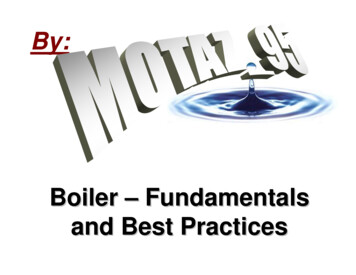
Transcription
By:Boiler – Fundamentalsand Best Practices
Boiler - FundamentalsSteam production and steam usesSteam purity and steam qualityTypes of boilersBasic boiler principlesBasic boiler calculations
Steam ProductionandSteam Uses
Steam ProductionWhen heat is added to water, itstemperature rises at a rate of 0.56 C(1 F) for each heat input of 2.095kJ/kg (1 Btu/lb)If we take water at 0 C (32 F) and weadd 419 kJ/kg (180 Btu/lb) then wewill increase the temperature of thewater by 100 C (180 F)This rise in temperature can bedetected and is called Sensible Heat(Specific Enthalpy - Water)
Steam TablesPressure Temperature Sensible Heatpsig 366339200388362Latent HeatBtu/lb971946929912882858838Total HeatBtu/lb1151116411731180119019971200Volume DrySaturated ft3/lb26.8013.909.306.603.892.762.14Pressure Temperaturebarg 48.802763.502781.702792.20Specific VolumeSteam 419.04505.60562.20640.70697.50781.60845.10
Steam ProductionSteamAt normal atmospheric pressure, anyfurther addition of heat to water at100 C will not increase thetemperature but will convert some ofthe water into steamIn order to convert water into steam2,257 kJ/kg (971Btu/lb) of additionalheat must be addedThis cannot be detected as a rise intemperature and is called the LatentHeat of Vaporisation (SpecificEnthalpy - Evaporation)
Steam ProductionSteamTotal Heat of Steam Sensible Heat Latent Heat of VaporisationSpecific Enthalpy :Steam Water EvaporationThus the Total Heat of Steam(Specific Enthalpy - Steam) is 2,676kJ/kg (1151 Btu/lb)This data is found in Steam Tables
Steam ProductionSteamFrom steam tables we can see that thetotal heat of steam does not vary agreat deal as the boiler pressureincreaseThe boiling point (b.p.) increases as thepressure increasesThus the sensible heat increases as thepressure increases, and the latentheat decreasesBoiler pressures are expressed in psia,psig, bar, kg/cm2, kpa
Steam UsesSpace heatingDrying - paper millProcess heatingSterilisationHumidificationPower generation
Steam PurityandSteam Quality
Steam PuritySteam purity is an expression of the quantity ofnon water components in the steamComponents can be dissolved in the steam,dissolved in water droplets entrained in thesteam or carried as discrete solid particles inthe steamSteam impurities are normally expresses as aquantity in parts per million (ppm) or parts perbillion
Steam QualitySteam quality relates to the quantity ofmoisture present in the steam100% quality specifying no moisturecontent0% quality specifying all liquidLiquid droplets entrained in the steamleaving a boiler contain dissolvedsolids
Types of Boilers
Types of Boilers Fire Tube Water Tube Waste Heat
Types of BoilersFire Tube BoilersWater Tube BoilersWaste Heat BoilersLow Pressure SystemsMedium to High PressureSystemsProcess applicationsHRSG
Fire Tube BoilersAlso referred to as smoke tube boilers, shellboilers, package boilersMultiple gas paths - 2, 3 and 4 passInternal furnace or fire box as the 1st passDry back or wet back designSingle fuel or dual fuel designLittle or no steam separation equipment
Fire Tube Boilers
Fire Tube Boilers
Fire Tube BoilersTypical designs are O, D and A type boilersSteam separation equipment - drumfurnitureCyclone separatorsDemister padsBaffle platesHave economisers and superheatersLarge water tube boilers are field erectedand may be unique design
Fire Tube BoilersSTEAM DRUMRISERSSUPERHEATERDOWNCOMERSSCREEN TUBESECONOMISERWATER WALLSAIR HEATERMUDDRUM
Fire Tube Boilers
Waste Heat BoilersVarious types and designsShell and tube exchangerLinked to processAmmonia plant
Waste Heat BoilerAmmoniaPlant
Heat Recovery SteamGenerators (HRSG)Various types and designsShell and tube exchangerWater tube boilerMultiple drum systemlow pressure (LP)medium pressure (MP)high pressure (HP)
Multi Pressure Boiler Systemwith Integral Deaerator
Steam GeneratorsCoil designs, vertical or horizontalBucket typesSteam water separatorBoiler water returned to feed tankMay include economiser and superheater
Steam Generator - Coil
Basic Boiler Principles
Basic Boiler PrinciplesEXTERNALTREATMENTSATURATED STEAMEVAPORATED WATERMAKE UPWATERANDSOLIDSHOT WELLFEEDWATERDEAERATORWATERANDSOLIDSRETURNED CONDENSATEWATER AND HEATBlowdown - Removes boiler water witha high concentration of solids which isreplaced by feedwater containing a lowconcentration of solidsIntermittent blowdownto remove suspendedsolids in boiler waterContinuousblowdownto removedissolvedsolids inboiler water
Basic Boiler PrinciplesWater and solids enter the boilerWater leaves the boiler as steamSolids concentrate in the boilerTherefore the boiler water will contain more solidsthan the feedwaterThis Concentrating effect is calledThe Cycles of Concentration or The Cycles
Basic Boiler PrinciplesA boiler can only tolerate a specificnumber of cycles ofconcentrationThis will vary depending onType and pressure of the boilerType of external treatmentPercentage condensate return
Basic Boiler PrinciplesThe chemical factors which limit theboiler water cycles of concentration areSuspended solids (Total Hardness)Dissolved solidsTotal alkalinity (M Alkalinity)Silica
Basic Boiler PrinciplesHow do we determine the chemicalcontrol limits that we apply to anoperating boiler ? British Standard BS2486:1997 ASME Guidelines* 1994 Consensus on operating practices forthe control of feedwater and boilerwater chemistry in modern industrialboilers
Basic Boiler Calculations
Basic Boiler CalculationsMake UpFeedwaterCondensateReturn
Basic Boiler Calculations Feedwater Make up Condensate Return
Basic Boiler CalculationsSteam Make (Flow)FeedwaterFlowBlowdown
Basic Boiler Calculations Feedwater Make up CondensateReturn Feedwater Flow (FWF) Steam Make Blowdown
Basic Boiler Calculations Feedwater Make up Condensate Return Feedwater Flow (FWF) Steam Make Blowdown(BD) Feedwater Flow (FWF) Steam Make Steam Make Cycles 1
Basic Boiler Calculations Feedwater Make up Condensate Return Feedwater Flow (FWF) Steam Make Blowdown(BD) Feedwater Flow (FWF) Steam Make SteamMake Cycles -1 Blowdown Steam make or Cycles –1 % Blowdown FWFCycles1as a % of FWFCycles
Basic Boiler CalculationsCondensate Return is also expressed as % ofFWFIf Condensate Return 60% Make up 40%% Condensate % Make up 100% FWFAs the boiler water cycles of concentrationincrease then the feedwater flow and the steammake approach the same number
Basic Boiler CalculationsCalculate the feedwater composition (impurities)from make up and condensate analysis belowMake-UpTotal HardnessM AlkalinityTDSSilica% Condensate22003506Condensate01015050Feedwater
Basic Boiler CalculationsCalculate the feedwater composition (impurities)from make up and condensate analysis belowMake up Condensate Feed waterTotal HardnessM AlkalinityTDSSilica% Condensate22003506010150501105182.53
Boiler Water Best Practises
Boiler WaterInternal TreatmentTechnology
Why is Effective Internal BoilerWater Treatment Necessary ?
Effective Internal Boiler WaterTreatmentControls Deposition Corrosion Carryoverand
Enhances System Reliabilityand Efficiency Avoids unscheduled shutdowns Helps ensure uninterrupted production Reduces maintenance costs Reduces operating costs
What Operating Costs areAssociated with BoilerOperation ?
Boiler Operating Costs Fuel - Gas, Oil, Coal Water - Influent and Effluent Regenerants - Salt, Acid,Caustic Water Treatment
Boiler Operating Costs Fuel - Gas, Oil, Coal Water - Influent and Effluent Regenerants - Salt, Acid, Caustic Water Treatment
Boiler Operating Costs Need to minimise all operating costsReducing boiler water blowdown giveswater, energy and chemical savings Need to maximise efficiencyMaintain clean heat transfer surfacesHeat recovery systems
Effective Internal Boiler WaterTreatmentControlsDeposition
Boiler Water Deposit Control Hardness salts Calcium Magnesium Metal oxides Iron Copper
Comparison of Heat Transfer SurfacesWith and Without DepositsMetalFireside600 FMetalWatersideFiresideScaleWaterside800 Fandabove500 FWithout deposits500 FWith deposits
Energy Loss from Scale Deposits(from Energy Conservation Programme Guide for Industry & Commerce)Scale8ica7S il5Iron&Energy Loss ceS2101640.4 mm1320.8 mm3641.2 mm1161.6 mm5642.0 mmScale Thickness, inches or mm3322.4 mm
Long Term Overheating
Boiler Water Deposit Control Removal of impurities Pretreatment plant Chemical treatment Controlled blowdown
Effective Internal BoilerWater TreatmentControls Deposition Corrosion
Boiler Water Corrosion Control Oxygen pitting Caustic corrosion Embrittlement or gouging Acidic attack
Oxygen Corrosion - Pitting
Caustic Gouging
Acid CorrosionAcid Corrosion
Effective Internal BoilerWater TreatmentControls Deposition Corrosion Carryover
Control of Boiler Water Carryover Effective mechanical steam separation Proper control of boiler water chemistry Antifoam, as needed Avoid major contaminant ingress Proper boiler operating practices
What Types ofInternal Boiler WaterTreatments areAvailable ?
Internal TreatmentProgrammesGeneral Classifications Precipitating Solubilising Combination
Internal TreatmentProgrammes Phosphate/Polymer Phosphonate/Polymer Chelant/Polymer Phosphate/Chelant/Polymer All Polymer Coordinated pH/Phosphate/Polymer All Volatile Treatment (AVT)
Boiler Water Polymersare Crucial to theSuccess of anyInternal TreatmentProgramme
How do Boiler Water PolymersFunction ?
Boiler WaterPolymersThe mechanisms by which boilerwater polymers function are Complexation / Solubilisation Crystal modification Dispersion
Calcium phosphate,magnesium silicatecrystals formed inboiler water withoutdispersant
Calcium phosphate,magnesium silicatecrystals formed inboiler water in thepresence of asulphonated polymer
Variables Affecting PolymerPerformance Functional group carboxylated (SCP/SCCP) sulfonated (SSP) phosphorylated (HTP) Polymer backbone Molecular weight
Typical Polymer StructuresCH2CH2C OO-CHCHCH2C OC OOHNH2XPolyacrylateAcrylate-Acrylamide CopolymerCH3CCH2CHCH2OC OCHCHCC OSO3O-X CHOXXPolymethacrylateSulfonated Styrene-MaleicAnhydride CopolymerY
Typical Polymer StructuresCH2ORP-OCHC OCH2O-O- H OCH2 O]m HPOHO-nPolyethylene glycol allyl ether (PEGAE)OCHEDP[CH2CH3 CH3 -OCH2P OPhosphonateOCHO-CH2CO PO-OHXPoly (isopropenyl phosphonic acid)PIPPA
DepositionPolymer PerformancevsMolecular WeightPolymer Molecular Weight
Programme SelectionConsiderations Boiler pressure, design Pre-treatment plant type Feedwater quality Hot well, deaerator type Steam turbine Control capabilities
Chemical Factors Total Dissolved Solids (TDS) Alkalinity Silica Suspended Solids
ASME Boiler Feedwater QualityGuidelines for Modern IndustrialWater-TubeBoilersHardnessCopperIronDrum Pressure (kg/cm²) 0 - 2122 - 3132 - 4243 - 5253 - 6364 - 7071 - 105 (ppm Fe)(ppm Cu)(ppm 020.0150.0150.010.300.300.200.200.100.050.0
Internal TreatmentProgrammes Phosphate/Polymer
Phosphate/Polymer Treatment Reactions:OHCa PO4 Ca(OH)PO4 Calcium Phosphate HydroxideHydroxyapatite Mg Mg(OH)SiO3 MagnesiumSiO3Silica OHHydroxideSerpentine
Phosphate/Polymer TreatmentCharacteristics Hardness controlled by precipitation Polymers used to control hardnesssludge and metal oxides Phosphate residual used for programmecontrol Hydroxide alkalinity required (pH : 10.5 12)
Phosphate/PolymerTreatmentBoiler Control Parameters Phosphate residual as PO4 depending onhardness in the feedwater usually associated with boiler pressure and environmental legislation M alkalinity of 700 ppm as CaCO3 (25 % ofTDS) Polymer : min 360 ppm as SP8100 Still the most used method for treating lowpressure boilers
Phosphate/PolymerTreatmentAdvantages Disadvantages Tolerates a wide range offeedwater hardness Is a precipitationprogramme (somedeposition is normal) Non corrosive treatment Suitable for low to mediumpressure systems Easy operator control Higher blowdown ratesmay be required
Internal Treatment Programmes Phosphate/Polymer Phosphonate/Polymer
Phosphonate/PolymerCharacteristics Organic phosphor donors combinedwith three synergistic polymers Complexes hardness, iron and copperions in BFW Disperses/solubilises contaminants inboiler minimising sludge formation
Phosphonate/Polymera) SolubilisingBoiler Control Parameters– 200 - 300 ppm in blowdown– (BFW hardness tot Fe) max 1 ppm for300 ppm in boiler– filtered tot. PO4 min 6 ppm in BD– Other : conductivity SiO2 M-alk
Phosphonate/Polymerb) PrecipitatingBoiler Control Parameters Phosphate residual as PO4 depending onhardness in the feedwater M alkalinity of 700 ppm as CaCO3 (25 % ofTDS)
Internal TreatmentProgrammes Phosphate/Polymer Phosphonate/Polymer Chelant/Polymer
Chelant/PolymerTreatment Common Chelating Agents EDTA NTA
Chemical Structure ofEDTA- OOC - CH2H HCH2 - COO N-C-C-N- OOC - CH2CH2 - COO H H
EDTA/Calcium ComplexCOOCH2CONOCaNOCOCH2OCH2COCH2CH2CH2
Chelant/Polymer TreatmentCharacteristics Are solubilising treatments Chelant complexes hardness and soluble iron /copper Polymers used to enhance metal oxide control Must be fed to the feedwater line
Chelant/Polymer TreatmentAdvantages Disadvantages Solubilising treatment Requires intensiveoperator control Effective on hardness andsoluble iron Allow reduced blowdown Increased reliability andefficiency Suitable for low to mediumpressure systems Potentially corrosive ifmisapplied
Internal TreatmentProgrammes Phosphate/Polymer Phosphonate/Polymer Chelant/Polymer Phosphate/Chelant/Polymer
Chelant/Phosphate/PolymerTreatmentCharacteristics Utilises EDTA chelant (partial chelation) Primarily a solubilising programme Phosphate provides back-up upset protection Residual phosphate test used as programme control Polymers used to control metal oxides and otherprecipitates
Chelant/Phosphate/PolymerTreatmentAdvantages Primarily a solubilising treatment Effective on hardness and iron May allow reduced blowdown Increased reliability andefficiency Easy and accurate control test Tolerates a wide range offeedwater hardness Suitable for low to mediumpressure systems Disadvantages Some precipitation ispossible Potentially corrosiveif misapplied
Internal TreatmentProgrammes Phosphate/Polymer Chelant/Polymer Phosphate/Chelant/Polymer All Polymer
All Polymer TreatmentCharacteristics Certain polymers can be effectivecomplexing agents Principle mechanism is complexation ofsoluble impurities Secondary mechanism is dispersion ofparticulates Fed to the boiler feedwater
Limitations of Polyacrylate BasedAll Polymer Programmes Low tolerance to feedwater quality upsets Potential for calcium polyacrylate deposition Releases ammonia Economiser iron pick-up Precise testing for polymers is difficult
Internal TreatmentProgrammes Phosphate/Polymer Phosphonate/Polymer Chelant/Polymer Phosphate/Chelant/Polymer All Polymer/OptiSperse AP
What is OptiSperse AP ? A new, revolutionary programme usingpatented co-polymer technology A stand-alone all polymer / all organic boilerinternal treatment programme whichprovides superior control over hardness andiron deposition
OptiSPerse AP Treatment vs.Traditional All Polymer Traditional All PolymerProgramme Generates ammonia Forms calcium-polymerdeposits with BFWhardness excursions orunderfeed Overfeed may causefoaming OptiSperse APProgramme No ammonia generated No treatment relateddeposition No steam purityproblems Not corrosive to preboiler Corrosive to economisercircuitsurfaces May be fed ahead of Must be fed downstream ofcopper alloys in BFWcopper alloys
Research Boiler Studies Under FoulingConditionsTest Conditions900 psig (63 kg/cm2)All-polymer ProgrammeCa/Mg/Fe presentDWDTRADITIONALALL-POLYMEROPTISPERSE AP0123POLYMER/HARDNESS RATIO45
Research Boiler StudiesUnder Potential Fouling ConditionsDeposit Weight Density(Equal Polymer Actives)300 psig (21 kg/cm2)600 psig (42 kg/cm2)OPTISPERSE AP900 psig (63 kg/cm2)Traditional All-Polymer
Internal TreatmentProgrammes Phosphate/Polymer Phosphonate/Polymer Chelant/Polymer Phosphate/Chelant/Polymer All Polymer CoordinatedpH/Phosphate/Polymer
Coordinated pH/PhosphatePolymer TreatmentCharacteristics Primarily for high purity/high pressuresystems Mainly a corrosion control programme Phosphate used to control pH and neutraliseexcess caustic Polymers used to control deposition
Relative Corrosive AttackCorrosion of Mild Steel vs. pH8.5 pH12.7 pHSafe Range1234567891011121314
Caustic ConcentrationMechanismMagnetiteNaOHSteam OutNaOHNaOHNaOHNaOHBoiler Water inFe3O4 PorousDepositNaOH
PreventionmagnetitesteamescapesporousdepositHPO42 Na NaHPO42 Na Na HPO42 HPO42 Na HPO42 -Boiler water in
Minimising CausticConcentration and Corrosionusing PhosphateNaOHCausticSoda Na2HPO4Na3PO4DisodiumPhosphateTrisodiumPhosphate H2OWater
Co-ordinated Congruent Phosphate/pHControl Chart"Free" CausticRegionpHiMax1N2.6:mmuarydnBo uOa/PN13.0:1N2.7:O4a/PtrolnoC1234olaM4tior Ra1N2.8:O4a/PO4a/ParydnBou5 6 7 8 10olMO4a /PN12.2:atioRraVectorControlDiagram15 20Ortho-phosphate, as PO4 mg/l"Captive"AlkalinityRegionCausticTrPh i-Sos odp h iu 2Di-SodiumPhosphatewnoMwdoB loPh noos Soph diuat me30 40 50 60
Internal TreatmentProgrammes Phosphate/Polymer Phosphonate/Polymer Chelant/Polymer Phosphate/Chelant/Polymer All Polymer Coordinated pH/Phosphate/Polymer OptiSperseHTP
Characteristics of HTP-2 A unique new phosphorylated boiler polymer Particularly effective on iron Demonstrated clean-up ability Designed for high purity/high cycles systems Suitable for use up to 125 kg/cm²
HTP-2 Polymer StructureCH3CH2CO POHOXPoly (isopropenyl phosphonic acid) . . . PIPPA
Internal TreatmentProgrammes Phosphate/Polymer - OptiSperse PO, OptiGuard MCP Phosphonate/Polymer - OptiSperse PQ Chelant/Polymer - OptiSperse CL Phosphate/Chelant/Polymer - OptiSperse CP All Polymer - OptiSperse AP, OptiGuard MCA Coordinated pH/Phosphate/Polymer - OptiSperse HTP All Volatile Treatment (AVT)
Steam Production When heat is added to water, its temperature rises at a rate of 0.56 C (1 F) for each heat input of 2.0