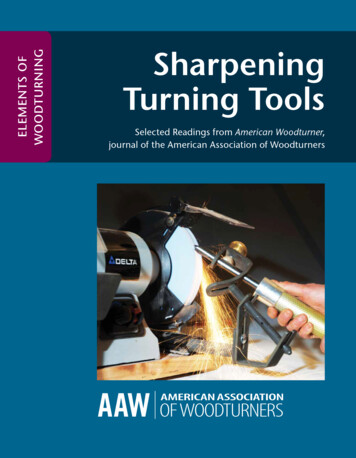
Transcription
elements of woodturningSharpeningTurning ToolsSelected Readings from American Woodturner,journal of the American Association of WoodturnersAmerican Association of Woodturners 222 Landmark Center, 75 Fifth Street West, St. Paul, MN 55102-7704877-595-9094 www.woodturner.org
Contents34Published by American Association of Woodturners,222 Landmark Center, 75 5th St. W., St. Paul, MN 55102-7704.877-595-9094, www.woodturner.org.Copyright 2014 American Association of Woodturners. All rightsreserved. No part of this publication may be reproduced in any formwithout written permission. Readers may create any project for personaluse or sale, and may copy patterns to assist them in making projects. Theinformation in this book is presented in good faith; however, no warrantyis given nor are results guaranteed. American Woodturner magazine andthe American Association of Woodturners disclaim any and all liability.IntroductionThe EditorsLearn to Sharpen All Your Turning ToolsAlan Lacer15Shaping Tool EdgesDavid Ellsworth18Testing the Steel in Turning ToolsAlan Lacer21Grinder WheelsBill Neddow26Comparing Sharpening AlternativesJim Echter32Improving a GrinderBob Vaughan35Jigs Grind Consistent EdgesKirk Deheer38Turners Test Sharpening JigsAAW Members44Safety Lessons: Sharpening JigsJim Rodgers46Virtues of Wet GrindingTerry Martin48Narrow-Belt SharpeningKenneth A. Ray50Shop-Built Sharpening JigsKing Heiple54Shop-Built Wide-Belt SystemJim Echter58Does Honing Pay Off?Alan Lacer & Jeryl Wright64How to Hone Edge ToolsAlan Lacer67Scraper SharpnessAlan Lacer & Jeryl WrightAmerican Woodturner (ISSN 0895-9005) is published bimonthlyby American Association of Woodturners.Sharpening Turning ToolsISBN: 978-1-939662-15-6Printed on Demand in United States of AmericaAmerican Association of Woodturners, www.woodturner.org2www.woodturner.org
IntroductionIt’s often said that a woodworker is only as sharp as his tools,and that’s doubly true for woodturners.Consider a 10-inch bowl blank rotating on the lathe at amodest 600 RPM. The rim of the blank travels at 1570 feet perminute, or about 18 miles per hour. Modern tool steel is amazinglytough and durable, but that’s the same as powering the sharp edgeof a gouge through almost quarter-mile of wood, every minute.No steel could stay sharp for very long.That’s why the lathe demands sharp tools, and why everywould-be woodturner needs to develop a workable sharpeningsystem. Fortunately, as this volume will show, there are severalgood technologies and approaches. For beginners it is a matterof choosing your sharpening procedure, making the investmentto acquire the technology, and learning how to use it. Which iswhere this little book comes in.It’s a common beginner mistake to turn for too long beforesharpening, and consequently to become exasperated by poorresults. The cure is simple: learn how to sharpen, and sharpenoften. Sharpen before you think the tool is dull, not after.Selected Readingsfrom AW JournalFrom its founding in 1986, the American Association ofWoodturners has published a regular journal of advice,information, and good fellowship for everyone interestedin the field. Led by a series of dedicated editors and boardmembers, the AW Journal has evolved to become AmericanWoodturner magazine, now published in full color six timeseach year.The AW Journal is a genuine treasure-trove of practical,shop-tested information written by woodturners for theirfellow woodturners. Sharpening Turning Tools is part of anongoing series being extracted from this archive. SharpeningTurning Tools is available as a 72-page printed book, or as adownload that is readable on all your electronic devices.Safe woodturning is fun woodturning. A little timespent with this book will help you build strong skills at thelathe while teaching you best woodturning practices.www.woodturner.org3
Learn to SharpenAll Your Turning ToolsAlan LacerWDon’t be too bashful in grinding tools. You really can’t hurt them—you only shorten them.and joiner knives, router bits orshaper cutters—either these arethrowaways or cutting tools sentto specialty shops. Even the otherdomain where sharpening wasessential to learn—that of carving—has often been replaced by spinning4 Learn to Sharpen All Your Turning Toolsbits and cutters that require nosharpening, just replacement. Alas,the poor woodturner still mustlearn to sharpen. However, there arenumerous benefits from learningthis skill.www.woodturner.orgAW 18:3, p52, AW 18:4, p56ere these your firstexperiences in sharpeningturning tools? You believed the tools cameready to use? You thought because the adsaid you could turn 4,822 bowlswithout sharpening, theyweren’t kidding? When you did try grinding,the surfaces looked like a flintchipped arrowhead? In frustration, you went out andspent several hundred dollarsfor every grinding jig on themarket, only to discover theyhad not reached the level of apencil sharpener? You sent your tools to asharpening service only tohave them sharpened like asaw blade?Sharpening takes some knocksbecause some turners see it as a taskor chore to be endured and not asa skill—just like turning—that willtake time to learn. The good news isthat sharpening is closely related tothe skill of woodturning.At one time every conceivablewoodworker learned sharpeningskills as part of their activity—whether it be sharpening sawblades, axes, spokeshaves, chisels,or plane irons. Today however, fewcabinet or furnituremakers sharpencircular or bandsaw blades, planer
Here’s how sharpening skillsmimic woodturning: You takea turning tool and place it on atool rest, it meets a round objectapproaching the edge, and youmanipulate the cutting edge. Soundslike what we do as turners, right?Learn the skill to sharpen and you arelearning turning—and vice versa.If sharpening frustrates you,you may need to adopt a tried andtrue learning strategy: a progressionfrom simple and relatively easyactivities to something difficult andmore complex. If you think about it,this is how most skills are acquired.If you take up playing the fiddle,you don’t start with the Brahmsviolin concerto as your first task.You probably start with playingnotes, then scales, Yankee Doodle,and finally progress in difficulty atthe rate of your learning. The samepath that works for learning math,cooking, computers, golf, drawing,driving, and sailing holds true ofsharpening turning tools.The good news to all of thisis that learning those simple tasksfirst has several benefits: Most ofthose tasks are also foundational—not just easy—and will be thebasis for learning the moredifficult maneuvers.I wonder how many folkshave quit woodturning over theyears because they either couldnot sharpen the tools or foundthey spent more time sandingthan turning? So, if you are earlyon in your career as a turner oryou are still frustrated about thissharpening thing, join me and trythis progressive order of learning tosharpening your tools.To begin with, you can’t shapeand sharpen your tools by hand.We can certainly hone the toolsby hand—but honing only keeps asharp tool sharp or regains a smallloss of keenness on a cutting-typeturning tool.www.woodturner.orgWorking with dull tools islike trying to drive your carwith flat tires—it just isn’tvery satisfying.No, power equipment is theorder of the day for a host of reasons,not the least of which is the type oftool steels used today. Most turningtools currently being sold are not justhigher heat-working steels but alsohigher wear-resistant steels. Yourgrandpappy’s Arkansas oil stone isgoing to have a tough go on a GlaserV-15 tool or on most of the English,Canadian, and Australian tools nowon the market. And the fact that toomany tools need major reshapingfrom their new condition, we willneed some power assistance to dothe job.Buying yourgrinder and wheelsI find that it is not as simple as“anything will work” for a grinder.If you have a 3600 rpm grinder witha 120-grit gray wheel, 1/2" wide andworn down to 4" in diameter—it willbe tough sledding. Nor do I find theslow speed water grinders to be myfirst choice for a grinder. Ditto fora belt or disc sander either. At least90 percent of the turners I knowworldwide use a wheel grinder—andfor good reason.Here’s my grinder preference:an 8" dry wheel grinder, witheither variable speed or a fixed rateof 1725 (or 1800), a rock-solid toolrest system, and at least one decentwheel. The 8" wheel offers a lot oversmaller and larger wheels: the 8"has 25 percent more surface areathan a 6" wheel per revolution.This translates to greater efficiency,cooler grinding, and a much longerwear period before replacement.The 10" and greater diameter wheelsleave too little of a hollow-grind forme—and I use the concave surfaceas a two-point honing jig (see Spring2002 article).I prefer the dry wheel as theaction is towards me—this allowsme to determine a lot of things fromthe spark trail: where I am grinding,the degree of grinding, and when tostop grinding (sparks just trail overthe top of the tool). With a watertype grinder, the action is away fromLightMirrorTool restStrong and sturdy tools rests, good lighting, solid mounting and at least one goodwheel are minimal requirements for a reliable grinder. The tool rest on the left is anafter-market rest. A supporting strap was added to the right rest for increased rigidity.Learn to Sharpen All Your Turning Tools 5
me and there is no longer a sparktrail. Those grinders are fantastic forcarbon-steel tools like plane irons,cabinet makers chisels, scissorsand the like—but not a first choicewith most turners. I like the slower1725 speed for a grinder. As I aim toremove minimal material, the 1725speed grinder has a cooler action,and I just find it a more gentle actionthan a 3600 rpm screamer (thoseseem to double my mistakes!). Weare now seeing two-speed grindersand infinitely adjustable grinderson the market, which will probablybe common with most grinders atsome point.If the tool rest assembly is flimsy,I cannot consistently grind my toolsnor is it really safe to do so. Placeyour thumb in the center of thetool rest of your grinder and pushdown. You should feel virtually zerogive—if it feels springy, improve orreplace. You can add extra supportstrapping, build a wooden rest, orpurchase one of several after-marketaccessory rests. Also, the rest shouldbe adjustable both in angle and theability to slide towards the stone toaccommodate for wear as well askeeping the rest close to the stone forsafety purposes. Finally, a light is aworthwhile accessory to the grinderif one did not come attached to it.Thoughts on grindingwheels and dressersWheel dresser examples left to right: graydressing stick, tee diamond, round diamond,star-wheel. In the foreground is a boroncarbide stick.It is challenging to look at a wheel and guess its grit size and hardness. Most stones havea code—in this case, the bottom row of numbers.The most important codes to a turner arecircled. The “54” designates grit size; “J” indicates the hardness designation.First, work with the widest wheelyou can fit to your grinder. In mostcases this is 3/4" or 1"—but the widerthe better. Next, throw away yourgray wheels. Spend a lot or spend alittle, but acquire at least one decentgrinding wheel to sharpen with.The wheels I would suggest arefriable aluminum oxide—now inpatriotic colors of red (okay, oftenpink), white, and blue. The word“friable” refers to the ability of thestone to fracture, exposing freshgrinding surfaces as you use it. Graywheels usually are not very friable,the cutting particles round over, thusreducing grinding ability and oftenglazing and generating considerableheat. The color code of these wheelsmakes them easy to spot. However,there really is a difference between a 10 wheel and 100 wheel.My advice: If you have an 8"grinder look for wheels that sell forbetween 25 and 55 and you’ll befine. Two other critical aspects ofthe wheels: grit size and hardness. Ilike to work with two different gritson my grinder. For initial shaping ofa tool or any other heavy grindingoperation, I rely on a 36- or 46-gritwheel. For the actual process ofsharpening an edge, I prefer eithera 60- (the new 54-grits are closeenough) or 80-grit. My ideal setup6 Learn to Sharpen All Your Turning Toolsis a 60-grit on the left side of mygrinder (I am right handed; reversethis if you are a lefty) and a 36-griton the other side.And finally, how hard shouldthe stone be? Most stones—but notsome of the real cheapies—indicatethe hardness as shown in the photo.This makes a difference in its friablequality and how well it performson tougher steels. Stone hardnessfollows the alphabet scale from softto hard as you go down the alphabet.Most of the stones commonly foundrange from H through K. My firstchoice is a J followed by the K.Almost as critical as a goodstone is a dresser. These are tools thatperform a number of functions: truethe wheel to the axis of your grinder,flatten the face of the wheel, removethe buildup of metal particles, andexpose or sharpen the abrasiveparticles. There are several choices:star-wheel, gray dressing stick, boroncarbide stick, and diamond. I preferthe multiple diamond dresser (not asingle point) in a round or tee shape.Keep it by the grinder, and use itlightly but frequently.Finally, deal with the hazardsassociated with tool grinding.One of the greatest hazards is toprotect yourself from flying particles,whether they are grit from thewheel or pieces of steel removed inwww.woodturner.org
the grinding process. The plasticshields on most grinders areworthless to see through after ashort time—a full face shield is myfirst choice followed by goggles.Only use a grinder with metalshrouds to contain the wheel just incase it shatters into pieces.Another serious hazard is thedust produced from grinding. I liketo think of it as ground up glass. Iknow of no turners who use a wetdust collecting system to direct thegrinding dust into—but this is morecommon with jewelers and othermetal workers. And, of course, don’tdirect the dust into your normalwood dust collecting system—thinkof the drama of sparks and wooddust meeting!What is most common is towear a quality respirator, one ratedfor small particulate matter. Andfinally, keep the pinch and crushfactor to a minimum by alwaysworking with the tool rest as close tothe wheel as possible.60 to 45 bevel angleOrder of learningFrom my own learning and watchinghundreds of students try to learn thesharpening process, I recommendlearning the turning tools inthis order:1. Scrapers (all shapes, but notincluding profile scrapers)2. Parting Tools3. Skew Chisels We’ll cover theabove tools in this issue.4. Roughing Gouges5. Detail Gouges6. Bowl Gouges1. Sharpening scrapersThese are tools, of almost anyshape, that are intended primarilyto cut with a burr and not rub thebevel on the wood. Yes, I know weviolate both of those guidelinesfrom time to time, but that does nothelp someone who is starting out.Of all the turning tools, scrapers areIllustrations: Angelo IafrateOne version of a side-cutting scrapersome of the most straightforwardto sharpen. Few turners strugglewith these tools in getting the basicprocess, and wedon’t have to be too fussy aboutshapes, angles, and multi facets onthe ground face.The first rule of sharpeningturning tools: Profile the tool first,then pull a bevel up to meet thatprofile. For a scraper, personalpreference determines the shape.You will probably discover that theslight dome on a new “round nose”scraper you just bought isn’t veryrounded. You may even find youdon’t use one side of the roundedend, so it may take on the shape ofWoodturning scraping tools are quite similar to the cabinetmaker’s scrapers (background,shown with a burnisher). Both types of scrapers usually cut with a burr and both can makeuse of a burnisher to raise that burr. Turning scrapers are thicker and heavier in weight andcome (or can be made into) in an array of shapes for specific purposes.www.woodturner.orgLearn to Sharpen All Your Turning Tools 7
a side-ground scraper. Whateverthe specific need or your style ofturning, shape the tool first.Next, rough in the bevel angle.When most of these tools are new,I find the bevel to be 80 to even 90degrees below the cutting edge. Ibelieve manufacturers started withthe notion that a scraper needs a lotof support under the edge since youdon’t have the secondary fulcrumof a bevel-rubbing tool to add extrasupport (your tool rest is the primaryfulcrum). Unless your scrapers are1/8" thick, this is a bad notion.As a matter of fact, if I am usingthe tool at a scraping angle (withno bevel support) and the bevelinadvertently touches the wood,I can get a catch. I treat the bevelson scrapers as clearance angles, somine are ground between 45 to 60degrees. I also don’t have to worryabout single facets and a hollowgrind on the ground bevel: I don’thone the bevel on these tools so itis not as critical as it is with otherturning tools. However, grindinguniform bevels on these toolsis great practice for all the toolsto follow.The process for sharpening isstraightforward. After profiling,proceed to grind the bevel tomatch the profile. If you need someassistance early on in sharpening,set the tool rest angle to that 45- to60-degree window. Start at the backof the bevel, keeping the tool flaton the rest, and progress along thecutting edge until sparks just comeover the top. I don’t look for a heavystream of sparks, but consistent“tracer bullets” that tell me I havereached the cutting surface.Being a scraper, the raised burrwill be my cutting edge at least 90percent of the time. I can use theburr right off of the grinder (usefulif heavy stock removal is calledfor) or remove that burr with a flatstone and pull up a new burr witha cabinetmaker’s burnisher or thehoning stone.By using one of the othermethods, I find it easier to producedifferent types of burrs—some forheavy work, some for fine finishingwork. In those cases where the burris too aggressive for a particularpiece of wood (you may feel it“picking” at the wood rather than asmooth leveling action), try scrapingwith a sharp edge—produced bygrinding—then removing the burron top with a flat honing stone. Thisis similar to the action of scrapingwith the edge of a knife or thefurnituremaker scraping the top ofa table with a large piece of brokenglass. When you work a sharp edgein a scraping action, it may quicklydull the edge. However for thatwindow of doing fine scraping, itmay be just the ticket.2. Parting toolsThere are several variations of thistool, but the most common is arectangular section of steel with thecutting edge in the middle that’sground on both sides. This is a greattool to learn cutting tool sharpeningas it has a relatively small area togrind (the edge is usually no greaterthan 1/4") and the edge is in aflat plane.For profiling, make sure the edgeis ground straight across, and theincluded angles of the ground bevelsare around 25 degrees. Fortunately,new parting tools most often arriveprofiled in an acceptable manner—not sharp mind you, but routinelyshaped fine. To sharpen, either setthe tool rest at the approximateangle desired, use the edge of therest as a steady, or use your fingers toadjust the angle.Start at the back of the bevel(called the “heel”), keep the edgehorizontal, and lap from side toside on the wheel until you justsee sparks trailing over the top of8 Learn to Sharpen All Your Turning Tools25 angleDiamond-section parting tool (profile andangles same as rectangular tool)the cutting edge. Flip over the tooland repeat the same procedure onthe other side. The objective is toproduce a single facet with a slighthollow grind. If your movementsare controlled and steady, thisall happens. If jerky, uneven,inconsistent, too much pressure,“grind and look” and “grind andlook,” then things probably won’t beso good.Go slow, be deliberate, leavethe tool on the wheel, and use onlyenough pressure as it takes to keepthe tool from bouncing on the rest.I am always surprised how muchof grinding and turning is reallyabout feeling your way along ratherthan seeing.In grinding, most of the actionis on the other side of what you cansee. We can help the looking partalong—especially when learningthe process—by placing our head tothe side of the grinder or by the useof a mirror (attributed to a NorthCarolina turner). In time, most ofyour grinding will be by feel andwatching the spark trail to give theadditional feedback.www.woodturner.org
3. Skew chiselsFortunately, the sharpening of askew chisel is similar to the partingtool: two ground flat planes thatmeet to form a cutting edge. Theonly real difference is in the skewedangle of the cutting end—essentiallya clearing and viewing advantageover a square-across chisel.Again, profile the tool first. Fora “traditional” straight-edged skew,I recommend 70 degrees from pointto point. Rather than measuringincluded angles to measure thesteepness of the two ground bevels,I use the thickness of the steel as thereference. Using this method, grindthe bevels back to approximately1.5 times the thickness of the blade.For the sharpening process,follow these steps: Keep the edgehorizontal and parallel to the faceof the wheel, start at the heel andlap back and forth. Continue thisprocess until sparks just trail over theedge. Flip over the tool and repeatthe same procedure.If you have an “oval style” skew(my last choice for a skew) you willfind it wants to wobble rather thanremain in a flat plane. In that case,maintain pressure in the center ofthe tool with a thumb to essentiallylock it into a fixed plane. As analternative, investigate a grinding jigthat locks the darn thing in place.If you are grinding a curvededged skew, simply grind the edgewhile it is generally parallel to theface of the wheel. This will requirea rotational motion that follows thecurve of the edge. If the skew plaguesyou with multiple facets, go aheadand set the tool rest to the suggestedbevel angle. Keep the tool flat on therest and follow the above strategies. Ihave had good success just using thefront or back edge of the tool rest asa point to slide along for a straightskew or to pivot on while grindinga curved edge.www.woodturner.orgBevel length:Thickness of blade x 1.5Approximately 70 from point to pointUntil you have a sense of where you aregrinding on the tool, it’s helpful to eitherplace your head to the side of the wheel ormake use of a small mirror. The mirror, shownabove, allows you to see your placement ofthe tool on the wheel.Typical grinding of a skew chiselUsing the back edge of the tool rest, pivot the curved skew to grind the edge. Using arotational movement, grind in the area that is roughly parallel to the face of the wheel.Learn to Sharpen All Your Turning Tools 9
Tests for sharpnessof cutting toolsIf you can see the edge, there is noedge. Short of turning, this is thebest test I know. Use an incandescentlight to check for any reflectionalong the edge; a sharp edgedisappears into a black line. Dullspots will reflect light.What comes off the tool, dustor curls? Even in dry material, asharp tool forms a longer chip orribbon, dull tools produce dustor very short chips.How much effort does it requireto remove the material? Unlessyou are roughing out a large piece,a sharp tool presented at the rightangle is almost effortless; a dull toolrequires more force.What does the cutting actionsound like? A sharp tool makes asound reminiscent of a sharp handIf you can see the edge,there is no edge.plane; the dull tool sounds flat ormakes a scraping sound.How clean is the surface whenyou stop the lathe for inspection?Sometimes it is a difficult piece ofwood, but generally a sharp toolgives far superior results to thesurface of the wood.4. Spindle roughing gougeThe spindle roughing gouge isperhaps the friendliest gouge to useand one of the easiest to sharpen.It differs from all the previous tools(Fall 2003 issue) as we are now intocurved edges. Traditionally, the toolis a deep U-shape with a straightacross cutting edge.Profiling is fairly straightforward. Make sure the tool isstraight across when viewed from thetop and viewed from the side. Youcan have the top corners canted backa few degrees, but not canted forward(a forward cant will make a moreaggressive tool). The bevel angleshould be approximately 45 degrees.Sharpening begins at onecorner, with the heel of the beveltouching the wheel and the cuttingedge parallel to the face of thewheel. Rotate the tool in the samecurved plane until you reach theother corner, then return to thepoint where you began by rotatingbackwards (but still grinding) toyour original motion. I tend to repeatthese motions until I have lappedall the way to the cutting edge. Stopwhen the sparks just trail over thetop of the edge.Notes on overheating the toolBy now you may have come up against the problemof bluing the grinding surface of the tool. If you havehigh-carbon steel tools, you have a problem: thesteel has now been re-tempered to a hardness thatis too soft to hold an edge for woodturning. If youhave high-speed or high-heat-working tool steel—noproblem. But how do you know what kind of steel?Generally the high-carbon tool steels produce acomplex, white, bursting spark when placed on thegrinding wheel. The high-speed steels tend to haveindividual, orange sparks. Often the manufacturerstamps the handle or steel itself with “HSS” or “HighSpeed Steel.” I have found some inexpensive importedtools stamped with those designations, but sparkedlike high carbon tools—so be careful.carbon steel tools—and some of my old favorites areof that steel—quench in water frequently for heavygrinding or delicate points of skew chisels.If you have high-speed tools, don’t quench in water:the effect may be too shocking for the steel andpossibly produce small fractures at the cutting edge.The high-speed steels easily handle temperatures of700 to 1000 degrees F with no loss of hardness (bluingis around 580 degrees F). If the high-speed tools gettoo hot to handle (during heavy grinding), I just placethem on a large metal heat sink like a lathe bed andtake a short break. The best rule for all steels is learnto work without generating a lot of excessive heat andeliminate the need for quenching.Here are some suggestions regarding overheating.First, learn to grind with a lightness of hand andmovement of tool that does not overwork an area,thereby reducing heat. Second, use friable wheels thatgrind cooler, and dress the wheel often. If you have10 Learn to Sharpen All Your Turning Toolswww.woodturner.org
Grind the beveland not the edge.On the larger roughing gouges,some turners like to work aboutone third of the edge at a time untilthat section is fully sharpened.They make one final pass along theentire length of the bevel to blendit all together. The biggest problemturners seem to have is moving thetool edge in and out when trying torotate the tool through that largecurved plane. Use your fingers tocreate an artificial plane to lockthe tool in. If you have troublestaying in that 45 degree bevel zone,set the angle of the tool rest andmaintain downward pressure tokeep the tool flat and thereby in thecorrect orientation.If by chance you have a largeshallow gouge (3/4" or larger) thatwas packaged in your tool set asa roughing gouge, here are mysuggestions. Odds are pretty goodit has a domed edge (maybe almostlooks like your thumbnail). Youmight consider simply grindingit straight across and sharpeningas suggested for the deep-flutedroughing gouge.If you decide to leave it withthat “fingernail” look—in order todo some detailing work such as largecoves or beads— then approach it theway you would the detail gouge.Detail gouge30ºSide viewTop view5. Detail gougeWhat’s in a name? A shallow flutedgouge with a fingernail shape-primarily designed for spindle workand used for detailing work--willbe the same tool no matter whatwe call it. I wish we could some daystandardize a few names for turningtools, but that’s a lot to ask for. Thistool goes by at least four names:detail gouge, spindle gouge, shallowgouge, and fingernail gouge. All ofthese names point to some truthabout it, but still leads to muchconfusion. For this article, it’s adetail gouge.This detail gouge is probablythe first tool to get your goat. (ItAt right are improperly ground gouges:A: A detail gouge ground too pointy. Thisis caused by either rotating the entire toolparallel to the face of the grinding wheel (aswith a roughing gouge), or over grindingthe sides.B: A bowl gouge ground on the side with aconcave profile. This makes an aggressivetool and one that does a poor job of levelingif used to shear scrape.ABCC: A roughing gouge overground along theedge. This most often shows up as a jaggedor saw-toothed edge.www.woodturner.orgLearn to Sharpen All Your Turning Tools 11
Give a protractor a try.We got a few letters after lastissue’s grinding article aboutgrinding the correct angle. Thismetal protractor—available forabout 12—is one inexpensiveand reliable solution.was the first tool I‘m aware of thata grinding jig was developed to dothe sharpening.) No tricks of settingthe tool rest at the right angle willhelp, nor will simply rotating thetool back and forth. Nope, we nowhave a tool that is in an oval planewith the steel below the edge invarying thicknesses.Let me explain. If I shape thetool into a fingernail shape, orientthe tool with the flute facing thegrinding wheel, and rotate it alonga circular path that is parallel to theface of the wheel, I will probablyproduce a pointy or “spear-pointed”cutting edge that is not very versatilenor friendly to the user.Profiling is essential to thedetail tool. It performs astutely informing concave and convex formsin between center work or detailson feet, bases and rims of bowl andvessel work. The shallow draft of itsflute (a low “sweep” if we are talkingto carvers) allows the tool to sneakin between details, often on its sideand do
good technologies and approaches. For beginners it is a matter of choosing your sharpening procedure, making the investment to acquire the technology, and learning how to use it. Which is where this little book comes in. It’s a common beginner mistake to turn for too long before sharpening