the operators were well trained, multi-skilledoperators. As per the skill inventory report, skills of all theoperators were more than 90%. The work-study departmenthad made a balancing chart and the production line followedit. Cutting section issues the cut bundles when the productionline requested. A cut bundle contained 70 pieces. The factoryuses their own time database to calculate the standard timesof the products. According to that the standard time of amen’s short was 33.61 minutes. Expected production in an 8hours working day from this line was 500 pieces.Initially, WIP of each operation were counted in theproduction line hourly- for 6 days. The average total WIP ofthe line was 426 and the WIPs of the operations were variedfrom 0 to 15. Also the average production output of this linefor these 6 days were 424 pieces.B. Designing the Kanban SystemWhen designing a Kanban system the optimal number ofKanbans should be calculated, and a mechanism to extractthe Kanban cards should be established [11], [15], [16]. Theflow of the Kanban should be designed as per the operationsflow of the production line [4]. All required manufacturingdata to determine the number of Kanban cards and its flowwas collected from the manufacturing line itself.All input operation/s and output operation/s of eachoperation and the machine used in each operation werestudied. It was decided to maintain 4 pieces bundles. A 4pieces bundle was considered as 1 Kanban. Depending on theoperations and the required parts, 1 Kanban may containsdifferent parts. Required cut parts are delivered to therespective input operation by a line issuer with 4 pieces (Ibundle) at a time.The number of Kanbans was calculated as follows [17],[18]:𝑁𝑢𝑚𝑏𝑒𝑟 𝑜𝑓 𝐾𝑎𝑛𝑏𝑎𝑛𝑠 (𝐷𝑒𝑚𝑎𝑛𝑑 𝐿𝑒𝑎𝑑 𝑡𝑖𝑚𝑒)(1)(1 𝑆𝑎𝑓𝑒𝑡𝑦 𝑠𝑡𝑜𝑐𝑘)/ 𝐶𝑜𝑛𝑡𝑎𝑖𝑛𝑒𝑟 𝑠𝑖𝑧𝑒AfBfCfAs the lead time (production time) per garment is 33.61minutes, the production time for 4 pieces is 134.44 minutes.The expected daily production (demand) is 500 pieces.Therefore, the expected production during the lead time is140.04 pieces. As 4 pieces bundles were maintained, theadditional 3 pieces contained in the bundle can be consideredas the safety stock. The number of Kanban to be maintainedin the line was 35. There are 35 operators in the line-itrequired to maintain 1 Kanban with each operator.The daily demand was 500. The available time to produce500 pieces (125 Kanbans) was 28,800 seconds. Therefore,the Takt time is 0.96 minutes-Takt time is the available timeto produce single piece of the demand [20]. Thus, eachRetrieval Number: 100.1/ijese.C2509067321DOI: 10.35940/ijese.C2509.067321Journal Website: www.ijese.orgDfEf2Facing attachon frontpocket bagClose pocketbagTurn &outlinepocket bagOutline flyhemAttachzipper to entityTable- I: Details of the front section operationsCuttingsection0.824 O/LAf0.58L/SBf0.60L/SCuttingsection0.10Df &Stores0.40L/SL/S,zipperfootPublished By:Blue Eyes Intelligence Engineeringand Sciences Publication Copyright: All rights reserved.
International Journal of Emerging Science and Engineering (IJESE)ISSN: 2319–6378 (Online), Volume-7 Issue-3, June 2021FfGfHfIfJfKfLfMfNfOfPfQfRfSfO/L frontrisesAttach fly tofrontTack waistband piecestogetherSew waistband KansaistitchIron waistband hemTack labelson waist bandPocket bagattach onfrontTack pocketbag on side &waistTack pocketmouth topAttach WBto fly cornerTurn WBcorner of flysideSew fly edgestitchSew fly JstitchTack andturn fly box3 O/LCuttingsection0.22L/SE f & nIf0.30L/SJf &Stores0.282 L/SCf & Gf0.58L/SLf0.38L/SMf0.14L/SNf & K n0.22XfYfO/L fly box3 O/LTack fly boxL/SendAttach flybox to theL/Sfront panelTack waistband on flyL/Sbox cornerClose zipperL/STack crotchL/STotal SMVSf0.10Tf0.09Rf & Uf0.30Vf0.08WfXf0.210.167.04Total number of Kanbans allocated to the front section was7 and the total SMV of the front operation section is 7.04.Number of Kanban belongs to each operation was calculatedbased on the standard time of the operation. Number ofKanbans belongs to the operation i is calculated as,(𝑆𝑡𝑎𝑛𝑑𝑎𝑟𝑑 𝑡𝑖𝑚𝑒 𝑜𝑓 𝑡ℎ𝑒 𝑜𝑝𝑒𝑟𝑎𝑡𝑖𝑜𝑛 𝑖 𝑁𝑢𝑚𝑏𝑒𝑟 𝑜𝑓 𝐾𝑎𝑛𝑏𝑎𝑛𝑠 𝑎𝑙𝑙𝑜𝑐𝑎𝑡𝑒𝑑 𝑡𝑜 𝑡ℎ𝑒 𝑠𝑒𝑐𝑡𝑖𝑜𝑛) /𝑇𝑜𝑡𝑎𝑙 𝑠𝑡𝑎𝑛𝑑𝑎𝑟𝑑 𝑚𝑖𝑛𝑢𝑡𝑒 𝑣𝑎𝑙𝑢𝑒 𝑜𝑓 𝑠 𝑏𝑒𝑙𝑜𝑛𝑔𝑠 𝑡𝑜 𝑡ℎ𝑒 𝑠𝑒𝑐𝑡𝑖𝑜𝑛The calculated values of number of Kanbans for alloperations were decimal values. The operations werecombined and made groups to get approximate integer valuesfor the number of Kanbans. When combining the operations,as much as possible, combined operations use the same partsand the same machine to minimize the handling times. TableII shows combined operations and the allocation of Kanbansof the front section.Table- II: Number of Kanbans assigned to each operation and the combination of operations in the front sectionOperationNumber of erationoperationsCuttingAfFacing attach on front pocket bagL/S0.82section0.8AfBfClose pocket bag4 O/L0.580.6BfCfTurn & outline pocket bagL/S0.600.62.0CuttingsectionDf &StoresCuttingsectionE f & FfCuttingsectionHfIfDfOutline fly hemEfAttach zipper to the flyFfO/L front risesGfL/SL/S,zipper foot0.100.403 O/L0.22Attach fly to frontL/S0.26HfTack waist band pieces togetherL/S0.24IfJfSew waist band Kansai stitchIron waist band hemKansaiIron0.240.30Retrieval Number: 100.1/ijese.C2509067321DOI: 10.35940/ijese.C2509.067321Journal Website: www.ijese.org3Published By:Blue Eyes Intelligence Engineeringand Sciences Publication Copyright: All rights reserved.0.10.40.20.31.00.20.20.31.0
Kanban in Apparel Manufacturing: A Case StudyJf &StoresKfTack labels on waist bandCf & GfLfMfLfMfNfNf & K fOfPfQfCuttingsectionSfTfRf & UfVfWfXfL/S0.28Pocket bag attach on frontTack pocket bag on side & waistTack pocket mouth top2 L/SL/SL/S0.580.380.140.60.40.11.1OfPfQfRfAttach WB to fly cornerTurn WB corner of fly sideSew fly edge stitchSew fly J 8SfTack and turn fly boxL/S0.22TfUfVfWfXfO/L fly boxTack fly box endAttach fly box to the front panelTack waist band on fly box cornerClose zipper3 0.21.2YfTack crotchL/S0.160.2Thereafter operators were allocated to each operation. Asthe total number of operators allocated to the line was 35 andthe total SMV was 33.61, on average, each operator isassigned 0.96 minutes of work approximately. Table IIIshows the allocated operations to each operator/s and thenumber of Kanbans for their operations. The combinedoperations are named as groups.by indicating the piece numbers of the order. As an exampleoperations Af, Bf & Cf are carried out at the operation groupG1 and the number of Kanbans allocated is 2, and they arenamed as K1 & K2. The card is attached to the box. G1collects the box from the material handler and completes theoperations. As the system is a pull system the materials arepulled from the downstream operations. G4 collects the partsin the box K1, as G4 is the internal customer of G1 and putthem to the box K4. At the same time the part number stickeris pasted in K4, as the part number sticker of K4 is alreadytaken by the G5. Then G1 collects the next bundle from thematerial handler and put into K1 and, as the part numbersticker is taken from the G4 the respective part number istaken and pasted. When a there are 2 internal customers, thegroup will collect 2 stickers of part numbers from 2 groups.The Kanban card for them are designed to paste both stickersto make sure the collection of parts. All the materialtransports should happen at the same time at 3.84 minutesintervals.2 - (K1, K2)1- (K3)1- (K4)1- (K5)1- (K6)1- (K7)2.000.981.061.100.741.16Number ofoperatorsassignedTotalSMVAf, Bf, CfDf, Ef, Ff,, GfHf, If, Jf,, KfLf, Mf, NfOf, Pf, Qf,, RfTf, Uf, Vf,, Wf ,Xf, YfNumber ofKanbanOperationsassignedGroupTable- III: Number of operators and the Kanbanassigned to the front operation sectionG1G2G3G4G5G6211111As per the SMV allocations for the operators, the time ofthe operator assigned to the group 5 was 0.74 minutes and forgroup 6, it was 1.16 minutes. The operator at the 5th grouphas less time of work, she can help the operator at the group6.Figure 2 shows the number of Kanban allocated to eachgroup and the flow of the WIPs in the front operation section.The operations are shown in the circles. The material flowdirection is shown by arrows. The material handler of theline, who carries the cut bundles from the cutting section,puts the garment parts (4 from each part) required to performthe respective operations into boxes. Cards are preparedindicating the card number, style number, group number andthe parts included as shown in the Figure 1. A smallremovable sticker is fixed by the material handler on the cardRetrieval Number: 100.1/ijese.C2509067321DOI: 10.35940/ijese.C2509.067321Journal Website: www.ijese.org0.3Fig. 1. Sample of a Kanban card4Published By:Blue Eyes Intelligence Engineeringand Sciences Publication Copyright: All rights reserved.
International Journal of Emerging Science and Engineering (IJESE)ISSN: 2319–6378 (Online), Volume-7 Issue-3, June 2021Fig. 2. Flow of the materials in the Front operation sectionSame procedure was repeated for the other sections: backoperations, assembly section 1 and assembly section 2. TableIV, Table VI & the Table VIII show the number of Kanbansand operation combinations for the back section, assemble 1section and assemble 2 sections respectively. Table V, TableVII & Table IX show the operator allocations for thosesections respectively. Figure 3, Figure 4 and Figure 5 showthe material flow and the group allocations of the backsection, assemble 1 section and assemble 2 sectionsrespectively.Table- IV: Number of Kanban assigned to each operation and the combination of operations in the back sectionOperationNumber of uttingsectionBbIron welt facingIron table0.90CuttingsectionCbIron back & side pocket underpatchesIron table1.00CuttingsectionDbMark back under patch placementTable0.30DbEbSew back darts, Tack back darts onthe waistL/S0.32EbFbOut line back darts.Cb & FbCuttingsectionGbAttach back under patchHbBb, Gb& 4Velcro m/c0.620.7Facing attach on back pocket bag.L/S0.36IbMake back weltwelt0.95IbJbTack welt pocket endsL/S0.580.6JbKbClose welt pocket bag facingL/S0.360.4KbLbClose back pocket bagL/S0.921.01.0LbMbTurn & outline back pocket bagL/S0.951.01.0Retrieval Number: 100.1/ijese.C2509067321DOI: 10.35940/ijese.C2509.067321Journal Website: www.ijese.org5Published By:Blue Eyes Intelligence Engineeringand Sciences Publication Copyright: All rights reserved.1.10.41.01.01.0
Kanban in Apparel Manufacturing: A Case StudyCuttingsectionAbIron back pocket flapsAbNbAttach snaps on back under flapNbObObPbQb & M b0.20Snap buttonm/c0.40Outline flaps (back)L/S0.520.5PbQbTack welt pocket endsIron pocket facingBTIron0.620.300.7RbSew welt top mouth outline withflapsL/S0.96BbCbDb, Eb, FbGb, HbIbJb, KbLbMbAb , Nb, G17Number ofoperatorsassignedNumber ofKanbanTotal SMVGroupOperationsassignedTable- V: Number of operators and the Kanbanassigned to the back operation sectionG7G8G9G10G11G12G13G14G151.1Iron table0.20.41.00.31.01.0Pb, QbRbTotal1110.920.969.0911111As the operator’s time at G15 is comparatively high and inG13 is comparatively less, the operator at G13 was askedinstructed to help the operator G15 to complete theproduction. In addition, the operator at G7 was instructed tohelp the operator at G8 to maintain the time balancing.Figure 3 shows the flow of the materials in the back operationsection.111111111Fig. 3. Flow of materials in the back operation sectionTable- VI: Number of Kanban assigned to each operation and the combination of operations in the assembly section 1OperationMachineInputIdentityDescriptionSMVY f & SbAaBaAaBaCaSew side seamOut line side seamMark under patch placement5O/L2 ChainTable0.550.860.40CuttingsectionDaIron flapsIron0.65Retrieval Number: 100.1/ijese.C2509067321DOI: 10.35940/ijese.C2509.067321Journal Website: www.ijese.org6Number of KanbanOperationPublished By:Blue Eyes Intelligence Engineeringand Sciences Publication Copyright: All rights reserved.Combinedoperations0.60.90.42.00.72.0
International Journal of Emerging Science and Engineering (IJESE)ISSN: 2319–6378 (Online), Volume-7 Issue-3, June 2021Snapmachine0.40Outline flaps (front)L/S0.76GaIron side pocket under patchIron0.80HaAttach underside patchL/S0.75IaSew front pocket pleatsL/S0.33JaSew front pocket hemL/SKaAttach side pocketsLaLaMaDaEaAttach snaps on flap under partEaFaCuttingsectionG a, C a0.40.80.90.81.70.450.40.50.9L/S0.901.01.0Attach side flapsL/S0.58MaNaSew in seamsSew front & back rises5 O/L5 O/L0.300.390.60.30.41.4NaOaOut line in seamOaPaOut line front & back risesCuttingsectionIaHa & JaFa&KaFeed of thearm2 L/STable- VII: Number of operators and the Kanbanassigned to the Assembly 1 sectionGNumber ofoperatorsassignedTotal SMVNumber ofKanbanOperationsassignedGroupGAa, Ba,21.812Da, Ea,21.812GGa, Ha21.552GIa, Ja10.781G0.650.7Ka10.901La, Ma,11.271GOa, Pa10.97124At G20 & G21, the allocated operators have less time thanthe other operators and the operator assigned to G23 has morework than the average. Therefore, the operators in the G 20 &G21 were instructed to help the operator at G23. Figure 4shows the flow of the materials in the Assembly section 1.Fa2021Fig. 4. Flow of materials in the Assembly section 1Retrieval Number: 100.1/ijese.C2509067321DOI: 10.35940/ijese.C2509.067321Journal Website: www.ijese.org1.1Na23Ca190.422G180.327Published By:Blue Eyes Intelligence Engineeringand Sciences Publication Copyright: All rights reserved.
Kanban in Apparel Manufacturing: A Case StudyTable- VIII: Number of Kanban assigned to each operation and the combination of operations in the assembly 2sectionOperationNumber of KanbanMachineSMVIdentityPaQaRaQaRaSaTack loops on WBAttach waist bandSew waist band top edge out lineL/SL/SL/S0.650.720.580.70.70.62.0SaTaClose waist band2L/S0.941.01.0TaUaBar tack garmentBT1.001.01.0UaVaSew Reese hole waist band0.200.2WaMark & attach waist band button0.200.2XaSew bottom hem0.700.7XaYaBar tack loopsBT1.001.001.0YaZaAttach snap buttonsSnap0.900.930.9Va utGroupOperations assignedNumber ofKanbanTotalSMVNumber ofoperatorsassignedTable- IX: Number of operators and the Kanbanassigned to the assembly 2 sectionG25G26Qa, Ra, SaTa211.810.9421Reesebutton holeButtonAttach2 L/SG27G28G29G33UaVa, Wa XaYaZa11111.11.001.11.00.91111In the assembly section 2 operator at G26 was instructed tohelp the operator at G28. Figure 5 illustrates the movementsof the Kanbans in the Assembly section 2.Fig. 5: Flow of materials in the Assembly section 2was 208 minutes. Though, some lean manufacturingtechniques have been implemented, the factory need tofurther improve them. During this period of 2 weeks, averageproduction output was 518 pieces - the minimum andmaximum production per day were 492 pieces and 526 piecesrespectively. The production output has increased by 22%.According to the lighting arrangement of the factory theline layout was limited to 2 straight lines. Therefore somematerials were moved to some distance as per the materialflow.III. RESULTS AND DISCUSSIONOne week after the implementation of the Kanban system,the number of Kanbans at the allocated places were countedhourly for 2 weeks. At every observation, the number ofKanbans recorded were similar to the Kanban allocations ofeach group and the total number of Kanbans were 35 at all thetime. It was instructed to stop the line quickly when anycritical problems happened. Accordingly, the line wasstopped at 38 such incidents during the 2 weeks period-untilthe problem is solved. The reasons for the stoppages werequality problems (20 times), machine breakdowns (12 times)and input delay from the cutting section (4 times) and thestores (2 times). The total time lost during these 38 stoppagesRetrieval Number: 100.1/ijese.C2509067321DOI: 10.35940/ijese.C2509.067321Journal Website: www.ijese.org8Published By:Blue Eyes Intelligence Engineeringand Sciences Publication Copyright: All rights reserved.
International Journal of Emerging Science and Engineering (IJESE)ISSN: 2319–6378 (Online), Volume-7 Issue-3, June 2021Here the lighting and the line setup should organize tominimize the material movements. By eliminating the abovementioned drawbacks the factory can maximize the gain ofthe Kanban system.15.16.IV. CONCLUSIONThe pull system incorporated with Kanban system is aproved to be highly effective in manufacturing industries.This research implemented a Kanban system in a highlylabor-intensive apparel manufacturing Industry. Despiteseveral line stoppages due to various problems during theobserved time of 2 weeks, the production output has beenincreased by 22%. Moreover, the correct number of Kanbancards at the Kanban collecting points is an indication of theeffective implementation of the Kanban system.The selected factory had implemented some of the majorlean manufacturing tools and techniques: setup reduction,TPM and TQM are among them. Having implemented thesetools and techniques would be a reason for effectiveimplementation of the Kanban system. If the machinesbreakdowns were high and if the quality issues were high, theKanban cards would not flow as expected. Number ofKanban card at the collecting points together with theimproved production output is an indirect indication of thesuccess of the other tools. As indicated by the skill matrix ofthe operators, the factory has a highly trained work force.Highly trained work force, implementation of major leanmanufacturing tools and techniques are essential componentsfor successful implementation of a Kanban system.17.18.19.20.AUTHORS PROFILERMVS Ratnayake, is currently serving as a SeniorLecturer in the Department of Textile and ClothingTechnology, Faculty of Engineering, University ofMoratuwa. She has obtained a degree in B.Sc.Engineering specializing the Production Engineeringfrom the Faculty of Engineering, University ofPeradeniya, Sri Lanka and a Post Graduate diploma in Operational Researchand a M.Phil. Degree in Lean Manufacturing from the University ofMoratuwa, Sri Lanka. She has worked in a reputed Apparel factory in SriLanka as a Production Engineer for nearly 5 years, just after obtaining thefirst degree.RMVS Ratnayake is a Charted Engineer and a member of the Institute ofEngineers Sri Lanka and a life member of Applied Statistics Association, SriLanka. She has supervised several post graduate researches and currentlysupervising 2 post graduate research projects. She is authorized for morethan 15 journal papers and about 10 conference papers. She renders herservice as a reviewer to many international reputed journals. She is workingas a consultant to the Manufacturing industry in Sri Lanka and have involvedin many consultancy 4.W. J. Hopp and Spearman (2004), Pull or Not to Pull, Manufacturing &Service Operations Management, 2004 Vol. 6, No. 2, pp. 133–148N. Gopalakrishnan, Simplified Lean Manufacture- Elements, Rules,Tools & Implementation, PHI Learning private limited, NewDelhi-110001, (2012), pp 125-126M. P. Groover, Automation, Production Systems and Computerintegrated Manufacturing, Published by Pearson Education Inc., 5thEdition, 2010, ISBN-978-81-203-3418-2, pp 775M. M. Magana, O. T. Everardo, C. C. Wilson and J. L. G. Alcaraz,Impact of the Planning from the Kanban System on the Company’sOperating Benefits, Sustainability, 2018, Volume 10, Issue 7Y. Hirakawa, Performance of a multistage hybrid push/ pull productioncontrol system, International Journal of Production Economics,(1996), Volume 44, Issues 1-2, pp 129-135J. Heizer and B. Render, Lean Manufacturing Case Study with KanbanSystem, Journal of Procedia Economics and Finance, 2005, 7thedition,. pp 174–180T. Ohno, Toyota Production System: Beyond Large Scale Production,Productivity Press, Cambridge, Mass, 1988Y. Sugimori, K. Kusunoki, F. Cho and S. Uchikawa S. ToyotaProduction system Materialization of Just-In-Time and respect forHuman system, The International Journal of Production Research,(2007), 15:6, 553-564, ISSN: 0020-7543M. Shahil, Implications of Just-In-Time systems of Toyota- A casestudy, The final report produce for the Degree of Master of Innovation& Operations Management, 2017, pages 35-37H. W. Harahap, M. F. Marif and Y. Arkeman, Design &Implementation to reduce the finished good inventory, InternationalJournal of Science & Research, 2018, Volume 7, Issue 1N. B. Adnana, A. B. Jaffar, N. B. Yusoff and N. H. B. A. Halim,Implementation of Just in Time Production through Kanban System,International Knowledge Sharing Platform, 2013, Volume 3, No.6N. A. A. Rahman, S.M. Sharif and M. M. Esa, Lean manufacturingcase study with Kanban system implementation. Procedia Econ.Finance, (2013), No.7, pp 174–180.M. D. Al-Tahat, Optimizing of work in progress (WIP) in Kanbancontrolled production lines, Dirasat Engineering Sciences, (2005),Volume 32, No. 2, 123–132Rajat, L. B. Wakode and R. P. Talmale, Overview on KanbanMethodology and its implementation, International Journal forRetrieval Num
Kanban is a card-based control system to convey instructions not to produce until needed [8], [12]. The objective of Kanban is to minimize the inventory of the work in progress (WIP) and the total cost of inventory [1], [13], [14].): it is an effective inventory management system. Kanban