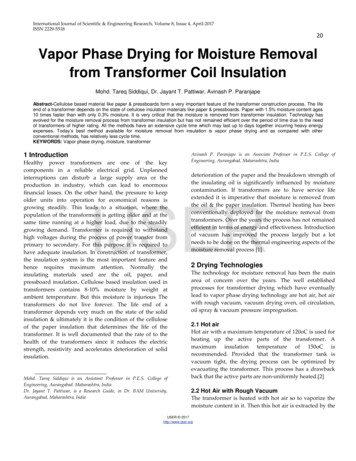
Transcription
International Journal of Scientific & Engineering Research, Volume 8, Issue 4, April-2017ISSN 2229-551820Vapor Phase Drying for Moisture Removalfrom Transformer Coil InsulationMohd. Tareq Siddiqui, Dr. Jayant T. Pattiwar, Avinash P. ParanjapeAbstract-Cellulose based material like paper & pressboards form a very important feature of the transformer construction process. The lifeend of a transformer depends on the state of cellulose insulation materials like paper & pressboards. Paper with 1.5% moisture content ages10 times faster than with only 0.3% moisture. It is very critical that the moisture is removed from transformer insulation. Technology hasevolved for the moisture removal process from transformer insulation but has not remained efficient over the period of time due to the needof transformers of higher rating. All the methods have an extensive cycle time which may last up to days together incurring heavy energyexpenses. Today’s best method available for moisture removal from insulation is vapor phase drying and as compared with otherconventional methods, has relatively less cycle time.KEYWORDS: Vapor phase drying, moisture, transformer1 IntroductionHealthy power transformers are one of the keycomponents in a reliable electrical grid. Unplannedinterruptions can disturb a large supply area or theproduction in industry, which can lead to enormousfinancial losses. On the other hand, the pressure to keepolder units into operation for economical reasons isgrowing steadily. This leads to a situation, where thepopulation of the transformers is getting older and at thesame time running at a higher load, due to the steadilygrowing demand. Transformer is required to withstandhigh voltages during the process of power transfer fromprimary to secondary. For this purpose it is required tohave adequate insulation. In construction of transformer,the insulation system is the most important feature andhence requires maximum attention. Normally theinsulating materials used are the oil, paper, andpressboard insulation. Cellulose based insulation used intransformers contains 8-10% moisture by weight atambient temperature. But this moisture is injurious Thetransformers do not live forever. The life end of atransformer depends very much on the state of the solidinsulation & ultimately it is the condition of the celluloseof the paper insulation that determines the life of thetransformer. It is well documented that the rate of to thehealth of the transformers since it reduces the electricstrength, resistivity and accelerates deterioration of solidinsulation.Avinash P. Paranjape is an Associate Professor in P.E.S. College ofEngineering, Aurangabad, Maharashtra, Indiadeterioration of the paper and the breakdown strength ofthe insulating oil is significantly influenced by moisturecontamination. If transformers are to have service lifeextended it is imperative that moisture is removed fromthe oil & the paper insulation. Thermal heating has beenconventionally deployed for the moisture removal fromtransformers. Over the years the process has not remainedefficient in terms of energy and effectiveness. Introductionof vacuum has improved the process largely but a lotneeds to be done on the thermal engineering aspects of themoisture removal process [1]IJSERMohd. Tareq Siddiqui is an Assistant Professor in P.E.S. College ofEngineering, Aurangabad. Maharashtra, IndiaDr. Jayant T. Pattiwar, is a Research Guide, in Dr. BAM University,Aurangabad, Maharashtra, India2 Drying TechnologiesThe technology for moisture removal has been the mainarea of concern over the years. The well establishedprocesses for transformer drying which have eventuallylead to vapor phase drying technology are hot air, hot airwith rough vacuum, vacuum drying oven, oil circulation,oil spray & vacuum pressure impregnation.2.1 Hot airHot air with a maximum temperature of 120oC is used forheating up the active parts of the transformer. Amaximum insulation temperature of 150oC isrecommended. Provided that the transformer tank isvacuum tight, the drying process can be optimized byevacuating the transformer. This process has a drawbackback that the active parts are non-uniformly heated.[2]2.2 Hot Air with Rough VacuumThe transformer is heated with hot air so to vaporize themoisture content in it. Then this hot air is extracted by theIJSER 2017http://www.ijser.org
International Journal of Scientific & Engineering Research, Volume 8, Issue 4, April-2017ISSN 2229-551821means of rough vacuum to remove water so vaporized.This ensures that the water which has vaporized does getreabsorbed in the insulation materials. But this processalso is time consuming as well not efficient. [2]2.3 Vacuum Drying OvenIn this process the transformer is kept in a vacuum ovenwhere it is heated by means of electrical heaters. Thisresults in water being evaporated which is present in thelayers of insulation. Once the required temperature hasbeen attained, vacuum is created in the oven with the helpof vacuum pump so that the water vapor present in airaround the transformer is extracted & maximum dryingcan be ensured.[2]2.4 Oil CirculationTransformer oil is circulating through oil purificationequipment. After filtering the oil to remove the particles,the oil is heated to 80oC. In a so called vacuum degassingunit, all residual gasses are removed and the moisturecontents of less than 5ppm can be reached. This is anecessary maintenance process for oil filled transformersbut not very efficient for removing moisture as there isindirect heating of the insulation which takes a very longtime.[2]2.6 Vacuum Pressure ImpregnationIn VPI the transformer coils are heated initially to removethe moisture from the layers of insulation. After thedesired temperature has been attained, vacuum is createdin the tank so as remove the air along with the watervapor. On reaching the desired level of vacuum, resin,which is atmospheric pressure, is allowed to impregnatethe coils at a low pressure. As a result of the pressuredifference, resin impregnates the innermost parts of thecoils thereby providing effective insulation.[2]3 Vapor Phase DryingAs of now, the most advanced drying technologyfor power transformer is the vapor phase dryingmethod. Vapor phase drying is the method whichapplies vacuum but the method of heating is notthrough air. In this method the carrier of heat isvapor of low viscosity solvent like kerosene with asufficiently high flash point instead of air. In vaporphase drying, as shown in figure 01, the vapor isheated in a chamber by the use of electric heatersand is passed over the core coil assembly keptinside for drying. The solvent vapors thuscondense on the drying mass and are collectedback in form of liquid solvent which is recirculatedin the system. For this purpose the vapor phasedrying systems have an evaporator and condensersystem in addition to the vacuum chamber andvacuum pulling equipments such as vacuum pump,roots pump etc which are part of conventionalvacuum system. Thus the system in total consistsof solvent heat conveyer system consisting ofstorage, evaporation, condensation, filtration,solvent feedback and control arrangement.IJSER2.5 Oil SprayAfter removing the transformer oil from the tank, spraynozzles are assembled at the man holes & flanges of thetransformer tank. The tank is evacuated by a vacuumpump to a pressure of 5mbar. Oil is pimped through filterdevices & a heating unit to the top of the autoclave. Vianozzles, the oil is sprayed onto the surface of the activeparts. The active parts are heated up & the moistureevaporates. The vacuum pump unit continuously sucksthe water vapor out of the transformer tank. The absenceof oxygen allows the increase of the oil temperature to 120oC. in this process also the drying times are very long.[2]IJSER 2017http://www.ijser.org
International Journal of Scientific & Engineering Research, Volume 8, Issue 4, April-2017ISSN 2229-551822Fig 013.2 Methodology of VPDThe drying process typically consists of following steps [3](a) Preparation(b) Heating and drying(c) Pressure reduction(d) Fine vacuumIJSERFigure 2 shows the sequence of operation of VacuumPhase Drying in a vacuum vessel and the four typicalstages of vapor phase of drying process.a)PreparationThe complete evaporator and the condenser system isapplied with full vacuum to the level of 5 torr beforedrawing the solvent in the evaporator and heating it to thelevel of 130 C. The vacuum chamber of the VPD is alsoapplied with vacuum of 5 torr. The core coil assembly iskept with slope to assist draining of the solventFigure 02b) Heating and DryingHeating is started after all the air has been taken out. Thevalves are kept open for the solvent vapors to enter thevacuum chamber and condense over the surface of thedrying mass loaded. The condensation releases the heatand the loaded mass temperature increases thus causingevaporation of water. The mixture of water and solventdrains out for recirculation.c) Pressure ReductionDuring this stage the supply of solvent vapor is stoppedand most of the solvent vapors which were absorbed bythe insulation re-evaporate, condense out in the condenserIJSER 2017http://www.ijser.org
International Journal of Scientific & Engineering Research, Volume 8, Issue 4, April-2017ISSN 2229-551823and finally get returned to the evaporator. This phasecontinues till the pressure in the vessel reaches 15-20 Torr.d) Fine VacuumThis is the final stage of the cycle which immediatelyfollows the pressure reduction stage. The vessel or thevacuum chamber is again reduced to pressure notexceeding 0.1 Torr. The water extraction is monitored andrecorded at regular intervals. When the water extractionrate becomes constant to the desired level the cycle is(c) The solvent must not have any effect on the insulationproperties and their expected life.(d) The solvent must be reusable for unlimited no of timeshowever this not true practically as it is required to betopped up at regular intervals and to be changed after 3-5years.(e) Flash point should be above 55 Cstopped.3.5 Advantages of VPDAdvantages associated with VPD can be enumerated asfollows. [4]3.3 Time Saved in VPDAs compared to the conventional method of vacuumdrying, the time required for moisture removal fromtransformers of the same rating, VPD has a relatively lesscycle time. This is evident from the followingTABLE. 1Prevents oxidation during drying,Uniformity of Temperature (Heating),Excellent Quality of Dryness,Associated Components Drying.A further advantage of the vapor-phase process is that dirtand dust deposits formed on live components duringfactory assembly are carried away by condensate duringthe heating stage.Cycle time in hrs (avg.)IJSERRatingVacuumdryingVPD11 KV, 500KVA161211 KV, 1000KVA181211 KV, 2000KVA181433 KV, 3000KVA302433 KV, 5000KVA362433KV, 10000KVA42304 ConclusionIt is well documented that the rate of deterioration of thepaper and the breakdown strength of the insulating oil issignificantly influenced by moisture contamination.Conventional drying processes have not remainedefficient in terms of cycle time and effectiveness.Introduction of vacuum has improved the process largelybut a lot needs to be done on the thermal engineeringaspects of the moisture removal process.In this age, when energy crisis is rampant in every sector,vapor phase drying may serve to bring down the energyconsumption in moisture removal from transformerinsulation by effectively reducing the cycle time. Yet, tohave a greater impact on energy saving, further research isrequired in vapor phase drying.3.4 Properties of The Solvent VaporVPD uses solvent vapor as a heat carrier instead of air.This solvent vapor should posses certain properties whichcan be enumerated as follows [3]a) Vapor pressure must be distinctly lower than that ofwater, so that a large pressure difference assists efficientwater diffusion from the beginning of the heating phase.(b) Evaporation heat should be very high.References[1] Anand Bhanpurkar, Ajay Bangar , Rajan Sharma,H.P.Tripathi. "Comparative analysis of moistureremoving processes from transformer which are usedto increase its efficiency." Global Journal of Researches inEngineering (Global Journals Inc. (USA)) 12, no. 5(2012): 6-10.IJSER 2017http://www.ijser.org
International Journal of Scientific & Engineering Research, Volume 8, Issue 4, April-2017ISSN 2229-551824[2] Stefan Zabeschek, Helmut Strzala. Drying of high voltagepower transformer in the feild with a mobile vapor phasedrying equipment. Ehringshausen, Germany: HEDRICHVacuum Systems, 2007.[3] “Transformers” by Bharat Heavy ElectricalsLimited.[4] AlFanar Technical Seervices. VAPOR PHASEDRYING PLANT. Jubail, KSA: AlFanar TechnicalSeervices.[5] Vishvas Power Engineering Services (P) Ltd., K5MIDC, Butibori, Nagpur, Maharashtra, IndiaIJSERIJSER 2017http://www.ijser.org
International Journal of Scientific & Engineering Research, Volume 8, Issue 4, April-2017 . for power transformer is the vapor phase drying . 2.4 Oil Circulation . Transformer oil is circulating through oil purification eq