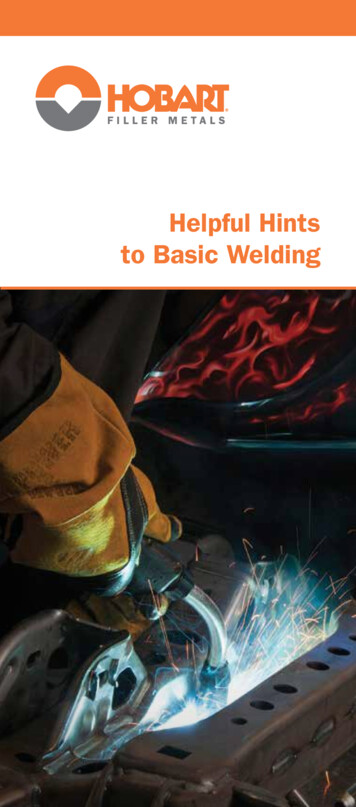
Transcription
Helpful Hintsto Basic Welding
F O R E W O R DThis guide, and all the informationcontained within, is intended to provide you withhelpful hints for basic welding. It is not intendedas a comprehensive manual, nor does it containthe scope of information needed for commercialor industrial welding purposes.If you are not familiar with the safety practices,procedures and techniques of basic welding,you will need to supplement this guide withadditional reading material and/or enroll in abasic welding course.For any welding that involves the protection oflife, limb or property, always seek the servicesof a competent professional welder.
T A B L EO FC O N T E N T SEveryday Welding Applications.2Welding Safety.3Stick or Wire: Which is Your Welding Preference?.4Basic Stick Welding – A Quick Review.5Stick Electrodes.5Equipment and Tools.6Techniques.6Setting the Amperage.7Striking an Arc.7Electrode Angles.8Arc Length.8Travel Speed.97 Factors in Selecting Arc Welding Electrodes.9Filler Metals Selector Guide.10Examples of Good and Bad Stick Welds.12Wire Welding – A Quick Review.14Wire Electrodes.14Equipment and Tools.15Techniques.15Wire Polarity.16Wire Feed Speed and Voltage.16Initiating an Arc.17Electrode Stick-Out.17Electrode Angles.17Welding Gun Manipulation.18Travel Speed.19Shielding Gases and Their Welding Advantages.19Examples of Good and Bad Wire Welds.201
EVERYDAY WELDING APPLICATIONSWelding is an efficient and easy way to cut down onmaintenance or repair costs associated with metalequipment around the house or farm. Through welding, youcan repair a wide variety of things including:Home Improvement Lawnmower decks and handlesDuctworkFencingSteel patio furnitureGarage door tracks and bracketsWheelbarrowsRecreationHarrow disk repair with Hobart 335Astick electrodes Basketball rims and postsSwing setsTrampolinesWagonsSnowmobile skis and skagsBicycles and tricyclesAgricultural Four-wheeler repair with Hobart’sHB-28 solid wireCombinesGrain wagonsBalersFarm equipment framesTractors and trailersGalvanized roofingTrailer hitchesTrailer frames and sidesAutomotive TailpipesMotorcyclesBumpersTrailer hitchesAuto bodies and door bracketsHelpful Hint #1Before starting any welding project, be sure you readabout welding safety!2
WELDING SAFETYAlways remember welding is serious business! Make sureyou protect yourself by following these important safety tips:Always wear protective clothing!Wear a heavy cotton shirt, cuffless trousers, high shoes anda cap to protect yourself while weldingor removing slag.Always wear a weldinghelmet with visor shade #10or darker!Arc rays from the welding processproduce intense visible and invisible(ultraviolet and infrared) rays that canburn eyes and skin. NEVER WELDWITHOUT PROPER EYE PROTECTION!Always wear safety glasses!Wear safety glasses with side shieldsto protect your eyes while weldingand removing slag.Always wear leatherwelding gloves!Wear gloves to protect your handsand wrists from hot sparks andradiation burns while welding andremoving slag.Weld in a well-ventilatedarea fumes and gases canbe hazardous!Welding may produce fumesand gases that can make you ill. Besure to keep your head out of thefumes – do not breathe the fumes!Keep weld area freeof flammables!Move paint, solvent, gasoline, paperproducts and other flammables awayfrom the weld area so they won’tcatch fire from sparks and hot slag.3
Protect others!Set up protective screens or barriers to protect other personsfrom flash and glare; warn others not to watch the arc.When welding small parts, donot weld on the garage floor ordriveway use a welding table!The heat generated by the electric arc cancause cement to explode or set asphalton fire.Do not weld on tanks or containers thatpreviously held flammable materials!Even though it may be empty, a tank or container thatpreviously held a flammable material may still containcombustible vapors or residue that can result in anexplosion.Be familiar with your welding equipment!Understanding how to properly operate welding equipmentprotects you from harm and your equipment from damage.Helpful Hint #2To learn more about basic welding, call theHobart Institute of Welding Technology!For course information, call 937.332.5000 or 800.332.9448,or visit their web site at www.welding.orgSTICK OR WIRE: WHICH IS YOURWELDING PREFERENCE?There are several different welding processes that are idealfor projects around the house of farm: Stick welding – properly known as SMAW (ShieldedMetal Arc Welding) Wire welding – properly known as GMAW (Gas MetalArc Welding) or FCAW (Flux-cored Arc Welding)All of these processes involve the joining of metals by meansof an electric arc. This electric arc, at a temperature of about10,000 F, melts both the metal electrode and the base metal(the metal being welded) together, producing a molten weldpuddle that quickly solidifies to form the weld.4
S T I C KW E L D I N GAlthough these processesdepend on the use of anelectric arc, they differ intechnique, including the typeof electrode and equipmentrequired. Stick welding is amanual arc welding processin which a covered metal stickelectrode is used as the fillermetal for making the weld.Wire welding is consideredas a semi-automatic process,using a wire electrode that’sconveniently fed througha welding gun.Front-end loader repair with Hobart 18ACstick electrodeStick welding requires youto have more skill becauseyou have to consistentlyconcentrate on the electrodewhile you are welding, keepingit in the proper welding positionand manually maintainingthe proper arc length as theRepairing farm equipment using Hobart’selectrode gets shorter.Champion and 418 stick electrodes.Wire welding is considered tobe somewhat easier than stickwelding because the weldinggun continuously feeds the wire while you weld, allowingyou to focus on gun position for maintaining the proper arclength. Plus, you don’t have to worry about the electrodegetting shorter.Whether you prefer stick welding or wire welding the welding process you use is most likely the oneyou have the most experience with or have the equipment for.Stick welding(properly knownas Shielded MetalELECTRODEHOLDERArc Welding orSMAW) requiresuse of a coveredMETAL RODSTICK ELECTRODEstick electrode, aFLUX COATINGWELD BEADmetal rod that’sSLAGGAS SHIELDINGcoated with aELECTRIC ARCmaterial calledGROUNDEDWORKPIECEflux. An electrodeMOLTEN WELD PUDDLEholder is used tohold and supplycurrent to the stick electrode, causing it to melt and depositmolten metal. As the electrode melts, the flux coating breaksdown to perform several functions: 1) form a gas shielding5
S T I C KW E L D I N Gto protect the weld puddle from the air,2) keep the weld puddle clean fromcontaminants, and 3) produce a light,protective coating, called slag, over theweld. The slag is removed by tapping theweld with a chipping hammer or chiseland cleaned off with a wire brush.5-lb. Plastic Paks of Hobartstick electrodesStick electrodes ideal for various homeand farm welding projects includeHobart’s 335A, 18AC, 418 and 447A.These premium stick electrodes aregreat for many different applications andcome in a variety of diameter sizes. Fora list of product applications, see pages10-11.Equipment and ToolsIn stick welding, the equipment and toolsthat are required are: power source welding machine –complete with welding cable, electrodeholder and ground cable and clamp chipping hammer or chisel, and a wirebrush (for removing slag)Repairing farm fencing in the fieldusing Hobart’s 418 stick electrodes protective clothing including helmetand glovesHelpful Hint #3If you have to use an extension cord to get power to yourwelding equipment, make sure the cord is the correct sizeto carry the current from the outlet to the power supply!TechniquesTo produce a good quality weld, it isimportant to master the following stickwelding techniques. the first thing youshould do before you start weldingis make sure the workpiece – theitem you are welding – is as clean aspossible. Use a clean cloth, wire brush orsandpaper to remove any rust, dirt, paint,grease, oil or other contaminant. Do notuse cleaning solvents because you canrun the risk of an explosion or fire, orGreat for many applications, Hobartillness from toxic vapors.18AC features a smooth, stablearc and offers excellent re-strikingcapabilities.6
S T I C KW E L D I N GHelpful Hint #4Be sure to connect the ground clamp of your weldingequipment to the workpiece before you start welding!Setting the AmperageSelect the proper amperage based on the specifications ofthe stick electrode. Sometimes, you may find that you have to“fine tune” the setting so that the electrode melts properly.The best way to check this is to perform some test welds onsome scrap metal and look at the weld. If you notice that theweld is piling up or you see signs of burn-through (holes in thebase metal), then the amperage is probably set too high; not penetrating the joint (little depth) or not fusing to theworkpiece (doesn’t cover joint walls) properly, then theamperage is probably set too low.Striking an ArcTo strike an electric arc, bring thetip of the stick electrode near whereyou want to start the weld. Almostlike striking a match, strike the stickelectrode slightly across the workpieceuntil you have established an arc.Once you have an arc, be sure to keep the electrode slightlyabove the workpiece, otherwise it will stick and you will haveto break the electrode free of the workpiece. If you havetrouble striking an arc, you may be lifting the electrode toohigh off of the workpiece, causing the arc to go out.The most important thing you want to do after you’ve initiatedthe arc is to maintain proper position of the electrode andarc. This involves three key factors, namely: electrode angles arc length travel speedHelpful Hint #5Position the ground clamp on the workpiece so thatyou will be welding away from the clamp. This will helpkeep arc blow (interference from magnetic fields)to a minimum when using DC current.7
S T I C KW E L D I N GElectrode Angles45 10 -15 TRAVELElectrode angles are the angles at whichyou should hold the stick electrode inrelation to the workpiece while welding.These angles differ depending on the typeof weld you intend to make.For instance, when doing a lap weld (onepiece of metal overlaps another) or aT-weld (joining two metals to form a ‘T’),hold the electrode so that so that it pointsinto the weld joint at an angle of 45 .When you start welding, angle it 10-15 toward the direction of travel until youcomplete the weld and terminate the arc.For butt weld (joining two pieces of metalbutted together), first hold the electrodeso that it is pointing into the joint of theworkpiece at an angle of 90 . Then, as you start welding,angle the electrode so that it is pointing 10-15 in thedirection of travel (see illustrations above). When completingthe weld, bring the electrode back to 90 and lift it toterminate the arc.T-weld with 45 work angleand 10 -15 travel angleSpatterArc LengthMaintaining theproper arc length isanother key factorToo ShortNormalToo Longin producing a goodArc lengthsquality weld. Thearc length is thedistance from the end of the stick electrode to the surfaceof the molten weld puddle. Be careful to watch the stickelectrode as you weld because as it becomes shorter andshorter, you have to keep moving the electrode toward theweld joint to maintain the proper arc length.A good rule of thumb to follow is: try to keep the end of theelectrode at a distance from the joint that’s approximatelyequal to the diameter of the stick electrode. For example,if the stick electrode you are using is 1/8" in diameter, thenkeep the end of the electrode about 1/8" from the moltenweld puddle.Keep in mind that an arc length that is too long makes acoarse, uneven cracking sound that will often go out. You willalso see an excessive amount of spatter (metal particlesoutside the weld) and the weld will be too wide.A short arc makes a soft buzzing noise and produces aweld that is too narrow. In some cases, the stick electrodewill stick to the workpiece. If this happens, move thestick electrode side to side and pull it to free it from theworkpiece.8
S T I C KW E L D I N GHelpful Hint #6Arc re-starts are much more effective when the flux coveringat the end of the stick electrode is flush with the metal rod.Travel SpeedTravel speed is the rate at which you weld. A good travelspeed produces a uniform weld that is slightly convex inappearance. However, if you travel too slow, the weld will pileup, wasting filler metal. If you go too fast, the weld will benarrow and lack proper penetration and fusion.Helpful Hint #7For examples of good and bad welds,along with descriptions and illustrations of commonstick welding defects, see pages 12-13.7 FACTORS TO CONSIDER INSELECTING ARC WELDING ELECTRODES1. Base Metal Strength PropertiesKnow and match mechanical properties. Mild steel –generally E-60XX or E-70XX electrodes match base metal.Low alloy steel – select electrodes that match base metalproperties.2. Base Metal CompositionKnow and match composition. Mild steel – any E-60XX orE-70XX electrode is satisfactory. Low alloy steel – selectelectrode that most closely matches base metal composition.3. Welding PositionMatch electrode to welding position encountered.4. Welding CurrentMatch the power supply available. Some electrodes aredesigned for direct current (DC); others, alternating current(AC); some, either. Observe correct polarity.5. Joint Design and Fit-upSelect for penetration characteristic – digging, medium, orlight. No beveling or tight fit-up – use digging. Thin material orwide root opening – light, soft arc.6. Thickness and Shape of Base MetalTo avoid weld cracking on thick and heavy material ofcomplicated design, select electrode with maximum ductility.Low hydrogen processes or electrodes are recommended.7. Service Condition and/or SpecificationsDetermine service conditions – low temperature, hightemperature, shock loading – match base metalcomposition, ductility and impact resistance. Use lowhydrogen process. Also, check welding procedure orspecification for electrode type.9
GENERALRECREATIONALHOME IMPROVEMENTAGRICULTURALAUTOMOTIVEF I L L E R10M E T A L SApplicationThickness Stick Electrode/Dia/AmpsAuto BodyAuto Door BracketsAxlesBumpersMotorcyclesTailpipesTrailer HitchesTrailer FramesTrailer SidesTrailersBalersCombinesFarm Equipment FramesGalvanized RoofingGrain WagonsLawnmower DecksLawnmower HandlesWheelbarrowsDuctworkFencingGarage Door TracksGarage Door BracketsSteel Patio FurnitureBasketball BracketsBasketball PostsBasketball RimsBicyclesSnowmobile Skis & SkagsSwing SetsTrampolinesTricyclesWagonsAngle IronSheet 16"3/64"1/16"1/8"-3/8".022"-1/8"N/A335A/3/32" / 50-10018AC or 418/ 1/8" /90-14518AC or 418/ 1/8" /90-14518AC or 418/ 3/32" /80-100447A/ 3/32" /40-8518AC or 418/ 1/8" /90-14518AC or 418/ 1/8" /90-150447A/ 3/32" /40-8518AC or 418/ 1/8" /90-15018AC or 418/ 1/8" /90-14518AC or 418/ 1/8" /90-14518AC or 418/ 1/8" /90-145335A/ 3/32" /50-10018AC or 418/ 1/8" /90-145335A/ 3/32" /50-100447A/ 3/32" /40-60447A/ 3/32" /40-85N/A335A/ 3/32" /50-100447A/ 3/32" /40-8518AC or 418/ 3/32" /40-9018AC or 418/ 3/32" /50-9018AC or 418/ 1/8" /90-145335A/ 3/32" /50-10018AC or 418/ 1/8" /90-145447A/ 3/32" /40-6018AC or 418/ 3/32" /50-90447A/ 3/32" /40-85447A/ 3/32" /40-85447A/ 3/32" /40-60447A/ 3/32" /40-8518AC or 418/ 1/8" /90-145447A/ 3/32" /40-85
S E L E C T O RG U I D /.035"/80-200HB-28/.024"/25-110HOME IMPROVEMENTFabshield 21B/.030"/30-85Fabshield 21B/.035"/50-100N/AN/AN/AFabshield 21B/ .035"/ 30-85N/AN/AFabshield 21B/ .035"/ 50-100N/AFabshield 21B/ .045"/ 80-180Fabshield 21B/ .035"/ 30-150N/AFabshield 21B/ .030"/ 30-100Fabshield 21B/ .045"/ 80-180Fabshield 21B/ .045"/ 80-150Fabshield 21B/ .030"/ 30-100Fabshield 21B/ .035"/ 50-100Fabshield 21B/ .030"/ 30-85Fabshield 21B/ .045"/ 80-180Fabshield 21B/ .035"/ 50-100Fabshield 21B/ .035"/ 50-150Fabshield 21B/ .045"/ 80-180Fabshield 21B/ .045"/ 80-180Fabshield 21B/ .035"/ 50-200Fabshield 21B/ .045"/ 80-180Fabshield 21B/ .030"/ 30-100Fabshield 21B/ .035"/ 50-150Fabshield 21B/ .035"/ 50-150Fabshield 21B/ .035"/ 50-150Fabshield 21B/ .030"/ 30-100Fabshield 21B/ .035"/ 50-150Fabshield 21B/ .045"/ 80-180Fabshield 21B/ .030"/ 50-150AGRICULTURALSolid Wire/Dia/AmpsAUTOMOTIVEFlux-Cored Wire/Dia/Amps11
S T I C KW E L D I N GEXAMPLES OF GOOD AND BADSTICK WELDSGOOD WELDProper voltageand travel speedBAD WELDWelding currenttoo lowBAD WELDWelding currenttoo highCROSS-SECTIONCROSS-SECTIONCROSS-SECTIONWeld FaceWeld FaceWeld FaceSmooth andwell-formedNarrow andconvexWide and flatwith excessivespatterUniform contourIrregular contourGoodpenetrationand fusionPoorpenetrationand fusion12Very irregularcontourUndercuttingalong edges
S T I C KW E L D I N GBAD WELDTravel speedtoo fastBAD WELDTravel speedtoo slowCROSS-SECTIONCROSS-SECTIONWeld FaceWeld FaceNarrow andconvexExcessively wideand flat, porousIrregular contourIrregular contourPoorpenetrationand fusionExcessivepenetrationalong edges13
W I R EW E L D I N GWIRE WELDING – A QUICK REVIEWWelding fabrication using theHobart Ironman 250 with HobartHB-28 solid wire2-lb. spool ofHobart’s HB-28solid wireWire welding is a semi-automaticprocess in which a continuous wireelectrode is automatically fed through awelding gun. By simply positioning thegun near the workpiece and depressingthe trigger, you can initiate an arc andmaintain the automatic feeding of thewire electrode while you weld until yourelease the trigger.Among the many types of wireelectrodes available on the market,the two best suited for homeand farm welding are solid wireelectrodes and flux-cored wireelectrodes. If you use a solidwire electrode, then you aredoing what is known as MIGwelding (properly known as gasmetal arc welding or GMAW).10-lb. spool box ofHobart’s FabshieldIf you use a flux-cored wire21B flux-cored wireelectrode,then you are doingflux-cored welding (also calledflux-cored arc welding or FCAW).Wire ElectrodesA solid wire electrode, likeHobart’s HB-28, requiresWELDING GUNuse of a shielding gas toprotect the molten weldNOZZLEpuddle from impurities inthe atmosphere, namelyoxygen and nitrogen. As aresult, no slag is produced.SOLID WIREELECTRODECommon shielding gasesMETALGAS SHIELDINGDROPLETSfor solid wire applicationsELECTRIC ARCWELD BEADGROUNDEDinclude 100% CO2, (carbonWORKPIECEdioxide) and 75% Ar/25%CO2 (75% argon and 25%MOLTEN PUDDLEcarbon dioxide); however, there are also other commerciallyavailable mixed-gas combinations that ca be used.Helpful Hint #8Refer to the wire manufacturer’s recommendations forshielding gas or see page 19 for how a specific shielding gascan enhance the welding process.Flux-cored wires, such as Hobart’s Fabshield 21B, aredifferent from solid wires in that they have a center coreof flux. This flux, when melted, creates a shielding gasto protect the molten weld puddle from oxygen and other14
W I R EW E L D I N Gimpurities; hence, noexternal shielding gas isrequired.* Any impurities inthe weld are brought to theweld surface in the form ofa thin covering called slagwhich should be removedwith either a chippinghammer or chisel andcleaned off with awire brush.WELDING GUNNOZZLEFLUX-CORED WIREELECTRODEMETALDROPLETSWELD BEADSLAGELECTRIC ARCGAS SHIELDGROUNDEDWORKPIECEFlux-cored wires that do notMOLTEN WELD PUDDLErequire shielding gas are calledself-shielded wires; however,there are flux-cored wires thatdo not require use of a shielding gas, but these are primarily used forindustrial applications in which the shielding gas helps the weld metalattain certain characteristics.*Equipment and ToolsIn wire welding, the equipment and tools that are required are: Power source welding machine –complete with welding gun and guncable assembly; automatic wire feederand control system; and ground cableand clamp Shielding gas system* that consists ofa gas cylinder, regulator, flowmeter andgas hose Wire cutters, chipping hammer orchisel, and wire brush Proper clothing including helmetand glovesAutomotive repair using theMillermatic 211 and HB-28solid wireNot required for Fabshield 21B.*Helpful Hint #9While welding, be sure to keep your gun cable as straightas possible to avoid erratic arc behavior.TechniquesTo produce a good quality weld, it is important to master thefollowing wire welding techniques. However, before startingany welding project, make sure the workpiece – the item youare welding – is as clean as possible. Use a clean cloth,wire brush or sandpaper to remove rust, dirt, paint, grease,oil or any other contaminant. Do not use cleaning solventsbecause you run the risk of an explosion or fire, or illnessfrom toxic vapors.15
W I R EW E L D I N GWire PolarityBe sure to check the wire manufacturer’s instructions for wirepolarity and set the power source accordingly. If the powersource is not set for the proper polarity,you may end up with a poor qualityweld.HB-28 solid wire requires the powersource to be set for DCEP (DC current,electrode positive) or else the weldmay lack penetration and have poorappearance due to excessive spatter.Shop repairs made easilywith Hobart’s HB-28solid wireFabshield 21B wire requires the powersource to be set for DCEN (DC current,electrode negative); otherwise, the weldmay be porous and produce slag that isdifficult to remove.Wire Feed Speed and VoltageSelect the proper wire feed speed (amperage) and voltagebased on the specifications of your wire electrode.Sometimes, you may need to “fine tune” the settings. Thebest way to check wire feed speed and voltage settings is toperform some test welds on scrap metal and check the weld.Be sure that you do not use wire feed speed that is set too fast as it willcause too much metal to be deposited, wasting filler metal orresulting in possible burn-through;do not use wire feed speed that is set too low because it willproduce a weld that doesn't penetrate or fill the joint properlyand may cause the wire to “burn back” or melt at the tip;do not use voltage that is too high because it will createa flatter, wider weld bead that is porous, plus excessivespatter. In addition, high voltage can cause undercutting,a groove melted into the workpiece that doesn't get properlyfilled with weld metal;do not use voltage that is set too low or the weld bead will benarrow and lack proper penetration and fusion.Helpful Hint #10Listen to the arc for an indication of whether or not you arewelding properly. A good arc sound is one that is consistent andsounds like bacon frying. If you hear excessive popping andcracking, it’s a good indication that the electrode is sticking toofar out of the gun or the wire feed speed is too fast.16
W I R EW E L D I N GInitiating an ArcTo initiate an arc, simply position the gun close to the weldjoint and depress the trigger.Once the arc is initiated, pay close attention to the followingkey factors in achieving a good quality weld: electrode stick-out electrode angles welding gun manipulation travel speedElectrode Stick-OutElectrode stick-out is thelength of unmelted wireNOZZLEcoming out of the contact tipCONTACTof the welding gun. It affectsTIPthe amount of amperageSTICK-OUTdrawn by the wire and isimportant because it canaffect the outcome of yourweld. Determining how muchstick-out to use depends onthe diameter size of your wire.For instance, a good guideline to follow is: for .024" and.030" wire, use 3/8"-1/2" stick-out; for .035" and .045"wire, use 1/2"-5/8".You can make slight adjustments to the stick-out to “fine-tune”the amperage for the result you want. For instance, bylengthening the stick-out, you slightly decrease theamperage; by shortening the stick-out, you slightly increasethe amperage.Electrode AnglesIn wire welding, you want tobe sure that you properlyposition the wire electrodeover the weld joint formaximum coverage. Thisinvolves paying specialattention to the work angleand the travel angle.45 Lap weld with 45 work angleThe work angle is the angleat which the wire is pointingat the weld joint. For lap andT-welds, the work angle is45 , for butt welds, it is 90 .90 Butt weld with 90 work angle17
The travel angle is theangle of the wire as ittravels along the weldpath. For most wirewelding applications,this angle is 15-30 .15 -30 DragTRAVEL15 -30 drag level angleFor home and farmwelding applications,the travel angle mostcommonly used is calleda drag angle, when theelectrode is pointing in adirection that’s oppositethe arc travel.Helpful Hint #11While welding, be sure to keep your gun cable as straightas possible to avoid erratic arc behavior.Welding Gun ManipulationHow you manipulate the welding gun, therefore the electrode,is another key factor in producing a good quality weld.For lap and T-welds,manipulating the gun tocreate a series of smallovals provides goodwelding coverage. Becareful not to move toofar back into the weldpuddle or else fusionproblems may occur.Oval pattern for lap and T-welds“Z” pattern for butt joints18For butt joints,manipulate the gunso that the electrodemoves in a ‘Z’ patternwhile traveling alongthe workpiece. Thispattern is most effectivebecause it produces aflatter weld, spreadingthe molten weld puddleevenly across the joint.
Travel SpeedTravel speed is the rate at which you weld. As you weld, watchthe molten weld puddle and listen to the arc for evidence oftraveling too fast or too slow. Moving at a high travel speedor too fast causes insufficient penetration, plus you’ll hearpopping sounds as the wire comes into contact with the coldmetal just ahead of the puddle. Welding at low travel speeds,or moving too slow, will cause the weld metal to pile up,resulting in poor fusion. (See pages 20 and 21 for examplesof good and bad welds.)Shielding Gases andTheir Welding Advantages100% CO2provides broadpenetration andreduces the chanceof porosity75-80% Ar/20-25% CO2allows high weldingspeeds withoutburn-through, andwith minimaldistortion and spatterFor more than 80 years, Hobart has dedicated itself toproviding the technology, the expertise and the commitment toquality required to keep pace with an evolving welding industry.And it’s because of this dedication that welders choose Hobartfirst because they know that with every Hobart product theypurchase, they’ll get complete customer satisfaction.Recognized worldwide as a leading manufacturer of highquality welding products, Hobart is headquartered in Troy,Ohio, where it shares its home with the Hobart Institute ofWelding Technology. Hobart’s presence in the industry isfurther strengthened by its nationwide network of handpickeddistributors who stand ready to help customers with a widearray of Hobart welding solutions.For more information about Hobart welding products orto receive a Hobart Full-line Catalog, visit us on the webat www.hobartbrothers.com or contact your local Hobartdistributor.19
W I R EW E L D I N GEXAMPLES OF GOOD AND BADWIRE WELDSGOOD WELDProper wire feedspeed, voltageand travel speedBAD WELDWire feed speedtoo lowBAD WELDWire feed speedtoo highCROSS-SECTIONCROSS-SECTIONCROSS-SECTIONWeld FaceWeld FaceSmooth andwell-formedWide and flatwith excessivespatterUniform contourGoodpenetrationand fusion20Weld FaceNarrow andconvexIrregular contourVery irregularcontourUndercuttingalong edgesSlag may be difficult to remove
W I R EW E L D I N GBAD WELDTravel Speedtoo fastBAD WELDTravel Speedtoo slowCROSS-SECTIONCROSS-SECTIONWeld FaceWeld FaceNarrow andconvexExcessivelywide and flatwith spatterIrregularcontourIrregular contourExtremelyporousPoor penetrationalong edges21
HobartBrothers.comHobart Brothers CompanyTroy, OH 45373 USAPhone 800.424.1543Fax800.541.6607International Fax 937.332.4094www.hobartbrothers.com
required. Stick welding is a manual arc welding process in which a covered metal stick electrode is used as the filler metal for making the weld. Wire welding is considered as a semi-automatic process, using a wire electrode that’s conveniently fed through a welding gun. Stick