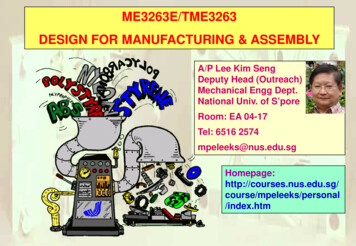
Transcription
ME3263E/TME3263DESIGN FOR MANUFACTURING & ASSEMBLYA/P Lee Kim SengDeputy Head (Outreach) MechMechanical Engg Dept.National Univ. of S’poreRoom: EA 04-17Tel: 6516 .edu.sg/course/mpeleeks/personal/index.htm
ME3263EDESIGN FOR MANUFACTURING & personal/Injection%20Mould%20e /index.html
TYPICAL APPLICATIONSPlastic InjectionMouldingA/P Lee Kim Seng
Features of Injection Molded Plastic PartA/P Lee Kim Seng
Examples Injection Molded Plastic Part
Injection MoldingInjection molding technology is a method ofprocessing predominantly used for thermoplasticpolymers.It consists of heating thermoplastic material untilit melts, then forcing this into melted plastic intoa steel mold, where it cools and solidifies.The increasing sophisticated use of injectionmolding is one of the principal tools in the battleto produce elegant product structures withreduced part counts.A/P Lee Kim Seng
Injection MoldingIn order to exploit the versatility of injectionmolding technology for economicalmanufacture, it is necessary to understandthe basic mechanisms of the process andrelated aspects of the molding equipmentand materials used.A/P Lee Kim Seng
A TYPICAL INJECTION MOULDING SYSTEMClampingunitInjection UnitMouldControllerChillerChiller : Heat ExchangerPumpOutletManifoldMouldInletManifoldDryer
Plastic molding processesClampingunitMouldInjection UnitControllerChillerInjection moldingBlow moldingInsert moldingRotational moldingVacuum formingDryer
Other types of plastic molding processesClampingunitMouldInjection UnitDryerControllerChillerStretch blow moldingGas injection moldingPlastic dip coatingExpanded PS moldingExtrusion Blow Molding
A TYPICAL INJECTION MOULDING SYSTEM
A TYPICAL INJECTION MOULDING SYSTEM
Basic Phases in Injection Moulding1. Mould closes. Screw moves forwardfor injection.3. Screw in full forward position. Packingcompletes.5. Cooling completes. Mould opens forpart ejection.2. Filling Completes. Screw continues movingforward for packing.4. Cooling and Plasticising.Moulding Sequence Mould Closes1st Stage Filling2nd Stage PackingCooling and PlasticisingMold OpensPart Ejected.
Injection Moulding Cycle1. 1st Stage Filling2. 2nd Stage Packing3. Cooling4. Mould Opens5. Part Ejected6. Mould ClosesA. Remaining CushionB. Holding Pressure VolumeC. Injection VolumeD. Decompression
Injection Molding Operations Fountain Effect Flow Hot resin flow from the middle of the flow channel to the walls andcools
Pressure Curves (1) (2) (3) (4) (5)Hydraulic PressureInjection Pressure (Pressure in front of screw)Pressure in GatePressure near GatePressure far from Gate(5)(4)(3)(2)(1)
Basic characteristics of a Cavity Pressure Curve453612 Start Injection Melt reaches sensor position Cavity is volumetrically filled (SwitchOver) Peak Cavity Pressure 4 5 The volumechange due to cooling of the melt iscompensated by additional melt pressedinto the cavity. Freezing point at the gate. Atmospheric pressure.
Optimised Process ConditionsOptimisedProcessConditions
CADProductDesignCAMMould DesignMaterialMouldManufacturingCAEIPC
A SINGLE CAVITY MOULDMould BaseTWO CAVITIES MOULD
INJECTION MOULDS
Mold Layout
Continuing a molddesign for anexisting projectDesigning a mold fora new projectDataPreparation Load AssemblyData Preparation Load Part IMOLD CSYS Scale Factor Containing BoxFilling ModuleProceeding onwith where youhave left off Layout Gate Design Runner DesignPartingMold Base Parting Line Insert Creation Choose Type Enter sizeHot Runner Design Manifold Selection Manifold Design Nozzle Design Gate DesignEjector DesignSlider DesignLifter DesignIMOLDCoolingDesign Design Ejection Edit EjectionStandardLibraryElectrodeDesign
Runner System Several types of runners single part runner multiple part runner symmetrical runner non-symetrical runner runner-less designs with hotmanifolds
Sprue Guidelines The sprue must not freeze before any other cross section. This isnecessary to permit sufficient transmission of holding pressure. The sprue must de-mold easily and reliably.Dco tmax 1.5 mmDs Dn 1.0 mmα 1º - 2ºtan α Dco - Ds / 2LSprue
Runner Guidelines Common runners Full-round runner Trapezoidal runner Modified trapezoidal runner (a combination ofround and trapezoidal runner) Half-round runner Rectangular runner
Gate SystemSubmarineGatePinpoint GateTunnel GateSide GateDifferent type of gates availableFan GateSprue Gate
Gates & ndard gatepositionStandard gate positionsA/P Lee Kim Seng
Gates & RunnersA/P Lee Kim Seng
Where would you put theGating for the part shown ?
Hot Runner System The ideal injection molding system delivers molded parts of uniform density, and free from allrunners, flash, and gate stubs. To achieve this, a hot runner system, in contrast to a cold runner system, is employed. Thematerial in the hot runners is maintained in a molten state and is not ejected with the moldedpart. Hot runner systems are also referred to as hot-manifold systems, or runnerless molding.FIGURE 1. Hot runner system types: (a) the insulated hot runner, (b) the internallyheated hot-runner system, and (c) the externally heated hot-runner system
Cam Operated SlidersFinger Cam PinA/P Lee Kim Seng
Hydraulic Operated SlidersA/P Lee Kim Seng
SliderEjectorPinA/P Lee Kim Seng
Type #1Type #2Type #3Type #4Type #5
Ejector PinA/P Lee Kim Seng
LifterA/P Lee Kim Seng
E LearningRef:Application of Multimedia andInternet Technology ine Learning of IndustrialDesign.Dr Shum SP, SimonIMCC 2002, Xiamen /project.swfA/P Lee Kim Seng
Multi Colours Moulding
Thank YouA/P Lee Kim Seng
Injection Molding A/P Lee Kim Seng In order to exploit the versatility of injection molding technology for economical manufacture, it is necessary to understand the basic mechanisms of the process and related aspects of t